
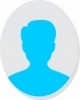
- Open Access
- Authors : Dr. Viswa Mohan Pedagopu , Tsegaye Alemayehu Atiso , Mebratu Markos Woldegiorgis
- Paper ID : IJERTV9IS110041
- Volume & Issue : Volume 09, Issue 11 (November 2020)
- Published (First Online): 12-11-2020
- ISSN (Online) : 2278-0181
- Publisher Name : IJERT
- License:
This work is licensed under a Creative Commons Attribution 4.0 International License
Design and Analysis of Container using S-2 Glass for an Automotive
Next >
Dr.Viswa Mohan Pedagopu #1, Tsegaye Alemayehu Atiso #2, Mebratu Markos Woldegiorgis #3
1 Professor (A), Department of Mechanical Engineering, Wolaita Sodo University, Ethiopia
2 Dean, College of Engineering, Wolaita Sodo University, Ethiopia
3 Head, Department of Mechanical Engineering, Wolaita Sodo University, Ethiopia
Abstract The S2 Glass material have been proved their existence in design of automotive structures with their ultimate strength, temperature and performance. It is necessary to identify the effect of buckle on various structures to withstand in the global competition. The reason behind the issue is most of the successful designs fail at the practical application. In this paper, a solid S2 glass structure container various layers has been designed and analyzed thermally its buckling effect with or without a hole using ANSYS and FET. A circular cylindrical shell elliptical headed container is considered due to its outstanding demand in the pressure vessel and automobile engineering. The attention-grabbing stage of buckling phenomena occurs before the deformed or non-deformed and a partial deformed sometimes contour of structure. Finally, concluded with pros and cons of using S2 Glass composites in high temperature environment likewise in automotive industries.
Keywords S-2 Glass buckling with and without hole/cut
– storage tanks — finite element technique and elliptical head structure
I. INTRODUCTION
A pressure vessel is a container designed to hold gas or liquid at high pressure at distinct ambient pressure. However, vessels must be designed with a formal code like ASME and BPVC etc., include Storage tanks, glassware, autoclaves, compressed gas cylinders and compressors in refrigerators. However, the most common type of pressure vessel is storage tanks to store liquids and gases for industrial and automotive purposes or processes. Heat exchangers and Process vessels are used to remove, combine, agitate, or break down products in a controlled environment in engineering industry. The pressure tank creates high water pressure using compressed air to open and close the valve by pushing or pulling. The Kevlar is a material that chemically, thermally stable with a high tensile and toughness. It can withstand at a high temperatures in polyamides. It is used as a friction, combustion protector material in the automotive industry and an aerospace industry respectively. Recent researches put forward the usage in advanced and modern technological application Nevertheless of its disadvantages of efficiency quickly absorbs moisture, it is used in both bulletproof and stab proof vests manufacturing. Now days, the material Kevlar weaving is most popular protective tool in defense industry. But Kevlar products are most costly to
produce due to difficult process of spin fibers and use of sulfuric acid.
II. LITERATURE REVIEW
A self designed steel structure is modeled using PRO/E and the analysis was done using ANSYS. The result has been concluded that the stress values are decreased for vessel with hole/cut than the vessel without hole/cut and the stresses and displacements are within the range of permissible values for Kevlar material. [7].In a thin laminated composite cylindrical shell a static and buckle analyses is done to determine the stress and deformation fields with an elliptical head without cutout and with cutout is presented. A self designed steel structure is modeled using PRO/E and the analysis is done by using ANSYS. The result has been concluded that the steel displacement without cut is much higher than with cut. The buckling factor is increasing with the increase in displacement [6]. A result is obtained by an analysis that maximum tangential stress resultant concentration near a circular cutout in a tension-loaded, circular, quasi- isotropic shell increases by approximately 18% as the shell radius-to-length ratio decreases. [1]. an efficient finite element model developed based higher order zigzag theory covering different features of laminated composites such as boundary conditions, ply orientations aspect ratio, thickness ratio and loading. A numerical result on buckling responses for different problems defined finite element model for laminated composite plates was capable to the exact solutions and recommended for research and industrial applications [2]. The critical buckling load factor of anti symmetric composite laminates presented on the effect of the skew angle, aspect ratio, length-to-thickness-ratio, fiber orientation angle, numbers of layers in the laminate and laminate sequence on the critical buckling load factor was found to increase with the skew angle depends on the laminate was large, the variation of critical buckling load factor with the number of layers was not appreciable [3]. The study for elastic buckling behavior of laminated composite plates with through-the-width de-laminations are focused on various parameters, such as size of de- lamination, support condition, aspect ratio, width-to- thickness ratio, stacking sequences, and location of de- lamination and multiple de-laminations It was noted that variations in length-to-thickness ratio affects the critical buckling load. The buckling load decreases as the a/t ratio increases. [4] [5].
III. STRAIN ANALYSIS OF PRESSURE VESSEL WITHOUT CUT
1. Import iges Model from Pro/Engineer
Figure 1. Import iges Model from Pro/Engineer
Pro/EngineerEnter units in command prompt: /units, si, mm, kg, sec, k
Preferences: structural PREPROCESSOR:
Main Menu> Preprocessor> Element Type> Add/Edit/ Delete
ADD Element Type: solid 20 nodes 95 Material Properties:
Material modals:
Structural Properties: (S2glass)
Density 0.00000246Kg/mm3 Youngs Modulus 86900Mpa Poissons ratio – 0.23
2. Meshed Model Generate Mesh
Main Menu> Preprocessor> Meshing> Mesh Tool>Smart size set to7
[Mesh] [Pick All] [Close] Warning. Meshed ModelFigure 2. Meshed Model
LOADS
>Apply>Structural>Displacement >On Areas>All Dof
>ok
>Apply>Structural>Pressure> On Areas 21
Figure 3. Loads sharing on the container all areas
Solution
Solution Solve Current LS ok Post Processor:
General Post Processor Plot Results Contour Plot – Nodal Solution DOF Solution Displacement Vector Sum
Figure 4. Displacement vector
The maximum displacement is 10.7992mm and the minimum is 1.19991mm.
General Post Processor Plot Results Contour Plot Nodal Solution Stress Von Mises Stress
Figure 5. Von Mises Stress
The maximum stress is in the range of 354.763N/mm2 to 44.3454N/mm2 which is at the head of the pressure vessel.
General Post Processor Plot Results Contour Plot Nodal Solution Stress total mechanical Von Mises Strain
Figure 6. Strain propagation
The maximum strain is 0.005041 and the minimum strain is 0.560e-3
TABLE 1 Displacement stress and strain
S2 Glass Material Properties Young modulus- 596GPa Poissons ratio – 0.23
Density- 1.85g/cc: Displacement vector sum
IV. STRAIN ANALYSIS OF PRESSURE VESSEL WITH CUT
1. Import Model
Figure 7. Imported model with cut
The maximum displacement is 2.67429mm and the minimum is 0.297143mm.
Stress
Figure 8. Stress Analysis with cut
The maximum stress is in the range of 140.294N/mm2 to 166.831N/mm2 which is near the hole.
STRAIN
Figure Figure 9. Strain Propaation with cut
The maximum strain is 0.00192 and the minimum strain is 0.213e-3
S2 GLASS
Youngs Modulus 86900Mpa Poissons ratio 0.23
Density 0.00000246Kg/mm3
TABLE 2. Displacement, Stress and Strain with cut
First Set
Figure 10. S2 Glass with cut For the first mode, the maximum displacement is 1.04198mm and buckling factor is 14174.5.
Second Set
Figure 11. For the second mode, the maximum displacement is 1.10344mm and buckling factor is 10776.6.
Third Set
Figure 12. For the third mode, for the third mode, the maximum displacement is a1.15223mm and buckling factor is 10771.2.
V. SHELL ELEMENT – 5 LAYERS
1. Import S2 Glass Material Preferences>select structural>ok
Preprocessor>element type>add/edit/delete>shell>linear layer99>ok
Real constants>add/edit/delete>enter no of layers 5>ok Material properties of S2 GLASS
Youngs Modulus 86900Mpa Poissons ratio 0.23
Density 0.00000246Kg/mm3
Sections>Shell>lay-up>add/edit>enter thickness>ok Plot section>range of layers 1-5>ok
Figure 13. 5 layered S2 Glass Material
TABLE 3. Sets and factors
Meshing>mesh tool>ok
Figure 14. Mesh model S2 Glass Material
Apply loads Pressure=0.0139MPa Solution>solve>current ls>ok
General post processor>plot results>counter plot>nodal solution>ok
Displacement>displacement vector sum>ok
DISPLACEMENT
Figure 15. The maximum displacement is 1.14763mm and minimum is 0.127514mm.
STRESS
Figure 16. The maximum stress is in the range of 9.73393N/mm2 to 10.9507N/mm2
STRAIN
Figure 17. The maximum strain is 0.985e-4 and minimum is 0.109e-4.
VI. SHELL ELEMENT – 11 LAYERS
S2 GLASS:
Next >