
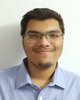
- Open Access
- Authors : Aniruddha Atre , Dhiren Bhabad , Aditya Bhorde , Vedant Aher, M. R. Khodke
- Paper ID : IJERTV10IS050310
- Volume & Issue : Volume 10, Issue 05 (May 2021)
- Published (First Online): 28-05-2021
- ISSN (Online) : 2278-0181
- Publisher Name : IJERT
- License:
This work is licensed under a Creative Commons Attribution 4.0 International License
Design and Buckling Analysis of Connecting Rod
Aniruddha Atre1
Dept. of Mechanical Engineering BRACTs Vishwakarma Institute of Technology
Pune, Maharashtra
Aditya Bhorde2
Dept. of Mechanical Engineering BRACTs Vishwakarma Institute of Technology
Pune, Maharashtra
Prof. M. R. Khodke3
Dept. of Mechanical Engineering BRACTs Vishwakarma Institute of Technology
Pune, Maharashtra
Vedant Aher2
Dhiren Bhabad1
Dept. of Mechanical Engineering BRACTs Vishwakarma Institute of Technology
Pune, Maharashtra
Dept. of Mechanical Engineering BRACTs Vishwakarma Institute of Technology
Pune, Maharashtra
AbstractConnecting rod plays a crucial role in the working of an IC Engine, whose key role is to transmit power from the piston pin to the crankpin. It basically acts as a rigid link and transmits the reciprocating motion of the piston to the rotational motion of the crankshaft. It is a slender part with its length considerably greater than its width. It is mainly subjected to axial compressive stress. In this paper, we have considered a 4-stroke single cylinder IC Engine of 66 mm bore diameter and 99 mm stroke length, and calculated the required dimensions. We have modelled the Connecting rod using SOLIDWORKS software, and carried out Static and Buckling Analysis in ANSYS software.
Keywords Connecting Rod, IC Engine, Finite Element Analysis, Static Structural, Buckling Analysis, ANSYS.
-
INTRODUCTION
Connecting Rod is vital component for the basic working of IC Engines. It connects the piston and the crankshaft together and helps to convert the reciprocating motion of the piston into rotational motion of the crankshaft. It also transfers oil from crankpin to piston pin for lubrication. Its key is that it should have the capability to withstand the compressive stresses from the maximum gas pressure on the piston crown and the inertia force of the reciprocating parts as well as buckling and fatigue stresses. [3, 4, 5]
The connecting rod is generally made from materials like medium carbon steels or alloy steels. The carbon content varies from 0.35 to 0.45 percent in medium carbon steels.
Typically, nickel chromium or chromium molybdenum steels are used as alloy steels. The connecting rod is usually manufactured by the drop forging process, casting process and powdered metallurgy. [1]
The performance and lifespan of connecting rod is affected by numerous factors and design parameters. These factors include the type of engine to be used, maximum speed and torque that the engine can generate, shank cross-section like I-section and H-section. Design parameters include thickness of shank, radius of fillet, criteria for material selection, manufacturing processes used etc. By improving these aspects, we can increase the performance of connecting rods. [6, 7]
Connecting rods are widely employed in range of engines such as Single Cylinder engines, Multi Cylinder- In-line engines, V- engine, Radial engine, Opposed-Cylinder engine and Opposed-Piston engines. A connecting rod has three parts – a small end, a shank section, and a big end. They can be produced as single piece or two-piece components. To ensure that the bearings would fit properly, the piston pin end and crankpin end pinholes are machined as parallel holes. The piston and the connecting rod are coupled at the small end by the piston pin. The small end of the connecting rod will have a solid bushing of Phosphor Bronze or an analogous material. As the big end revolves with the crankshaft, the small end is forced to swivel on the piston pin. The bushing is necessary due to the high pressure and temperatures, in spite of only a slight movement relative to the piston pin. A two-piece conn. rod is made up of two parts to enable it to be clamped around the crankpin. The bottom part, or rod cap, is made of identical material as the rod and is fastened to the conn. rod by two bolts. The surface that is in contact with the crankpin is generally a split shell bearing. The two parts of the bearing are positioned in between the small end and crankpin by dowel pins. From the perspective of functionality, connecting rods must have the required rigidity at the lowest possible weight. [8]
-
ANALYTICAL DESIGN
For the CAD model, the calculations have been done as per the procedure mentioned in [1, 2].
Sr. No.
Parameter
Value
1.
Angle of inclination of connecting rod with line of stroke. (°)
3.3
2.
Yield Stress of Connecting Rod (c in MPa)
330
3.
Constant a for steel
7500
4.
Factor of Safety (F.S.)
3
5.
Bore Diameter (D in mm)
66
6.
Stroke Length (l in mm)
99
7.
Maximum Pressure (Pmax in MPa)
5
8.
Thickness of the bush (tb in mm)
2
9.
Marginal Thickness (tm in mm)
5
10.
Allowable bearing pressure for small end (Pb1 in MPa)
12.5
11.
Allowable bearing pressure for small end (Pb2 in MPa)
6
12.
Let the thickness of the connecting rod be t
10.
Allowable bearing pressure for small end (Pb1 in MPa)
12.5
11.
Allowable bearing pressure for small end (Pb2 in MPa)
6
12.
Let the thickness of the connecting rod be t
=> 20 mm
Table 1. Data & Assumptions
-
Inner Diameter of Small End =
=
=
1 1.5
=> 31 mm
-
Outer Diameter of Small End =
= + 2 + 2
=> 45 mm
-
Inner Diameter of Big End =
-
Outer Diameter of Big End =
= + 2 + 2
=> 61 mm
=
=
2 1
=> 47 mm
Figure 1. Schematic of forces acting on Connecting Rod. [1]
i. cos() = 0.98748
2
2
-
Force acting on connecting rod =
= ( )
4
cos ()
=> 17113 N
-
Critical Buckling Load = = . .
=> 51338.6 N
iv. Total Length = = 1.5
=> 148.5 mm
-
Applying Rankines Formula to find thickness t
Figure 2. Typical cross-sectional view of Connecting Rod. [1]
-
-
-
CAD MODELLING
=
=
1 2
330 112
1 148.5 2
The Connecting Rod was designed in the CAD software SOLIDWORKS, using the dimensions calculated above. All the units are in mm. The main design parameters are as
1 + ( )
t = 3.875 mm 4 mm
1 + 7500 (1.78)
given in Table 2.
Sr. No.
Parameter
Value
1.
Length
148.5 mm
2.
ID of Small End
30 mm
3.
OD of Small End
44 mm
4.
ID of Big End
40 mm
5.
OD of Big End
54 mm
6.
Height at Middle Section
20 mm
7.
Height at Small End
16.5 mm
8.
Height at Big End
23.5 mm
9.
Width for cross-section
16 mm
10.
Height for cross-section
20 mm
Sr. No.
Parameter
Value
1.
Length
148.5 mm
2.
ID of Small End
30 mm
3.
OD of Small End
44 mm
4.
ID of Big End
40 mm
5.
OD of Big End
54 mm
6.
Height at Middle Section
20 mm
7.
Height at Small End
16.5 mm
8.
Height at Big End
23.5 mm
9.
Width for cross-section
16 mm
10.
Height for cross-section
20 mm
-
Height at Middle Section = = 5
=> 20 mm
-
Height at Small end =
= 0.75+0.9
2
=> 16 mm
-
Height at Big end = 1
= 1.1 +1.25
2
=> 23 mm
Table 2. Design Parameters for Connecting Rod
-
Width for cross-section = B = 4t
=> 16 mm
-
Height for cross-section = H = 5t
Figure 3. Top View of Conn. rod
Figure 4. Side View of Conn rod
Figure 5. Isometric View of Conn. Rod
-
-
FINITE ELEMENT ANALYSIS OF CONNECTING ROD
Using Ansys Geometry Design Modeler, the small end was sliced into two equal parts. This was done so that the force would be applied only to the lower half of the small end, similar to actual conditions. It can be seen in Fig 6. below.
Figure 6. Conn. Rod Model
-
MESHING
Tetrahedron geometry was used for the meshing. The element type was Tet10 10 noded Tetrahedron. Mesh refinement was carried out at the locations as per the Structural Error Plot was showing significant error.
Figure 7. Meshing
-
BOUNDARY CONDITIONS
end is free translation along Z axis and free rotation about Y
axis. Therefore, the connecting rod behaves as if the small end and the big end are hinged at the piston pin and crankpin respectively.
Figure 8. Boundary Condition 1
Figure 9. Boundary Condition 2
Dynamic behavior is observed for both, the small end and big end of the connecting rod. The small end moves along with the piston pin, whereas the big end moves with the crankpin. Hence, Remote Displacement has been applied to both the ends. Condition given to the big end is free rotation about Y- axis as it rotates with the crankpin. Condition given to small
-
STATIC STRUCTURAL
Figure 10.a. Equivalent Stress Contours
Figure 10.b. Plot for Equivalent Stress
Figure 11.a. Plot for Total Deformation
Figure 11.b. Total Deformation Contours
Figure 12. a. Normal Stress Contours
Figure 12. b. Plot for Normal Stress
-
BUCKLING ANALYSIS
The eigen value buckling analysis system in ANSYS was used for the estimation of buckling modes (See Fig. 13.a., 13.b., 14.a., 14.b.). It is a linear buckling analysis method. The buckling load has been evaluated by taking the product of applied load and load multiplier. The buckling analysis was done for two modes. The results generated by ANSYS for both the modes resembled the real-world scenario of failure of connecting rod, i.e., the first and second mode of buckling are exactly alike to the buckling failure of connecting rod. (See Fig. 13. a., 14. a.) [8]
Figure 13. a. Total Deformation Contours
Figure 13. b. Plot for Total Deformation
Figure 14. a. Plot for Total Deformation
Figure 14. b. Total Deformation Contours
-
-
RESULTS
multiplier we can conclude that the Connecting rod can withstand upto three times the current load without buckling.
Sr. No.
Parameter
Results
Theoretical
Analytical (max)
1.
Normal Stress (b in MPa)
110
157
2.
Critical Buckling Load (PCR in N)
51338.6
51646.73
3.
Total Deformation for Static Analysis (in mm)
–
0.055
4.
Total Deformation for Buckling Analysis (in mm)
–
1
Sr. No.
Parameter
Results
Theoretical
Analytical (max)
1.
Normal Stress (b in MPa)
110
157
2.
Critical Buckling Load (PCR in N)
51338.6
51646.73
3.
Total Deformation for Static Analysis (in mm)
–
0.055
4.
Total Deformation for Buckling Analysis (in mm)
–
1
Thus, it can be concluded that the design and analysis of the Connecting Rod was carried out both, accurately and successfully.
Table 3. Result table
For calculating the Theoretical Buckling Load, the force acting on the small end was multiplied by Factor of Safety. The load multiplier which we get from buckling analysis in ANSYS, is nothing but the Factor of Safety. So, for calculating the Analytical Buckling Load, we need to multiply the Force Applied by the load multiplier. Load multiplier was 3.0178 for mode 1 (See Fig. 13.b.) and 6.6396 for mode 2 (See Fig. 14. a.).
-
CONCLUSIONS
In this study, we have designed the Connecting Rod, carried out Finite Element Analysis for Connecting Rod, and the results have been tabulated in the previous sections. The following inferences can be drawn from Finite Element Analysis
-
Static Analysis shows that the stress generated in the model is within acceptable limits or maximum allowable stress.
-
The Displacement Plot shows very insignificant deformation, which has no consequence on the functioning of the Connecting Rod. Hence, it will not deform under the applied load.
-
Buckling Analysis shows the buckling shape accurately, with the maximum deformation in the centre part of the Connecting Rod
-
Buckling Analysis gives buckling factor greater than 1 and hence the Connecting Rod will not buckle under currently applied load.
-
The values of Theoretical Factor of Safety and Analytical Load Multiplier are almost identical. From the load
REFERENCES
-
Bhandari V.B., Design of Machine Elements 3rd Edition, 2010, Tata McGraw Hill Education (India) Pvt. Ltd., New Delhi.
-
Khurmi R.S., Gupta J.K., A Textbook of Machine Design, 2005, Eurasia Publishing House Pvt. Ltd., New Delhi.
-
M.N. Ilman , R.A. Barizy, Failure analysis and fatigue performance evaluation of a failed connecting rod of reciprocating air compressor, Department of Mechanical and ndustrial Engineering, Gadjah Mada University, Indonesia, Engineering Failure Analysis 56, 2015, 142149..
-
A. Strozzi, A. Baldini, M. Giacopini, E. Bertocchi, S. Mantovani, A repertoire of failures in connecting rods for internal combustion engines, and indications on traditional and advanced design methods, Department of Engineering Enzo Ferrari, University of Modena and Reggio Emilia,.
-
Mohammed Mohsin Ali H, Mohamed Haneef, Analysis of Fatigue Stresses on Connecting Rod Subjected to Concentrated Loads At The Big End, 4th International Conference on Materials Processing and Characterization, Science Direct, Materials Today: Proceedings 2 , 2015
, 2094 2103.
-
DR.B.K.Roy, Design Analysis and Optimization of Various Parameters of Connecting Rod using CAE Softwares, International Journal of New Innovations in Engineering and Technology (IJNIET), Vol. 1 Issue 1, October 2012.
-
Tukaram S. Sarkate, Sachin P. Washimkar, Sachin S. Dhulekar, Optimization of steel connecting rod by aluminum connecting rod using finite element analysis, International Journal of Recent Advances in Engineering & Technology (IJRAET), ISSN (Online): 2347 – 2812, Volume-1, Issue – 1, October, 2013.
-
N. P. Doshi, N. K. Ingole, Analysis of Connecting Rod Using Analytical and Finite Element Method, International Journal of Modern Engineering Research (IJMER), Vol.3, Issue.1, Jan-Feb. 2013 pp-65-68 ISSN: 2249-6645.
-
Biradar Akshaydatta Vinayakrao, Prof. Swami M. C. Analysis and Optimization of Connecting Rod used in Heavy Commercial Vehicles, International Journal of Engineering Development and Research (IJEDR), Vol 5, Issue 3, 2017. ISSN: 2321-9939.
-
A. R. Pani , R. K. Patel, G. K. Ghosh, Buckling analysis and material selection of connecting rod to avoid hydro-lock failure, Materials Today: Proceedings, July 2019.
-
Nagaraju K L, Chandan R, Buckling Analysis Of Connecting Rod, International Research Journal of Engineering and Technology (IRJET),
Volume: 03 Issue: 08 | Aug-2016, e-ISSN: 2395 -0056
-
N. K. Sahu, S. K. Singh, Buckling Analysis of Connecting Rod with Ultra Fine Grained Material AA2618, International Journal of Engineering Research & Technology (IJERT), ISSN: 2278-0181, Vol. 6 Issue 06, June 2017