
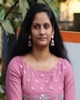
- Open Access
- Authors : Neethi B.
- Paper ID : IJERTV10IS010260
- Volume & Issue : Volume 10, Issue 01 (January 2021)
- Published (First Online): 03-02-2021
- ISSN (Online) : 2278-0181
- Publisher Name : IJERT
- License:
This work is licensed under a Creative Commons Attribution 4.0 International License
Damage Detection in Fibre Reinforced Polymer (FRP) Strap Retrofitted Beams
Neethi B.
Structural Engineering Consultant at Ram Associates, Trivandrum and Former Assistant Professor (Adhoc), Dept of Civil Engineering, College of Engineering Muttathara, Kerala
Abstract – Retrofitting is the modification of existing structures to make them more resistant to seismic activity, ground motion etc. Many of the existing reinforced concrete structures throughout the world are in urgent need of rehabilitation, repair or reconstruction because of deterioration due to various factors like corrosion, lack of detailing, failure of bonding between beam-column joints etc. Fibre Reinforced Polymer (FRP) composite has been accepted in the construction industry as a promising substitute for repairing and in incrementing the strength of RCC structures. But the study about the damage detection in beams retrofitted using Fibre Reinforced Polymer (FRP) strap is limited. So here is an attempt to study about the behaviour of beam retrofitted using fibre reinforced polymer and whether fully bonded FRP strap on a beam or partially bonded FRP strap on a beam is effective. Also a comparative study of beams retrofitted with different number of layers of FRP strap and to carry out analytical study using ANSYS software in order to predict the mid span deflection of concrete and to done the comparative study based on the experimental results.
Index Terms – ANSYS, Carbon Fibre Reinforced Polymer (CFRP), Control beam, Fibre Reinforced Polymer (FRP), Retrofitting.
1 INTRODUCTION
Retrofitting is the modification of existing structures to make them more resistant to seismic activity, ground motion etc. For buildings, this means making changes to the systems inside the building or even the structure itself at some point after its initial construction and occupation. Typically this is done with the expectation of improving amenities for the buildings occupants and/or improving the performance of the building. The development of new technologies mean that building retrofits can allow for significant reductions in energy and water usage.
Structures deteriorate due to problems associated with reinforced concrete. Natural disasters like earthquakes have repeatedly demonstrated the susceptibility of existing structures to seismic effect and hence implements like retrofitting and rehabilitation of deteriorated structures are important in high seismic regions. Thus retrofitting and strengthening of existing reinforced concrete structures has become one of the most important challenges in Civil engineering[6]. In such case complete replacement of an existing structu.re may not be a cost-effective solution and it is likely to become an increased financial burden if upgrading is a viable alternative. In such occasions, repair
and rehabilitation are most commonly used solutions. Among them strengthening with Fibre Reinforced Polymers (FRP) composite materials in the form of external reinforcement is of great interest to the Civil engineering community
2 FIBRE-REINFORCED POLYMERS (FRP) Fibre-reinforced polymers/plastics is a recently developed material for strengthening of RC and masonry structure. This is an advanced material and most of the development in its application in structural retrofitting has taken place in the last two decades[13]. It has been found to be a replacement of steel plate bonding and is very effective in strengthening of columns by exterior wrapping. The main advantage of FRP is its high strength to weight ratio and high corrosion resistance. FRP plates can be 2 to 10 times stronger than steel plates, while their weight is just 20% of that of steel. However, at present, their cost is high. The CFRP strengthening provides additional flexural or shear reinforcement, the reliability for this material application depends on how well they are bonded and can transfer stress from the concrete component to CFRP laminate. Also, CFRP has made this technique even more acceptance worldwide. CFRP improvement was as much as twice of the GFRP[2]. So in this thesis carbon fiber reinforced polymer was used as the retrofitting agent.
3 EXPERIMENTAL DETAILS
The current study presents results from the finite element analysis of the seven full-scale beams. Comparisons of the mid-span deflection between finite element results and those from the experimental beams of the study of Al- Amery and Al-Mahaidi are done. In the experimental study. four RC beams with various CFRP retrofitting schemes were analysised. All beams were 2700 mm long, 260 mm deep, and 140 mm wide. One concrete beam was kept without retrofitting and was considered as a control beam for comparison. The rest of the beams were provided with either CFRP sheets for flexural strengthening, or, with CFRP straps for shear strengthening. Two beams, and, were tested in four- point bending over a total span of 2300 mm and a shear span of 700 mm, while the rest, were tested in three- point bending. This was intended to increase the applied moment at the critical section of the beam. All the beams have a width of 140 mm, a depth of 260 mm and rebars as shown in Fig.1. The details of the beams are given in Table 1. The CFRP straps are of one layer 50 mm wide CFRP in a complete loop with 75 mm
overlap and spacing of 200 mm along the beam span. The CFRP sheets are of three layers applied centrally in a wet lay-up process along the bottom surface of the beams having a width of 100 mm and a length of 2000 mm.
CFRP provided |
Type of loading |
Total span (mm) |
Shear span (mm) |
None |
Four point bending |
2300 |
700 |
Straps |
Four point |
2300 |
700 |
CFRP provided |
Type of loading |
Total span (mm) |
Shear span (mm) |
None |
Four point bending |
2300 |
700 |
Straps |
Four point |
2300 |
700 |
Table 1. Details of the beams
bending |
|||
Sheets |
Three point bending |
2400 |
1200 |
Straps + sheets |
Three point bending |
2400 |
1200 |
CFRP straps are 50 * 0.176 mm at 200 mm c/c spacing with single loops. CFRP sheets are 2000 * 100 * 0.176 mm applied symmetrically in three layers.
Fig.1. Typical details beam specimen; (a) cross-sectional details, (b) four point loading for Control beam and beam having CFRP strap, (c) three point loading for beam having CFRP sheet and beam having CFRP strap + sheet
4 FULL SIZE BEAMS:
Seven full size beams were analysised for the study and is compared based on different cases. Each beam had a different strengthening scheme as described below
-
A Control Beam with no CFRP strengthening.
-
A beam with partially bonded CFRP straps of one layer 50 mm wide CFRP in a complete loop with 75 mm overlap and spacing of 200 mm along the beam span.
-
A beam with CFRP sheets are of three layers applied centrally along the bottom surface of the beams having a width of 100 mm and a length of 2000 mm.
-
A beam with combination of CFRP strap + sheet strengthening.
-
A beam with fully bonded CFRP straps of one layerin a complete loop along the beam span.
-
A beam with partially bonded CFRP straps of three layer 50 mm wide and spacing of 200 mm along the beam span.
-
A beam with partially bonded CFRP straps of five layer 50 mm wide CFRP in a complete loop and spacing of 200 mm along the beam span.
These seven beams full sized beam of 2700mm x 260mm x 140mm size were analysed and compared based on different cases are
-
Control beam and a beam retrofitted with partially bonded CFRP straps is compared and find which is more effective
-
To carry out analytical study using ANSYS software of the control beam, a beam with partially bonded CFRP straps of one layer, a beam with CFRP sheets and a beam with combination of CFRP strap + sheet strengthening in order to predict the mid span deflection of concrete and each of the beam is compared with each of the experimental results.
-
To perform a study of beams retrofitted using CFRP straps with different number of layers ( such as one layer, three layer and five layer) in order to study the variation of deflection curve.
-
To find whether fully bonded or partially bonded CFRP strap on a beam is effective.
5 ANSYS SOFTWARE MODELLING
The ANSYS structural analysis software suite is trusted by organizations around the world to rapidly
solve complex structural engineering problems with ease. ANSYS finite element program (ANSYS 14.5), operating on a WINDOW x64 system, was used in this study to simulate the behavior of the beams and it was released on 2012.
-
Element Type
-
Reinforced Concrete:
SOLID65 is used for the 3-D modelling of solids with or without reinforcing bars. The solid is capable of cracking in tension and crushing in compression. The element is defined by eight nodes having three degrees of freedom at each node: translations in the nodal x, y, and z directions. Up to three different rebar specifications may be defined. Solid 65 is used for modelling the concrete beam block and it is shown in Fig.2.
Fig.2.Geometry of SOLID653-D reinforced concrete solid
-
Steel Reinforcement:
A LINK180 element was used to model the steel reinforcement bars. Two nodes are required for this element. The 3-D spar element is a uniaxial tension- compression element with three degrees of freedom at each node: translations in the nodal x, y, and z directions. As in a pin-jointed structure, no bending of the element is considered. The geometry and node locations for this element type are shown in Fig.3.
Fig.3. Geometry of LINK180 3-D spar
-
CFRP Elements:
A SHELL181 element was used to model the CFRP elements. It is suitable for analyzing thin to moderately- thick shell structures. It is a four- noded element with six degrees of freedom at each node: translations in the x, y, and z directions, and rotations about the x, y, and z axes. The degenerate triangular option should only be used as filler elements in mesh generation. The geometry and node locations for this element type are shown in Fig.4
Fig.4. Geometry of SHELL181 Finite Strain Shell
-
-
Material Properties
-
Reinforced Concrete:
Development of a model for the behavior of concrete is a challenging task. Concrete is a quasi- brittle material and has different behavior in compression and tension. Poissons ratio for concrete was assumed to be
0.15 for all the seven beams. for the convience the open shear transfer coefficient used in this study was equal to
0.4 and closed shear transfer coefficient used is 0.8. For concrete stress – strain curve are plotted and non-linear property are provided based on Mac Gregery Equation. Average material property of different elements are given in the table 2.
Table 2. Material property of different elements
Material
E (MPa)
Poissons ratio
Concrete
38609
0.15
Steel (N12)
2×105
0.3
Steel(R5)
2×105
0.3
CFRP Elements
2.15×105
0.35
-
Steel Reinforcement:
The modulus of elasticity of the steel rebars (i.e for 10 mm and 12mm diameter bars) used for the study was 2x 105 MPa and the poissons ratio for steel reinforcement was assumed to be 0.3 for all beams. The stressstrain relationship for steel reinforcement is shown in table 3 below.
Table 3. Stressstrain relationship for steel reinforcement
Stress
Strain
0.0015
300
0.002
400
0.0025
440
0.0032
480
0.0044
500
0.022
510
-
CFRP Elements
The modulus of elasticity of the CFRP elements used for the study is 2.15x 105 MPa and the poissons ratio for CFRP Elements was assumed to be
0.35 as shown in figure 5.12. The stress strain relationship for steel reinforcement are plotted in fig. 5
Fig. 5 Stress strain graph of CFRP elements
6 RESULT AND DISCUSSION
For ANSYS, deflections are measured at the same location as for the experimental beams. Fig 6 (a) to
(d) show the load-deflection plots from the finite element analyses as per the order such as CB, strap only, sheet only, strap+sheet and the experimental results from the previous studies for all the beams.
14
0
12
0
10
0
80
60
14
0
12
0
10
0
80
60
ansy
ansy
Experim e
Experim e
0 5 10 15
Midspan defelction (mm)
0 5 10 15
Midspan defelction (mm)
14
0
12
0
10
0
80
60
40
14
0
12
0
10
0
80
60
40
ansy
Exper i
ment
ansy
Exper i
ment
0 5 10 15
Midspan deflection (mm)
0 5 10 15
Midspan deflection (mm)
Load
Load
Load
Load
(b)
(a)
factors that may cause the stiffness in the finite element models such as microcracks and slip.
15
0
15
0
Experi m ental
Experi m ental
5
0
5
0
0
0
10
Midsp(acn)deflection
10
Midsp(acn)deflection
2
2
14
0
13
0
12
0
11
0
10
0
90
80
70
60
50
14
0
13
0
12
0
11
0
10
0
90
80
70
60
50
Contro l
Contro l
15
15
Load
Load
Fig. 7 shows the load – deflection plots of Control beam and the beam having partially bonded CFRP strap. The midspan deflection of the finite element analysis of control beam is slightly less than that of midspan deflection of the beam with strap. The ultimate load for the finite element analysis of control beam is 11% higher than the ultimate load of beam retroffited using CFRP
Midspan deflection
Stra
0
Stra
0
5
5
10
10
15
15
10
10
5
5
Exp e
Exp e
0
0
0
0
1
1
2
2
3
3
Load
Load
Load
Load
Midspan deflection
(d)
Fig.6 Load-deflection plot of ANSYS v/sexperimental value
In general, the load – deflction plots for all four beams from the finite element analyses agree quite well with the experimental data. or the four beams, the finite element load – deflection plots in the linear range are stiffer than the experimental plots. There are several
Midspan defelction (mm)
Midspan defelction (mm)
Fig. 7 Load-deflection plots of Control beam and the beam having partially bonded CFRP strap
Fig 8 shows the load – deflection plots of the beam having partially bonded CFRP strap and fully bonded CFRP strap. The midspan deflection of the finite element analysis partially bonded CFRP strap is slightly
greater than that of midspan deflection of the beam with fully bonded CFRP strap. But the ultimate load of the fully bonded CFRP strap is 20% higher than that of partially bonded CFRP strap
15
0
Partiall
y
15
0
Partiall
y
Fully Bonde
0
Fully Bonde
0
0
Midspan deflection
1
0
Midspan deflection
1
5
5
5
5
1
1
Load
Load
Fig 7 Load-deflection plots of the beam having partially bonded CFRP strap and fully bonded CFRP strap
Load
Load
Fig 8 shows the load-deflection plots of the beam having one layer of CFRP strap three layer of CFRP strap and five layer of CFRP strap. Here the midspan deflection of the finite element analysis of one layer of CFRP strap is slightly greater than that of midspan deflection of the beam with three layer of CFRP strap which is then again greater than the midspan deflection of five layer of CFRP strap. Difference between the midspan deflection of one layer of CFRP strap and five layer of CFRP strap is approximately 36%
16
0
14
0
12
0
10
0
80
60
One layer
Three layer Five
16
0
14
0
12
0
10
0
80
60
One layer
Three layer Five
0 5 10 15
Miidspan deflection (mm)
0 5 10 15
Miidspan deflection (mm)
Fig. 8 Load-deflection plots of the beam having one layer of CFRP strap three layer of CFRP strap and five layer of CFRP strap
7 CONCLUSION
The mid span deflection at ultimate state was predicted using ANSYS 14.5 software for the seven concrete beams reinforced with steel bars subjected to three
point loading and four point loading. It is then compared with the predicted results obtained from previous studies. Conclusions for finite element models of the full-scale beams is as follows:
-
-
Carry out analytical study using ANSYS 14.5 software for the prediction of the mid span deflection of seven concrete beams
-
The general behavior of the finite element models represented by the load-deflection plots at midspan show good agreement with the test data from the full-scale beam tests. However, the finite element models show slightly more stiffness than the test data in both the linear and nonlinear ranges. The effects of bond slip (between the concrete and steel reinforcing) and microcracks occurring in the actual beams were excluded in the finite element models,
contributing to the higher stiffness of the finite element models.
-
Final loads from the finite element analyses are lower than the ultimate loads from the experimental results by 3% – 12%. This is probably due in part to neglecting the inclined portions of the steel reinforcement; ignoring the effects of concrete toughening mechanisms; and using assumed materials properties values instead of measured values.
-
Increase in the layer of CFRP strap will strengthen the beam upto a particular limit only. After that the increase in the number of layer may not affect the beam.
-
The beam retrofitted using CFRP straps will carry more load as compared with the control beam. Thus the control beam can be strengthened by using CFRP strap.
REFERENCE
-
Yapa, H. D. and Lees, J. M., Rectangular Reinforced Concrete Beams Strengthened with CFRP Straps, Journal Composites Construction, 2014, vol. 18(1), pp. 1 10
-
Ronagh, H.R. and Eslami, A., Flexural retrofitting of RC buildings using GFRP/CFRP A comparative study,
Composites: Part B Eng., 2013, vol. 46, pp 188196
-
Sen, T. and Reddy, H. N. J., Strengthening of RC beams in flexure using natural jute fibre textile reinforced composite system and its comparative study with CFRP and GFRP
-
strengthening systems, International Journal of Sustainable Built Environment, 2013, vol. 2, pp 4155
-
Hashemi, S. and Al-Mahaidi, R., Experimental and finite element analysis of flexural behavior of FRP-strengthened RC beams using cement-based adhesives, Construction and Building Materials, 2011, vol. 26, pp 268273
-
Kim, H.S., and Shin, Y.S., Flexural behavior of reinforced concrete (RC) beams retrofitted with hybrid fiber reinforced polymers (FRPs) under sustaining loads, Composite Structures, 2011, vol. 93, pp 802811
-
Obaidat, Y.T., Heyden, S., Dahlblom, O., Farsakh., G. A. and Jawad, Y. A., Retrofitting of reinforced concrete beams using composite laminates, Construction of building materials, 2011, vol. 25, pp 591 597
-
Hoult, N. A., and Lees, J. M., Time-Dependent Behavior of RC Beams Retrofitted with CFRP Straps, Journal Composites Construction, 2011 , vol. 15, pp 75-84
-
Godat, A, Qu, Z., Lu, X. Z., Labossiere, P., Ye, L. P. and Neale,
K. W., Size Effects for Reinforced Concrete Beams Strengthened in Shear with CFRP Strips, Journal Composites Construction, 2010 , vol. 14, pp 260-271
-
Kothandaraman, S. and Vasudevan, G., Flexural retrofitting o f RC beams using external bars at soffit level An experimental study, Construction and Building materials, 2010, vol. 24, pp 22082216
-
Farhat, F. A., Nicolaides, D., Kanellopoulos, A. and Karihaloo,
B. L., Behavior of RC Beams Retrofitted with CARDIFRC after Thermal Cycling, Journal of Materials in Civil Engineering , 2010, vol . 22, pp 21-28
-
Hoult, N. A., and Lees, J. M., Efficient CFRP Strap Configurations for the Shear Strengthening of Reinforced Concrete T-Beams, Journal Composites Construction, 2009, vol. 13, pp 45-52
-
Benjeddou, O., Ouezdou, M. B., and Bedday, A., Damaged RC beams repaired by bonding of CFRP laminates, Construction and Buildimg Materials, 2007, vol. 21, pp 1301
1310
-
Al-Amery, R. and Al-Mahaidi, R., Coupled flexuralshear retrofitting of RC beams using CFRP straps, Composite Structures, 2006, vol. 75, pp 457-464
-
Bonfiglioli, B., Pascale, G. and Mingo, S. M. D., Dynamic testing of reinforced concrete beams damaged and repaired with fiber reinforced polymer sheets, Journal of Materials in Civil Engineering , 2004, vol . 16, pp 400 406
-
Pham, H. and Al-Mahaidi, R., Experimental investigation into flexural retrofitting of reinforced concrete bridge beams using FRP composites, Composite Structures, 2004, vol. 66, pp 617 625