
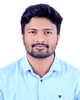
- Open Access
- Authors : Vedant Waladkar , Piyush Vitthaldas , Siddhi Karle , Neha Ingale
- Paper ID : IJERTV11IS070157
- Volume & Issue : Volume 11, Issue 07 (July 2022)
- Published (First Online): 27-07-2022
- ISSN (Online) : 2278-0181
- Publisher Name : IJERT
- License:
This work is licensed under a Creative Commons Attribution 4.0 International License
Design, Analysis & Fabrication of the Powertrain System for All-Terrain Vehicle
Neha Ingale, Siddhi Karle, Piyush Vitthaldas, Vedant Waladkar
Mechanical Engineering Department,
PCETS Pimpri Chinchwad College of Engineering & Research (Ravet), Pune.
Abstract The primary goal of this project is to design, analyze, and build a two-stage reduction gearbox for use in all- terrain vehicles. A gearbox is a mechanical device that consists of a number of gears housed in a casing or a basic gear train. It transmits speed and torque conversions from the engine or CVT to the wheels, making it the most important component of the powertrain system. The gears inside the gearbox can be any of the many various types of gears available on the market, ranging from spur gears to worm gears and even planetary gears. The gearbox used in this article is a spur gear train. This paper focuses on selecting the gearbox's overall reduction ratio, as well as material selection, gear dimension selection, shaft dimension selection, key design selection, and bearing selection from the SKF bearing catalogue The bending and wear strengths are estimated to determine the factor of safety, and then the results are validated using Finite element analysis.
Keywords Geartrain, Shaft Design, SKF Bearings, Catia, FEA.
-
INTRODUCTION
The BAJA SAE INDIA is an international student competition. BAJA focuses primarily on an out-of-classroom learning approach in which engineering students from throughout India collaborate as a team. Each team's purpose is to develop and build a prototype of a durable single-seat off- road four-wheel vehicle that must pass a series of tests before competing in the endurance race. The MINI BAJA event was first held in the United States by SAE International. In January 2007, the event was officially launched in India. As per specifications given in the rulebook for SAE BAJA INDIA 2022, There are 5 total departments:
-
Roll cage
-
Suspension
-
Steering
-
Brakes
-
Engine and Powertrain
The Engine being the heart of vehicle, used in this powertrain system is Briggs and Stratton make which is Four Stroke, Single Cylinder, 305cc, 10hp and 18.4Nm Gross torque. Transmission done using Continuous Variable Transmission (CVT), using CVT by OEM provider CVTech CVT instead of manual transmission giving seamless transmission ratios between 0.43 to 3.0. The power train system is designed for overall reduction of 10.5 : 1 along with Design and Analysis of the system, gear and shaft material selection, Transmission of torque from gearbox to wheels using CV axles, achieving performance targets, stopping, steering system for adequate control is done. A frame design is based on the suspension, steering, and gearbox subassembly designs of the
specific vehicle, giving flexibility to optimize it in terms of weight and longevity. As a result, analysis provides us with a mathematical model that identifies opportunities for component optimization and weight reduction for an overdesigned component. Because of its diverse function in vehicle dynamic behavior, the automotive chassis is one of the most significant structural components of any propelled vehicle. The purpose of this presentation is to show the design and development of a vehicle for a single-seated combustion engine vehicle. The major goal is to assess chassis and member deformation, as well as design a gear train system based on requirements, static analysis, and modal analysis, in order to save weight while ensuring optimal vehicle operation in a demanding low energy consumption race.
-
-
OBJECTIVE
To build a system capable of producing the torque required to drive the vehicle, as well as a gearbox capable of maintaining the required center distance between the input shaft connected to the secondary CVT and the output shaft connected to the half shaft. In addition, a wide range of gear ratios must be obtained, as well as maximum speed and high torque. The system must be affordable, lightweight, and efficient. The vehicle with a gearbox is intended for an ATV (All-Terrain Vehicle) with the engine specifications shown below.
-
Capacity: 305cc
-
Maximum Torque: 19Nm @2800 rpm
-
Maximum power: 10Hp @3800 rpm.
-
-
DESIGN PROCEDURE
Before you begin to format your paper, first write and save the content as a separate text file. Keep your text and graphic files separate until after the text has been formatted and styled. Do not use hard tabs, and limit use of hard returns to only one return at the end of a paragraph. Do not add any kind of pagination anywhere in the paper. Do not number text heads- the template will do that for you.
Finally, complete content and organizational editing before formatting. Please take note of the following items when proofreading spelling and grammar:
-
Fixed Parameters
Max engine RPM: 3800 Max vehicle speed: 60 kmph
Max engine torque: 19.2 N-m Tyre diameter: 23 inches Max gradient:37 o
CVT efficiency: 85% Spur gear efficiency: 94%
Co-efficient of rolling resistance: 0.023 Gross weight: 220kg.
-
Procedure
-
The entire torque necessary was obtained after calculating the overall torque required to move the vehicle.
-
By dividing the whole torque to the engine torque and CVT's under drive ratio, the engine torque and CVT's ratio are predefined. This would be the gearbox's last reduction.
-
Aside from the torque requirement, the vehicle must also achieve a top speed of 60 kmph.
-
At 60 kmph, the engine's maximum RPM was divided by the CVT's overdrive ratio and the wheel RPM. This would result in the required speed reduction of 60 kmph.
-
The torque reduction condition and the maximum speed condition are not the same. As a result, we have a range to work with.
-
To eliminate tooth hunting, maintaining the overall gear ratios between the torque required and max speed condition, and maintain the center-to-center distance between the input shaft and output shaft of the gears, the number of teeth in each gear was taken as prime numbers.
-
The gearbox is connected to the wheel assembly via a half shaft. It's a device for transmitting torque at an angle. It has a joint with a constant velocity. It is rzeppa in this situation. Through the use of splines, it is connected to the gearbox's output shaft.
-
-
CALCULATIONS Air drag resistance = ½ * * A* v*Cd
A = Area of vehicle, m2
= density of air , kg/m3 (1.122 kg/m3) V = maximum velocity m/sec
Cd = coefficient of drag, 0.44 Fr = surface friction, 0.014
m = mass of vehicle, kg
g = acceleration due to gravity, 9.81 m/sec2 = friction coefficient
Considering maximum velocity of 60 kmph = 16.67 m/sec.
T.E max = * Wr
= * (Wt – cos() * % Wr) Tt = Total Effort, N
-
max = Tractive Effort maximum, N Wt. = Total weight of vehicle, 2158.2 N
%Wr = % weight of rear, 0.65 Tw = Torque on wheel, N-m Te = Engine torque, N-m
Lr = Lower ratio
over = overall transmission efficiency
-
Calculation of rolling resistance Rolling Resistance (RR) = Fr * m * g
= 0.014 * 220 * 9.81
= 30.2148 N
-
Calculation for air resistance
Air Resistance (AR) = ½ * * A* v2 *Cd
= ½ * 1.122 * 0.867 * 16.672 * 0.44
= 59.47 N
-
Calculation of grade resistance
Grade Resistace (GR)= sin() * m * g
= sin (30.11) * 220 * 9.81
= 1082.69 N
-
Calculation of total tractive effort
Total Tractive Effort (T.T.E)
= A.R + R.R + G.R
= 59.47 + 30.2148 + 1082.69
= 1172.3748 N
-
T.E max = * Wr
= * (Wt. – cos() * % Wr)
= 1 * (2158.2 * cos(30.11) * 0.65)
= 1213.534 N
-
Torque on wheel Tw = T.T.E * radius of tyre
= 1172.37 * 0.2921
= 342.45 N-m
-
Torque on wheel Tw = Te * Lr * over
324.45 =18.6 * Lr * 0.90
Lr = 19.38 (approx. 20)
Lr = 20:1
-
Calculating for maximum torque at 3800 rpm
Te = 18.6 N-m Lr = 20
Tw= Te * Lr * over
= 18.6 * 20 * 0.90
= 334.8 n-m (Pull at wheel)
-
Force on wheel Fw = Tw / dynamic radius of tyre
-
= 342.45/0.2921
= 1172.37 N
For Condition = (0 % gradient track)
Vw = velocity of wheel at 3600 rpm
Rw = Dynamic radius of tyre = 0.2921 m N engine = engine rpm
Lr = lowest ratio
Wg = gross vehicle weight, N Fw = Force on wheel
-
TTE = RR + AR + GR
-
RR = Wg * 0.05(dry road)
= 2158.2 * 0.05
= 107.91 N
-
GR = 0 N (0 % gradient track)
Vw = (Rw * 2 * * N engine) / (60 * Lr) Vw = (0.2921 * 2 * * 3800) / (60 * 20)
Vw = 5.8 m/sec
-
Air drag Resistance = ½ * * A* v2*Cd
= ½ * 0.867 * 1.122 * (5.8)2 * 0.44
AR = 7.19 N
-
F = (Fw TTE)
= (1172.37 (107.91 + 7.19))
= 1057.27 N
-
Acceleration, a = (F *g)/ W
= (1057.27 * 9.81)/ (2158.2)
a = 4.81 m/sec2
-
Gradeability = G = tan -1 (1057.27/2158.2) G = 26.09 deg
F = Force, N
Wt = Total weight of vehicle, N Vw = Max velocity, m/sec
Rw = Radius of wheel
Nw = Speed at wheel, rpm
N engine = engine speed, rpm Hr = higher ratio
-
Vw = 60 kmph = 16.67 m/sec
-
Ww = Vw/Rw
= (16.67/0.2921)
= 57.06 radsec
x. Nw = (Ww * 60) / 2
= (57.06 * 60) / 2
= 545 rpm
-
N engine / Nw = Hr
Hr = (3800/545)
Hr = 6.97 (approx. 7)
Ft = (7.5 * 103)/ 17.1240
= 437.9817 N
Fr = Ft tan (20)
= 159.4123 N
Force acting on spur gear (2nd stage)
-
Pinion
V = ( dp Np) / (60 * 100)
= ( * 18 *2.5 * 3479.2125)/ (60 * 1000)
= 8.1977 m/sec
Ft = (7.5 * 103)/ 8.1977
= 914.890 N
= Ft tan (20)
= 332.9930 N
Shaft Calculations: –
-
Input Shaft
Calculations of velocity of vehicle
Linear velocity of wheel
V = Radius of wheel * Angular Velocity
= 0.2921 * 57.06
= 16.67 m/sec
= 59.90 km/hr
AB = 90 mm BD = 20.5 mm DE = 41 mm
MEFy = 0
Fig. 1. A
Considering tramission efficiency 90%
V = 53.91 km/hr
Force acting on spur gear (1 st stage)
-
-
Pinion
= ( * 18 *2 * 8.8372 * 103)/ (60 * 1000)
V = ( dp Np) / (60 * 100)
= 16.6577 m/sec Ft = (7.5 * 103)/ 16.6577
= 450.2422 N
Fr = Ft tan (20)
= 163.874 N
-
Gear
-
-55 + RB 450.2422 + RE RB + RE = 505.2422 N
ME = 0
-( 55 * 151.5) + (RB * 61.5) (450.2422 * 41) = 0
RB = 435.6492 N RE = 69.593 N
B.MA and B.ME = 0
B. MB = – 55 * 90 = -4950 N-m
B.MD = (-55 * 110.5) + (435.6492 * 20.5)
= 2853.3086 N
= 141.732 * 103 N-mm
Mt1 = 3 * 2.54 * 18.6
V = ( dp Np) / (60 * 100)
= ( * 47 *2 * 3479.2125)/ (60 * 1000)
= 17.1240 m/sec
180.5 = (16/ d3) * [ (2 * 4950)2 + (1.5 * 141.732 * 103)2]
180.5 = (16/ d3) * 212828.38
d = 18.17 mm (standard 20mm) Intermediate Shaft diameter = 30 mm
Output Shaft
= 216 mill revs
C = P * (L10)1/3 * L.F
= 572.5405 * (216)1/3 * 0.4
= 1374.09 N
Bearing No. = 61804
D = 32 mm B = 07 mm Co = 1500
C = 2700
BD = 41 mm DE = 20.5 mm
Fig. 2. B
Bearings for intermediate Shaft Fr = 1318.936 N
N = 2727.27
Diameter = 30 mm
Dynamic load factor P = Fr = 1318.936 N
Fy = 0
RB + RE = 1.11 * 103 N
ME = 0
(RB * 61.5) (1.11 * 103 * 20.5) = 0 RB = 370 N
RE = 740 N
BMD
-
MB and B.ME = 0
B.MD = (370 * 41) = 15170 N
Mtz = 559.8414 * 103 N-mm
max = 16 /[ d3 (1-0.64)] * [ (2 * 15170)2 + (1.5 * 559.8414
* 103)2]
180.5 = 16 / [ d3 (1-0.64)] * 840310.0024
d = 30.088 mm (standard 30 mm)
Bearing Calculations Expected life = 500 h
L.F = 0.4
Bearings for input Shaft Diameter = 20 mm
N = 7200 rpm Fr = 572.5405 N
Dynamic load factor P = Fr = 572.5405 N
L10 = (60 * N * 500) / 106
L10 = (60 * N * 500) / 106
= 81.81 mill rev
C = P * (L10)1/3 * L.F
= 1318.936 * (81.81)1/3 * 0.4
= 2290.26 N
Bearing No. = 61806 D = 42 mm
B = 07 mm Co = 2080
C = 3120
Bearings for output Shaft Fr = 880.44 N
N = 2727.27
Diameter = 30 mm Dynamic load factor P = Fr = 1880.44N
L10 = (60 * N * 500) / 106
= 81.81 mill rev
C = P * (L10)1/3 * L.F
= 880.44 * (81.81)1/3 * 0.4
= 1528.839 N
Bearing No. = 61806 D = 42 mm
B = 07 mm Co = 2080
C = 3120
VI. SOFTWARE USED
-
CATIA V5
CATIA is an acronym that stands for Computer Aided Three- Dimensional Interactive Application. It's more than just CAD (Computer Aided Design) software. It is a comprehensive software suite that includes CAD, CAE (Computer-Aided Engineering), and CAM (Computer-Aided Manufacture). It is a major 3D programme utilised by enterprises in a variety of industries ranging from aircraft to automobiles to consumer goods.
Part Design : This Catia module allows you to build exact 3D mechanical parts using a simple and flexible user interface, from assembly drawing through iterative detailed design.
Fig. 3. Isometric View ( Geartrian )
Fig. 4. Stage 1. CAD Model
Fig. 5. Stage 1. CAD Model
-
ANSYS 18
-
Organizations throughout the world rely on the ANSYS Mechanical software suite to handle difficult structural and thermal challenges quickly and easily. ANSYS structural mechanics solutions can simulate every structural aspect of a product, including nonlinear static analysis that provides stresses and deformations, modal analysis that determines vibration characteristics, and advanced transient nonlinear phenomena involving dynamic effects and complex material behavior. You may import complex assembly geometries, optimally mesh them, and apply realistic boundary conditions with ANSYS
Mechanical software solutions. Following these pre-processing processes, you can run analyses to evaluate the system's strength, vibration, motion, and thermal response. A number of graphical tools make it simple to visualize the.
Fig. 6. Stage 1. Parameters
Fig. 7. Stage 2. Parameters
Fig. 8. Stage 1. Stress ( Von-Mises )
Fig. 9. Stage 2. Stress
Fig. 10. Stage 1. Deformation
Fig. 11. Stage 2. Deformation
Fig. 12. Casing Parameters
Fig. 13. Casing Deformation ( Brake Caliper Mount )
Fig. 14. Stress (Von Mises for Brake Caliper Mount )
Analysis Table:
Parameters |
1st Stage |
2nd Stage |
Casing |
Analysis Type & Element |
Static Structural & Tetrahedral |
Static Structural & Tetrahedral |
Static Structural & Tetrahedral |
Number of Nodes |
39638 |
78928 |
133994 |
Number of elements |
23041 |
45081 |
79011 |
Elements Size (mm) |
4 |
4 |
4 |
Max Force or moment (N-m) |
10 |
19.6 |
525 |
Total deformation (in mm) |
0.043 |
0.002 |
0.096 |
Max equivalent Stress (Mpa) |
435.06 |
304.29 |
142.37 |
FOS |
3.07 |
3.52 |
2.18 |
Life (min) |
2085.6 |
1617.5 |
89199 |
Damage (min) |
1000 |
1000 |
1000 |
Table: 2 Analysis Result Table
CONCLUSION
-
Analysis of Chassis was carried out on various loading case, It was clear from analysis chassis will be safe.
-
By using Ansys result we conclude overall design will be safe.
-
The Obtained results in theory and in Ansys are in all acceptance and satisfies the required criteria.
REFERENCES
[1] Payne, Eric T., Design of an SAE Baja Racing Off-Road Vehicle Powertrain (2015). Honors Research Projects. 30. [2] Chetan Chaudhari, Aditya Pasalkar, Akshay Gavade, Ashish Jagtap Design of two stage single speed gearbox for transmission system ofSAE BAJA vehicle, IRJET 2018, ISSN: 2395 0056, Volume 05 Issue
10 Oct 2018
[3] Aditya V Gawale, Chandramani Singh, Kailas M Kawale, Shubham P Sutar Design of Powertrain system for an All-Terrain Vehicle IJARIIE 2018 ISSN: 2395-4396 Vol. 4, Issue 3, 2018AibekMusaev, De Wang, LITMUS: Landslide Detection by Integrating Multiple Sources , may 2014 [4] Enrico Armentani, Venanzio Giannella, Antonio Parente, Mauro Pirelli Design for NVH: topology optimization of an engine bracket support,ISSN 2452-3216, Science Direct 2020
[5] Skinner, Sean Sebastian, Modeling and Tuning of CVT Systems for SAE® Baja Vehicles (2020). Graduate Theses, Dissertations, and Problem Reports. 7590. [6] Bhandari V. B., Design of Machine Elements, Tata Mc-Graw Hill Publishing Co. Ltd, 4th Edition- 1997.