
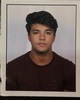
- Open Access
- Authors : Apurav Sharma, Mehul Gupta, Dr. Sanjeev Dhama, Mr. Sugandh Gupta
- Paper ID : IJERTV13IS040256
- Volume & Issue : Volume 13, Issue 04 (April 2024)
- Published (First Online): 01-05-2024
- ISSN (Online) : 2278-0181
- Publisher Name : IJERT
- License:
This work is licensed under a Creative Commons Attribution 4.0 International License
Design Analysis of Low-cost Subsonic Open Section Wind Tunnel
Apurav Sharma Mehul Gupta
Undergraduate Student of Undergraduate Student of Aerospace Engineering, Aerospace Engineering,
Chandigarh University Chandigarh University
Dr. Sanjeev Dhama
Faculty Member of Aerospace Engineering, Chandigarh University
Mr. Sugandh Gupta
Faculty Member of Aerospace Engineering, Chandigarh University
Abstract – Subsonic wind tunnel play a crucial role in aerodynamic research; it provides a controlled environment to study the airflow characteristics that are important for the development and improvement of various aerospace systems. This paper will focus mainly on the design, construction, and performance enhancement of low-cost small-scale open-section subsonic wind tunnel, with a focus on achieving better accuracy and efficiency in aerodynamic testing. With the growing demand for affordable and reliable aerodynamic research and testing equipment facilitates the importance of developing low cost- or cost-effective solutions without affecting the data
-
INTRODUCTION
The wind tunnel is an instrument That provides a controlled environment to study the complex behavior of air flow around various structures and objects this instrument simulates the conditions encountered by automobiles aircraft buildings and other aerodynamic bodies allowing us to assess and optimize their performance characteristics.
accuracy and experimental integrity. The research begins with comparing and overviewing existing wind tunnel designs and identifying common areas for reducing the cost and improvement. CFD was used to simulate and validate the flow parameters. The profile of this wind tunnel includes wind tunnel of total length 2.75 meters.
Keywords- Open Section Subsonic Wind Tunnel; Aerodynamic Research; Low-Cost; Small-Scale; Reliable; CFD; Simulation; Mean Velocity;
Fig. 1 – Old NASA Langleys First Wind Tunnel
(Source: https://www.nasa.gov/image-article/nasa-langleys- first-wind- tunnel/#:~:text=The%20honeycombed%2C%20screened%2 0center%20of,arrangement%20to%20smooth%20the%20flo w.)
The concept of wind tunnel goes back to the late 19th century, with early experiments and research conducted by pioneers such as Otto Lilienthal and Sir George Cayley. From back then, wind tunnel technology has evolved greatly, with significant advancements in design, instrumentation, and construction techniques that enhanced their accuracy and reliability. The wind tunnel being one of the most important discoveries in the field of engineering and revolutionizing the industries has two most basic types. The open section wind tunnel and the closed section wind tunnel.
Open-section wind tunnel has a simple design and the air flows through the test section and leaves the tunnel into the environment without being used or recirculated. These open- section wind tunnels are mostly used for low-speed aerodynamic testing such as automobiles, buildings, etc. They provide simplicity and ease of operation but face challenges with environmental variables like temperature and humidity,
Fig. 2 – Basic Open-Section Wind Tunnel
Closed-section wind tunnels are more complex and circulate air within a closed loop. This allows for precise control of the flow conditions and this makes the closed-section wind tunnels more viable for a wide range of scenarios. Scenarios like high-speed testing. These wind tunnels are more complex and expensive to operate but provide more efficient results.
Fig. 3 – Closed Section Wind Tunnel
The history of wind tunnels goes as far as the late 19th century with great advancements happening in the early 20th century. Francis Herbert Wenham, a pioneer in wind tunnel
development was an English engineer who constructed the 1st known wind tunnel in 1871. It was small and had limited capabilities but provided a start for later developments.
Everybody knows the Wright brothers. Pioneers of the aviation sector. They used a wind tunnel to refine their aircraft designs and achieved the power of flight in 1903. They showed how important a tool like a wind tunnel is for aviation.
Fig. 4 – Wright Brothers Wind Tunnel (1901)
(Source: www.wright- brothers.org/Adventure_Wing/Hangar/1901_Wind_Tunnel/ 1901_Wind_Tunnel.htm)
During World War I and World War II, we saw rapid growth in the advancements in wind tunnel technology due to military needs. It became an essential tool for designing better aircraft. Giving us technology like swept winds and more efficient propellers.
In the late 20th century we witnessed the growth of wind tunnel technology with the development of closed-section wind tunnels simulating high speed and high-altitude conditions. we saw the growth of software like CFD helping our understanding of aerodynamic conditions to a new level. NASA and many other organizations utilize wind tunnels extensively for testing spacecraft and rockets. Spacecraft are designed to operate in outer space, where there is no atmosphere, yet rockets must pass through Earth's atmosphere to reach space. Wind tunnels play a crucial role in developing new technologies for vehicles like the Ares rockets and Orion spacecraft. These are next-generation vehicles intended to transport astronauts into space, and NASA engineers have utilized wind tunnel testing to refine their designs. Wind tunnel experiments have also contributed to NASA's efforts to enhance the safety of space shuttles by testing new ideas and modifications. Moreover, wind tunnels continue to be invaluable in improving spacecraft and rocket designs across the board. They are instrumental in testing spacecraft components such as parachutes, especially in setups that mimic the atmospheric conditions of other celestial bodies like Mars. Wind tunnels are not only used for current projects but have a historical significance as well.
In late 1901, the Wright brothers faced challenges with their early aircraft designs, prompting them to build a wind tunnel. This decision allowed them to create a more controlled
environment for testing and compare the results obtained in the wind tunnel to the actual flight performances of their kites and lightweight planes.
Fig. 5 – Low-Speed Wind Tunnel at NASA (Source: www1.grc.nasa.gov/facilities/9×15/)
Wind tunnels play a critical role in the aerospace industry, primarily serving as controlled environments for testing aircraft and gathering essential data for design improvements. The main objective behind wind tunnel testing is to obtain accurate information that aids aeronautical designers in developing new and advanced types of airplanes. This is particularly crucial due to the complexity of modern high- performance aircraft, which require a vast array of data before achieving optimal designs. Unlike flight testing, which can be costly and risky, wind tunnels offer a safer and more cost- effective means of gathering design information. They enable engineers to simulate various flight conditions and aerodynamic scenarios, helping them refine aircraft designs to meet performance, safety, and efficiency standards. As aircraft continue to evolve, with advancements in size and speed, the importance of wind tunnels becomes even more pronounced, necessitating the development of increasingly sophisticated tunnel designs to replicate full-scale flight conditions for model testing accurately.
-
Literature Review
Sahith Reddy Madara and Jerrin Thadathil Varghese in their paper on the Design and Fabrication of a Low-Cost Open Circuit Subsonic Wind Tunel focused mainly on decreasing the cost of development, reducing the scale, and getting better accuracy of test results from an open circuit wind tunnel. The dimension profiles that they used were as follows, the dimensions of the contraction cone inlet i.e. 80 cm x 77 cm with a length equal to 70 cm, a contraction length of 900 mm, The area ratio between the inlet section, and the outlet of the settling chamber of the diffuser is 2 with dimensions 35 cm x 35 cm to 65 cm x 62.5 cm. The test Section has a dimension of 340mm x 360mm x 500mm. The paper discusses creating a fast stream of air through a test section to analyse the life and drag coefficients of the objects. It also mentions different materials to be used in the construction of the wind tunnel,
materials such as paper honeycomb core, plywood, and plexiglass. Different test results are shown in the research paper
H Ifeanyichukwu U. Onyenanu et al. mainly focused on designing and fabricating a wind tunnel testing machine. The machine was intended to create wind streams at different speeds through the test section.
Prof. Abdulrahman A. Alrobaianet et al. showcased A New Approach to Low-Cost Open-Typed Subsonic Compressible Flow Wind Tunnel for Academic Purpose. This paper focuses on the design and development of a cost-effective yet simple test section for a subsonic wind tunnel aimed at educational purposes. Their research aimed to demonstrate high-speed flow around a model in a test section without interference. They fabricated a square nozzle to achieve a max velocity of 340 m/s. The test section measures 25 mm x 25 mm x 70 mm and is strategically placed to avoid dead zones and end effects. measures 25 mm x 25 mm x 70 mm and is strategically positioned to avoid dead zones and end effects of the ducts allowing pressure measurements at different locations. Sensors connected with PVC tubes and LabVIEW interface enable data acquisition.
Nelton Koo Chwee Yang designed and fabricated a small wind tunnel. He used a software called SolidWorks used often in aerospace engineering for 3D modelling and Simulation. In the wind tunnel, Yang measured how much drag a sphere experienced when it was placed in a stream of air moving at different speeds that were all below 100 m/s. to measure the drag force acting on the sphere he used a system called integral balance and to measure the air speed he used an instrument called Pitot Static Tube. Yang also used strings to observe how the air was moving inside the wind tunnel. He compared his results with the data that had been published before to check if they matched.
Md. Arifuzzaman and Mohammad Mashud on Design Construction and Performance Test of a Low-Cost Subsonic Wind Tunnel focuses on designing and fabricating a low-cost tunnel for aerodynamic research. Their main goal was to reduce construction costs and enable easy installation in laboratories. The wind tunnel had a square cross-section of 0.90m × 0.90m and a length of 1.35m with an overall length of 7.35m viable for laboratory settings. The testing of the wind tunnel revealed a maximum wind velocity of 28 m/s in the test section, with a nearly linear velocity profile along the width and height. except a 12% allowance of boundary layer formation on the four side walls. the fabricated wind tunnel met design specifications and was ready for various tests.
Todd David Walker improved a subsonic wind tunnels drive system by boosting the speed of the test section by 19 mph and increasing the drive system efficiency by 21%. Whereas,
J.H. Ringer and R.D. Mehta developed a new method for designing contraction cone shapes in small wind tunnels by accurately predicting boundary layer behaviour. Milan Vlajnacs research emphasized designing and fabricating a high-efficiency, low-cost wind tunnel by implementing a magnetic suspension system. The magnetic suspension system is an advanced technology that allows levitation and control of objects inside the wind tunnel without any physical contact and minimizes interference and turbulence.
Furthermore, a few reference books were taken into consideration for the research and validation of aerodynamic and thermodynamic parameters in the wind tunnel including Aero Engineering Thermodynamics by Dr. Dharminder Singh Chand and Fundamental of Aerodynamics by John
D. Anderson.
Bell and Mehta: the nozzle cross-section area ratio is supposed to be 6 to 10 (range) [Contraction Design for Small Low-Speed Wind Tunnels by James H. Bell and Rabindra D. Mehta].
-
DESIGN CRITERIA
The following wind tunnel is a low-cost, small-scale, open-loop subsonic wind tunnel.
The basic components that are essential for the working of a subsonic wind tunnel are:
-
Settling chamber
-
Honeycomb Mesh
-
Contraction cones
-
Test chamber
-
Diffuser
-
Exit
Settling chamber:
The settling chamber allows for smooth air entry, minimizing turbulence and ensuring it has uniform flow.
Fig. 6 – 3D Inlet design made in SolidWorks
The design of the settling chamber/Inlet is proportional to the other component designs that are connected to the inlet as the cross-sectional area of the inlet is the size of the inlet area of the contraction cone.
Contraction Cone/Nozzle:
The contraction cone plays a crucial role in the wind tunnel by accelerating the flow going to the test chamber.
The design of the nozzle starts by matching its shape and size to that of the testing chamber. For example, if the test chamber has a shape, with 45-degree bevelled edges the nozzle exit should also have 45-degree bevels.
To design the nozzle inlet cross section, it is important to define the nozzle area ratio. This ratio should determine the maximum flow acceleration and pressure losses in upstream sections.
Fig. 7 – 3D design of Nozzle made in SolidWorks Using the formula used for the Nozzle/Contraction cone:
Where;
r=radius of the nozzle cross-section
z = Distance of cross-section from the inlet
Test chamber:
Fig. 8 – 3D test section made in SolidWorks
When creating a miniaturized test area for a wind tunnel, there are various important factors to consider to guarantee precise and effective aerodynamic testing in a limited space. Initially, the shape and dimensions of the test section must be chosen thoughtfully to fit small-scale models while retaining
realistic airflow properties. It is essential to have smooth paths for the flow and gentle expansions/contractions to reduce turbulence and enhance pressure regain. The utilization of boundary layer control tools such as honeycomb structures or screens is beneficial in sustaining a clearly defined flow pattern. The ratio of contraction must be fine- tuned to guarantee consistent airflow, and the placement of instrument ports should be strategic for sensor instalment.
The test section is the most important part of ventilation as it is where the test sample is placed. The test sample should not be mixed or separated and should be moved continuously. For the flow to be laminar and smooth, the Reynolds number must be less than 2100.
Diffuser:
Fig. 9 – 3D model of the diffuser section made in solid works
The design of a diffuser in a wind tunnel is essential and is important to:
-
Airflow deceleration
-
Pressure recovery
-
Reduction in turbulence
The diffuser links the entry section to the settling chamber. It must ensure that there is no separation of flow within this segment. The ratio of areas between the entry section and the outlet of the settling chamber for the diffuser is 2. To avoid flow separations, it is recommended that the maximum angle of the diffuser suitable for this ratio is 20 degrees.
Honeycomb esh:
Fig. 10 – 3D model of the mesh made in solid works
The design of a honeycomb mesh is complex and requires precise work
The work of the honeycomb mesh is to:
-
Flow strengthening
-
Turbulence reduction
-
Uniform flow distribution
-
Improve the overall aerodynamic performance of the wind tunnel
The area of the mesh is equal to the cross-sectional area of the settling chamber and will fit inside or at the inlet of the settling chamber.
Exit:
Fig. 11 – 3D model of the exit of the wind tunnel
The exit of the wind tunnel is the component that encompasses the fan.
The cross-sectional area of the exit is the same as that of the cross-sectional area of the exit of the diffuser.
Fig. 12 – Heavy-duty electric fan
TABLE 1: Specifications of newly designed subsonic wind tunnel
-
-
MATERIAL SELECTION
Test Section
The test section is where we place objects to study. So, it should be strong, transparent (so that flow visualization is visible), and Cheap as we design our wind tunnel for educational and research purposes. Acrylic Sheets (also known as Plexiglass or Perspex) are to be used to achieve this. Acrylic Sheets are transparent thermoplastic materials that offer excellent visibility (transparency) and impact resistance allowing visual inspection of airflow in a wind tunnel. Its a cost-effective and better alternative to glass as it provides durable protection against scratches and breakage. It is a very lightweight material that makes transporting, installing, and handling easier, and also simplifies maintenance and adjustments. Acrylic Sheets can be drilled, cut, and shaped very easily using common tools, machines, and techniques such as drilling, sawing, and heat bending. The ease of fabrication enables easy modifications and customizations to the test section to meet research requirements.
Contraction Section (Cone/Nozzle)
The contraction Cone of a wind tunnel can be made using plywood, specifically marine-grade plywood or exterior- grade plywood, recommended due to its resistance to moisture and good durability. Marine-grade plywood is specially designed to endure exposure to water and humidity as it is formulated using special types of glues and coatings providing superior resistance to moisture. It has high strength and stability as it is constructed using multiple layers of high- quality wood veneers joined(bonded) together with waterproof glues resulting in a material that can withstand pressures and stresses occurring in wind tunnel. It is sanded to get a smooth finish on both sides providing an optimal and
smooth surface for airflow and minimizing turbulence. The thickness of plywood depends on factors such as the size of the wind tunnel, the contraction ratio, and expected airflow velocities.
Honeycomb Structure
For a low-cost Subsonic Wind Tunnel PVC Pipes along with Metal window mesh can be used to make honeycomb structures providing a lightweight, durable, and cost-effective solution. PVC pipes are very lightweight which is advantageous in situations of portability and easy to install, also they can be easily drilled cut, and assembled, and have a resistance to corrosion and rust making them suitable for humid environments. Metal window mesh is typically made of materials such as aluminium or stainless steel, which offers strength and stability to the honeycomb structure. It provides structural support, reinforces the overall structure, and provides good ventilation and visibility. Combining PVC pipes with metal window mesh is a great solution that leverages lightweight and cost-effectiveness.
Fan/Electric Motor
An exhaust Fan can be used to evacuate air from the wind tunnel to maintain a controlled airflow and pressure airflow. They are generally more affordable compared to other types of fans, and have a simple design consisting of a motor and fan blades enclosed in housing. Exhaust fans can create a negative pressure and promote airflow through the subsonic wind tunnel. For a low-cost subsonic wind tunnel, a moderate airflow capacity of 500 to 2000 cubic feet per minute (CFM) may be optimal, with a Power rating ranging from 50 watts to 500 watts as per the Voltage and Current available in your facility and with a speed control function which can be regulated using a Fan regulator.
Diffuser and Inlet Section
Marine Grade Plywood can be used to make the diffuser and the inlet section is supported by Aluminium or Steel rods which are used for constructing support structures and frames in the wind tunnel. Rods offer a high strength-to-weight ratio and can withstand heavy loads and vibrations occurring within the tunnel. Aluminium rods are lightweight and resistant to corrosion making them suitable for the wind tunnel where weight and durability are important factors.
Additionally, Materials like Foam Board (also known as foam sheet or foam core) can be used for insulation, soundproofing, and construction of internal components of wind tunnels such as flow straighteners or baffles in the wind tunnel. It is an inexpensive and lightweight material composed of polystyrene foam sandwiched between plastic sheets or paper sheets that can be easily cut, shaped, and glued.
-
3D model and successful design analysis
The model was made in SolidWorks which is an industry- leading CAD (Computer-Aided Design) and CAE (Computer-Aided Engineering) software. The design analysis and simulation were done on both SolidWorks are Ansys Software.
Fig. 13 – Wind tunnel 3D model made in SolidWorks
The following images show the results and simulations: These simulations were done for the above-mentioned dimensions proving the working of the wind tunnel to be successful.
Fig. 14 – Velocity Profile of air inside wind tunnel (SolidWorks)
Fig. 15- Pressure profile inside the wind tunnel (Ansys Student)
Fig. 16 – Velocity profile inside wind tunnel (Ansys Student)
Fig. 17 – Velocity vector profile (Ansys Student)
Fig. 18 – Velocity contour (Ansys Student)
-
RESULT AND CONCLUSION
The following design analysis and simulations helped us in making a low-cost subsonic open-section wind tunnel with specific dimensions with maximum efficiency and the least number of shocks.
The following tunnel can be made using cheap materials as mentioned in the paper and can be used to demonstrate the working of a wind tunnel in institutions and schools where having a generic wind tunnel is not viable.
REFERENCES
-
Sahith Reddy Madara* et al. (Ijitr) International Journal of Innovative Technology and Research Volume No.5, Issue No.3, April May 2017, 6154-6161. from
-
vlab.amrita.edu,. (2015). Wind Tunnel – Pressure. Retrieved 2
May 2017,
-
Cattafesta L, Bahr C and Mathew J 2010 Fundamentals of wind- tunnel design Encyclopedia of Aerospace Engineering 1-10
-
Barlow J B, Rae W H and Pope A 1999 Low-speed wind tunnel testing
-
Panda M K and Samanta a K 2016 Design of Low-Cost Open Circuit Wind Tunnel-A Case Study Indian Journal of Science and Technology9
-
Gonzalez Hernandez MA, Moreno Lopez AI, Jarzabek AA et al (2013) Design methodology for a quick and low-cost wind tunnel. Wind Tunn Des Their Divers Eng Appl.
-
Bradshaw P, Pankhurst RC (1964) The design of low-speed wind tunnels. Prog Aerosp Sci 5:169.
-
Mehta RD, Bradshaw P (1979) Technical notes design rules for small low-speed wind tunnels. Aeronaut J R Aeronaut Soc 83:443449.
-
Abdulrahman A. Alrobaian, S. A. Khan, Mohammed Asadullah, Fharrukh Ahmed. G. M & Imtiyaz. A (2018) A New Approach to Low-Cost Open-Typed Subsonic Compressible Flow Wind Tunnel for Academic Purpose
-
Design and construction of an open-circuit wind tunnel with specific measurement equipment for cycling Bert Celisa, , Harm
H. Ubbensb
-
Design of a Tri-sonic Wind Tunnel Avik Arora, Varun Adishankar, Jayakrishnan R.
-
Design, Construction, And Testing of An Open-Loop Low-Speed Wind Tunnel Muhammad Adnin Bin Mat Bahari
-
Design, Fabrication and Testing of A Small Scale Low Reynolds Number Table Top Wind Tunnel Syed Shahrukp, Nithin Raj N, Jayaprakash BP, Premkumar Naik R, Dr. G Balakalyani , S. Srinivasan
-
Small-Scale Open-Circuit Wind Tunnel: Design Criteria, Construction and Calibration Mauro S.*a, Brusca S.B, Lanzafame R.A, Famoso F.A, Galvagno A.B and Messina M.