
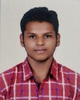
- Open Access
- Authors : Mathi Hrushikesh , Swarna Nadipudi
- Paper ID : IJERTV11IS110126
- Volume & Issue : Volume 11, Issue 11 (November 2022)
- Published (First Online): 01-12-2022
- ISSN (Online) : 2278-0181
- Publisher Name : IJERT
- License:
This work is licensed under a Creative Commons Attribution 4.0 International License
Design and Analysis of Human Powered Vehicle Chassis
Mathi Hrushikesp
Under Graduate Student Department of Mechanical Engineering
Vasavi College of Engineering, Hyderabad
Swarna Nadipudi2
Under Graduate Student Department of Mechanical Engineering
Vasavi College of Engineering, Hyderabad
Abstract The aim of the designed Human Powered Vehicle is not only to move at higher speeds compared to a normal upright bicycle but also to tackle the obstacles on the road along with sufficient strength to resist high deformation due to external impact during collision to ensure riders safety. A semi- recumbent bicycle is a type of bicycle in which the rider mounts in a reclined position. The semi-recumbent bicycles chassis is designed using Solidworks 2018 and is done after the brief anthropometric study of riders. The anthropometric study helped us in designing a chassis that fits riders of wide ergonomic range with the same safety standards all throughout the ergonomic range. MATLAB software used to determine the trial and offset values for the design minimizing the calculation work.
The model is then imported to Ansys Workbench in IGES format where static structural analysis is performed. AISI 4130 alloy is chosen for the chassis material. Tetrahedron mesh generated along with added boundary conditions is analyzed and values of von-mises stress, total deformations and factor of safety determined to prove the safety.
KeywordsSolidworks, Ansys Workbennch, von-mises stress, factor of safety
Fig. 1. Recumbent Bicycle
Semi recumbent cycle has the seat angle more than 45deg but less than 90 deg which provides a clear driver view and optimum fairing advantage this is more preferred for a comfortable rider position.
-
INTRODUCTION
During the recent times extraction of crude oil has enormously increased which is leading to increased carbon foot print and it contributes for 40 percent of green-house emissions considering the requirement of eco-friendly accustomed transportation to be implemented into regular commodity. As such the main goal includes the design of a Human Powered vehicle abiding to the rule guide of ASME and safety being the top priority with sustainable design that can be implemented in a cost-effective way. To increase the sustainability of the human powered vehicle and to accommodate rider comfort we chose to design a semi recumbent bike. Out of the designs such as Upright, Recumbent and semi recumbent, semi recumbent is known to have better aerodynamic configuration and balanced drive position with clear driving view.
Recumbent cycle is considered when the angle of seat is less than 45 deg and it provides more fairing advantage which helps in reducing the amount of drag.
Fig. 2. Semi Recumbent Bicycle
Upright cycle has a seat angle of 90deg and is the most generalised position to ride which provides clear view but its inefficient for drag.
Fig. 3. Upright Recumbent Bicycle
-
LITERATURE REVIEW
Thomas J. Ayres et al. [2] has studied various cases of crash for recumbent bicycles and tricycles, where he categorized the contributory factors for crash and has concluded tricycles to be at lower risk of crash compared to recumbent bicycles.
Fabio Malizia et al. [3] in his paper has focused on increasing the comprehension of cycling aerodynamics and on improving the aerodynamics of bicycle equipment. The connection between the different subfields of cycling aerodynamics and linking new research with past discoveries is crucial to efficiently drive future studies have been stated.
David Gordon et al. [4] has focused mainly on the evolution of the designs in the human powered vehicles and the improvement which made the drive more comfortable ergonomically and also experience less drag force with better aerodynamic bodies using different materials.
Warren Beauchamp et al. [5] has given a information about the components used to build a human powered vehicle and the different variants available. The reason for the wider use of certain materials along with limitations of some have been stated. It gives an overall view of the design parameters to be considered.
Bambang Suhadri et al. [10] has focused on the concept of rear wheel drive in bicycles which can be used for day-to-day purpose in city conditions. The research aims in development of a recumbent bicycle with the help of biomechanics simulation and finite element analysis on the design under different terrain conditions.
-
DESIGN PARAMETERS AND CALCULATIONS
Wheel Sizes
Wheel with diameter of 20 inch at front and 26 inches at rear have been chosen for the semi recumbent design.
Turning radius (R) = 2000mm, as per the guide lines of ASME the turning radius for HPV should be less than 8 meters.
Turning angle (A) = 40 degrees
Wheelbase (L)
It is the distance between the centers of front and rear wheels.
L=R*Sin(A) (1)
L= 1250mm
Headtube Angle (h)
It determines the inclination of the steering rod. The range of headtube angle lies in range between 70 to 75 degrees for semi recumbent bicycle. An optimum value of 72 degrees is chosen for the design.
Trail and Offset
These are important for stable steering of the bicycle and reduce impact of bumps on the fork rods.
Offset of 30mm is considered in optimum range. O= 30mm
Trial=[r*cos(h)-O] (2)
Sin(h)
r: radius of front wheel in mm h: Head Tube angle
O: Offset
[25.4*cos (72)-30]Sin (72)
Trial= 50.98mm
Roll Over Protection System
Considering the adverse effects with attaining maximum speed rider needs to embed into safety cover which the roll over protection (RPS) guides it an enclosed cage structure has been designed to provide maximum safety.
Bump impact on front fork: Rider weight assumed = 84Kgs
Weight of vehicle along with accessories = 18Kgs Force = (84+18) *9.81 = 1000.62 N
For additional allowance in case of a heavier rider a force of 1200 N is considered to be set for the analysis.
Torque on Bottom Bracket:
Torque = Force*distance from the center of rotation
T =F*r
(3)
Considering a force of 50Kg acting on pedals of length 120mm
T= 50*9.81*120 = 58860N-mm
-
CAD MODEL
Design has been considered in accordance with the rider ergonomics which can provide maximum efficiency in terms of speed drag and has maximum safety. Considering which we have designed a semi recumbent cycle by taking the seat
ergonomics.
Trial & Offset
T= 50.98mm, O=
30mm
Increase in trail and decreases in offset increases steering stability.
Head Tube angle
A= 72o
72 angle Head tube makes the steering handling easy which is passed through fork.
Bottom Bracket
Diameter= 41.96mm
The conventional Bottom Bracket
Dimensions have been considered.
angle as 55 to provide comfort for the rider and also makes it easy for the application of torque on the drive train, which provides optimum fairing advantage. The dimensions are considered by taking average length of rider for torso and the leg length for drive train.
Solidworks 2018 has been used for the designing the 3-D model. Weldment of diameter 1.125 inch with thickness of 3mm has been applied as it is available in market on commercial scale.
Fig. 4. Frame Dimensions
DIMENSIONS
VALUES
JUSTIFICATIONS
Length
973.88mm
With respect to the average torso length of the rider length is classified.
Width
628.41mm
In accordance to the average width of rider also
considering the previous year width has been increased.
Fillet radius
100mm
In order to neglect sharp edges fillet radius of 100mm has been given at the Roll bar
connections.
Wheel Base
1250mm
To achieve the turning radius and to get it stable for the different rider
Fig. 5. Front view of frame TABLE I. Chassis Dimensions
Fig. 6. Front fork
Fig. 7. Rear fork
Fig. 8. Chassis Isometric view
-
MATERIAL SELECTION
TABLE II. Material Properties
CATEGORY
AISI 1080
AISI 4130
AISI 9130
Ultimate tensile strength
615 MPa
560 MPa
802.5 MPa
Yield strength
375.8 MPa
460
MPa
439.9
MPa
Elongation
24%
28%
17.3%
Reduction in area
45.0
55.6
42.1
Hardness
174
156
241
Impact strength
61J
87 J
78.6 J
Density
7.85g/cub
7.7g/cub
7.85g/cub.c
.cm
.cm
m
Modulus of elasticity
190-210Gpa
190-210Gpa
190-210Gpa
To manufacture a chassis with high strength towards external forces, AISI 4130 Alloy Steel is the material chosen for the semi recumbent cycle since it provided the proper basis for the construction and serves the purpose of high strength, less area reduction and weldability.
-
FINITE ELEMENT ANALYSIS
The analysis is performed using ANSYS Workbench software, where the CAD model is converted to IGES format and given as the model input.
Static analysis is performed on the chassis design and maximum and minimum values of deformation, stress and Factor of Safety are tabulated to demonstrate its safety.
-
Mesh Generation:
Meshing is the process of creating small discrete elements of the component for solving using mathematical equation to obtain the required output.
A mesh size of 5mm is used for meshing the chassis and a tetrahedron mesh is generated for this task. The number of nodes are 678492 and 350282 elements have been generated after meshing.
Fig. 9. Meshed chassis
-
Top Load Analysis
-
Boundary Conditions
A point load of 2670 is acted at an angle of 12 on the top of the roll bar as pet the guidelines set by ASME for their HPV competitions considering the rider safety. This is done considering that point to get the first impact during toppling condition.
Roll bar attachment points and the clamps of Fork and Rear fork have been considered to be fixed and the RPS at the top is considered to be a simply supported beam suspended with 3 supports and a vertical load of 2670N acting on 12 degrees with respect to Y axis.
Fig. 10. Top load Boundary Conditions
-
Top Load Analysis Outcomes Total Deformation:
Fig. 11. Deformation due to Top load
A maximum deformation of 2.634 mm is obtained at the top after the analysis run.
Equivalent Stress:
Fig. 12. Equivalent Stress due to Top Load
Equivalent stress of 192.05 MPa is experienced by chassis in top load condition.
FOS:
Fig. 12. FOS in Top load condition
Minimum FOS obtained is 1.3018 from which the design can be proved safe.
-
-
Side Load Analysis
-
Boundary Conditions
A Load of 1330N has been applied towards the negative Z axis direction adhering to the ASME guidelines for HPV.
During Side loading key assumptions made were to fix the Clamps of Front Fork and Rear Fork additional to it roll bar attachment points have been fixed and also the roll bar attachment points at the shoulder length have been curved to avoid sharp edges and to reduce the damping impact during roll over.
Fig. 14. Side load Boundary Conditions
-
Side Load Analysis Outcomes Total Deformation:
Fig. 17. FOS in Side load condition
Minimum FOS of 2.5096 is obtained for design, hence making it safe.
-
-
Structural Analysis
-
Boundary Conditions
Considering front wheel drive and a weight of 50 kg acting on the pedals when the torque is been applied. Since in the Front wheel drive major concentration of weight acts on the front wheel so considering 60% weight on the crank and on pedals of 120 mm and assuming the clamps of fork and rear fork to be fixed.
Torque of 58860 N-mm is given.
Fig. 15. Deformation due to Side load
Maximum deformation of 1.2425 mm is obtained after the anslysis.
Equivalent Stress:
Fig. 16. Equivalent Stress due to Side Load
Maximum stress of 99.618 MPa is experienced by the chassis.
FOS:
Fig. 18. Boundary conditions for Structural analysis
-
Structural Analysis Outcomes Total Deformation:
Fig. 19. Deformation due to torque
Maximum deformation of 2.2739 mm has been observed at the bottom bracket mounting.
Equivalent Stress:
Fig. 20. Equivalent stress due to torque
Maximum stress of 50.322 MPa is generated due to the torque acting during pedaling.
FOS:
Fig. 21. FOS
Minimum FOS of 4.968 is obtained making the design par the safety limit.
-
-
Front Fork Analysis
-
Boundary Conditions
Head tube attachment is considered to be fixed and also the momentum has been applied to it considering its rotation inside the head tube. Moment of 50000 N-mm has been applied to the fork head. A force of 1200N is applied over the clamps of the fork at the bottom.
Sr.no
Type of Analysis
Deformation (mm)
Stress (MPa)
FOS
1
RPS Side Load
1.2425
99.618
2.509
2
RPS Top Load
2.634
192.05
1.3018
3
Structural
2.2739
50.322
4.968
4
Fork
0.52903
172.83
2.6615
Fig. 22. Boundary Conditions on Front Fork
-
Static Analysis Outcomes Total Deformation:
-
Fig. 23. Deformation of front fork
Maximum deformation of 0.52903 mm is obtained upon the impact of bump on the front fork.
Equivalent Stress:
Fig. 24. Equivalent stress in front fork
Maximum stress generated is172.83 MPa on the front fork.
FOS:
Fig. 25. FOS for front fork
The minimum FOS 2.6615 which is greater than 1, hence the fork withstands against the bumps on path.
-
-
RESULTS
TABLE III. Results
-
CONCLUSIONS
Conclusions are raised in comparison with the required range and achieved values so as to compare the safety and ergonomics criteria with respect to the ASME standards
TABLE IV. Conclusions
FACTORS
REQUIRED
ACHIEVED
RPS Side oad Analysis
Deformation <3.8mm
Achieved =1.2425mm
RPS Top Load Analysis
Deformation<5.1cm
Achieved =2.634mm
Structural Analysis
FOS>1
Achieved=4.968
Fork Analysis
FOS>1
Achieved=2.6615
Reasons for achieving safety values in all four above mentioned categories is due to the material strength possessed by AISI 4130 with strength of 560Mpa which enables a tough impact strength to the chassis and the low deformation rates prove the design is safe, as the ergonomic structure it maintains with no sharp edges and maintaining fillets at every end cross section has reduced the damping impact and such has increased its probability to endure deformation.
-
REFERENCES