
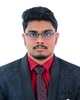
- Open Access
- Authors : Arnell Justin Arul Prince , Adem Sudarsan Reddy , Konduru Nagateja , Nagineni Nikhil Chowdary
- Paper ID : IJERTV10IS040129
- Volume & Issue : Volume 10, Issue 04 (April 2021)
- Published (First Online): 27-04-2021
- ISSN (Online) : 2278-0181
- Publisher Name : IJERT
- License:
This work is licensed under a Creative Commons Attribution 4.0 International License
Design and Analysis of A Spur Gear with Composite Material
Arnell Justin Arul Prince
B.Tech, Dept. Mechanical Engineering, Hindustan Institute of Technology and Science, Padur, Chennai
Adem Sudarsan Reddy
B.Tech, Dept. Mechanical Engineering, Hindustan Institute of Technology and Science, Padur, Chennai
Konduru Nagateja
B.Tech, Dept. Mechanical Engineering, Hindustan Institute of Technology and Science, Padur, Chennai
Nagineni Nikhil Chowdary
-
ech, Dept. Mechanical Engineering, Hindustan Institute of Technology and Science, Padur, Chennai
Abstract- Spur gears are the simplest and widely used in power transmission. In recent years it is required to operate machines at varying load and speed. Gear teeth normally fail when load is increased above certain limit. Therefore, it is required to explore alternate materials for gear manufacturing. Composite materials provide adequate strength with weight reduction and they have emerged as a better alternative for replacing metallic gears. Composites provide much improved mechanical properties such as better strength to weight ratio, more hardness, and hence less chances of failure. So this work is concerned with replacing metallic gear with composite material so as to improve performance of machine and to have longer working life. Efforts have also been carried out for modeling using 3D modelling software called SOLIDWORKS 2016 and finite element analysis of gears using ANSYS WORKBENCH R 2016. Composite gears have been manufactured by stir casting, which is economical method. Composite gears offer improved properties over steel alloys and these can be used as better alternative for replacing metallic gears.
Keywords-Composite material, Coir, Glass Fiber, Epoxy resin composite
-
INTRODUCTION
Spur gears or straight-cut gears are the simplest type of gear. They consist of a cylinder or disk with teeth projecting radially. Though the teeth are not straight-sided (but usually of special form to achieve a constant drive ratio, mainly involute but less commonly cycloidal), the edge of each tooth is straight and aligned parallel to the axis of rotation. These gears mesh together correctly only if fitted to parallel shafts.[1] No axial thrust is created by the tooth loads. Spur gears are excellent at moderate speeds but tend to be noisy at high speeds.[2]
Spur gear teeth are manufactured by either involute profile or cycloidal profile. Most of the gears are manufactured by involute profile with 20° pressure angle. When two gears are in mesh at one instant there is a chance to mate involute portion with non-involute portion of mating gear. This phenomenon is known as "interference" and occurs when the number of teeth on the smaller of the two meshing gears is less than a required minimum. To avoid interference we can have undercutting, but this is not a suitable solution as undercutting leads to weakening of tooth at its base. In this situation Corrected gears
are used. In corrected gears Cutter rack is shifted upwards or downwards
A gear or cogwheel is a rotating machine part having cut teeth or, in the case of a cogwheel, inserted teeth (called cogs), which mesh with another toothed part to transmit torque. Geared devices can change the speed, torque, and direction of a power source. Gears almost always produce a change in torque, creating a mechanical advantage, through their gear ratio, and thus may be considered a simple machine. The teeth on the two meshing gears all have the same shape.[1] Two or more meshing gears, working in a sequence, are called a gear train or a transmission. A gear can mesh with a linear toothed part, called a rack, producing translation instead of rotation.
The gears in a transmission are analogous to the wheels in a crossed, belt pulley system. An advantage of gears is that the teeth of a gear prevent slippage.
When two gears mesh, if one gear is bigger than the other, a mechanical advantage is produced, with the rotational speeds, and the torques, of the two gears differing in proportion to their diameters.
In transmissions with multiple gear ratiossuch as bicycles, motorcycles, and carsthe term "gear" as in "first gear" refers to a gear ratio rather than an actual physical gear. The term describes similar devices, even when the gear ratio is continuous rather than discrete, or when the device does not actually contain gears, as in a continuously variable transmission
-
ETYMOLOGY
The word gear is probably from Old Norse gørvi (plural gørvar) 'apparel, gear,' related to gøra, gørva 'to make, construct, build; set in order, prepare,' a common verb in Old Norse, "used in a wide range of situations from writing a book to dressing meat". In this context, the meaning of 'toothed wheel in machinery' first attested 1520s; specific mechanical sense of 'parts by which a motor communicates motion' is from 1814; specifically of a vehicle (bicycle, automobile, etc.) by 1888.[11]
Fig 1.1Wooden cogwheel driving a lantern pinion or cage gear
Fig 1.3
1.3Spur gear
Fig 1.2
A cast gearwheel (above) meshing with a cogged mortise wheel (below). The wooden cogs are held in place by nails.
Historically, cogs were teeth made of wood rather than metal, and a cogwheel technically consisted of a series of wooden gear teeth located around a mortise (or mortice) wheel, each tooth forming a type of specialised 'through' mortise and tenon joint. The wheel can be made of wood, cast iron, or other material. Wooden cogs were formerly used when large metal gears could not be cut, when the cast tooth was not even approximately of the proper shape, or the size of the wheel made manufacture impractical.[14]
The cogs were often made of maple wood. In 1967 the Thompson Manufacturing Company of Lancaster, New Hampshire still had a very active business in supplying tens of thousands of maple gear teeth per year, mostly for use in paper mills and grist mills, some dating back over 100 years.[15] Since a wooden cog performs exactly the same function as a cast or machined metal tooth, the word was applied by extension to both, and the distinction has been generally lost.
TYPES
-
Internal gear
An external gear is one with the teeth formed on the outer surface of a cylinder or cone. Conversely, an internal gear is one with the teeth formed on the inner surface of a cylinder or cone. For bevel gears, an internal gear is one with the pitch angle exceeding 90 degrees. Internal gears do not cause output shaft direction reversal.[16]
Spur gears or straight-cut gears are the simplest type of gear. They consist of a cylinder or disk with teeth projecting radially. Though the teeth are not straight-sided (but usually of special form to achieve a constant drive ratio, mainly involute but less commonly cycloidal), the edge of each tooth is straight and aligned parallel to the axis of rotation. These gears mesh together correctly only if fitted to parallel shafts.[17] No axial thrust is created by the tooth loads. Spur gears are excellent at moderate speeds but tend to be noisy at high speeds.[18]
-
Helical
Fig 1.4
Fig 1.5
Helical gears
Top: parallel configuration Bottom: crossed configuration
Helical or "dry fixed" gears offer a refinement over spur gears. The leading edges of the teeth are not parallel to the axis of rotation, but are set at an angle. Since the gear is curved, this angling makes the tooth shape a segment of a heix. Helical gears can be meshed in parallel or crossed orientations. The former refers to when the shafts are parallel to each other; this is the most common orientation. In the latter, the shafts are non- parallel, and in this configuration the gears are sometimes known as "skew gears".
The angled teeth engage more gradually than do spur gear teeth, causing them to run more smoothly and quietly.[19] With parallel helical gears, each pair of teeth first make contact at a single point at one side of the gear wheel; a moving curve of contact then grows gradually across the tooth face to a maximum, then recedes until the teeth break contact at a single point on the opposite side. In spur gears, teeth suddenly meet at a line contact across their entire width, causing stress and noise. Spur gears make a characteristic whine at high speeds. For this reason spur gears are used in low-speed applications and in situations where noise control is not a problem, and helical gears are used in high-speed applications, large power transmission, or where noise abatement is important.[20] The speed is considered high when the pitch line velocity exceeds 25 m/s.[21]
A disadvantage of helical gears is a resultant thrust along the axis of the gear, which must be accommodated by appropriate thrust bearings, and a greater degree of sliding friction between the meshing teeth, often addressed with additives in the lubricant.
-
Skew gears
For a "crossed" or "skew" configuration, the gears must have the same pressure angle and normal pitch; however, the helix angle and handedness can be different. The relationship between the two shafts is actually defined by the helix angle(s) of the two shafts and the handedness, as defined:[22]
-
for gears of the same handedness,
-
for gears of opposite handedness,
where is the helix angle for the gear. The crossed configuration is less mechanically sound because there is only a point contact between the gears, whereas in the parallel configuration there is a line contact.[22]
Quite commonly, helical gears are used with the helix angle of one having the negative of the helix angle of the other; such a pair might also be referred to as having a right-handed helix and a left-handed helix of equal angles. The two equal but opposite angles add to zero: the angle between shafts is zero that is, the shafts are parallel. Where the sum or the difference (as described in the equations above) is not zero, the shafts are crossed. For shafts crossed at right angles, the helix angles are of the same hand because they must add to 90 degrees. (This is the case with the gears in the illustration above: they mesh
correctly in the crossed configuration: for the parallel configuration, one of the helix angles should be reversed. The gears illustrated cannot mesh with the shafts parallel.)
-
3D animation of helical gears (parallel axis)
-
3D animation of helical gears (crossed axis)
-
-
-
Double helical
Fig 1.6
Double helical gears overcome the problem of axial thrust presented by single helical gears by using a double set of teeth, slanted in opposite directions. A double helical gear can be thought of as two mirrored helical gears mounted closely together on a common axle. This arrangement cancels out the net axial thrust, since each half of the gear thrusts in the opposite direction, resulting in a net axial force of zero. This arrangement can also remove the need for thrust bearings. However, double helical gears are more difficult to manufacture due to their more complicated shape.
Herringbone gears are a special type of helical gears. They do not have a groove in the middle like some other double helical gears do; the two mirrored helical gears are joined together so that their teeth form a V shape. This can also be applied to bevel gears, as in the final drive of the Citroën Type A.
For both possible rotational directions, there exist two possible arrangements for the oppositely-oriented helical gears or gear faces. One arrangement is called stable, and the other unstable. In a stable arrangement, the helical gear faces are oriented so that each axial force is directed toward the center of the gear. In an unstable arrangement, both axial forces are directed away from the center of the gear. In either arrangement, the total (or net) axial force on each gear is zero when the gears are aligned correctly. If the gears become misaligned in the axial direction, the unstable arrangement generates a net force that may lead to disassembly of the gear train, while the stable arrangement generates a net corrective force. If the direction of rotation is reversed, the direction of the axial thrusts is also reversed, so a stable configuration becomes unstable, and conversely.
Stable double helical gears can be directly interchanged with spur gears without any need for different bearings.
-
Bevel
Fig 1.7 Bevel gear operating a lock gate
Wooden cogs set in bevel mortise wheels driving a millstone. Note wooden spur gears in the background.
A bevel gear is shaped like a right circular cone with most of its tip cut off. When two bevel gears mesh, their imaginary vertices must occupy the same point. Their shaft axes also intersect at this point, forming an arbitrary non-straight angle between the shafts. The angle between the shafts can be anything except zero or 180 degrees. Bevel gears with equal numbers of teeth and shaft axes at 90 degrees are called miter (US) or mitre (UK) gears.
-
Spiral bevels
Fig 1.8
Spiral bevel gears can be manufactured as Gleason types (circular arc with non-constant tooth depth), Oerlikon and Curvex types (circular arc with constant tooth depth), Klingelnberg Cyclo-Palloid (Epicycloid with constant tooth depth) or Klingelnberg Palloid. Spiral bevel gears have the same advantages and disadvantages relative to their straight- cut cousins as helical gears do to spur gears. Straight bevel gears are generally used only at speeds below 5 m/s (1000 ft/min), or, for small gears, 1000 r.p.m.[23]
Note: The cylindrical gear tooth profile corresponds to an involute, but the bevel gear tooth profile to an octoid. All traditional bevel gear generators (like Gleason, Klingelnberg, Heidenreich & Harbeck, WMW Modul) manufacture bevel gears with an octoidal tooth profile. IMPORTANT: For 5-axis milled bevel gear sets it is important to choose the same calculation / layout like the conventional manufacturing method. Simplified calculated bevel gears on the basis of an equivalent cylindrical gear in normal section with an involute
tooth form show a deviant tooth form with reduced tooth strength by 10-28% without offset and 45% with offset [Diss. Hünecke, TU Dresden]. Furthermore, the "involute bevel gear sets" cause more noise.
-
Hypoid
Fig 1,9
Hypoid gears resemble spiral bevel gears except the shaft axes do not intersect. The pitch surfaces appear conical but, to compensate for the offset shaft, are in fact hyperboloids of revolution.[24][25] Hypoid gears are almost always designed to operate with shafts at 90 degrees. Depending on which side the shaft is offset to, relative to the angling of the teeth, contact between hypoid gear teeth may be even smoother and more gradual than with spiral bevel gear teeth, but also have a sliding action along the meshing teeth as it rotates and therefore usually require some of the most viscous types of gear oil to avoid it being extruded from the mating tooth faces, the oil is normally designated HP (for hypoid) followed by a number denoting the viscosity. Also, the pinion can be designed with fewer teeth than a spiral bevel pinion, with the result that gear ratios of 60:1 and higher are feasible using a single set of hypoid gears.[26] This style of gear is most common in motor vehicle drive trains, in concert with a differential. Whereas a regular (nonhypoid) ring-and-pinion gea set is suitable for many applications, it is not ideal for vehicle drive trains because it generates more noise and vibration than a hypoid does. Bringing hypoid gears to market for mass-production applications was an engineering improvement of the 1920s.
-
Crown
Fig 1.10
Crown gears or contrate gears are a particular form of bevel gear whose teeth project at right angles to the plane of the wheel; in their orientation the teeth resemble the points on a crown. A crown gear can only mesh accurately with another bevel gear, although crown gears are sometimes seen meshing with spur gears. A crown gear is also sometimes meshed with an escapement such as found in mechanical clocks.
-
Worm
Fig 1.11
4-start worm and wheel
Worms resemble screws. A worm is meshed with a worm wheel, which looks similar to a spur gear.
Worm-and-gear sets are a simple and compact way to achieve a high torque, low speed gear ratio. For example, helical gears are normally limited to gear ratios of less than 10:1 while worm-and-gear sets vary from 10:1 to 500:1.[27] A disadvantage is the potential for considerable sliding action, leading to low efficiency.[28]
A worm gear is a species of helical gear, but its helix angle is usually somewhat large (close to 90 degrees) and its body is usually fairly long in the axial direction. These attributes give it screw like qualities. The distinction between a worm and a helical gear is that at least one tooth persists for a full rotation around the helix. If this occurs, it is a 'worm'; if not, it is a 'helical gear'. A worm may have as few as one tooth. If that tooth persists for several turns around the helix, the worm appears, superficially, to have more than one tooth, but what one in fact sees is the same tooth reappearing at intervals along the length of the worm. The usual screw nomenclature applies: a one-toothed worm is called single thread or single start; a worm with more than one tooth is called multiple thread or multiple start. The helix angle of a worm is not usually specified. Instead, the lead angle, which is equal to 90 degrees minus the helix angle, is given.
In a worm-and-gear set, the worm can always drive the gear. However, if the gear attempts to drive the worm, it may or may not succeed. Particularly if the lead angle is small, the gear's teeth may simply lock against the worm's teeth, because the force component circumferential to the worm is not sufficient
to overcome friction. In traditional music boxes, however, the gear drives the worm, which has a large helix angle. This mesh drives the speed-limiter vanes which are mounted on the worm shaft.
Worm-and-gear sets that do lock are called self locking, which can be used to advantage, as when it is desired to set the position of a mechanism by turning the worm and then have the mechanism hold that position. An example is the machine head found on some types of stringed instruments.
If the gear in a worm-and-gear set is an ordinary helical gear only a single point of contact is achieved.[26][29] If medium to high power transmission is desired, the tooth shape of the gear is modified to achieve more intimate contact by making both gears partially envelop each other. This is done by making both concave and joining them at a saddle point; this is called a cone-drive[30] or "Double enveloping".Worm gears can be right or left-handed, following the long-established practice for screw threads.[16]
-
-
LITERATURE SURVEY
Rufus Ogbuka Chime
The range of computer applications in engineering design covers procedures from preliminary conceptual design to the production of manufacturing drawings and specifications. Most computer applications intended for production use can be classified into five or more major categories: analysis, computer-aided drafting and design, geometric modeling, data base management systems, and artificial intelligence. Gears are machine elements that transmit angular motion and power by the successive engagement of teeth on their periphery. They constitute an economical method for such transmission, particularly if power levels or accuracy requirements are high. Spur gears are the most common variety and the most economical to manufacture.. Axes of mating gears are parallel. Spur gears are used to transmit rotary motion between parallel shafts. They are cylindrical, and the teeth are straight and parallel to the axis of rotation. The pinion is the smaller of two mating gears; the larger is called the gear or the wheel. The scope of this work includes, to design, model and simulate Spur Gear, to select Gear materials ,to analysis spur gears also to detailed factor safety in design Computer aided design uses the mathematical and graphic processing power of the computer to assist the engineer in the creatoion, modification, analysis, and designs many factors have contributed to CAD technology becoming the necessary tool in the engineering technical data base, CAD combines the characteristic of designer and computer that are best applicable to the design process, the combination of human creativity with computer technology provides the design efficiency that has made CAD such as popular design tool. Gears are useful when the following kinds of power or motion transmission are required: (1) a change in speed of rotation, (2) a multiplication or division of torque or magnitude of rotation, (3) a change in direction of rotation, (4) conversion from rotational to linear motion or vice versa (rack gears), (5) a change in the angular orientation of the rotational motion (bevel gears), and (6) an offset or change in location of the rotating motion.
B.Sivakumar1, I. Joe Michael
A gear or gear wheel is a rotating machine part having cut teeth, or cogs, which mesh with another toothed part in order to transmit power. Two or more gears working in tandem are called a transmission and produce a mechanical advantages through a gear ratio and thus may be considered a simple machine. gears are mostly used in the mechanical field for power transmission, this project report on stress analysis of spur gears. Spur gear made of cast iron is considered as the conventional model in this project. The conventional model is optimized with carbon fiber high modulus material and the analysis is carried out. Boundary constraints are defined and the total deformations for model are calculated and the results are tabulated
S.Mahendran#, K.M.Eazhil*, L.Senthil Kumar
To design the spur gear to study the weight reduction and stress distribution for cast steel and composite materials. Gearing is one of the most critical components in a mechanical power transmission system, and in most industrial rotating machinery. It is possible that gears will predominate as the most effective means of transmitting power in future machines due to their high degree of reliability and compactness. In addition, the rapid shift in the industry from heavy industries such as shipbuilding to industries such as automobile manufacture and office automation tools will necessitate a refined application of gear technology. To design the spur gear model using designs software. To study the impact analysis for cast steel and composite materials. To study the torque loading for cast steel and composite materials. Finally, comparing and analyzing of the composite gear with existing cast steel gear is to be done.
Ms. Nilesha U. Patil1*, Mr. Sunil P. Chaphalkar2 ,Mr. Gajanan L. Chaudhari
Gears are machine elements used to transmit motion and power between rotating shafts by means of progressive engagements of projections. Gears have wide variety of applications. Their application varies from watches to very large mechanical units like the lifting devices and automotives. Engineering components made of composite materials find increasing applications ranging from space craft to small instruments. It is possible that gears will predominate as the most effective means of trasmitting power in future machines due to their high degree of reliability and compactness. The main objective of the present work is to investigate Finite Element Analysis of the spur gear pair for different material in ANSYS software. In this paper A review has been taken for case-I purpose is to design the spur gear and study the weight reduction and stress distribution for cast steel and composite materials and results are observed. And in case-II Static analysis is performed to determine the deformation and Von- mises stresses. Analysis is done by considering different materials for gears like Structural Steel, Gray Cast Iron, Aluminium Alloy and Epoxy E Glass UD, and results are compared.
R. Vigithra
Gears are machine elements used to transmit motion and power between rotating shafts by means of progressive engagements of projections. Gears have wide variety of applications. Their application varies from watches to very large mechanical units like the lifting devices and automotives. Engineering components made of composite materials find increasing applications ranging from space craft to small instruments. Overwhelming advantages such as light weight, higher dimensional stability and minimal attack by environment when compared with other ordinary mild steel gears. Modern level advanced polymer composite materials have opened a new level of soundless, lubricant free, high resilience and precision gearing in power and motion transmission. A proper understanding and prediction of gear failure is an important pre-requisite for any reliable application. In this project, a spur gear is designed using advanced modelling software (pro-engineer) and is meshed and analyzed using analysis software Abaqus 6.10 by the application of torque load. Two types of analysis are carried out using the software namely the static stress analysis and modal analysis. In static stress analysis tooth contact of a pair of spur gear system is analyzed as a body contact in three dimensional co- ordinates. The analysis consists of one loading condition to apply torque load on driving gear by constraining all degrees of freedom of driven gear. The hexagonal element model is meshed with in such a way that the elements around the gear teeth are fine and coarse at other places. The three dimensional elemental stresses and displacement magnitude are found out. Using modal analysis, the natural mode shapes and frequencies of composite gears is determined under free vibration. The interpretation of Eigen values which come from solving the system are that they represent the frequencies and corresponding mode shapes. The analysis is thus carried out making a comparison for a mild steel spur gear and carbon fibre
/ epoxy resin composite spur gear. The results in the variation of three dimensional stresses, displacement, frequencies and Eigen values are plotted and viability to manufacture such gears is predicted.
-
MODELING
-
INTRODUCTION TO SOLIDWORKS:
SolidWorks (stylized as SOLIDWORKS), is a solid modeling computer-aided design (CAD) and computer-aided engineering (CAE) software program that runs on Microsoft Windows. The SolidWorks is produced by the DASSAULT SYSTÈMES a subsidiary of Dassault Systèmes, S. A. based in Velizy, France since 1997.
SolidWorks is currently used by over 2 million engineers and designers at more than 165,000 companies worldwide. In 201112, the fiscal revenue for SolidWorks was reported $483 million.
HISTORY:
SolidWorks Corporation was founded in December 1993 by Massachusetts Institute of Technology graduate Jon Hirschtick, Hirschtick used $1 million he had made while a member of the MIT Blackjack Team to set up the
company. Initially based in Waltham, Massachusetts, USA, Hirschtick recruited a team of engineers with the goal of building 3D CAD software that was easy-to-use, affordable, and available on the Windows desktop. Operating later from Concord, Massachusetts, SolidWorks released its first product SolidWorks 95, in 1995. In 1997 Dassault, best known for its CATIA CAD software, acquired SolidWorks for $310 million in stock.
SolidWorks currently markets several versions of the SolidWorks CAD software in addition to e Drawings, a collaboration tool, and Draft Sight, a 2D CAD product. SolidWorks was headed by John McEleney from 2001 to July 2007 and Jeff Ray from 2007 to January 2011. The current CEO is Gian Paolo Bassi from Jan 2015. Gian Paolo Bassi replaces Bertrand Sicot, who is promoted Vice President Sales of Dassault Systèmes Value Solutions sales channel.
CREATING A PART AND DRAWING:
When SolidWorks is first opened, you have to open a part, assembly or drawing. When a new part is opened, there is a blank work area on the right and a column on the left called the Feature Manager. In the Feature Manager, there are the three main planes listed front, top and right. To begin a sketch, a plane to draw on must be selected. Right click on the desired plane and select the sketch icon in the fly-out menu. For the first sketch the view will rotate so that you are looking perpendicular to the plane you selected.
The first feature sketched is called the base feature. Added on features are called boss or cut features. These add or subtract material to create the part. It is best to keep the geometry of each feature as simple as possible. Create a part with a large number of simple features rather than a few complex ones. Your work will be much easier to perform and less prone to errors in the long run.
Plan how the part is going to be used before beginning the sketch. Which faces do you want for the front, top and right views? Where do you want the origin to be? It is easier to take a few minutes and plan ahead than to have to redo a part because the wrong orientation was used. A quick hand sketch on a sheet of paper to determine the final appearance can save a lot of effort and time. A good habit to get into is to place the origin on a plane of symmetry if there is one. This will save you a lot of work in creating a part.
When you start sketching the base, rough out what the base face will look like. It does not have to be exactly to dimensions. When you finish your rough sketch most lines will be blue. This means that you have an under-defined sketch. At this point you add geometric relations or constraints and dimensions to the drawing to get it completely defined. A fully defined sketch has all black lines. You will also see near the bottom right of the screen a note Fully Defined. If it says u\ Under Defined you will need more dimensions or relations before extruding. If you try to define it too much the sketch turns red meaning that it is over-defined. At this point you will have to remove some relations or dimensions to get back to completely defined. Once you have a fully defined sketch, then you can extrude it or revolve it to create the base. Get in the habit of extruding and
cutting with fully defined features only as it will save time and effort later on.
After the base feature is created, additional features may be added. Again the new features must be sketched on a plane. This plane can be one of the three primary planes, one of the faces of the base or any boss, or on a user defined plane. Right click on the plane desired, then select the sketch icon. In the transparent view menu o at the top of the work area select the view orientation to do the sketch. Try to use the geometric relations as much as possible to orient a new feature to a previous feature. Thus if the first feature is changed, the second feature will follow along with it rather than having to be re- dimensioned. SolidWorks is a parametric program, which means that the dimensions drive the size and shape of the part rather than the reverse. The benefit of this is that a parts size and shape can be altered by just changing the appropriate dimension rather than having to redraw the part. Careful selection of the geometric relations and dimensions can simplify the task.
MODELING METHODOLGY:
SolidWorks is a solid modeler, and utilizes a parametric feature-based approach to create models and assemblies. The software is written on Para solid-kernel.
Parameters refer to constraints whose values determine the shape or geometry of the model or assembly. Parameters can be either numeric parameters, such as line lengths or circle diameters, or geometric parameters, such as tangent, parallel, concentric, horizontal or vertical, etc. Numeric parameters can be associated with each other through the use of relations, which allows them to capture design intent.
Design intent is how the creator of the part wants it to respond to changes and updates. For example, you would want the hole at the top of a beverage can to stay at the top surface, regardless of the height or size of the can. SolidWorks allows the user to specify that the hole is a feature on the top surface, and will then honor their design intent no matter what height they later assign to the can.
Features refer to the building blocks of the part. They are the shapes and operations that construct the part. Shape-based features typically begin with a 2D or 3D sketch of shapes such as bosses, holes, slots, etc. This shape is then extruded or cut to add or remove material from the part. Operation-based features are not sketch-based, and include features such as fillets, chamfers, shells, applying draft to the faces of a part, etc.
Building a model in SolidWorks usually starts with a 2D sketch (although 3D sketches are available for power users). The sketch consists of geometry such as points, lines, arcs, conics (except the hyperbola), and splines. Dimensions are added to the sketch to define the size and location of the geometry. Relations are used to define attributes such as tangency, parallelism, perpendicularity, and concentricity. The parametric nature of SolidWorks means that the dimensions and relations drive the geometry, not the other way around. The dimensions in the sketch can be controlled independently, or
by relationships to other parameters inside or outside of the sketch.
In an assembly, the analog to sketch relations are mates. Just as sketch relations define conditions such as tangency, parallelism, and concentricity with respect to sketch geometry, assembly mates define equivalent relations with respect to the individual parts or components, allowing the easy construction of assemblies. SolidWorks also includes additional advanced mating features such as gear and cam follower mates, which allow modeled gear assemblies to accurately reproduce the rotational movement of an actual gear train.
CHANGING VIEWS:
It is best to carefully consider the presentation of what face goes with what view before beginning a part. However, if you have selected wrong and discover this well into the part constructions, may be possible to redefine the standard views. With the part showing and all sketches closed, select the view orientation tool on the Feature Tab, or Insert Modify View Orientation, or just press the space bar. The icon looks like a telescope. An orientation dialogue box will appear. Click on the push pin to keep the box open. Double click on the view name in the box which you wish to change. Then single click on the view you wish it to be. Finally, click on the update standard views, the center icon on the top of the box. You will get a warning message which states Changing the standard view will change the orientation of any standard orthogonal, named and child views in the drawings of this model. Select yes to make the change. You may reset the standard views you first selected by clicking on the right icon Reset Standard Views, or by just redefining the standard views again. Click the X in the upper right corner to close the dialogue box when you are done.
Finally, drawings can be created either from parts or assemblies. Views are automatically generated from the solid model, and notes, dimensions and tolerances can then be easily added to the drawing as needed. The drawing module includes most paper sizes and standards (ANSI, ISO, DIN, GOST, JIS, BSI and SAC).
FILE FORMAT:
SolidWorks files use the Microsoft Structured Storage file format. This means that there are various files embedded within each SLDDRW (drawing files), SLDPRT (part files), SLDASM (assembly files) file, including preview bitmaps and metadata sub-files. Various third-party tools (see COM Structured Storage) can be used to extract these sub- files, although the sub files in many cases use proprietary binary file formats.
COMMONLY USING TOOLS FOR MODELLING IN SOLIDWORKS:
-
Extrude
-
Extrude cut
-
Revolve
-
Revolve cut
-
Sweep
-
Swept cut
-
Fillet
-
Chamfer
-
Mirror
-
Pattern
-
-
CALCULATIONS:
Module-3 tooth-14,Outer dia-60mm,Inner dia- 25mm,Thickness=6mm
Standard proportions:
-
American Standard Association (ASA)
-
American Gear Manufacturers Association (AGMA)
-
Brown and Sharp
-
14 ½ deg; 20 deg; 25 deg pressure angle
-
Full depth and stub tooth systems.
Specifications for standard gear teeth:
Table 3.1
Forces on spur gear teeth
Ft = Transmitted force
Fn = Normal force or separating force
Fr = Resultant force
-
= pressure angle
Fn= Ft tan
Fr = Ft/ cos
Forces on spur gear teeth:
Power, P= T n/63,000
-
Torque, T = Ft r and r = Dp/2
-
Combining the above we can write Ft= T 2/ D p
14-tooth, 8 pitch, 1-inch-wide, 20°
Determine driving force, separating force, and maximum force that would act on mounting shafts.
P = Tn / 63,000 T = 63,000P/n
T = (63,000)5 / 1725
= 183 in-lb
Find pitch circle: Dp= Np / Pd
Dp= 14 teeth / 8 teeth/in diameter
Dp= 1.75in (Material Used for Spur Gear Is CAST IRON Find transmitted force:
Ft = 2T/Dp
Ft = (2)183 in-lb / 1.75in = 210 lb
Find separating force:
Fn = Ft tan
Fn =210lb tan 20° Fn = 76 lb
Find maximum force:
Fr = Ft cos
Fr = 146 lb cos 20° Fr = 138 lb
-
-
Design Procedure: 2d layout of Spur gear-
3.3 3D MODEL TOP VIEW
Fig 3.1 FRONT VIEW
Fig 3.2 SIDE VIEW
Fig 3.3 TOP VIEW
Fig 3.4
SIDE VIEW
FRONT VIEW
ISOMETRIC VIEW
Fig 3.5
Fig 3.6
Fig 3.7
-
-
ANALYSIS
project is driven by a schematic workflow, represented visually on a flowchart like diagram called the Project Schematic. To build an analysis, you add building blocks called systems to the Project Schematic; each system is a block of one or more components called cells, which represent the sequential steps necessary for the specific type of analysis. Once you have added your systems, you can link them together to share and/or transfer data between systems. From the cells in the Project Schematic, you can work with various ANSYS applications and analysis tasks. Some of these open in tabs within the Workbench environment, while others open independently in their own windows.
ANSYS applications allow you to specify parameters such as geometry parameters, material properties and boundary conditions. Parameters can be defined within the application and managed at the project level in the Workbench environment. To perform your analysis, you will work through the cells of each system in order typically from top to bottom defining inputs, specifying project parameters, running your simulation, and investigating the results. Workbench enables you to easily investigate design alternatives. You can modify any part of an analysis or vary one or more parameters, and then automatically update the project to see the effect of the change on the simulation result.
THE PROJECT TAB
When yo open a project in ANSYS Workbench, it opens to the Project tab. The Project tab is just one of many tabs that can be opened in Workbench, but it is the main workspace in which you will build your analysis.
Like all tabs, the Project tab is made up of different views that can be reconfigured according the information you want to see. By default, the Project tab is comprised of the Toolbox view and the Project Schematic view.
THE TOOLBOX IN THE PROJECT TAB
The Workbench Toolbox view contains the types of data you can add to your project.
In the Project tab, the Toolbox contains the different types of systems you can add to the Project Schematic. Systems are divided into categories which can be expanded or collapsed to show or hide the systems in that category. You can select systems from the following categories:
-
Analysis Systems
-
Component Systems
-
Custom Systems
-
Design Exploration
-
External Connection Systems
-
-
-
ANSYS WORKBENCH
ANSYS Workbench combines the strength of our core simulation tools with the tools necessary to manage your projects. You will work with your ANSYS Workbench project on the main project workspace, called the Project tab. The
ANSYS WORKBENCH SYSTEMS
The systems available in the Project tab Toolbox are divided into the following categories:
-
Analysis Systems
Complete systems with all the necessary component cells already defined and
ready to be populated. For example, a Static Structural analysis system includes all the cells needed for the analysis, Engineering Data through Results.
-
Component Systems
Component building blocks which represent only a subset of a complete analysis. For example, you can use a Geometry component system to define your geometry and then connect the component system to several downstream systems, so component system can then be connected to several downstream systems, so that the downstream systems share the same geometry source.
The Component Systems category also includes applications that open outside of ANSYS Workbench (rather than as a tab), allowing you to use Workbench to manage your analysis data and files. This can be useful for products such as Mechanical APDL, which uses numerous files during an analysis.
-
Custom Systems
Predefined templates for custom coupled systems, comprised of multiple analysis
systems with predefined data connections. You can also create templates for your own custom system templates, which will then be stored and displayed as part of this category.
-
Design Exploration
Design Xplorer systems that can be added beneath the Parameter Set bar, allowing you to perform various design exploration studies.
-
External Connection Systems
Enables you to integrate custom, lightweight, external applications and processes into the ANSYS Workbench Project Schematic workflow. Features exposed by the External Connection also allow you to perform automation and customization activities. With the External Connection, you can integrate custom, lightweight, external applications; define User Interface (UI) elements, such as buttons in the Workbench Toolbar or entries in custom menus, and create the scripts that enable them; and create new systems to facilitate interaction with the Workbench Project Schematic.
ANALYSIS SYSTEMS
One way to start an analysis in ANSYS Workbench is to select an analysis system from the Toolbox. When you select one of these analysis types, the corresponding system will appear in the Project Schematic, with all the necessary components of that type of analysis. Some analysis types offer different solvers, noted in parentheses. The features available can differ from one solver to another.
Available analysis systems include:
-
Design Assessment
-
Electric
-
Explicit Dynamics
-
Fluid Flow (CFX)
-
Fluid Flow (Fluent)
-
Fluid Flow (Polyflow)
-
Harmonic Response
-
Hydrodynamic Diffraction
-
Hydrodynamic Time Response
-
IC Engine
-
Linear Buckling and Linear Buckling (Samcef)
-
Magneto static
-
Modal and Modal (Samcef)
-
Random Vibration
-
Response Spectrum
-
Rigid Dynamics
-
Static Structural and Static Structural (Samcef)
-
Steady-State Thermal and Steady-State Thermal (Samcef)
-
Thermal-Electric
-
Through flow
-
Transient Structural and Transient Structural (Samcef)
-
Transient Thermal and Transient Thermal (Samcef) When you either double-click or drag an analysis system onto the Project Schematic it appears in the Project Schematic as a system. Components for that analysis type's system are listed as individual cells.
For example, a typical structural analysis might have the following components/cells:
-
-
Engineering Data
-
Geometry
-
Model/Mesh
-
Setup
-
Solution
-
Results
Right-click on each cell to see a menu of actions that are available for that cell. Selecting an action may launch a separate application, if appropriate. When you've completed the necessary actions in that application, you can solve in the application or return to the Project Schematic to Update the project and continue. Updating a project allows other systems or other cells within the same system to acquire the newest information.
ANSYS Workbench provides templates for some of the commonly used coupled analyses, such as one-way FSI analyses, pre-stress modal, thermal stress, random vibration, and response spectrum. Select these templates from the Custom Systems area of the Toolbox.
STRUCTURAL ANALYSIS
The ANSYS structural analysis software suite is trusted by organizations around the world to rapidly solve complex structural engineering problems with ease. FEA analysis (finite element) tools from ANSYS provide the ability to simulate every structural aspect of a product:
-
Linear static analysis that simply provides stresses or deformations
-
Modal analysis that determines vibration characteristics
-
Advanced transient nonlinear phenomena involving dynamic effects and complex behaviors
-
-
-
MATERIALS CHOSE FOR ANALYSIS:
-
Glass fibre
-
Coir fibre Glass Fiber
Glass fiber properties:
Table 4.2
-
-
Analysing Procedure Ansys Imported
Table 4.1
Fig 4.3 Fixed support
Fig 4.4 Force applied
-
GLASS FIBER: DEFORMATION:
Fig 4.1
Meshed
Fig 4.5
Fig 4.2
STRAIN
Result:
S.no
Deformation(mm)
Cast iron
1.1101
Coir fiber
1.0428
Glass fiber
1.0137
STRESS
-
COIR FIBER DEFORMATION
STRESS
STRAIN
Fig 4.6
Fig 4.7
Fig 4.8
Fig 4.9
Table 4.3 5.CONLUSION
The literature survey of composite spur gear was performed. Then the study in weight reduction and stress distribution of spur gear for cast steel and composite materials has been done. On the basis of that study, the analysis of both cast steel and composite materials are analyzed in the application of gear box which is used in automobile vehicles. From these analysis we got the stress values for composite materials is less as compared to the cast steel spur gear. So from these analysis results, we conclude that, the stress induced, deformation and weight of the composite spur gear is less as compared to the cast steel spur gear. So, Composite materials are capable of using in automobile vehicle gear boxes up to 1.5KN in the application of Tata super ace model instead of existing cast steel gears with better results.
REFERENCES
[1]. V. Siva Prasad, Syed AltafHussain, V.Pandurangadu, K.PalaniKumar, Modeling and Analysis of Spur Gear foSugarcane Juice Machine under Static Load Condition by Using FEA, International Journal of Modern Engineering Research (IJMER), Vol.2, Issue.4, July-Aug 2012 pp-2862-2866, ISSN: 22496645 [2]. K. Mao, A new approach for polymer composite gear design, Mechanical Engineering, School of Engineering and Design, Brunel University,Uxbridge, Middlesex UB8 3PH, UK, accepted 14 June 2006
[3]. K. Mao, A numerical method for polymer composite gear flash temperature prediction, Mechanical Engineering, School of Engineering and Design Brunel University, Uxbridge, Middlesex UB8 3PH, UK, accepted 8 January 2007 [4]. S. Kirupasankar, C. Gurunathan, R. Gnanamoorthy,Transmission efficiency of polyamide nanocomposite spur gears, Indian Institute of Information Technology, Design and Manufacturing (IIITD&M) Kancheepuram, Melakottaiyur, Chennai 600 048, India, Materials and Design 39 (2012) 338-343
[5]. N.A. Wright1, S.N. Kukureka, Wear testing and measurement techniquesforpolymer composite gears, School of Metallurgy and Materials, The University of Birmingham, Edgbaston, Birmingham B15 2TT, UK, Wear 251 (2001) 15671578. [6]. JesperBrauer, SörenAndersson, Simulation of wear in gears with flank interferencea mixed FE and analytical approach, Department of Machine Design, KTH, Brinellvagen 83, 100 44Stockholm, Sweden, Wear 254 (2003) 12161232.
Fig 4.10