
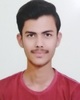
- Open Access
- Authors : Abhinav Mishra , Aniket Kumar Sahu
- Paper ID : IJERTV10IS010120
- Volume & Issue : Volume 10, Issue 01 (January 2021)
- Published (First Online): 25-01-2021
- ISSN (Online) : 2278-0181
- Publisher Name : IJERT
- License:
This work is licensed under a Creative Commons Attribution 4.0 International License
Design Analysis and Optimization of an All-Terrain Vehicle (ATV)
(Designing Frame, Knuckle and Suspension Arms)
Abhinav Mishra / B.Tech UG Student Department of Mechanical Engineering National Institute of Technology Raipur, Chhattisgarh
Aniket Kumar Sahu / B.Tech UG Student Department of Mechanical Engineering National Institute of Technology
Raipur, Chhattisgarh
Abstract The paper summarizes the steps taken in finalizing the design of an electric ATV, made for SAE BAJA which provides a platform for undergraduate students to apply the principles of engineering to expose their proficiency in the automotive world. The purpose of the paper is to calculate various boundary conditions on the frame, steering knuckle, suspension arms of a light ATV under extreme conditions and use them to improve the overall design which requires the minimum amount of material while providing a significant Factor of safety. An iterative approach using standard calculations & FEA is discussed in the study for simulation and optimization of the design. For all parts, stress & deformation analysis is performed. For design optimization in the knuckle, topology is done. Von mises Stress, total deformation and safety factor were calculated for each part under appropriate boundary conditions. The study discussed step by step calculations of forces on each component in detail and their simulations with an appropriate degree of precision. Following the methodology shown in the study will be useful in the development of a Light ATV, further, the suggested simulations will ensure the safety of the vehicle.
Keywords Von mises stress, Deformation, Safety factor, Design, Material Selections, FEA, Topology, Knuckle, Frame, Suspension Arms.
-
INTRODUCTION
As the name suggests an ATV is a vehicle that runs on tough terrains and hence every part of the vehicle was designed such that it can successfully withstand different types of loadings in off-road conditions without having any permanent deformation in it (i.e., von-mises stress value in the analysis should be very much lower than the yield stress of the material).
All the parts of the vehicle are designed in SOLIDWORKS 2018 and analyzed in ANSYS 19.2 with extreme boundary conditions and for setting up the steering and suspension geometry LOTUS shark was used.
-
RESEARCH GAP
A detailed calculation of boundary conditions and stepwise approach to design the parts of a light ATV which can withstand extreme loads was needed so that one can find a complete study in one paper, further current publications either fail to take all the required forces in consideration or fail to explain their calculations.
-
METHODOLOGY
Finalizing the design was an iterative process. Steps included in the process-
-
Preparation of basic design
-
Calculation of boundary conditions.
-
Analysis of the design under calculated boundary conditions using the finite element method in Ansys software
-
Optimization of design based on results obtained from the analysis
-
Again, applying step 3 and 4 on optimized design
-
Repeating the process to get the desired design
-
-
FRAME
The Frame is a structure made up of metal tubes whose main objective is to ensure the safety of the driver and carry different components of the vehicle such as powertrain, steering & suspension etc.
The design process of the frame can be divided into four steps-
-
Material and cross-section Selection
-
Designing the roll cage according to the rulebook,
-
Analysis of the roll cage with calculated boundary conditions.
-
Ergonomics check using PVC Pipes.
-
Material & Cross Section Selection
After considering each parameter like strength, weight, stiffness, cost, availability and a detailed market survey we shortlisted two AISI graded materials which were fulfilling the requirements first one was AISI 1018 steel and the second one was AISI 4130 steel, the details of both, as provided by the dealer, are given in the below table.
TABLE 1. COMPARISON BETWEEN AISI 4130 AND AISI 1018
Material
AISI 4130
AISI 1018
Yield Strength
659 MPa
418.82 MPa
Welding Method
TIG/MIG
SMAW/MIG
Carbon %
0.3
0.18
Density
7.85 g/cc
7.87 g/cc
We can see AISI 4130 provides good strength, but at the same time it is costlier than AISI 1018 and has poor weldability, and also after considering the fabrication constraints like available welding method (we used SMAW), availability of the material in local market and total cost, we selected AISI 1018 steel as our primary and secondary material because it is cheap, easily available, can be welded by SMAW and it also provides sufficient bending strength and bending stiffness to overcome the constraints for primary material as given in the rulebook.
The cross-section was selected after calculating bending strength and bending stiffness of primary material and the calculated figures are as below
Material Used – AISI 1018
Yield Strength (Sy) – 418.82 MPa
Young's Modulus of elasticity (E) – 205 GPa Outer diameter (Do) – 25.4 mm
Inner diameter (Di) – 19.4 mm (thickness = 3mm) Second moment of area (I) – 13478.64 mm4 Distance from central axis (c) – 12.7 mm
Calculated bending strength – 444.497 MPa Calculated bending stiffness – 2763.121 Nm2
We can see that bending strength and bending stiffness is exceeding the minimum required value i.e. 387.377 MPa and 2763.121 Nm2.
So, the cross-section of primary material was decided to be 1-inch outer diameter and 3 mm thickness and that of secondary material to be 1-inch outer diameter and 2 mm thickness.
-
Designing of Roll Cage
The design process of the roll cage was iterative and based on several engineering and reverse engineering processes. Firstly, we decided the driver of the vehicle according to weight and height and then took every required measurement to start the designing process of the roll cage in SOLIDWORKS 2018. During the designing, we took care of each rule given in the rulebook, the driver ergonomics and also the requirements of various domains. In this way, we prepared a basic model of our roll cage and we used CATIA V5 to prepare a driver manikin and checked for required clearances for the driver. Now the only thing we had to do was certain modifications based on the analysis. After these modifications, we got the final design of the frame.
Fig-1: Final design of the roll cage Fig-2: Drivers view in CATIA V5
-
Finite Element Analysis (FEA)
The roll cage is made up of circular pipes with hollow sections and thus we can neglect the thickness of the pipe and the pipe can be assumed as a curved rectangular surface, so we have used 2D elements for meshing the roll cage. The method used was quadrilateral dominant. We tried both the first order and second-order elements but didn't find any significant difference in the results so after considering the time & hardware constraints, we used first-order elements. We also did the mesh dependency test (grid independence) for different element sizes and found the saturation around 3mm as shown in the Figure. We have used the appropriate value of proxiity for the joints, as they are the areas of high-stress concentration. The Boundary conditions were considered such that they satisfy the actual dynamic loading conditions in static structural.
Fig-3 Variation of Stress with the mesh size.
Fig-4: Variation of Deformation with the mesh size.
From Impulse-Momentum Theorem,
F*t = m*(u-v)
here,
F = Impulsive force, t = time,
m = mass of the vehicle, v = final velocity,
u = initial velocity
Suppose the vehicle is going with its maximum velocity and strikes with an obstacle and comes into rest after the impact.
F*t = m*(vmaxx-0)
F = (m*vmax)/t (1)
We have considered two types of impact forces –
-
Impact of roll cage with a rigid body (like rock, wall): impulsive time of impact =0.15 seconds
-
Impact of roll cage with a deformable body (like a tree, another roll cage): impulsive time of impact
-
=0.30 seconds Front Impact
For front impact analysis, we assume the vehicle is going in the forward direction and it suddenly strikes a rigid obstacle like a wall with a maximum speed (i.e. 45 km/h) and comes into rest after the collision.
Then the impact force F will be,
F = (m*vmax)/t (from 1) m = 270 kg, vmax= 45 km/h or 11.12 m/s
F = (270*11.12)/0.15 F = 20,016 N
The impact forces were applied on the forward part of the vehicle and the rear suspension points were constrained to restrict all of the six degrees of freedom.
Fig-5: Front Impact – von-mises stress- 329.9 MPa FOS-1.27.
Fig 6: Front Impact – Max deformation- 1.84mm.
F = (270*11.12)/0.30 F = 10,008 N
The impact forces were applied on the rearmost part of the vehicle and the front suspension points were constrained.
Fig 7. Rear impact von-mises stress- 183.3 MPa FOS-2.23.
Fig 8. Rear impact Max deformation- 1.2844mm.
Rollover
As we know that the chances of having a rollover are more than that of the front, rear or side impacts, in adverse off- road conditions so to analyze the vehicle against a rollover condition becomes crucial.
We have to analyze the vehicle in the worst condition which it can experience at the event and that is when the vehicle falls upside down from a height let us say one meter.
Then from the law of conservation of energy,
m*g*h = (½)*m*V2 V = (2*g*h) ^(½)
Rear and Side Impact
For rear and side-impact analysis, it was assumed that some other vehicle comes and strikes with our vehicle, in this case, the impact will be of the second type, that is the impact of the roll cage with a deformable body, so the impact time will be 0.30 seconds.
Then the impact force F will be,
F = (m*vmax)/t (from 1) m = 270 kg, vmax= 45 km/h or 11.12 m/s
here,
Now from (1),
h = 1m and g = 9.81 m/s2 V = (2*9.81*1) ^(½)
V = 4.42 m/s
F = (m*vmax)/t
F = (270*4.42)/0.15
F = 7956 N
Time taken was 0.15 seconds as the ground is considered a rigid boundary.
The impact force is applied at the joint of RHO and FBM members at an angle of 45 degrees with the vertical and lower part of the roll cage being constrained.
RHO Roll Hoop Overhead member FBM Front Bracing Members
Fig 9. Roll cage roll over von-mises stress – 274.74 MPa FOS-1.58.
Fig 10. Roll cage (rollover) Max deformation- 1.60 mm.
Torsional Rigidity
Torsional Analysis of the roll cage is carried out to determine the torsional stiffness to withstand off road conditions while taking into consideration the torsional forces acting on the frontal and Rear members of the vehicle. Both tyres on the front and rear axle experience a moment. The torque is applied to one tyre and reacted by the other one which is equal and opposite hence a couple is generated which tries to twist the roll cage.
Front track width = BF= 1.37m Rear track width = BR= 1.32m Average track width = B = 1.34 m
Let us assume our vehicle is going over a bump and droop simultaneously with a left wheel over the bump and right over the droop,
Then the Net Torque = T = (FL -FR) *(B/2)
Here FL, FR are the upward forces acting on the left and right wheels,
Maximum torque will act when FR equals zero.
i.e. Tmax = FL*(B/2)
In this position, all the downward force will be equal to FL
-
FL= mg,
and also Tmax = mg*(B/2)
Tmax= 270*9.81*1.34/2 Tmax= 1782.5 Nm
Calculating the couple forces
2*F*(1.34/2) = 1782.5 F = 1330 N
Applying a force of 1330 N at front left suspension points and at the rear right suspension points with the rest of the two as constraints.
Fig 11. Roll cage (Torsion) Max stress 284.11MPa FOS-1.40.
Fig 12. Roll cage (Torsion) Max Deformation 5.46mm.
-
-
STEERING KNUCKLE
The Steering Knuckle is a very vital component that integrates the wheel assembly (that includes the steering, suspension, and brakes) and is connected to the frame with the help of suspension arms. It also plays a very important role in the steering mechanism by using the linear motion of the tie rod to give a turning effect to the wheels assembly (following Ackerman geometry).
Designing of Knuckle was a complex task as it is included in unsprung mass so it has to be lightweight and also it has to withstand various forces in off-road conditions so we had
to design the knuckle in such a way that it would give the best strength to mass ratio.
The complete design process of Knuckle can be divided into following steps-
-
Basic designing of knuckle according to suspension hardpoints.
-
Calculation of forces in different boundary conditions.
-
Analysis of Knuckle.
-
Topology optimization of analyzed Knuckle.
-
Final Designing according to optimized data.
-
Analysis of Final Knuckle.
-
Basic Designing
The basic design of the knuckle was made considering
-
Suspension Hardpoints: The location of Suspension points was calculated with the help of LOTUS Suspension Analysis software with the following wheel Alignment parameters at static:
Table 2. Wheel alignment parameters & their values.
Parameter
Value
Camber angle
-1.00 deg
Castor angle
5.09 deg
KingPin Angle
9.18 deg
Castor trail
23.27 mm
Scrub Radius
20.65 mm
Toe angle
0 deg
Ackermann%
76.3%
Roll Centre Height from ground
300 mm
Anti-Dive%
0
Anti-Squat%
0
-
Weight of the knuckle: Weight of the knuckle is very crucial as it adds up to the unsprung mass of the vehicle, so the design must give sufficient strength with the least possible weight.
-
Material to be used: Material selection is also a very important parameter; it defines the volume of the design and also the weight according to the strength of the material.
-
Machining Process adopted: Design is very much influenced by the available machining processes.
-
Cost: Along with the machining process, the cost is also a major constraint at the time of designing, as it influences many other parameters like material selection, machining process, accuracy in fabrication, etc
Firstly, the suspension hardpoints along with wheel centre point and outer track rod ball joint were plotted with their
respective coordinates in a space of SOLIDWORKS. The next step was to locate the distance of brake calliper mounting from the wheel centre, which depends on the positions of the hub and brake rotor and aso on the distance between both the holes of the brake calliper. Now we have all the required points for designing the knuckle, so designing starts with the main body that connects the lower wishbone outer ball joint to the upper wishbone outer ball joint and then the steering arm and calliper mountings are added on to it.
After some finishing works and reducing the sharp edges with the help of fillets and other features basic design looks like this
Fig 13. The final design of the knuckle
-
-
Calculation of Forces
For calculating the forces acting on the knuckle in adverse conditions we have considered a situation when effects of a bump, cornering, steering, and braking are acting at the same time. The forces in each case were calculated separately.
Force calculation due to a Bump –
We have considered a case when the vehicle goes over a bump and the wheel reaches its maximum travel in this position, the damper compresses completely and suspension arms rotate to their maximum, in that instant we can assume the whole assembly to be in static equilibrium.
We have used FOX Float 3 and referred to its manual for calculating force at maximum compression which is 5700 N for 4 inches of longitudinal travel. Now with the help of suspension hardpoints, we made two sketches of lower suspension arm assembly one for the vehicle in a static position and another for the above-described position. Distances and angles from the front view are shown in Fig.
This force will be acting on the spindle that passes through the wheel centre, therefore by considering static equilibrium condition we can calculate the value of the forces acting on both the ball joints. Let the force on lower ball joint in horizontal direction be (FLB)H and that on upper ball joint be (FUB)H
Then, from moment conservation about lower ball joint, (FUB)H = FC *(distance of wheel centre from the
lower ball joint)/(distance of upper ball joint from the lower ball joint)
Fig 14. Analysis of Suspension arm travel.
We can see that the angle between fox and suspension arms at extreme conditions is 51 degrees.
Let the force on the lower ball joint in vertical direction be (FLB)V, then at maximum compression position (i.e.static equilibrium) moment about pivot will be conserved.
(FLB)V*cos(3.27)*408.55 = 5700*sin(51)*245 (FLB)V=(5700*sin(51)*245)/(cos(3.27)*408.5) (FLB)V = 2660.76N
and,
(FUB)H = (2670.93*45.81)/95.49 (FUB)H= 1281.34 N
FC = (FLB)H + (FUB)H (FLB)H = 1389.58 N
Fig 16. Forces due to cornering.
Calculation of forces on Steering Arm –
Fig 15. Knuckle side view, Force due to bump
Force calculation due to cornering –
All the horizontal force on the ball joints is assumed to be acting due to cornering force only.
Let FC be the total cornering force acting on one wheel of the front turning with a velocity of V = 45 km/h or 11.12 m/s and with a turning radius of R = 2.5 m.
Then,
FC = m*V2/R
(m = 20% of total mass of vehicle)
FC = (0.2*270*(11.12)^2)/2.5 FC = 2670.93N
The steering axis intersects the ground at some distance from the point of contact of the wheel, this distance is equal to the vector addition of scrub radius and caster trail. Due to this separation, the net frictional force causes a moment about the steering axis and this moment is balanced by a force acting on the steering arm of the knuckle. Wheel and ground were assumed to be a point contact pair with the patch area zero.
Two Frictional forces are acting on the wheel in the described boundary conditions, one is cornering frictional force and the other is trailing frictional force hence there are two moments caused by each force with cornering frictional force and caster trail causing a clockwise moment and trailing frictional force and scrub radius causing an anticlockwise moment.
Clockwise moment –
Clockwise moment = (Cornering force)*(caster trail)
= (2670.93)*(23.27) Nmm
Clockwise moment = 62152.54 Nmm
Anticlockwise moment –
Trailing frictional force = *(20% of mass)*(g) Trailing frictional force = 1*0.2*270*9.81 N Trailing frictional force = 529.74 N
Anticlockwise moment = (Trailing frictional force)*(scrub radius)
= (529.74)*(20.65)
Anticlockwise moment = 10912.64 Nmm
Net moment –
Net moment = (clockwise moment) + (anticlockwise moment)
Net moment = 62152.54 – 10912.64
Net moment = 51239.9 Nmm
Moment due to steering arm –
Moment due to steering arm = (F)*(Perpendicular distance between outer track rod ball joint and steering axis) Moment due to steering arm = (F)*(82.82)
Moment due to steering arm = Net moment F*(82.82) = 51239.9
F = 618.69 N
Fig 17. Standard angles of wheel alignment.
Fig 18. Force of steering arm.
Calculation of Moment due to the clamping force of brake calliper –
Mass of vehicle with driver= 270kg FOS taken =1.5
Mass taken in Calculation=400 kg
Coefficient of friction between road and tyre=0.6 Centre of gravity (COG) height=485 mm Horizontal distance between front-wheel and COG=900 m
Horizontal distance between rear-wheel and COG=420 m
Dynamic weight transfer ratio: 55:45 Total braking force=2354.4 N
Total applied braking force= 3262.38N Tyre radius= 10.5 inches
Front braking : Force=1294.92 N
Force on one wheel = 1294.92/2 = 647.46
So moment about wheel centre due to braking force, Moment = (braking force)*(distance from wheel center) Moment = 647.46*67.82
Moment = 43910.73 Nmm
-
Analysis of Knuckle-
After basic designing and calculation of forces, now this was the time to analyse the design in calculated boundary conditions.
Spindle and knuckle were analysed separately, in this segment we will be discussing the analysis of knuckle only. The purpose of the analysis is to make sure the designed knuckle withstands the calculated forces with an appreciable factor of safety. Since the knuckle is a three-dimensional object, we need to have 3D mesh elements inside the volume and therefore we have used three-dimensional Hex Dominant mesh elements of second order with a mesh size of 2mm and with free face mesh type being quad/tri. Sharp corners and edges and curved surfaces are the locations which are very likely to have maximum stress concentration and therefore it becomes very important to have a good quality mesh in these areas, to fulfil this purpose we have used certain mesh features provided in Ansys Mechanical –
-
Mesh Defeaturing: Small corners can deviate the results by having maximum stress concentration to avoid this deviation Mesh Defeaturing is used it defeatures or removes small corners. The value of Mesh defeaturing taken was 0.4mm.
-
Capture Curvature: To capture small curves and to have good quality mesh at curvature. The minimum curvature size taken was 0.5mm.
-
Capture Proximity: This is the most important feature. It captures all proximities and helps to generate a small and good quality mesh in these areas. The minimum proximity size taken was 0.5mm.
Fig 19. Value and locations of forces.
-
Forces on Lower Ball joint-
(FLB)V = 2660.76N in vertically downward direction (B)
(FLB)H = 1389.58 N in a horizontal direction towards the wheel centre. (C)
-
Forces on Upper Ball joint –
(FUB)H= 1281.34 N in a horizontal direction towards the wheel centre.
-
Force on steering arm –
618.69 N in a horizontal direction towards the wheel centre.
-
Moment on calliper mounting –
A moment of 43910.73 Nmm in clockwise direction.
The results of the analysis –
Fig 20. Maximum stress 212.95 Mpa.
Fig 21. Max Deformation 0.70 mm.
-
-
-
Topology Optimization –
Topology Optimization ensures that the designed part doesnt weigh more than required without any compromise in the Factor of safety. Any extra material adds up to cst of manufacturing as well as unsprung mass and due to the extra material loads on moving parts are higher than necessary, and hence energy efficiency is also being compromised. We can see that there are some areas where the amount of material is more than necessary and there is a scope of material reduction in those areas
Fig 22. Topology optimization.
-
Final Designing
The final design of the Knuckle was made based on results obtained from topology optimization. The area of interests was the upper part of the knuckle, calliper mounting and steering arm.
Fig 23. Final designed knuckle.
-
Analysis of Final Knuckle
The final design was verified under the same boundary conditions. The results were satisfactory as there is no change in deformation and also stress is in the permissible range with a safety factor of more than 1.7.
Fig 24. Max Deformation 0.72mm.
Fig 25. Max Stress 243.55 Mpa.
-
-
SUSPENSION ARMS
The selection of Suspension geometry is done to fulfil our requirements with the minimum material application. A double-wishbone with dual A-arm, with a damper to lower wishbone is chosen for the front as it has the advantage of more variation in toe angle, camber angle and caster angle, for rear H-arm with camber link arm is selected due to its robust structure and lesser material requirement and fulfilment of requirements of rear suspension geometry.
To satisfy our wheel alignment parameters, the coordinates of the control arms were located using Lotus suspension analysis software for appropriate length and dimensions. For the selection of appropriate thickness of the control arms we used bending equation,
Fig 26. Loadings on suspension arms.
Considering Pure Bending,
Force due to Fox on Maximum compression = 5700N Vertical component = 5700sin(51)
=4429.73N
As it is distributed across 2 sides of the control arm, Force= 4429.73/2 = 2214.865N
Now, Balancing Moments about R2
2214.86 N* 245mm = R1 * 408.15mm R1= 1329.512 N
Maximum Bending Moment at 163.15mm from
M1 = 1329.512 * 163.15 = 216910.033 Nmm
Safety Factor, n= 2
Yield Stress = 418.18 MPa
/n=(M*y)/I
418.18/2 = (216910.03*25.4/2)/I I= 13174.9838 mm4
For 1 Inch external Diameter Tubular Pipe, I = /64* [(25.4)4 (d)4]
d = 19.6 mm Therefore thickness = (D – d)/2= 2.9 mm
The minimum requirement of thickness is 2.9mm and hence we used a pipe of external dia 1 inch with a thickness of 3 mm.
The control arms were designed and then simulated with extreme boundary conditions.
A force of 5700N was applied at the suspension link at an angle of 51 degrees with both inner and outer pivot point constrained.
Fig 27. Front suspension arm max deformation 0.30 mm.
Fig 28. Front suspension arm max stress 232.65Mpa.
Fig 29. Rear suspension arm max stress 265.07 Mpa.
Fig 29. Rear suspension arm max deformation 0.183 mm.
-
RESULTS
Frame – Maximum stresses (Von mises stress) and max deformation in all the impact tests of the designed frame are in acceptable range with a good safety factor.
Table: 3 Stress, Deformation and FOS results on frame
Test
Force (N)
Stress (MPa)
Deformation (mm)
FOS
Front
20000
329.9
1.84
1.24
Rear
10000
183.3
1.28
2.29
Side
10000
276.31
1.85
1.52
Roll Over
8000
274.74
1.60
1.52
Torsion
1330 (couple)
284
5.46
1.47
Knuckle – Knuckle was analysed in calculated boundary conditions and results obtained were used in topology optimization which eventually led us to the final design of the part.
Table 4: Stress, Deformation and FOS results on Knuckle
Stress (MPa)
Deformation (mm)
FOS
243.55
0.721
1.7
Suspension Arm – Thickness of suspension arm was calculated and arms were analysed at maximum wheel travel.
Table 5: Stress, Deformation and FOS results on Suspension Arm
Arm
Stress (MPa)
Deformation (mm)
FOS
Front
232.65
0.30
1.8
Rear
265.07
0.183
1.57
-
CONCLUSION
This paper summarizes ways for calculations, optimization, and economic as well as ergonomic designing of a light ATV with maximum possible safety factor under extreme boundary conditions. The impact analysis of the roll cage, structural and topological analysis of steering knuckle, suspension arms are well illustrated above.
ACKNOWLEDGEMENT
We would like to thank our seniors, professors & college administration for their guidance and support throughout our career. We would also like to thank our teammates for successfully helping to complete the designing and manufacturing of the ATV. Lastly, we want to thank our family and friends for motivating us to be part of the project and to write this paper.
REFERENCES
-
U. Yashvanth , Mohammad raffi , G. Raghu Vamsi Reddy . (2019). Dynamic impact analysis on ATV upright.International Journal of Mechanical and Production Engineering Research and Development (IJMPERD) 9, 5, 689 698.
-
Anshul Dhakar and Rishav Ranjan. (2016). Force calculation in upright of a FSAE race car. International Journal of Mechanical Engineering and Technology (IJMET) 7, 2, 168176.
-
Duygu Güler. (2006). Dynamic analysis of double-wishbone suspension. A Thesis Submitted to the Graduate School of Engineering and Sciences of zmir Institute of A Thesis Submitted to the Graduate School of Engineering and Sciences of zmir Institute of Technology.
-
Sanjay Yadav, Ravi Kumar Mishra (2016). Design and Analysis of Steering Knuckle Component. International Journal of Engineering Research & Technology (IJERT) 5, 4.
-
Gondi Prabhu Charan Teja, K.V.P.P.Chandu.(2016). Weight optimization of steering knuckle joint using FEA. International Research Journal of Engineering and Technology (IRJET) 3, 12.
-
Noorbhasha, IN. (2010). Computational analysis for improved design of an SAE BAJA frame structure. UNLV Theses, Dissertations, Professional Papers, and Capstones. Paper
Found the work really exceptional. Most detailed work I found related to BAJA
Wow. Thanks for publishing it. I will be using these for my team