
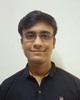
- Open Access
- Authors : Sumeet Rajendra Shelke , Saurav Vijay Patil , Harsh Sanjay Jha , Sneha Shirke
- Paper ID : IJERTV11IS060006
- Volume & Issue : Volume 11, Issue 06 (June 2022)
- Published (First Online): 09-06-2022
- ISSN (Online) : 2278-0181
- Publisher Name : IJERT
- License:
This work is licensed under a Creative Commons Attribution 4.0 International License
Design, Analysis and Manufacturing of Zero Turn Mode
Sumeet Rajendra Shelke
Department of Mechanical Engineering SOET, Sandip University
Nashik, India
Harsh Sanjay Jha
Department of Mechanical Engineering SOET, Sandip University
Nashik, India
Saurav Vijay Patil
Department of Mechanical Engineering SOET, Sandip University
Nashik, India
Prof. Sneha Shirke
Professor, Department of Mechanical Engineering SOET, Sandip University
Nashik, India
Abstract: Today as the population is increasing demand for vehicles are also increasing, which lead to problem like traffic or overpopulated area. Modern development has led to limited areas or congested area causes people to face the problems like car parking. To overcome this issue a solution is proposed and thus the concept of zero turn mechanism has been introduced. Zero turn mechanism enables user to take a Zero-turn in by keeping the position of vehicle constant. The vehicle will rotate around its vertical axis to face the direction the user wants to go in. In this concept wheels are mounted to front axles are turned opposite to each other, and so are the wheels connected to the rear axle. The wheels on the left half of the vehicle rotate in one direction and the other half in the opposite direction which leads to zero turn. In this project, Wheel hubs are connected to tie rod, tie rod to motor horn and motor horn connected to SG90 servo motor, for this project purpose servo motor is connected to Arduino. By using Arduino program several modes can be achieved like In-phase steering, also help in reducing turning radius of a vehicle along with having Zero Turn mode. This mechanism is very useful in congested areas or over crowded parking lot.Designed in SOLIDWORK, Static structural analyzed in Ansys.
Keywords Zero turn, Steering, Mechanism, steering, Arduino program.
-
In this condition, the tie rod will shift to another end and angle of a wheel is so set that the vehicles move in a circle of zero radii.
The objective of mechanism is: –
-
To show zero turn mechanism using tie rod, motor horn, and motor.
-
To solve the problem of parking in congested areas or movement of vehicles in limited area.
-
DESIGN OF ZERO TURN MODE
-
INTRODUCTION
In this paper we have shown working of zero turn mode using Arduino and Servo Motors. Zero turn is done by turning driven wheels at the same angle in opposite direction. By steering the rear wheels in the direction opposite the front wheels at low speeds, turning radius is greatly reduced. So, vehicle can be turned in the space equal to the length of the vehicle itself. In a typical front wheel steering system, the rear wheels do not turn in the direction of the curve and thus curb on the efficiency of the steering. The concept is to get zero turn mode using programming through a single push button, which is more convenient for the vehicle. As the vehicle rotates zero-turn, it is very useful to turn the vehicle in narrow space, parking problems at malls, traffic areas and back turning on narrow roads. Zero-turn vehicles are: –
-
-
-
These vehicles provide circular path vehicles turn at the same place where its standing.
Fig 2 . Zero Turn Mode and Components Assembly
-
Tie Rod:-
-
It is connected in between the Tyre hub and motor horn.
-
If tie is not regularly inspected then problems like Tyre wear, Vibration, shaking and vehicle pulling to one side will occur.
Fig 2.1 Tie Rod
-
-
Link Housing:-
-
It is connected to motor horn through a rod.
Fig 2.2 Link Housing
-
-
Motor Horn:-
-
It is connected in between Motor and Tie rod
-
Motor rotates the motor horn, which leads to movement of tie rod.
Fig 2.3 Motor Horn
-
-
Axial Joint Holder:-
It consists of axis joint out
It is connected through link sphere to tie rod
Fig 2.4 Axis Joint Holder
2.5 Axis Joint:-
Axis joint is inside the axis joint holder
It is directly connected to tyre
It consists of axis joint inside with consisting of pin
Fig 2.5 Axis Joint
-
Motor :-
-
Motor is connected to motor horn.
-
Motor helps the movements of tyre to achieve zero turn mechanism.
-
Fig 2.6 Servo Tower pro (SG90) Motor
-
n: –
-
Pin goes inside an Axis joint inside and after assembly it is placed inside axis joint out
-
Pin is fixed so that it can help in movement of tyre.
-
Fig 2.7 Pin
-
Axis joint inside: –
-
It helps in moving of tyre as the pin is fixed.
Fig 2.8 Axis Joint Inside
-
-
Link Sphere: –
-
It provides smooth movement of tie rod connected to axis holder.
Fig 2.9 Link Sphere
-
-
Arduino Board: –
-
It is used for tyre to provide the modes.
-
It is a microcontroller board and will help in achieving the zero-turn mechanism.
-
The board is equipped with sets of digital and analogue input/output (I/O) pins that may be interfaced to various expansion boards (shields) and other circuits. The board has 14 Digital pins,
6 Analog pins, and programmable with the Arduino IDE (Integrated Development Environment) via a type B USB cable.
Fig 2.10 Arduino Board
-
ANALYSIS
-
FEA Analysis of the Tie Rod Design
Finite element meshing is one of the geometric input conditions while carrying an FEA and it involves discretization of a area being in one, two or three dimensions. In other words, Meshing is a process in FEA in which the model to be analysed is branched into lower separate elements. The mesh sizes used greatly affect the results acquired in finite element analysis. altogether, discretization error reduces as the mesh is made finer and hence a more accurate result is acquired. still, the finer the mesh sizes, the additional the calculation time is needed. As the mesh sizes are meliorated, the results attained keeps changing until a point is reached when added refinement of the mesh produces little or no change in the results attained after taking a long time for the solver to induce results. When additional reduction in the mesh size has little or no effect on the result attained, the mesh is said to have assembled and the answer at this point is taken as the result to the problem. Mesh generation in FEA can be accomplished directly from a solid model for complex part design in a three- dimensional( 3D) CAD analysis model. calculating on the computational ways the complex solid model may affect the computational time or come too complex to assay duly, some simplification with an applicable idealization process similar as reducing mesh size in the FE model was needed in order to reduce the extended calculation time.
Fig 1
TABLE 1
Model(A4)>Staticstructural(A5)>Solution(A6)>Total Deformation
Fig 2
Model(A4)>Static structural(A5) > Solution(A6) >Directional Deformation
Fig 3
TABLE 2
Model(A4)>Static structural(A5) >Solution(A6) > Equivalent Elastic Strain
Time (s)
Minimum
(m)
Maximum
(m)
Average
(m)
1.
3.5362e-011
7.647e-005
2.749e-006
Fig 4
Model(A4)>Static structural(A5) >Solution(A6)> Equivalent Stress
TABLE 3
Time (s)
Minimum
(m)
Maximum
(m)
Average (m)
1.
6.8779
1.1881e+007
5.3168e+005
Model(A4)>Static structural(A5)>Solution(A6)> Equivalent Stress
Time (s)
Minimum (m)
Maximum (m)
Average (m)
1.
0.
2.3072e-005
9.0138e-006
Fig 5
Model(A4)>Static structural(A5)>Solution(A6)> Total Deformation
TABLE 4
Model(A4)>Static structural(A5)>Solution(A6)> Total Deformation
Time (s)
Minimum (m)
Maximum (m)
Average (m)
1.
0.
9.6451e-007
1.5504e-007
Fig 6
Model (A4) > Static structural (A5) > Solution (A6 )> Directional Deformation
TABLE 6
Model(A4)>Static structural(A5)>Solution(A6)> Equivalent Elastic Strain
Time (s)
Minimum (m)
Maximum (m)
Average (m)
1.
2.1563E-009
2.0858e-005
2.9828e-006
Fig 8
Model(A4)>Static structural(A5)>Solution(A6)> Equivalent Stress
TABLE 7
Model(A4)>Staticstructural(A5)>Solution(A6)> Equivalent Stress
Time (s)
Minimum (m)
Maximum (m)
Average (m)
1.
166.87
4.1229e+006
5.6915e+006
TABLE 5
Model(A4)>Static structural(A5)>Solution(A6)> Directional Deformation
Time (s)
Minimum (m)
Maximum (m)
Average (m)
1.
-8.6705e-008
8.6329e-008
-9.8852e-010
Fig 7
Model(A4)> Static structural(A5)>Solution(A6)> Equivalent Elastic Strain
-
Material Data
Structural Steel:-
Density
7850
kgm^-3
Coefficient of thermal expansion
1.2e-
005C^-1
Specific Heat
434 JKg^-
1 C^-1
Thermal Conductivity
60.5 W m^-1 C^-1
Resistivity
1.7e-007
ohm m
Structural Steel > Constants
Structural Steel>Color
Red
Green
Blue
132
139
179
Structural Steel > Compressive Ultimate Strength
Structural Steel > S-N Curve
Compressive Ultimate Strength
0
Alternating Stress Pa
Cycles
Mean Stress Pa
3.999e+009
10
0
2.827e+009
20
0
1.896e+009
50
0
1.413e+009
100
0
1.069e+009
200
0
4.41e+008
2000
0
2.62e+008
10000
0
2.14e+008
20000
0
1.38e+008
1.e+005
0
1.14e+008
2.e+005
0
8.62e+007
1.e+006
0
Structural Steel > Compressive Yield Strength
Compressive Yield Strength Pa
2.5e+008
Structural Steel >Tensile Yield Strength
Tensile Yield Strength
2.5e+008
Structural Steel > Strain-life parameter
Strength Coefficie nt Pa
Strength Exponen t
Ductility Coefficie nt
Ductility Exponen t
Cyclic strength Coefficie nt Pa
Cyclic Strain Hardening Exponent
9.2e+008
-0.106
0.213
-0.47
1.e+009
0.2
Structural Steel > Tensile ultimate Strength
Structural Steel > Isotropic Relative Permeability
Relative Permeability
10000
Tensile Ultimate Strength
22
Structural Steel>Isotropic Elasticity
Youngs Modulus Pa
Poissons Ratio
Bulk Modulus Pa
Shear Modulus Pa
2.e+011
0.3
1.6667e+011
7.6923e+010
-
3D Printing
We 3D printed the parts using Ender 3 V2 using Prusa Slicer software (v2.4.0). Software gave us complete information about the time required by the ender 3 v2 to complete each part and also weight of the part.
Information of ENDER 3 v2: –
The firmware version used in ender 3 v2: – Ver 1.0.2. Build size of the machine: – 220*220*250 mm.
Machine Size: – 475*470*620mm. Machine Power: – 350W.
Net Weight: – 8KG.
Material used: -Polylactic Acid
After importing STL File into Pursa Slicer software it provided a G-Code file. G-code file through a memory card is inserted into Ender 3 V2 with settings given below:-
TABLE 3.3 3D printer setting before start of Printing
Sr no
Printer Setting Name
Setting
1
PLA temp
200-210°C
2
Bed Temp
60
3
1st layer height
0.4
4
Next layer height
0.15
5
Infill
30%
6
Speed
20mm/sec
7
Quantity/Parts
4
We 3D printed the following Parts:-
-
Axis Joint Out:-
-
Axis Holder:-
-
Link Housing:-
-
Pin :-
-
Link Sphere:-
-
-
-
CALCULATIONS
-
Motor Information
-
3 pole ferrites, all nylon gear
-
Top ball bearing
-
Operating Voltage: 4.8V~6.0V
-
Operating speed: 0.12sec/60 degree
-
Output torque: 1.6kg/cm 4.8V
-
Dimension: 21.5 x 11.8 x 22.7mm
-
Weight: 9g
-
-
Steering Force Calculation
Total mass = 1600 kg
Mass with driver = 1670 kg
Mass on Front wheels = 0.45 * 1670 =751 kg Mass on rear wheels = 0.55 * 1670 = 918.5 kg Corner mass front = 375.2 kg
Corner mass rear = 459.25 kg
Coefficient of friction = 0.4 when wet road =0.7 when dry road conditions
Taking 0.8 as coefficient of friction.
The basic concept is that the torque required to turn the whee should be more than the resisting torque by friction.
Force of friction (on one wheel)
= µ * g * corner mass front
=0.8 * 9.81 * 375.2 + 1250
=4194N —–(1)
Force of friction on rear wheels
= µ * g * corner mass rear
=0.8 * 9.81 * 459.25 + 1250
=4852N —–(2)
As this method of IC vehicle steer of the wheel will happen at kingpin axis. Not including scrub radius in this calculation.
=4852*2 + 4194*2
=9704+8388
=18092N
-
-
WORKING OF MODEL
-
-
The Experimental setup:-
It is divided into Two categorial conditions:-
-
Normal/Neutral Mode
-
Zero Turn Mode
1. Neutral Condition: – In the neutral mode the motor horn points towards 90 degrees and any small radius turn will reflect the servo motor horn position according to the data captured by the steering wheel. This is the normal condition of steering system and for most of time this mode is activated.
Fig 5.1.1 Neutral Condition
Fig 5.1.2 Real Neutral Condition
2. Zero Turn Mode (ZTM):- The ZTM mode is a new concept on which this project is based. The 4 servo motors are taken to certain position as servo motor number 1 and 4 will point at 180 degrees while 2 and 3 will be at 0 degree to achieve favourable output.
Fig 5.2.1 Zero Turn Mode
Fig 5.2.2 Real Zero Turn Mode
-
-
Arduino And Connection To Servo Motors
Fig5.2 Arduino and Servo (SG90) Motor connection
-
Source Code For Microprocessor
int button=2;
#include <Servo.h> Servo servo1; Servo servo2; Servo servo3; Servo servo4;
void setup() { pinMode(button, INPUT); servo1.attach(3); servo2.attach(5); servo3.attach(6); servo4.attach(9);
}
void loop() {
// Normal Mode servo1.write(90); servo2.write(90); servo3.write(90); servo4.write(90); delay(5000);
// Zero turn Mode servo1.write(0); servo2.write(180); servo3.write(180); servo4.write(0); delay(5000);
}
RESULTS AND DISCUSSION
The report describes working of Zero Turn Mechanism using Arduino and 4 SG90 servo motors. The project works on overcoming a major drawbacks such as limited parking area, crowded areas or limited space for vehicle to move. The automization is done using Arduino UNO control board, in which program is uploaded through Arduino IDE, breadboard, jumper wires and servo motors. Zero Turn Mode works on single push button. By pushing the button, the vehicle provides zero turn.
The above mentioned zero turn mode is prototype. It is easy to use , cheap and cost effective. The Arduino programming is simple and can be modified. The Zero Turn Mode has been successfully designed and manufactured.
ACKNOWLEDGMENT
We would like to express our gratitude and appreciation to all those who helped us in completion of our project. Special thanks to project guide Prof. Sneha Shirke for providing us with the necessary help, suggestions and encouragement during completion of the project. We also sincerely thanks for the time spent proofreading and correcting our many mistakes. We sincerely thank our college for providing us the opportunity to develop our project. Last, but not the least, we would like to thank our friends for providing us the support and contributing in our project work.
REFERENCES
[1] J.M.Hughes,Arduino: A TechnicalReference, A Handbook for Technicians, Engineers, and Makers,Arduino Libraries(pages 1-12 and 157-211) [2] John Hoffman,MasteringArduino,A project-based approach to electronics, circuits, and Programming (Page 7-20 and 232-238) [3] Liza Wallach Kloski and Nick Kloski, HoneyPoint 3D,make: Getting Started with 3D printing, A Hands-on Guide to the Hardware, Software, and Service Behind the New Manufacturing Revolution. [4] http://auto.howstuffworks.com/jeep-hurricane [5] Arun Singh *, Abhishek Kumar, Rajiv Chaudhary, R. C. Singh [6] Kirpal Singh, Automobile Engineering, Standard publishers [7] Wheel Steering System Md. Danish Akhtar, 2013 [8] Zero Turn Four Wheel Steering System Er. Amitesh Kumar, Dr. DineshN. Kambale, Dec. 2014
[9] Study of 4 Wheel Steering Systems to Reduce Turning Radius and Increase Stability [10] Arunkumar S M1, Chandan Kumar Sahu2, Yubaraj G M3, Jahangeer A B4 360 Degree Wheel Rotation Vehicle International Journal of Latest Engineering Research and Applications (IJLERA) ISSN: 2455- 7137 Volume 02, Issue 05, May 2017, PP 75-81 [11] Mr. Sharad P. Mali1, Mr. Sagar Jadhav2, Prof.D.U.Patil3 Zero Turn Four Wheel Mechanism, International Engineering Research Journal (IERJ) Volume 2 Issue 2 Page 484-486, 2016, ISSN 2395-1621. [12] ShirsathSachin1, Jadhav Kiran2, Patil Rahul3, Mohite Abhilash4,D.D. Patil5STUDY OF ZERO-TURN VEHICLE International Conference On Emerging Trends In Engineering And Management Research, ICETEMR-16 23rd March 2016 ISBN: 978-81-932074-7-5. [13] Jaishnu Moudgil1,Shubhankar Mengi2, Mudit Chopra3, Dr.Jaswinder Singh4 360° Rotating Vehicle to overcome the Problem of Parking Space IJRMET Vol. 5, Issue 2, May-Oct 2015, ISSN: 2249-5762 [14] K. Lohith, Dr. S. R. Shankapal, M. H. Monish Gowda, Development of four-wheel steering system for a car, Volume 12, Issue 1, April 13. [15] International Journal of mechanical engineering & robotics research, National conference on Recent advances in Mechanical Engineering RAME -2013, Vol. 1, No.1, January 2014. [16] Xiaodong Wu, Member, IACSIT, Min Xu, and Lei Wang, Differential Speed Steering Control for Four-Wheel Independent Driving Electric Vehicle International Journal of Materials, Mechanics and Manufacturing, Vol. 1, No. 4, November 2013. [17] Allan Y. Lee, Performance of Four-Wheel-Steering Vehicle in Lane Change Maneuvers, California Institute of Technology. 5. D.Stajnko, P.Berk, B.Mursec, P.Vindis, The influence of different steering system on a wheel slips, Volume55 Issue 2 December 2012