
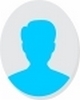
- Open Access
- Authors : Thushal Babukumar , Raja Reddy
- Paper ID : IJERTV12IS040190
- Volume & Issue : Volume 12, Issue 04 (April 2023)
- Published (First Online): 27-04-2023
- ISSN (Online) : 2278-0181
- Publisher Name : IJERT
- License:
This work is licensed under a Creative Commons Attribution 4.0 International License
Defining System Requirements for Model Based Design for Automotive Controllers
Thushal Babukumar Dept of Electrical Engg, PES Engg College Bangalore, India
Raja Reddy
Dept of Electrical Engg, PES Engg College Bangalore, India
Abstract Model-Based Design (MBD) has become increasingly popular in the development of automotive controllers due to its ability to improve the efficiency and accuracy of the development process. However, successful implementation of MBD relies heavily on the definition of clear and comprehensive system requirements. The purpose of this paper is to outline a framework for defining system requirements for MBD in automotive controller development. First, the paper provides an overview of MBD and its benefits in automotive controller development. It then discusses the importance of system requirements in the MBD process, highlighting the need for a clear understanding of the system's functionality, constraints, and performance requirements. The paper proposes a step-by-step approach for defining system requirements for MBD, which includes identifying system stakeholders and their needs, establishing system boundaries, defining system functions and performance requirements, and documenting system constraints. The paper also discusses the importance of validation and verification of the system requirements, as well as the need for continuous refinement throughout the development process. Finally, the paper provides examples of how the proposed framework can be applied to the development of automotive controllers using MBD. The examples demonstrate the importance of defining clear and comprehensive system requirements in the successful implementation of MBD in automotive controller development. Overall, this paper provides a valuable framework for defining system requirements for MBD in automotive controller development. The proposed approach can help developers to improve the efficiency and accuracy of the development process, resulting in higher quality and more reliable automotive controllers.
Keywords Model Based Design (MBD), System Requirements, Automotive Controllers, Electronic Control Units (ECUs)
INTRODUCTION
Model-Based Design (MBD) has revolutionized the development of automotive controllers, enabling faster and more accurate design iterations and improved quality of the final product. MBD involves the creation of a model that represents the system being designed, which is then used to simulate and test the system's behavior before it is built. The use of MBD in automotive controller development has become increasingly popular due to the advantages it offers, such as reducing development time and cost, improving system performance, and enabling easier integration of complex systems.
However, the success of MBD relies heavily on the definition of clear and comprehensive system requirements. The system
requirements define the functionality, constraints, and performance requirements of the system, which are used as the basis for designing and testing the model. Without well- defined system requirements, the MBD process can become inefficient, leading to delays and errors in the final product [1-5].
The purpose of this paper is to provide a framework for defining system requirements for MBD in automotive controller development. The framework outlines a step-by- step approach for defining system requirements, from identifying system stakeholders to documenting system constraints. By following this framework, developers can ensure that they have a clear and comprehensive understanding of the system requirements, which can help to reduce errors and improve the efficiency of the development process.
The paper begins by providing an overview of MBD and its benefits in automotive controller development. It then discusses the importance of system requirements in the MBD process, highlighting the need for a clear understanding of the system's functionality, constraints, and performance requirements. The paper emphasizes the importance of system requirements in enabling effective communication between stakeholders and ensuring that the final product meets the needs of all stakeholders. The paper then proposes a step-by-step approach for defining system requirements for MBD, which includes identifying system stakeholders and their needs, establishing system boundaries, defining system functions and performance requirements, and documenting system constraints. The paper explains each step in detail and provides examples to illustrate how the framework can be applied in practice [6].
The paper also discusses the importance of validation and verification of the system requirements. Validation involves ensuring that the system requirements accurately reflect the needs of the stakeholders, while verification involves checking that the model meets the system requirements. The paper emphasizes the need for continuous refinement of the system requirements throughout the development process to ensure that they remain relevant and accurate [7-12].
Finally, the paper provides examples of how the proposed framework can be applied to the development of automotive controllers using MBD. The examples demonstrate the importance of defining clear and comprehensive system requirements in the successful implementation of MBD in
automotive controller development. System V-Model is represented in figure 1 below.
Figure 1. System V-Model Representation Block Diagram
In conclusion, the paper provides a valuable framework for defining system requirements for MBD in automotive controller development. The proposed approach can help developers to improve the efficiency and accuracy of the development process, resulting in higher quality and more reliable automotive controllers [13].
-
DESIGN COMPLEXITY MBD DESIGN CONSTRAINTS
The technical design complexity for defining system requirements for Model-Based Design (MBD) in automotive controllers can be considered moderate to high. This is because the process involves several technical aspects, including identifying stakeholders, defining system boundaries, specifying system functions and performance requirements, and documenting system constraints.
In addition, MBD itself is a complex process that requires a thorough understanding of the system being designed and the modeling tools being used. The design of the model must be carefully crafted to accurately represent the system, and this requires knowledge of both the system and the modeling tools. Moreover, the system requirements must be validated and verified, which involves the use of specialized techniques and tools to ensure that the model meets the specified requirements. This can be a time-consuming and challenging process, particularly in complex systems with many stakeholders and requirements [14-22].
Overall, the technical design complexity for defining system requirements for MBD in automotive controllers requires a high level of technical expertise and attention to detail. The success of the process depends on the ability of the design team to accurately define the system requirements, validate and verify the model, and continuously refine the requirements throughout the development process.
-
APPROACH TO DEFINE SYSTEM REQUIREMENTS FOR MBD
Defining system requirements is a crucial step in the Model- Based Design (MBD) process for automotive controllers. The following is a step-by-step approach that can be used to define system requirements for MBD in automotive controllers:
-
Identify System Stakeholders: The first step is to identify the stakeolders who will be affected by the automotive controller. This includes end-users, customers, designers, and other stakeholders who may have a vested interest in the performance and functionality of the automotive controller. The purpose of this step is to understand the needs and requirements of all stakeholders, and to ensure that their needs are reflected in the system requirements.
-
Establish System Boundaries: The second step is to establish the boundaries of the system. This includes defining the scope of the system, identifying the inputs and outputs of the system, and determining how the system will interact with other systems. This step helps to ensure that the system requirements are clearly defined and that there is a clear understanding of the system's functionality [23-25].
-
Define System Functions and Performance Requirements: The third step is to define the functions that the system must perform and the performance requirements that the system must meet. This includes identifying the key features of the automotive controller, specifying the functional requirements of the system, and defining the performance metrics that the system must meet. This step helps to ensure that the system requirements accurately reflect the needs of the stakeholders [26- 30].
-
Document System Constraints: The fourth step is to document the constraints that may impact the development of the automotive controller. This includes identifying any physical, technical, or operational constraints that may limit the performance or functionality of the system. Constraints may include factors such as cost, size, weight, or power consumption. This step helps to ensure that the system requirements are realistic and achievable [31-35].
-
Validate and Verify System Requirements: The fifth step is to validate and verify the system requirements. This involves ensuring that the system requirements accurately reflect the needs of the stakeholders, that the requirements are complete and consistent, and that the requirements can be verified through testing or simulation. This step helps to ensure that the system requirements are accurate and that the final product meets the needs of the stakeholders.
-
Refine System Requirements: The final step is to continuously refine the system requirements throughout the development process. This involves
updating the requirements as needed, based on feedback from stakeholders, changes in technology, or changes in the design of the system. This step helps to ensure that the system requirements remain relevant and accurate throughout the development process.
In summary, the step-by-step approach for defining system requirements for MBD in automotive controllers involves identifying stakeholders, establishing system boundaries, defining system functions and performance requirements, documenting system constraints, validating and verifying the system requirements, and continuously refining the system requirements throughout the development process. By following this approach, design teams can ensure that they have a clear and comprehensive understanding of the system requirements, which can help to reduce errors and improve the efficiency of the development process.
-
-
VERIFICATION AND VALIDATION OF SYSTEM REQUIREMENTS
Validation and verification of system requirements are critical steps in the Model-Based Design (MBD) process for automotive controllers. Validation refers to the process of ensuring that the requirements accurately reflect the needs of the stakeholders and that they can be met by the system, while verification refers to the process of ensuring that the system meets the specified requirements.
The importance of validation and verification of the system requirements can be summarized as follows:
-
Ensure Accuracy: Validation and verification of system requirements are essential to ensure that the requirements accurately reflect the needs of the stakeholders. Without proper validation and verification, the system may fail to meet the needs of the stakeholders or may not perform as expected.
-
Reduce Errors: Validation and verification can help to reduce errors in the design of the system. By validating and verifying the system requirements, design teams can identify errors and correct them before the system is developed. This can help to reduce the cost of development and improve the quality of the final product.
-
Improve Efficiency: Validation and verification can improve the efficiency of the design process. By identifying errors early in the process, design teams can avoid costly and time-consuming rework later in the development process. This can help to reduce the overall time to market and improve the efficiency of the design process.
-
Ensure Compliance: Validation and verification of system requirements are often required by regulatory agencies or industry standards. By ensuring that the system requirements are validated and verified, design teams can ensure compliance with these requirements and standards.
-
Improve Communication: Validation and verification of system requirements can improve communication between stakeholders. By validating and verifying the system requirements, design teams
can ensure that all stakeholders have a clear understanding of the system requirements and the expected performance of the system. This can help to improve collaboration and ensure that the final product meets the needs of all stakeholders.
In summary, validation and verification of system requirements are critical steps in the MBD process for automotive controllers. By ensuring the accuracy of the system requirements, reducing errors, improving efficiency, ensuring compliance, and improving communication, design teams can ensure the successful development of a high- quality automotive controller that meets the needs of all stakeholders.
-
-
REFINEMENT OF REQUIREMENTS THROUGH THE DEVELOPMENT PROCESS
Continuous refinement of the system requirements throughout the development process is an essential part of the Model-Based Design (MBD) process for automotive controllers. It involves continuously updating and improving the system requirements based on feedback from stakeholders, changes in technology, or changes in the design of the system. The importance of continuous refinement of the system requirements can be summarized as follows:
-
Respond to Stakeholder Feedback: As the development process progresses, stakeholders may provide feedback on the system requirements. This feedback may identify new requirements, clarify existing requirements, or suggest changes to the requirements. By continuously refining the system requirements, design teams can ensure that the system meets the needs of all stakeholders.
-
Adapt to Changes in Technology: Technology is constantly evolving, and new technologies may become available during the development process. By continuously refining the system requirements, design teams can ensure that the system takes advantage of new technologies and remains up-to- date.
-
Address Design Changes: The design of the system may change during the development process due to changes in the requirements, changes in technology, or other factors. By continuously refining the system requirements, design teams can ensure that the requirements remain aligned with the design of the system.
-
Ensure Relevance: As the development process progresses, the system requirements may become outdated or irrelevant. By continuously refining the system requirements, design teams can ensure that the requirements remain relevant and aligned with the needs of the stakeholders.
-
Improve Quality: By continuously refining the system requirements, design teams can improve the quality of the final product. Refining the requirements can help to identify errors or omissions in the initial requirements and can help to ensure that the final product meets the needs of all stakeholders.
In summary, continuous refinement of the system requirements throughout the development process is essential to ensure the success of the MBD process for automotive controllers. By responding to stakeholder feedback, adapting to changes in technology, addressing design changes, ensuring relevance, and improving quality, design teams can ensure that the final product meets the needs of all stakeholders and is of the highest possible quality.
-
-
CONCLUSION
In conclusion, defining system requirements for Model-Based Design (MBD) for automotive controllers is a complex process that requires a step-by-step approach to ensure that the requirements accurately reflect the needs of the stakeholders and can be met by the system. The process involves identifying the stakeholder needs, creating a conceptual model, developing a functional model, and defining the system requirements.
Validation and verification of the system requirements are critical steps in the MBD process. By ensuring the accuracy of the system requirements, reducing errors, improving efficiency, ensuring compliance, and improving communication, design teams can ensure the successful development of a high-quality automotive controller that meets the needs of all stakeholders.
Continuous refinement of the system requirements throughout the development process is also essential to ensure the success of the MBD process for automotive controllers. By responding to stakeholder feedback, adapting to changes in technology, addressing design changes, ensuring relevance, and improving quality, design teams can ensure that the final product meets the needs of all stakeholders and is of the highest possible quality. In summary, the MBD process for automotive controllers is a highly iterative process that requires continuous refinement of the system requirements throughout the development process. The process involves a step-by-step approach to defining the system requirements, including identifying stakeholder needs, creating a conceptual model, developing a functional model, and defining the system requirements.
Validation and verification of the system requirements are critical steps that ensure the system meets the needs of stakeholders and regulatory requirements. Continuous refinement of the system requirements ensures that the final product remains aligned with stakeholder needs, adapts to changes in technology, and is of the highest possible quality. Overall, a well-defined and continuously refined set of system requirements is essential for the successful development of a high-quality automotive controller that meets the needs of all stakeholders.
REFERENCES
[1] Cerf, V. G. (2018). A comprehensive self-driving car test. Communications of the ACM, 61(2), 7-7. [2] Buyval, A., Gabdullin, A., Mustafin, R., & Shimchik, I. (2018, May). Realtime vehicle and pedestrian tracking for didi udacity self- driving car challenge. In 2018 IEEE international conference on robotics and automation (ICRA) (pp. 2064-2069). IEEE. [3] Shreyas, V., Bharadwaj, S. N., Srinidhi, S., Ankith, K. U., & Rajendra, A. B. (2020). Self-driving cars: An overview of various autonomous driving systems. Advances in Data and Information Sciences: Proceedings of ICDIS 2019, 361-371. [4] Woodward, B., & Kliestik, T. (2021). Intelligent transportation applications, autonomous vehicle perception sensor data, and decision-making self-driving car control algorithms in smart sustainable urban mobility systems. Contemporary Readings in Law and Social Justice, 13(2), 51-64. [5] Kosuru, V. S. R., Venkitaraman, A. K., Chaudhari, V. D., Garg, N., Rao, A., & Deepak, A. (2022, December). Automatic Identification of Vehicles in Traffic using Smart Cameras. In 2022 5th International Conference on Contemporary Computing and Informatics (IC3I) (pp. 1009-1014). IEEE. [6] Zhang, Y., Wang, J., Wang, X., & Dolan, J. M. (2018). Road- segmentation-based curb detection method for self-driving via a 3D- LiDAR sensor. IEEE transactions on intelligent transportation systems, 19(12), 3981-3991. [7] Wu, S., Hadachi, A., Vivet, D., & Prabhakar, Y. (2021). This is the way: Sensors auto-calibration approach based on deep learning for self-driving cars. IEEE Sensors Journal, 21(24), 27779-27788. [8] A. K. Venkitaraman and V. S. R. Kosuru, "Electric Vehicle Charging Network Optimization using Multi-Variable Linear Programming and Bayesian Principles," 2022 Third International Conference on Smart Technologies in Computing, Electrical and Electronics (ICSTCEE), Bengaluru, India, 2022, pp. 1-5, doi: 10.1109/ICSTCEE56972.2022.10099649. [9] Lin, M., Yoon, J., & Kim, B. (2020). Self-driving car location estimation based on a particle-aided unscented Kalman filter. Sensors, 20(9), 2544. [10] Lutin, J. M., Kornhauser, A. L., & MASCE, E. L. L. (2013). Therevolutionary development of self-driving vehicles and implications for the transportation engineering profession. Institute of Transportation Engineers. ITE Journal, 83(7), 28.
[11] V. S. R. Kosuru and A. K. Venkitaraman, "Preventing the False Negatives of Vehicle Object Detection in Autonomous Driving Control Using Clear Object Filter Technique," 2022 Third International Conference on Smart Technologies in Computing, Electrical and Electronics (ICSTCEE), Bengaluru, India, 2022, pp. 1-6, doi: 10.1109/ICSTCEE56972.2022.10100170. [12] Paravarzar, S., & Mohammad, B. (2020). Motion prediction on self- driving cars: A review. arXiv preprint arXiv:2011.03635. [13] Kosuru, V. S. R., & Kavasseri Venkitaraman, A. (2023). A Smart Battery Management System for Electric Vehicles Using Deep Learning-Based Sensor Fault Detection. World Electric Vehicle Journal, 14(4), 101. [14] Yoganandhan, A., Subhash, S. D., Jothi, J. H., & Mohanavel, V. (2020). Fundamentals and development of self-driving cars. Materials today: proceedings, 33, 3303-3310. [15] Chopra, R., & Roy, S. S. (2020). End-to-end reinforcement learning for self-driving car. In Advanced Computing and Intelligent Engineering: Proceedings of ICACIE 2018, Volume 1 (pp. 53-61). Springer Singapore. [16] Venkitaraman, A. K., & Kosuru, V. S. R. (2023). Resilence of Autosar-Complaint Spi Driver Communication as Applied to Automotive Embedded Systems. European Journal of Electrical Engineering and Computer Science, 7(2), 44-47. [17] Reke, M., Peter, D., Schulte-Tigges, J., Schiffer, S., Ferrein, A., Walter, T., & Matheis, D. (2020, January). A self-driving car architecture in ROS2. In 2020 International SAUPEC/RobMech/PRASA Conference (pp. 1-6). IEEE. [18] Kosuru, V. S. R., & Venkitaraman, A. K. CONCEPTUAL DESIGN PHASE OF FMEA PROCESS FOR AUTOMOTIVE ELECTRONIC CONTROL UNITS. [19] Lee, U., Jung, J., Shin, S., Jeong, Y., Park, K., Shim, D. H., & Kweon, I. S. (2016, October). EureCar turbo: A self-driving car that can handle adverse weather conditions. In 2016 IEEE/RSJ International Conference on Intelligent Robots and Systems (IROS) (pp. 2301-2306). IEEE. [20] Bloom, C., Tan, J., Ramjohn, J., & Bauer, L. (2017, July). Self- driving cars and data collection: Privacy perceptions of networked autonomous vehicles. In Symposium on Usable Privacy and Security (SOUPS). [21] Kosuru, V. S. R., & Venkitaraman, A. K. (2022). Evaluation of Safety Cases in The Domain of Automotive Engineering. International Journal of Innovative Science and Research Technology, 7(9), 493-497. [22] Rathore, A. (2016). State-of-the-art self driving cars. International Journal of Conceptions on Computing and Information Technology, 4(1), 1-5. [23] Venkitaraman, A. K., & Kosuru, V. S. R. (2022). A review on autonomous electric vehicle communication networks-progress, methods and challenges. [24] Estl, H. (2015). Paving the way to self-driving cars with advanced driver assistance systems. Worldwide Systems Marketing for Advanced Driver Assistance Systems (ADAS), Texas Instruments. [25] Rahul, V. S. (2022). Kosuru; Venkitaraman, AK Integrated framework to identify fault in human-machine interaction systems. Int. Res. J. Mod. Eng. Technol. Sci, 4, 1685-1692. [26] Alshamrani, S. S., Alkhudadi, B. A., & Almtrafi, S. M. (2022). Cyberattacks on Self-Driving Cars and Surgical and Eldercare Robots. Security and Communication Networks, 2022. [27] Kosuru, V. S. R., & Venkitaraman, A. K. (2022). Developing a Deep Q-Learning and Neural Network Framework for Trajectory Planning. European Journal of Engineering and Technology Research, 7(6), 148-157. [28] Szikora, P., & Madarász, N. (2017, November). Self-driving cars The human side. In 2017 IEEE 14th international scientific conference on informatics (pp. 383-387). IEEE. [29] Venkitaraman, A. K., & Kosuru, V. S. R. (2023). Hybrid deep learning mechanism for charging control and management of Electric Vehicles. European Journal of Electrical Engineering and Computer Science, 7(1), 38-46. [30] Alheeti, K. M. A., & McDonald-Maier, K. (2016, October). An intelligent intrusion detection scheme for self-driving vehicles based on magnetometer sensors. In 2016 International Conference for Students on Applied Engineering (ICSAE) (pp. 75-78). IEEE. [31] Park, J., Min, K. M., Kim, H., Hong, S. H., & Lee, M. G. (2022).Integrated Computational Materials Engineering for Advanced Automotive Technology: With Focus on Life Cycle of Automotive Body Structure. Advanced Materials Technologies, 2201057.
[32] Bramberger, R., Martin, H., Gallina, B., & Schmittner, C. (2020). Co-engineering of safety and security life cycles for engineering of automotive systems. ACM SIGAda Ada Letters, 39(2), 41-48. [33] Broch, F., Warsen, J., & Krinke, S. (2015). Implementing life cycle engineering in automotive development as a helpful management tool to support design for environment. Life cycle management, 319- 329. [34] Kosuru, V. S. R., & Venkitaraman, A. K. (2023). Advancements and challenges in achieving fully autonomous self-driving vehicles. World Journal of Advanced Research and Reviews, 18(1), 161-167. [35] Krinke, S. (2011). Implementing life cycle engineering efficiently into automotive industry processes. In Glocalized Solutions for Sustainability in Manufacturing: Proceedings of the 18th CIRP International Conference on Life Cycle Engineering, Technische Universität Braunschweig, Braunschweig, Germany, May 2nd-4th, 2011 (pp. 11-16). Springer Berlin Heidelberg.