
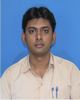
- Open Access
- Authors : Pramod S. Patil , Sunil Tulsiram Meharwade , Mohan Charan Patra
- Paper ID : IJERTV11IS040191
- Volume & Issue : Volume 11, Issue 04 (April 2022)
- Published (First Online): 05-05-2022
- ISSN (Online) : 2278-0181
- Publisher Name : IJERT
- License:
This work is licensed under a Creative Commons Attribution 4.0 International License
Design and Analysis of an Antenna Assembly Structure with optimum dynamic behaviour for Radar Applications
Pramod S. Patil D&E – Radar System-NS2, Bharat Electornics Limited,
Bangalore, India
Sunil Tulsiram Meharwade D&E – Radar System-NS2, Bharat Electornics Limited, Bangalore, India
Mohan Charan Patra D&E – Radar System-NS2, Bharat Electornics Limited, Bangalore, India
Abstract- An Antenna Assembly Fixture used as a securing frame to an antenna is basically a mounting structure. Antenna Structure means any structure, including a pole, mast, or tower, whether freestanding or mounted on another building or structure, that supports an antenna or an array of antennas. The height of an antenna structure is measured to the highest point of any antenna mounted thereon.
With the advance of technology the radar antenna structures are being smaller and their design alternatives are quite numerous that they can be produced in different shapes and can be conformed to original structures such as body panel of an aircraft [5] or car which is composed of light weight thin shell structures. Radar antennas as an integral part of the air or ground vehicles are subjected to various dynamic loadings which affect its overall radiation pattern which results overall degradation of antenna performance, especially at high amplitude resonance conditions due to low stiffness of host structures. In this study, to verify the adopted design concept, an Antenna Assembly Fixture was designed, analyzed and simulated for optimum dynamic behavior using Finite Element Analysis (FEA).
Keywords Passive vibration control, surface damping treatment, Narrow Flange Beam, topology optimization, parametric design and optimization, Planarity, Finite Element Method, modal strain energy, Factor of safety.
-
INTRODUCTION
The passive vibration control [1], namely surface damping treatment methodology is one of the measurement techniques that can be taken account at the initial design phase of such integration process which is based on increasing the damping capacity of host structure by adding viscoelastic materials between contacting surfaces. However, adding high density materials results increase of overall weight. Therefore, an extensive research activity has been carried out in order to design of surface damping treatment with spacer layer with minimum weight and maximum damping constraints [2].
In this study, to verify the design methodology, a Narrow Flange Beam (NFB) [3] [4] as per Bureau of Indian standards that represents the host structure, was designed, analyzed and tested for optimum dynamic behavior [2] [3]. Mainly topology and parametric optimization methods [13] are used in order to find best material layout of uniform spacer and best slotted configuration of spacer layer that maximize the damping performance of the design with minimum material condition. Experimental study is also conducted for layered
cantilever beam with developed concept design of slotted configuration under vibration load to verify the methodology used.
Radar Antennas
Advances in modern technology together with expanding needs have made possible various practical applications in communication field either in military and civilian sector. Especially the wireless technology is one of the growing field that allows us to send, convey and receive data regardless of location and distances without the need of cables or any other forms of electrical conductors through the use of a source of electrical energy, antenna elements and conductive space, which is usually open atmosphere, altogether forming a communication network.
In military applications one of the application area of wireless communication is, Radio Detection and Ranging, shortly Radar which was developed in World War II to detect the enemy targets. Through the years the application areas and their functions have been widened and they have been used for tactical, intelligence, surveillance, and reconnaissance purposes as well as keeping air routes safe by tracking air traffic, detecting moving targets such as missiles, vehicles for speed measurement and even in image generation purposes.
In radar systems, the generated electromagnetic waves are directed to an object or an area from which the required information will be collected. This process resembles the illumination of a region by a light. The waves collide, bounce and scattered back from the target locations then the antenna elements collect those bounced waves back again in order to gather desired information from it via signal processing.
A radar system performs this action continuously and simultaneously for stationary or moving targets [1]. The antenna is the first element in the transmitting or receiving those signals which are described as travelling electromagnetic waves in space/air. Depending on the purpose, antennas can work either in transmitter or receiver modes. Basically the electrical energy is converted into electromagnetic waves and antennas are used to radiate those waves in the form of a beam that is received by another antenna at which the electromagnetic waves are then converted into electrical signals after signal processing [2].
-
RADAR ASSEMBLY FIXTURE DESIGN
Radar consists of 4 types of radiating panels which needs to be assembled precisely on a mechanical antenna frame. The large structure of the complete Radar antenna. The heat load from the electronics is removed through liquid cooling. The antenna frame is a mechanical frame built with hollow tube sections bolted to each other to form an octagonal shape. Each Radiating panel weighs around 2.5 tons. The Radar assembly consists of Radiating assembly, Cooling network, mechanical fixture, brackets, RF cables etc. the overall weight of the whole Radar with all the assembly is around 25 tons.
To handle such a huge tonnage of load a special unique rugged fixture has to be designed to handle the assembly load in horizontal & vertical condition. The fixture should also take into account the center of gravity since maintaining the antenna assembly in vertical condition is very critical for the next NFTR assembly
In order to meet all the design requirements, the fixture is designed using standard narrow flange beams from Bureau of Indian Standards as per IS-12778. The narrow flange beam is used to have a longer section depth between the flanges to ensure stable load handling as indicated in Fig 1.
-
Fixture design details
Fig 1 : Radar assembly fixture (Front view)
Fig 2 : Radar assembly fixture (isometric view)
The fixture consists 4 nos of NPB 450 X 190 AS beams welded to each other to form a square section (refer Fig 2).
The NPB beams are reinforced with NPB 400 x 180 beams at all the corner of the squared section of the fixture.
To overcome the stress along the section of the beam gussets are welded to both sides of beam across the section. The fixture is divided into two U-sections which are bolted together to form the square shape. The fixture has lifting eye pads on either sides of the fixture to hoist the Radar assembly in horizontal & vertical condition using heavy duty cranes. The purpose of making the fixture into two U-sections is to handle the fixture safely during transportation.
-
Structural Analysis
The assembly fixture is analyzed for equivalent stress [6] both in horizontal & vertical condition using ANSYS workbench analysis software. The results are as shown below.
Fig. 3 : Equivalent stress in horizontal hoisting
The max equivalnt stress observed when the fixture is hoisted with the Radar assembly is 170.01 MPa which is under safe design limits. (Refer Fig.3)
Fig.4 : Total deformation in horizontal hoisting
The total deformation observed when the fixture along with radar assembly is hoisted in horizontal condition is 1.732 mm max, which is under safe design limits. (Refer Fig 4)
Fig 5 : Equivalent stress in Vertical hoisting
The max equivalent stress observed when the fixture is hoisted with the Radar assembly is 105.42 MPa which is under safe design limits. (Refer Fig 5)
Fig 6 : Total deformation in Vertical hoisting
The total deformation observed when the fixture along with radar assembly is hoisted in horizontal condition is 3.16 mm max, which is under safe design limits. (Refer Fig 6)
-
-
RESULTS AND DISCUSSIONS
Developing an integrated modular fixture design and assembly system is the major objective of this paper. The previous chapter has technically validated the Assembly Fixture in terms of load handling, ease of Mounting Antenna, Handling the fixture and operating within safe limit in terms of stress and deformation, ability to balance mass by keeping center of gravity in control and Factor of Safety. These simulation results have been validated with multiple iterations using a MCAD tool.
The design of Antenna Assembly Fixture for Heavy Duty Antenna structure was conceptualized through detailed solid modeling and simulation. Detailed FE Analysis for the Assembly Fixture was carried out to keep stresses encountered during vibrations [8] [9] [10] and Shock at bay.
The corresponding stress and deformation values are well within the acceptable limits.
The deformation and stress values achieved for various load conditions are listed in Table-1
Sl No.
Hoisting Position
Equivalent Stress
Total Deformation
1
Horizontal
186.63 Mpa
5.02 mm
2
Vertical
106.79 Mpa
7.71 mm
3
Factor of Safety
2
Table-1 Deformation and Stress Values
-
CONCLUSION
The major parameters (such as Return Loss curves, Radiation Patterns, Directivity and Beam-width) that affect design and applications were studied and their implications understood. Planarity and Flatness values on the mounting surface of the Antenna Assembly fixture are two major factors contributing for optimum electrical characteristics and for higher performance of Antenna. The planarity and flatness parameters for the Antenna Assembly Fixture have been imbibed at the design stage for achieving optimum electrical performance by means of Jigs, Fixtures and CNC machining. The overall planarity and flatness value is ±1.0mm across the total mounting surface area of 6.5m x 6.5m.
Another important feature of the Assembly Fixture is the ability to handle total Antenna load of 25 Tons with respect to its self-weight of 6 Tons. The simulation results indicate stability in operation with respect to deformation and strength using FEM analysis.
ACKNOWLEDGEMENTS
The authors would like to thank. Sri Umesh K S, General Manager, NS2, BEL, for giving us the opportunity to work on this project. He provided the motivation through his vast knowledge and experience in BEL Radars.
It is our duty to thank Smt. Dharani B, AGM, NS2, BEL, for her valuable suggestions and support during the course of the project. It was a good learning experience for us to work with their vast experience in Radar areas.
REFERENCES
[1] John E. Sirmalis, (1997), Extendible planar phased array mast,The United States of America as Represented by the Secretary of the Navy Patent
[2] US5977918 A (Patent) [3] Z. Xie, F. Peng, P. Zhang, W. Zhao, (2014), A smart Skin Antenna Structure for Global Navigation Satellite System, Applied Mechanics and Materials Vols.464, pp:316-320 [4] A.J. Lockyer, J.N. Kudva, D. Kane, B.P. Hill, C.A. Martin, A.C. Goetz, et al. (1994), A qualitative assessment of smart skins and avionic/structures integration, Proc. SPIE 2189, Smart Structures and Materials, 172 pp. 172183 [5] M.A. Hopkins, J.M. Tuss, A.J. Lockyer, K. Alt, R. Kinslow, J.N. Kudva, (1997), "Smart skin conformal load-bearing antenna and other smart structures developments", Collection of technical papersAIAA/ASME/ASCE/AHS/ASC structures, structural dynamics and materials conference, pp. 521530. [6] H.Schippers, H.V.Tongeren, Jaco Verpoorte and G.Vos, (2001), Distortion of Conformal Antennas on Aircraft Structures, Smart Structure and Materials, Proc. Of SPIE,Vol.4334 [7] P. Knott, C. Locker, S. Algermissen, and W. Gruner, Research on vibration control and structure integration of antennas,NATO/RTO/SET-131, in 2010
[8] P. Knott, "Deformation and Vibration of Conformal Antenna-arrays and Compensation Techniques", Paper presented at Multifunctional Structures/Integration of Sensors and Antennas, Paper 19, Neuilly- sur-Seine, France, 2006. [9] H. Schippers, J.H. van Tongeren, P. Knott, T. Deloues, P. Lacomme, and M.R. Scherbarth, "Vibrating Antennas and Compensation Techniques Research, NATO/RTO/SET 087/RTG 50," IEEE Aerospace Conference, 3-10 March 2007 [10] H. Schippers, J.H. van Tongeren, G. Vos, Development of Smart Antennas on Vibrating Structures of Aerospace Platforms", Paper presented at Multifunctional Structures/Integration of Sensors and Antennas, Paper 20, Neuilly-sur-Seine, France, 2006. [11] Lumsdaine, A. And Scott, R.A., Shape optimization of Unconstrained Viscoelastic Layers Using Continuum Finite Elements, Journal of Sound and Vibration, Vol. 216, No.1, p.29-52, (1998). [12] Johnson, C.D. and Kienholz, D.A. (1982), Finite Element Prediction of Damping in Structures with Constrained Viscoelastic Layers, AIAA Journal, 20(9), pp.1284-1290 [13] Lumsdaine, Topology optimization of constrained damping layer treatments, in Proceedings of the ASME International Mechanical Engineering Congress and Exposition, pp. 149156, New Orleans, La, USA, November 2002ABOUT AUTHORS
Shri. Pramod S. Patil is currently working in Bharat Electronics Limited, Bangalore as Manager. He obtained his B.E in mechanical in the year 2004 from BVBCET, VTU University Hubli, Karnataka. His area of interests is Design & development of structures, electronic enclosures, structural & thermal analysis for Radars.
Shri. Sunil Tulsiram Meharwade is currently working in Bharat Electronics Limited, Bangalore as Manager. He obtained his B.E in Mechanical in the year 2006 from R.V.College of Engineering, VTU, Bangalore, Karnataka. His area of interests is Design & Development of mechanical system and hardware for radars.
Shri. Mohan Charan Patra is currently working in Bharat Electronics Limited, Bangalore as Deputy General Manager. He obtained his B.E degree in Mechanical Engineering in the year 1999 from NIT, Tiruchirapalli, T.N. His areas of interest is Mechanical Design of Radar Systems.