
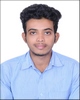
- Open Access
- Authors : Suyash Yashwant Wagh , Eshita Amal Nandi
- Paper ID : IJERTV9IS090137
- Volume & Issue : Volume 09, Issue 09 (September 2020)
- Published (First Online): 14-09-2020
- ISSN (Online) : 2278-0181
- Publisher Name : IJERT
- License:
This work is licensed under a Creative Commons Attribution 4.0 International License
Design and Analytical Calculations of Double Wishbone for Formula Student Race Car
Suyash Yashwant Wagh
-
Mechanical Engineer
JSPMs Rajarshi Shahu College of Engineering Pune, India
Eshita Amal Nandi
Pursuing B.E. in Mechanical Engineering JSPMs Rajarshi Shahu College of Engineering
Pune, India
Abstract The functional objective of the suspension system is to provide relative motion between the sprung and the unsprung mass. This is achieved by a spring to absorb the shocks and some kinematic linkages holding them together with particular degrees of freedom. Further for better handling the kinematics of the system is designed and optimized. This research focuses on the simulation, design, and analytical calculations of the kinematical linkage called A-arm. The double-wishbone suspension geometry was analyzed in Lotus Shark software to procure the most appropriate location of the hardpoints. A-arm was modeled in CATIA V5, Autodesk Fusion 360, and analyzed in ANSYS 16.0. Software results are correlated with the analytical calculations to obtain a feasible solution.
KeywordsDouble wishbone, A-arm, thickness calculation, rod end selection, vehicle dynamics, threaded joints, etc.
-
INTRODUCTION
The FS car's suspension controls the angle, position, and velocity of each wheel to maintain a high value of mechanical grip while transmitting the forces generated by tires to the chassis. A reliable method to determine the forces produced by the road loads in suspension members opted. In this paper, a detailed analytical calculation was explained for deciding the A-arm diameter using a set of calculations. The component is designed to be cost- effective, durable, and lightweight. As the double-wishbone undergoes tension and compression forces, the yield and buckling need to be calculated, followed by the threaded joints calculation for the rod ends as the force being transmitted through these to the chassis.
Fig1. Double wishbone
-
PROBLEM STATEMENT
The double-wishbone suspension system is independent. This design allows the race car engineers to control the wheel's motion throughout suspension travel, controlling the parameters such as camber angle, caster angle, toe, roll center height, and scrub radius.
They are a force transmitting and kinematic part, so dynamic stability is the most crucial factor. Designing by using lightweight material along with it being cost-efficient is the recent discovery many teams are trying to develop. In the era of upgrading trends, many teams are trying to evolve in a world full of research related to advanced materials.
In this fast-changing and technologically developed world, there is much-advanced software in use, but all that software is programmed on the necessary calculations. To correlate those results with calculations and further substantiate those software results, we need analytical calculation. Because sometimes that software is constrained to some limits. The paper explains the method to find the thickness of the a-arm by pen and paper calculation. These calculations require critical skill, and also, they are an essential set for sound stress engineers in the automobile industry.
Some teams want better design irrespective of cost, and some want a mediocre design with the economical product. But many teams are trying to get the intermediate between them, so to improve this, we need our work to be well developed from all angles and aspects. Hence analytical form is considered to be more cogent.
Fig2. Suspension Assembly
-
OBJECTIVES
-
A lot of forces during cornering, acceleration, and bump are applied directly during dynamic conditions, so it is essential to produce a compact, lightweight, and reliable suspension system to increase vehicle performance.
-
To reduce the unsprung mass.
-
Combining analytical calculations result with FEA as it provides a good starting point for the design.
-
To understand how much an advantage FEA gives during the design process, it's first necessary to understand how analysis and design optimization are performed without FEA.
-
To determine loads, restraints, and material properties, pen and paper calculations played a vital role.
-
The FEA result's verification and validation with an independent set of calculations are crucial to provide confidence in the analysis results.
-
-
ABBREVIATIONS Abbreviations Explanation
Ax Acceleration along X-axis
Ay Acceleration along Y-axis
Wf Weight on front
Wr Weight on rear
HCG CG height to the ground
WLongitudinal Longitudinal load transfer on a wheel WLateral Lateral load transfer on a wheel
FOS Factor Of Safety
Pact Actual Load
Pcr Critical Load
E Modulus of elasticity
dc Core Diameter
d Nominal Diameter
di Inner diameter
do Outer diameter
Maximum tensile stress
KL Equivalent length of column end condition
-
METHODOLOGY
Fig3. Design Flowchart
-
DESIGN PHILOSOPHY
-
Choosing suspension geometries and components involves a wide range of choices and compromises. An analysis of the tire, suspension component, chassis, and road interaction is required to decide the trade-offs that will result in an optimum configuration for the type of vehicle.
The necessary steps in designing a vehicle's suspension are:
-
Selection of the suspension type to be employed;
-
Selection of the wheels;
-
Establish the vehicle's dimensions: wheelbase and track width(s);
-
Model the suspension geometry;
-
Designing components.
TABLE I. KINEMATIC SIMULATIONS
Parameter |
Front |
Rear |
Scrub Radius |
56 mm |
70 mm |
Caster Trail |
12.64 mm |
0 mm |
Roll Rate |
132 Nm/deg |
124 Nm/deg |
Bump Coefficient |
0.083 deg/mm |
0.093 deg/mm |
Roll Gradient |
0.43 deg/g |
0.43 deg/g |
Wheel Rate |
15.22 N/mm |
11.73 N/mm |
Jounce |
30 mm |
30 mm |
Rebound |
30 mm |
30 mm |
TABLE II. VEHICLE PARAMETERS
Parameter |
Value (in mm) |
Wheelbase |
1545 |
Track (front) |
1000 |
Track (rear) |
1100 |
Static camber |
-2º |
Castor |
4º |
Static toe |
2º (in) |
Kingpin angle (front) |
4º |
Kingpin angle (rear) |
0º |
Roll center height (front) |
7.42 |
Roll center height (rear) |
32.55 |
Static weight distribution |
45:55 |
Fig4. Lotus simulation in roll condition
Fig5. Lotus simulation in steer condition
-
Load Transfer
The inertia of a mass is its resistance to change its state. For the change of state of a body, it must exprience acceleration in its motion direction. Acceleration, braking, or cornering is nothing but the change of state of the vehicle, which offers resistance for a while and results in load transfer in a direction opposite to the force causing the change. No doubt, this load transfer persists for a short duration of time, but its impact on the car's performance is much more crucial.
Fig6. Traction Circle
The max longitudinal acceleration Ax = 1.2g The max lateral acceleration Ay = 1.4g
However, the maximum acceleration experienced by the vehicle is during cornering accompanied by braking and given by:
1.22+1.42 = 1.84g (1)
Thus, maximum acceleration = 1.84g
Now, the weight of the car is 250 kgs. Wf: Wr = 45: 55
Wf = 112.5 kg = 1103.62 N
Wr = 137.5 kg = 1348.87 N.
Weight on single wheels in steady-state is: Wf (single) = 56.25 kg = 551.81 N
Wr (single) = 68.75 kg = 674.43 N
The total longitudinal load transfer can be calculated as Wlongitudinal = (WHCGAx)/wheelbase
Wlongitudinal = (250*135*1.2)/1545 (2)
= . = .5 (3)
The total lateral load transfer can be calculated as Wlateral = (W*HCG*Ay)/trackwidth
Wlateral = (250*135*1.4)/1000 (4)
lateral = 7.25 = 63.52 (5)
However, the max load transfer can occur during cornering and braking. This will be the diagonal load transfer on the front outer wheel.
Wdiagonal = (Wlongitudinal2+Wlateral2)
Wdiagonal = (26.212+47.252) (6)
= 4.03 = 30.06 (7)
Thus, the maximum load on a single wheel is: Wmax = Wf (single) + Wdiagonal
= 10.28 = 1081.84 (8)
Sprung mass = 250 kg (approx.)
The factor for static to dynamic conditions: 2.1 According to the mass distribution of 55:45 (Rear: Front)
Mass per wheel (Front) = 56.25 kg
Angle of inclination of the strut = 54(from horizontal)
Point of attachment of strut = 210 mm from chassis end (from suspension geometry)
Reaction force acting from the ground on the wheel= (56.25kg * 9.81) N =551.8125 (9)
Considering the A-arm hinges (A) as the point about which moment is taken;
The horizontal distance of reaction force from hinge point = 315 mm from suspension geometry
The horizontal distance of strut attachment point from hinge point = 210 mm
By taking moment about hinge points:
551.81 * 315 = Spring Force * sin 54 * 210 (10) Spring Force = 1023.11 N
Considering the dynamic factor,
Dynamic force acting on the spring = 2046.22N (11)
Hence,
Spring Stiffness = Dynamic Spring Force / Deflection
= 2046.22/ 55.8
= 36.67 N/mm 37 N/mm (12)
By using a similar procedure,
For Rear
Spring Force =1384.98N (13)
Dynamic Force acting on spring =2285.22
Spring Stiffness = 40.8 N/mm (14)
-
SPRING RATES
Front spring
Fig8. Double wishbone suspension system on car
Fig7. Free Body Diagram
-
DESIGN OF A-ARM
As calculated above, the maximum forces on the wheels are:
-
For Front
Fz =110.28*9.81=1081.84 N (15)
Fx = 1.2*9.81*(56.25+13.10) =816.388 N (16)
Force on single A arm =816.388/2 = 408.19 N
Fy=1.4*9.81*(56.25+23.62) =1096.93 N (17)
Force on single A arm = 1096.93/2 = 548.46 N
Calculated -Spring Force =1023.11 N.
The analytical calculation for:
Threaded Joints
Pact = [(F 2+F 2+Fz2)2+ (spring force)2]
Considering this as the inner diameter, the outer diameter was calculated by the following procedure:
Analytical Calculation for diameter calculation:
For Front
FOS = Pcr/Pact (22)
Pcr = ( 2EI) / (KL)2 (K=2 Because the condition
is one end fixed, other free) (23)
(FOS*(KL) 2*Pact)/2E = (/64) *(do4di4) (24) E = 205*103 MPa
x y
Pact = 1279.762+1023.112 = 1638.45 N (18)
Syt=215 MPa FOS=2
For permissible tensile stress
=Syt/FOS =215/2 =107.5 N/2 (19)
=Pact/ [(/4)*dc2] (20)
Now, dc =[(Pact*4)/* ]= 4.40 mm (21)
d=4.40/0.8 = 5.5 mm [(h=0.8d) the factor determining threads will not fail in shear.]
d=5.5 6mm
Fig9. Basic dimensions of screw threads (fine series)
-
Fine threads are used where the parts are subjected to dynamic load and vibration.
-
Hollow thin-walled parts where coarse threads are liable to weaken the wall considerably
-
These are used in parts which are used for the purpose of adjustment.
-
Hence from the standard reference table of fine series, we have chosen M6 x 1
Accordingly, the POS 6 rod end was selected.
Fig10. Mechanical properties of AISI 1018 steel
(2*(2*210)2*1638.45*64)/(2*205*103*) = do4di4 (25)
Considering di=6mm do = 9.18 10 mm
Fig11.1. Preferred series
Fig11.2. Preferred series
By using the preferred series R5 which is 1,1.6,2.5,4,6.30,8,10, the diameter 10 was selected.
Hence, do=9.18 10mm
Accordingly, an A-arm endplate was designed. To accommodate the spherical bearing, a bush (with accurate tolerance) was inserted in the laser cut part. This ensured proper fitment of the spherical bearing.
Slots on the laser cut part ensured accurate positioning of the damper mounts.
Fig12. Suspension Assembly
Fig13. Max Von-Misses stress = 217.57 MPa
Fig14. Max deformation = 0.102mm
X. CONCLUSION
The purpose of this paper was to find the diameter of the double-wishbone by analytical calculations. The force is calculated using basic concepts. This paper gives a clear idea of how the forces are taken into consideration. Material is selected based upon calculated forces. Double-wishbone is designed using suspension points and dynamic force applied considering the factor of safety. Design is validated by using Ansys 16.0 software. This design is fabricated and tested in the Formula Student race car in all dynamic conditions. No failure occurred at the time of testing, it can be concluded that forces calculations and design are up to the mark.
XI ACKNOWLEDGMENT
We would also like to thank Team Redline Racing for successfully designing and manufacturing the Formula Student race car.
XII REFERENCES
-
William F.Miliken, Doughlas L.Miliken.1995.Race Car Vehicle Dynamics Volume 146 of R.: Society of Automotive Engineers, SAE International
-
Thomas D. Gillespie, Fundamentals of Vehicle Dynamics (Society of Automotive Engineers)
-
Bhandari V.B. Design of Machine Elements 2014, McGraw Hill Education(India)
-
Supra SAEINDIA 2019 rulebook.
-
Shaikh Vasim.A Mist and Microstructure characterization in end milling AISI1018 August 2013, [Online] Available: https://www.researchgate.net/publication/307988801
-
Bansal.R.K A Textbook of Strength of Materials 2010, Laxmi Publications
AUTHORS
Suyash Yashwant Wagh completed Bachelor of Engineering in Mechanical Engineering from the JSPMs Rajarshi Shahu College of Engineering affiliated to Pune University, India. His research interests in the field of vehicle dynamics and completed certification training in MSC Adams simulation software.
Eshita Amal Nandi is currently in the final year of Bachelors of Engineering in Mechanical Engineering from the JSPMs Rajarshi Shahu College of Engineering affiliated to Pune University, India. Her research interests include in the field of analytical research, vehicle dynamics and simulation software.
.