
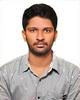
- Open Access
- Authors : Jayanth Burri , Anirudh Kyatham , Sriram Katta , Koushik Alapati, Dr. P. V. S. Subhashini
- Paper ID : IJERTV10IS110177
- Volume & Issue : Volume 10, Issue 11 (November 2021)
- Published (First Online): 03-12-2021
- ISSN (Online) : 2278-0181
- Publisher Name : IJERT
- License:
This work is licensed under a Creative Commons Attribution 4.0 International License
Design and Analysis of Chassis for a FSAE Car
Jayanth Burri1, Anirudh Kyatham2, Sriram Katta3, Koushik Alapati4
1,2,3,4 Graduates Mechanical Engineering
Vasavi College of Engineering Hyderabad, Telangana, India.
Dr. P. V. S. Subhashini1 Assistant Professor Mechanical Engineering Vasavi College of Engineering Hyderabad, Telangana, India.
Abstract Design and Analysis of Tubular frame chassis for a formula Student competition involve optimizing various parameters that ultimately affect the vehicle's performance.
The focus goes behind achieving high torsional, longitudinal, and lateral Stiffness, including strength to withstand various real-time situations performed during race conditions and reducing the number of members, weight, and accommodating a male Percy (95th percentile) and female Percy (5th percentile) drivers in it.
Here, while choosing the appropriate material, various considerations are taken and selected as per multiple requirements such as mechanical properties, strength to weight ratio, including market availability and price.
Keywordscomponent; formatting; style; styling; insert (key words)
-
INTRODUCTION
The main idea of designing tubular frame chassis is to accommodate all vehicle components for the functional aspect of the car and reduce the weight; furthermore, it requires knowledge regarding the subjects of aerodynamics, transmission, braking, suspension, impact attenuator and materials [1] – [4].
There are different types of chassis used in formula cars namely space frame chassis, ladder-frame chassis and composite monocoque chassis are widely used [5]. The tubes are welded together to create space frame chassis, the ladder frame chassis has a ladder shape and the composite monocoque chassis is made of single composite material.
Initially, the design of the roll cage starts with ergonomics. They are then designed according to the 95th percentile male, fitting the driver into the cockpit, accessible to the brake pedal, steering dashboard, and steering wheel [6]. This process also helps find the appropriate planes for placing the Bulkhead, front hoop, and main hoop. Later, as per the engine spacing and transmission requirements, a plane is chosen to accommodate the engine head.
During the real-time situation, a race car is acted upon by various loads statically and dynamically, generating various stresses needed to absorb the roll cage. These forces cause deformation in multiple portions of it, which are caused by acceleration or braking or cornering or when acted simultaneously. So, to resist these conditions, it needs to be
rigid enough; therefore, various tests are analyzed statically to maximize the strength and keep the driver safer [2].
The strength of a chassis depends upon factors such as material properties, weld strength and the tube cross-section. In the general process of material selection, we check the bending strength and bending stiffness for a given cross- section of the available materials or vice versa sometimes weaker materials with large cross-sections have high bending stiffness, so finding the right material with the right cross- section can reduce space and the number of tubes used in the structure [7][8].
For the chassis design, modal analysis, vibration analysis, front-impact, side-impact, torsional rigidity, rollover impact is conducted. This is done in Finite Element Analysis (FEM) to save time and testing expenditure [9]-[12].
-
DESIGN AND MATERIAL SELECTION
-
Design Approach
While designing the roll cage, we adopted a method. In the beginning phase, the basic design of the roll cage begins with the ergonomics, where a physical prototype of the 95th percentile male template is made. Then, with its help, we tried to determine the position of the main hoop plane. From there, the brake pedal plane is found out. Here pedal box clearances are given, so that bulkhead planes are obtained. Then, the front hoop plane is decided based on the accessibility of the driver. Then, the engine head plane is determined based on the engine spacing requirements and to accommodate the differential. Here, we changed the orientation of the 95th percentile template to recline position (based on which firewall design is made) so that driver does not strain his backbone; it also helps in decreasing the height of the main hoop, and even brake pedal plane can be moved closer so that driver can easily access pedal box, this process is iterative till the design gets suitable for both 95th percentile male and the driver. This also helps in knowing the height of roll hoops (i.e., front and main hoops), which allows following the 2in rule during the rollover condition of the car. Finally, in this phase, we get to know the distance between the planes.
In the next phase, suspension hardpoints are taken as input. These 16 hardpoints are obtained after performing the kinematic Analysis, where wheel parameters such as Camber,
Castor, Kingpin Inclinations are found, including the wheelbase, track width, and ground clearance. Then, a front hoop is drawn with the help of these points of a certain height that was already fixed before. As the remaining hoop distances are known from the earlier phase, all the hoops line diagrams are drawn; here, the cockpit cross-sectional template is used to provide sufficient room for the driver to access the gear lever and dashboard. At the same time, the internal cockpit template is used to provide legroom. Finally, we have drawn the line diagram of the whole roll cage as shown in fig 1. With the help of hardpoints, proper triangulation of members is done for the distribution of the loads correctly.
In the final phase, the tubes are assigned to the line diagram to satisfy the tube requirements per the FSAE rule book.
Figure 1: Hard-points and Cross-members line diagram
The initial sketch of the chassis is now completed so to check for compatible we checked using the PVC pipe mockup. The mockup arrangement is shown in Fig 2.
Figure 2: Mock-up Chassis
The final design along with suspension geometry, 95th percentile template projection, template fitting and drivers clearances are considered from the previous mockup and an optimum design is done. The final design is represented in Fig 3.
Figure 3:Chassis line diagram
-
Material Selection
The selection of proper material is the most crucial part while analyzing the various test conditions of the roll cage; it ultimately affects the vehicle's performance. Here, in the beginning, we gathered the steels of different carbon percentages, in the next step, we compared its Mechanical properties (such as Flexural modulus E.I., buckling strength, etc.) and Physical properties (such as Density, U.T.S., Poisson ratio, etc.) of material which ultimately helps in improving the stiffness and safety factor of chassis with less weight. In the final step after filtering the materials, we left with few materials which are available in the market so, in addition to all the above parameters which are needed to be considered, we have also compared the market cost, availability of each material and finalized the material as AISI 4130.
Material Strength
Young's Modulus (E)
210GPa
Yield Strength (Sy)
435 MPa
Ultimate Strength (Su)
670 MPa
Table 1: Material Strength of AISI 4130
Material Strength of Weld oint
Yield Strength (Sy)
180 MPa
Ultimate Strength (Su)
300 MPa
Table 2: Strength of Weld Joint
The figure below shows the color-coding of various pipe sizes as per the minimum requirement rules given from the Rule book (Supra International, FB_V1.1). Here the red color indicates the roll hoops that are of thickness 2.5mm, then comes the Blue indicates the roll hoop bracing, Bulkhead, where these are supporting members of Roll hoops which are of thickness 1.65mm followed by Green, indicates the supporting members for Roll hoop bracing which are known as main hoop bracing supports or front hoop bracing supports and then last one that we used is of 1mm thickness which is used as a nonessential member.
Figure 4:Chassis colour coding
The above mentioned are the sizes as per minimum requirement, which is assigned to our roll cage. However, we can use pipes of larger thicknesses. As per our design and analysis point of view, the dimensions we have given support the required application (i.e., Torsional Stiffness) during the race.
After selecting material, Analysis is to be performed to ensure its stability under various conditions; in addition, to ensure that the roll cage can fulfill the requirements for a high-performance race car, Analysis must be performed during the roll-cage design. Thus, it is essential to know about loads that act on the chassis, so that the static Analysis can be conducted the following load cases to be considered.
-
ANALYSIS RESULTS AND DISCUSSIONS
-
Front Impact Analysis
Most drivers usually experience 3G force while braking, 2Gforce accelerating, and 1.5G to 2G while cornering.
So based on the real-life condition's assumptions are made for analyzing every case.
Front-impact Analysis in front impact analysis, we consider that our vehicle is in static condition and rear side of the car is in fixed position considering the vehicle speed (vi) as 80kmph at time impact of 300msec and weight of the vehicle is 280kg. F*t=m(vi-vf), final velocity(vf) is 0 kmph, the resulting force is around20740N but in the real-time application during front impact, there is an energy-absorbing material (Impaxx700) which reduces the effect by four times, so extreme conditions at nodes of Bulkhead are taken as '4G'.
-
Fixtures: – Rear chassis points are fixed.
Loads: – Force applied on four members of Bulkhead.
Figure 5:Front Impact results
-
-
Side Impact Analysis
The common case of a side collision is when a vehicle is hit by another vehicle from the side in FSAE race considering the velocity of the car hitting the other car is 80kmph (vi) and
time of impact is 600msec as the collision is between two elastic bodies which increase the impact time.
Using F*t=m(vi-vf) the final velocity (vf) is 0 kmph the resulting force is around 10370 N. By, considering the energy absorbed be Impaxx 700 and energy lost due to the inelastic collision the extreme load on the chassis is 2G force
In the side-impact type of Analysis, we consider our vehicle is in static condition by fixing both the Front and rear suspension points of the car; this forms a fixed beam wherein the loads may act on
-
A single point
-
Uniformly distributed(continuous)
-
Fixtures: – Front and rear chassis points are fixed aside.
-
Loads: – Force is applied on the l members of the chassis' side impact members, including diagonal members.
Figure 6: Side Impact results
-
-
Torsional Analysis
This Analysis is mainly used to determine the torsional Stiffness of the chassis. If our vehicle's front wheel bumps and considering the critical condition of dynamic loading under the front member, this can be calculated by the formula below.
-
Fixtures: – Rear chassis points are fixed
-
Loads: – Torque applied on front chassis points.
Calculations for torsional Stiffness Roll Cage Weight = 27 kg Car Weight = 280 kg
Force (F) = 2746.8N
Torque = F × (1/2) Track width
= 2746.8N × (1/2) × 1.150 = 1579.41Nm
=
= tan-1(/ (1 /2) )
= tan-1(12.8689/ (1/2) *1150)
= 1.282
Torsional Stiffness(k)= Torque/Angle of deflection
Torsional Stiffness of chassis obtained is 1231.989 Nm/degree
Figure 7: Torsion Analysis results
-
-
Rollover Analysis
This Analysis concentrated on the vehicle when it got rolled over , when this happens the kinetic energy is converted to potential energy taking the impact time equals to 150msec. When this happens the load on the chassis is around 1.5G.
-
Fixtures: The base part of the chassis is fixed.
-
Loads: Force is applied on the top portion of the front hoop and main hoop.
Figure 8: Rollover Analysis
-
CONCLUSIONS
Triangulation of chassis at few points made better stress distribution and reducing the weight by removing additional members where stress concentration is low. By reducing the height of center of gravity increased down force on vehicle. Torsional stiffness is within safe limits and the FOS of different cases of testing is above 1. The cockpit area increased for better ergonomic conditions, and safety of rider has improved. The engine is changed considering the weight distribution to improve performance.
The roll cage also satisfies the basic need of a formula-type car, which is a lower weight to strength ratio. In accounting manufacturing, the design of the car is kept very simple. Thus, it can be concluded that this roll cage demonstrates good strengths in all tests and can be used to make a Formula Student Race Car.
-
ACKNOWLEDGMENT
-
-
The author would like to thank all the faculty of Department of Mechanical, Vasavi College of Engineering for their support and helping hands in equipment for this research.
REFERENCES
-
Formula SAE Rule book, SAE International, 2017-18
-
William F. Milliken and Douglas L. Milliken, Race Car Vehicle Dynamics SAE Inc, SAE Order No. R-146 United States of America, 1995
-
Gillespie, Thomas D. Fundamentals of vehicle dynamics. Vol.
114. SAE Technical Paper, 1992
-
Chepkasov S., Markin G. and AkulovaA.,Suspension Kinematics Study of the "Formula SAE" Sports Car, Procedia Engineering, Vol. 150, 2016, pp. 1280-1286.
-
Kumar MP, P. and Muralidharan, V., 2014. Design and Analysis of a Tubular Space Frame Chassis of a High Performance Race Car. International Journal of Research in Engineering and Technology, 3(02).
-
TriartiSaraswati., 2010. Ergonomic Factor Consideration in Designing Cars to Help Automotive Industries Face GlobaL Challenge: A Proposed Study. Proceeding, International Seminar on Industrial Engineering and Management ISSN : 1978-774X
-
Vijayan. S. N., Sendhilkumar, S. and Kiran Babu, K. M., 2015. Deisgn and Analysis of Automotive Chassis Considering Cross- Section and Material. International Journal of Current Research Vol. 7, Issue, 05, pp.15697-15701, May, 2015
-
Patil, K.Y. and Deore, E.R., 2015. Stress analysis of ladder chassis with various cross sections. IOSR Journal of Mechanical and Civil Engineering (IOSR-JMCE), 12(4), pp.111-116.
-
Aadithya, R. and *Muruganandam, D., 2016. Vehicle Chassis Analysis: Load Cases. International Journal of Recent Advances in Multidisciplinary Research Vol. 03, Issue 03, pp.1315-1317,
March, 2016
-
Patil, R. and Chikkali, V., FEA Analysis of FSAE Chassis. International Journal of Engineering Research & Technology (IJERT) Vol. 9 Issue 07, pp.290-295, July-2020
-
Jain, A., 2014. Computational Analysis and Optimization of Torsional Stiffness of a Formula-SAE Chasis (No. 2014-01- 0355). SAE Technical Paper.
-
Sethupathi, P.B., Chandradass, J., Sharma, A., Baliga, A.B. and Sharma, S., 2018, August. Design and optimization of FSAE chassis using FEA. In IOP Conference Series: Materials Science and Engineering (Vol. 402, No. 1, p. 012184). IOP Publishing.