
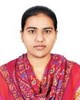
- Open Access
- Authors : Ayesha Firdose , Sreenath K
- Paper ID : IJERTV11IS070264
- Volume & Issue : Volume 11, Issue 07 (July 2022)
- Published (First Online): 05-08-2022
- ISSN (Online) : 2278-0181
- Publisher Name : IJERT
- License:
This work is licensed under a Creative Commons Attribution 4.0 International License
Design and Control of Inverter for Integration of Micro-Grid Connected Distributed Generation
Ayesha Firdose
M. Tech Student
Department of Electrical and Electronics Engineering Sri Siddhartha Institute of Technology, Tumakuru, Karnataka, India.
Sreenath K
Assistant Professor
Department of Electrical and Electronics Engineering, Sri Siddhartha Institute of Technology, Tumakuru, Karnataka, India.
Abstract For reliable, sustainable, safe and quality supply of electrical energy, Smart grids are widely used now. The Distributed generation system provides solution to many power system problems. Integration of DG units with existing grid requires suitable interface. In this work, an inverter is designed and controlled to achieve the best integration of smart grid and DGs. This project deals with the hybrid connection of wind power generator and solar power generator along with their controllers with the existing grid. Separate MPPT algorithms are selected for PV and wind system for optimized output. The combined output which is in the form of DC is then inverter so as to connect to the grid system.
MATLAB SIMULINK is carried out for each of the units and combined hybrid system. The simulation results are analyzed and validated.
Keywords Grid-connected models; power distribution system; existing controllers; microgrid; Matlab Simulink
I. INTRODUCTION
Electricity is a basic necessity for everybody nowadays. All the Industrial and even household equipment need electricity and the demand is ever increasing. The modern electrical power system consists of generation plants, a transmission network, and a distribution system. A reliable and economical supply of electric energy is a challenging task. The power systems are becoming large and complex systems. A integrated power system is extremely complex to control and operate in a secured and economical manner. The present transmission lines are critically loaded with very little reserve due to increase in load demand and increased generation from the units. It has led to decrease in security as the probability of a fault results in heavy loss both technically and economically. The limited conventional energy resources available in nature, the damage to the environment caused by these energy sources and the fact that they will be depleted is alarming. The scarcity of electricity is due to depletion of fossil fuel and an increase in demand because of industrial development, consumer consumption and lifestyle. In order to compensate for the shortages in energy, a solution must be sorted out and should meet the energy demand. The best solution is to consider the alternate energy sources and the most easily available and advantageous, among these is the power from sun and wind. The tapping of solar and wind energy into electric power is possible due to tremendous advancements in power electronics. When geographical locations are advantageous, solar energy wind energy alone can supply large loads. Both of these renewable energy sources are not constant, they are intermittent. But both these
sources can be combined to realize a more the efficient and reliable system and the output can be maintained to the required level. The hybrid system is a system in which both conventional energy sources and renewable sources are used. Therefore, even the energies with structurally different properties can form a hybrid system. For example, it is possible to form a hybrid system consisting of wind turbines and solar panels as in this study. When the wind speed is sufficient, the wind turbines can generate energy whether it is day or night. However, solar panels can generate energy in certain time periods depending on the sunshine duration. However, the customers are deprived of energy when the wind speed and/or the sun are insufficient/not available. In this case, the smart grids are engaged and the receivers are fed from the grid. Thus, the continuity of energy is ensured for the load without any interruption. Recently, the demand for smart grids has increased. The underlying reasons behind this demand are as follows: the detailed price information in the smart grid; the opportunity to choose among many programs, prices. The fact that various distributed generation resources are included in the system in addition to the central system; ensuring the development of new electricity market which takes into account the technological developments and different production options; the fact that the power quality is a priority in terms of smart grids. The increase of the productivity and efficiency along with the integration of artificial intelligence of the grid into asset management applications; taking precautions in advance for preventing the failure; minimizing the effects of failure and ensuring the continuity of communication; the fact that the system continues to operate by recovering itself rapidly under circumstances such as natural disasters and attack. In the present work, an attempt is made to make a micro smart grid by appropriately integrating solar, wind, and conventional grid to obtain a reliable hybrid power system.
-
PROBLEM STATEMENT
Wind power generation and solar power generation are integrated to a distribution power grid to make an hybrid micro power system. The integration causes some dynamic transient problems due to natural wind and solar irradiance change. Suitable controllers are to be used so that the load is primarily supplied using renewable energy and grid is used only to supply the deficiency. This work aims to select proper controllers, boost converter and inverter configurations to integrate the PV, wind and grid to make a micro grid.
SCOPE OF THE PROPOSED WORK
The objectives of the proposed work are:
-
To develop a solar PV system with proper control to be integrated to an existing grid.
-
To develop a wind power system with proper control to be integrated to an existing grid.
-
Both solar and wind systems are integrated into a distribution grid with the required controls.
-
The individual components are simulated and are integrated to realize the complete micro grid system.
-
THE MICROGRID SYSTEM
Micro grid (MG) is a group of single controllable entity which contains micro sources, energy storage system, load components, interfacing converters and many other devices. It is a kind of structure which provides self-management, and also builds strong control schemes and makes the electricity network more appropriate and smart with the use of micro source and energy storage devices.
The power connection between micro grid components such as distributed generators and energy storage system can be done through direct current (DC), and alternating current (AC). In this project AC micro grid has been considered.
There are some challenges while integrating with the renewable energy sources because their output is variable and intermittent also requires an energy storage system. If only one renewable energy source is considered then the integration is easier and it can be in standalone mode and it is also connected to the energy storage system. When the grid is connected to the integration of renewable energy sources then the power is injected directly into the power network. It creates some problem of power balancing, need to handle the transmission system operators.
-
BASIC STRUCTURE OF MICRO GRID SYSTEM
Figure 1. Components of Microgrid.
The interconnection as well as the power flow between different components of a typical MG power system is depictedin figure 1. Diesel generation is usually used in remote areas due to its stability and fast installation. The other energy sources (Wind, Hydro and Solar) are renewable and some of them, in particular wind and solar, are characterized by their intermittence. To refine the power profile, Fossil fuel storage system(FESS) are used given their high efficiency, ability to switch rapidly between load (charge) and generator (discharge) states.
MG Consumers are the local residential and industrial infrastructures with variable consumption profile. Operational
parameters and variables of the MG devices (voltage, frequency, speed, torque, power, temperature, etc.) are monitored by the micro grid energy management system (MEMS). It evaluates in real time the power requirements in the MG and produces controls for an optimal system operation (in particular, a constant frequency and voltage operation).
-
CONTROL AND MANAGEMENT OF MICROGRID Control system in micro grid contrast to conventional power systems, this is due to several reasons, among others:
-
Steady state and dynamic characteristics of micro grid different from conventional plants.
-
Micro grid possesses inherent unbalanced load due to one phase loads.
-
The supply of power from micro grid can come from uncontrolled sources such as wind.
-
The role of energy storage is very large in the control mechanisms used.
-
Micro grid accommodates disconnection and connection mechanisms to maintain expenses during its operating.
-
Micro grid requires initial requirements of power quality or service preferences for certain types of loads.
-
-
ADVANTAGES OF MICROGRID SYSTEM
The advantages of MG system are:
-
Micro grid, have ability, during a utility grid disturbance, to separate and isolate itself from the utility seamlessly with little or no disruption to the loads within the Micro grid.
-
In peak load periods micro grid can prevents utility grid failure by reducing the load on the grid.
-
Micro grid has environmental benefits made possible by use low or zero emission generators.
-
In micro grid to increasing energy efficiency, the use of both electricity and geat is permitted to get closer to user.
-
Micro grid can act to mitigate the electricity costs to its users by generating some or all of its electricity needs.
-
-
RESEARCH OPPURTUNITIES IN MICRO GRIDS Future directions which require further investigation in the context of micro grid research are:
-
To investigate performance of frequency/voltage control methods under different operation modes.
-
Integration of distribution generation and the connected challenges.
-
The control, protection and power quality issues.
-
Transformation of micro grid system to smart micro grids.
-
-
BASIC STRUCTURE OF PROPOSED MG SYSTEM
Block diagram of the system shown in Figure 2.2 consists of solar photovoltaic which gives DC output voltage. Wind turbine which gives AC output voltage, to integrate solar energy and wind energy it is necessary to convert AC voltage
of wind into DC voltage for this purpose universal bridge is used. So, this DC voltage boosted by using boost converter it will gives as input to the three-phase inverter getting AC output voltage. Three-phase inverter is connected to transformer; the transformer is used for increasing or decreasing the alternating voltages in electric power applications. Finally whole system is given to electric grid, which is an interconnected network for delivering electricity from producer to consumer.
Figure 5: Block diagram of system
-
REALIZATION OF THE PROPOSED MODEL
The proposed hybrid simulation model is designed in Matlab Simulink and consisted of 3 basic parts.
-
In the first step, DC voltage is obtained from the wind turbine and solar panel.
-
In the second step, the DC voltage is stepped to the required level.
-
In the third step, the 3-level NPC (neutral point clamped) inverter is developed.
-
In the fourth step, the renewable are integrated to the grid.
-
In the fifth step, the integrated system is simulated and the results are analyzed.
-
The first step of the proposed simulation, the wind turbine and the solar panel are connected in a parallel way. For the wind turbine, the wind speed is assumed as different variables like 6,8,10m/s and pitch angle value is taken as 0. For the solar panel, the irradiation is set to 1000w/m2 and the temperature is set to 250 C. The values are iterated for different settings such as 0, 500, 1000, 500, 0 w/m2 to account for the natural variations. Because irradiance is not constant it is varied. In other words, a micro modeling is done with reference to the natural conditions of the hybrid system.
In the second step, the boost converter simulation model is considered. In this, separate boost converters are used at the output side of the solar system and wind system to boost up the voltage up to the required level. As different output voltage result from solar and wind systems, they have to be properly taken care off. So it is necessary to use the MPPT controller to track maximum power of hybrid system as well as maintaining the duty cycle in boost converter. By using this controller we can achieve the required output voltage in the boost converter.
In third step, a suitable inverter topology is used to obtain the required ac system. The energy is converted to three phase 415V AC by using 3-phase three level Neutral Point Clamped (NPC) inverter. The NPC inverter is more advantageous than other inverters. The variation in output voltage can be achieved by the controlling the modulation index in the
inverter. The VSC (Voltage source controller) is used to maintain this modulation index in the inverter to achieve minimum 415V AC at the output side. The VSC controller not only controls the modulation index, it can be used to maintain unity power factor by varying active and reactive power. The inverter output is connected to the load as well as the grid. A 415/11000V transformer is used to connect the inverter output to the grid.
-
-
IMPLEMENTATION OF THE MICROGRID SYSTEM
-
-
3.1 SOLAR PV PANEL
A PV (Photovoltaic) cell is a semiconductor device that converts light energy to electrical energy by photovoltaic effect. If the energy of photon (light) is greater than the band gap then the electron is emitted and the flow of electrons creates current. However a PV cell is different from a photo- diode. In a photo-diode light falls on the n-channel of the semiconductor junction and it gets converted into current or voltage signal but a PV cell is always forward biased. Usually a number of PV modules are arranged in series and parallel to meet the requirements of energy. PV modules are arranged in series and parallel to meet the requirements of energy. PV modules of different sizes are commercially available.
A PV array consists of several PV cells is series and parallel connections. It is the combination of many PV modules. Parallel connections are responsible for increasing the current of the module whereas the series connection is responsible for increasing the voltage in the array. A solar cell can be modeled by a current source and a diode which is inverted is connected in parallel to it. It has its allowable series and parallel resistance. Series resistance is due to the blocking in the path of flow of electrons from n junction to p junction and parallel resistance is due to the leakage current shown in Figure 3.1.
Fig.3.1: Circuit Diagram of Solar PV Cell.
Diode Characteristic Id=I sat*[exp (Vd/VT)-1] (3.1)
Where: Id=diode current (A) VT=temperature voltage=k*T/q*Qd*Ncell*Ns (3.2)
Where: T= cell temperature(K).
k = Boltzmann constant=1.3806e-23 J.K^-1 q = electron charge = 1.6022e-19 C
Qd = diode quality factor
Ncell= number of series-connected cells per module Nser = number of series-connected modules per string
Fig.3.2: V-I and P-V Characteristic of Solar Panel
Specification of Solar panel:
radiation, the cell temperature and the output voltage level. Because of the nonlinear characteristic, a PV module has to be modeled appropriately for analysis and implementation. As the efficiency of the module is typically low, optimum operation with respect to the output is to be realized. The MPPT is incorporated for this purpose. Many MPPT techniques are investigated and adopted. The perturb and observe (P&O) algorithm is one of such techniques and is the most simple among them. The method moves the operating point towards maximum power point periodically by increasing or decreasing PV voltage.
The P&O method is also called hill-climbing. Hill- climbing consist of a perturbation on the duty cycle of the power converter while P&O is a perturbation in the operating voltage of the DC link between the PV array and the power converter.
TABLE 1: SOLAR PANEL PARAMETER E
PV MODULE
BOOST CONVERTER
LOAD
VOLTAGE AND CURRENT SENSOR
MPPT
DUTY CYCLE T
-
MPPT CONTROLLER
Solar Panels generate power by using the photovoltaic effect: electrons are transferred between different energy bands in the atom by means of irradiation. The solar panel has a p-v characteristic where a global maximum is present. This means that for a different operating point of the solar panel, a different output power is obtained. The maximum power is obtained when the solar panel operates at the voltage where the global maximum of the p-v characteristic is present. Therefore, only for one specific operating point, the maximum power output is obtained from the solar panel. This point in the p-v characteristic is called the maximum power point (MPP). This MPP changes when the irradiation and temperature changes or when the solar panel is partially shaded. The required block diagram is shown in Figure 3.3 Solar MPPT can be classified as:
-
Hill climbing or Perturbation and Observation (P&O).
-
Incremental and conductance.
-
Artificial Neural Network (ANN) with back propagation technique.
-
Fuzzy Logic Controller Intelligent Control (FLCIC) with DC-DC converter.
-
Open Circuit Voltage Control (OCVC).
-
Short-Circuit Current Control (SCCC).
-
Particle Swarm Optimization.
As the outputs of the PV Panels are changing, a proper controller is required to track the optimum output point. Such a controller is called Maximum Power Point Tracker (MPPT). The power output of a PV module is determined by the intensity of solar radiation, the cell temperature and the output of a PV module is determined by the intensity of solar
Fig.3.3: Block Diagram of the solar system with Boost converter and its controller
In the P&O method, positive and negative directions are assigned to increment and decrement of the power respectively. Similarly the different of perturbation is also given positive and negative directions. The sign of power is used to decide the sign of the perturbation. The incrementing and decrementing the voltage varies the power output as shown in Figure 3.4.
Fig.3.4: Characteristic Curves of PV Panel.
If there is any increase in the power, the next perturbation should be kept in the same (+ve) direction. On the other hand, if the power decreases, then the next perturbation should be in the reverse (-ve) direction. The perturbation process is repeated until the MPPT is reached. Obviously the operating point oscillates around the MPPT.
-
-
BOOST CONVERTER WITH MPPT
Boost converter is also known as step-up converter. DC to DC converter step-up the voltage and stepping down the current . It is consisting of diode and transistor and one
energy storage element like inductor, capacitor or both combinations. The output of the boost converter is greater than the input source voltage.
The output voltage of the solar photovoltaic system is given input to the boost converter which step up the input voltage. In the simulation circuit assuming the input voltage as 273.5V and we get the boosted output voltage is 900V dc. In the boost converter circuit IGBT switch connected in parallel with diode, inductor, capacitor and load.
Fig.3.6: Circuit Diagram and Waveform of Boost Converter.
Design of boost converter:
If Boost converter is working is working in discontinuous conduction mode. i.e, if it is less than five times the duty cycle. Then we select one solar panel voltage as 54.7V. PV output of one module voltage =54.7V.
Series connected panel=5.
Total voltage =273.5V.(Boost converter input voltage) Parallel connected panels=17.
Current of one module=5.58A. Total current from panel=94.86A. Total power of PV panel=26KW. Frequency=5 KHz (considered). Boost converter duty cycle
D=1-[vin/vout]=0.21 (3.3)
(It is less than0.5 and it is operated in DCM mode)
Resistance(R) =[V/I]=40.5 ohms (3.4)
(As per IEEE STD we select 50 ohms) Inductor value (L) = {(DR)(1-D)2 }/2f=5e-3H (3.5)
(As per IEEE STD we select 1mH) Capacitance value= (DV0)/ (VrefL)=7.9245F (3.6)
(As per IEEE STD we select 12000e6F)
The DC-DC converter is to change the input DC voltage level to another DC voltage level to another DC voltage level. The converter used is a step-up converter, to increase the level of the input voltage to a suitable level to charge batteries. The schematic representation of the boost converter is shown in Figure 3.6. The converter consists of mainly an inductor, switching device (IGBT) and a diode. The current from the source charges the inductor when switch is in the OFF state. When the switch is in ON state, the energy stored in the inductor superimposed with the source energy resulting in the increase of the output voltage. For ideal operating conditions, Vin and Vout can be obtained using 3.8. In 3.8, D represents the
duty cycle of the PWM signal and has a value between 0 and
1. This property is used to adjust the operating point of the MPPT.
Vin/Vout =1/ (1-D)
(3.8)
The MPPT controller executes the algorithm to track the MPP. The voltage and current of the PV panel are used the input parameters for the controller. The input control variables are normalized in the range of 0-5 volts. The output of the controller is the required duty cycle of the PWM, to achieve a specified output voltage of the system. These control variable values are also used to find the amount of energy generated and to identify possible failures in the system. The simulation model is represented in Figure 3.7.
Fig.3.7: Simulation of Solar Panel and Boost Converter with MPPT.
-
WIND SYSTEM
The wind power is generated due to the variation of wind speed. Among the various type of wind turbine permanent magnet synchronous wind turbine, which have higher reliability and efficiency. Hybrid wind driven PMSG-PV system which is AC power, is fed to the rectifier bridge, the variation in the wind power results into the variation in the output power of the rectifier. Therefore, there is requirement of DC-DC converter for increasing the amount of voltage of the wind system and making the output voltage constant. And for tracking the maximum power from the wind maximum power point tracking method is employed.
Fig.3.8: Block Diagram of Wind Turbine
Wind energy is one of or another form of solar energy, because of disorderliness it is considered to be low quality energy. A wind energy system transforms the kinetic energy of the wind into mechanical or electrical energy that can be harnessed for practical use.
-
PERMANENT MAGNET SYNCHRONOUS GENERATOR
-
Permanent magnet synchronous machine PMSM is an AC machine with a permanent field system in the rotor. It consists of a regular stator of an AC machine. The rotor comprises of permanent magnets and there are no brushes. As the frequency of the excitation in the stator
winding is proportional to the mechanical speed of the rotor, this family of machines is called synchronous. The PMSM is a thus a synchronous machine in which the traditional DC excitation is obtained by permanent magnets.
Three wind turbines are used here to get higher voltage and current. Each wind turbine parameters are as follows i.e., nominal mechanical output power 20e3W, base power of the electrical generator is 20e3/0.9(VA), pitch angle is 0 because to maintain better base speed of 12m/s, base rotational speed is 1.2pu, maximum power at base wind speed 0.73 and also using three phase sinusoidal, salient pole 6Nm, 300V dc, 4500rpm permanent magnet synchronous generator. The output voltage from wind system is always ac so we convert it to dc because of this reason rectifier is used after to get pure waveform the capacitive filter and low pass filter is used. The Figure (3.9) shows simulation of wind generation system.
Fig.3.9: Simulation of wind Generation System
-
WIND MPPT
Wind MPPT can be classified as:
-
Tip speed ratio (TSR) control
-
Optimum relationship based (ORB) control,
-
Perturbation and observation (P&O) control
-
Hybrid control
-
Intelligent control techniques like fuzzy logic control, neural network control.
-
The P&O MPPT used in the PV system can also be used in wind system as a controller, as explained in section (3.1.1 and 3.1.2). In this case, wind speed and other environmental conditions are used to track the maximum output point. The method is based on perturbing control variable in arbitrary small steps, and the next perturbation is decided on observing the changes in power curve due to preceding perturbation. P&O approach is a very simply in implementation and hence it is largely used of the several MPPT algorithms.
3.3 INVERTER
Inverter converts DC to AC with real and reactive power control. This AC is given to the grid with filtering operations. The below figure 3.10 shows the classification figure shows the various types of inverter.
Fig.3.10: Classification of inverters.
3.3.1 NEUTRAL POINT CLAMPED INVERTER
In a multilevel NPC converter topology, the voltages stresses across the switches are lower and there are more available control vectors. Thus, the harmonic content of the converter is reduced if appropriate switching vectors are selected. A three-level NPC converter is shown in Figure 3.11. The three phases have a common DC bus, divided by two capacitors into three levels. The voltage across each capacitor is VDC/2; and the voltage stress across each switching device is limited to VDC/2 through the clamping diodes. A three level NPC converter is able to produce five levels of line to line voltage and three levels of phase voltage. This NPC converter reduces harmonics in both voltage and current output.
Fig.3.11: Three-level NPC Inverter Topology.
3.4 VSC CONTROLLER
The three-level VSC converter, whose Simulink implementation is depicted in Figure 3.12 and Regulates dc bus voltage at 728.9V and keeps unity power factor. The control system uses two control loops: an external control loop which regulates dc link voltage to +/-450V (is it about the voltage control of the two dc split capacitors C1 and C2) and an internal control loop which regulates Id and Iq grid currents (active and reactive current components). Id current reference is the output of the dc voltage external controller. Iq current reference is set to zero in order to maintain unity power factor. Vd and Vq voltage outputs of the current controller are converted to three modulating signals Uref_abc used by the pulse-width modulation (PWM) three level pulse generator. The control system uses a sample time of 100s for voltage and current controllers as well as for the phase locked loop (PLL) synchronization unit. Pulse generators of dc-dc boost and VSC converters use a fast sample time of 1 inorder to get an appropriate resolution of PWM waveforms. Simulation part of VSC controller is shown in below Figure 3.12.
Fig. 3.12: Simulation VSC controller.
Grid side controller employed for controlling the dc link as well as grid side parameters. Basic problem of distributed generator system is that there is always load unbalance hence grid side voltage is unbalance. When unbalance load is connected then grid side current in three phases are not equal, creates voltage drop across the LC filter. For these control algorithms for unbalanced voltage compensation is employed. In this control technique, the error between RMS value of line voltages at grid and reference line voltage is given to the PI controller. The PI controller output is multiplied with unit sine wave generator which generated by reference line voltages (vab_ref, vbc_ref, vcb_ref). The reference angle for sine wave generator is being calculated from phase locked loop (PLL). Therefore from vab_ref, vbc_ref and vcb_ref, PWM pulses are generated which are given to the grid side PWM inverter.
The Figure 3.13 represents the overall simulation of proposed hybrid system. This model contains the following elements: the hybrid system of solar and wind energy. PV array can produces the maximum power of 26KW at 1000 w/m2 sun irradiance and I 25C solar cell temperature. And wind can also deliver maximum power of 17KW at the base speed of 12m/s. The separate 5 kHz dc-dc boost converter used in wind and solar system to boost up the voltage to 728.9V. The MPPT controller is implemented using a variant subsystems dc-dc MPPT boost controls that automatically varies and optimizes the switching duty cycle in order to generate the required voltage to extract maximum power using state flow implementation of P&O. VSC controller is used to regulates dc bus voltage at 728.9V, keep unity power factor and also gave pulse to inverter switches. To get 3-phase voltage we boost up the hybrid system voltage to 728.9V and NPC inverter is used to achieve 415V ac it is a half of dc link voltage. Then it filtered out and connected to step-up transformer to step-up the voltage to 11kv after it is connected 100MVA utility grid as well as load.
Fig.3.13: Simulation Schematic of the Integrating System.
RESULTS AND DISCUSSIONS
-
OUTCOMES OF SOLAR PV PANEL
Irradiance iteration are set in the PV panel (0, 500, 1000, 500,0), initial solar cannot generate any voltage and current. After some time it can produce voltage of 65 and current of 100 these values are obtained at maximum irradiance i.e., 1000 w/m2. Irradiance will not constant, when it gets change then the voltage and current also change. It is shown in Figure 4.1.
Fig.4.1: voltage and current waveform of solar PV panel.
-
WIND SYSTEM RESULT
Wind system always produces ac output voltage because of generator is used in wind as per rating of wind it can produce the three phase voltage of 709.8V AC waveform. It shown in the figure 4.2 after rectification it converter into 709.8V DC. For synchronizing the both wind and solar we need to convert AC voltage of wind to DC the maximum current turbine is 42A which is represented in Figure 4.3.
Fig 4.2. Output Voltage of Wind turbine.
Fig 4.3. Output current from wind turbine
-
BOOST CONVERTER RESULT
Both boost converter in wind and solar can boost up voltage up to 728.9Vdc with the help of MPPT duty cycle. DC link voltage waveform is shown in below Figure 4.4.
Fig.4.4: Vdc Voltage from Hybrid System.
-
INVERTER OUTPUT
728.9V from dc link can be converted to 415V AC by using inverter. Three phase NPC inverter can produces the phase to phase sin wave of 450.i.e. half of Vdc. Practical Indian standard require 440V minimum it can require 415V. This variation can be controlled by modulation index in inverter. Here we use 0.7 modulation index. It should be controlled by particular grid side controller whatever 728.9 Vdc is given it can be converted into 415Vac and filtered out then it is given to step-up transformer to step-up the voltages till 11kv, this 11kv is directly connected to the grid voltage is shown in below Figure 4.5. And we made analysis on the total harmonic distortion of inverter, then we achieve less THD of 3.55% is represented in Figure 4.6.
Fig.4.5: Grid Side Voltage and Current.
Fig.4.6: THD Analysis.
4.5 POWER FROM HYBRID SYSTEM
Figure 4.5 shows waveform of hybrid system (solar and wind system) and grid, and explains how these can manage the load requirement of 30KW the concept is wind power generation and solar power generation are integrated at DC link. It is considered to distribution power grid, which causes some dynamic transient problems due to natural wind and solar irradiance change. If the power generation changes in PV the wind has to supply. If wind power is not available then PV has to supply. If wind and PV both are not available, grid has to supply.
The waveform explains same concept, initially the solar and wind not generate any power its 0KW so grid has to supply to load, so its a negative power in grid i.e., -30KW. After sometime still solar has 0KW,but wind generate 6KW of power, so remaining power to satisfy load requirement is 24KW, this can be supplied from grid side (-24KW). After sometime solar generate 12KW of power and wind has 6KW so totally 18KW from these hybrid system supplied to load, remaining 12KW can be supplied from grid to load. Again 26 KW from solar, 15KW from wind, totally 41KW from hybrid system. The power generated is more than that of load requirement so the positive values shown in grid side i.e., 11KW these are shown in Figure 4.7.
Fig.4.7. Power from Hybrid system and Grid
5.1 CONCLUSION
The proposed work is expected to use the micro hybrid power system to realize an optimal micro power system. Wind power generation and solar power generation are integrated to distribution power grid, which causes some dynamic transient problems due to natural wind and solar irradiance changes.
The system is implemented so as to use the available power from renewable sources to the load and if there is a shortfall, then only the grid power is used. This can be achieved by using many controlling devices like MPPTs to tract maximum power as well as adjust the duty using many controlling devices like MPPTs to tract maximum power as well as adjust the duty cycle for the boost converter switch,
VSC controller to maintain unity power factor as well as maintain dc link voltage and give switching pulses to the inverter.
The special multilevel NPC inverter is used to get 3phase voltage and to achieve less THD. The integrated system is simulated using MATLAB/Simulink and the results are analyzed. The simulation results are in good agreement of the defined condition.
-
SCOPE FOR FURTHER IMPROVEMENT
There are several possibilities to improve the present the present proposed system. Some of them are:
-
Consideration of other renewable sources.
-
Consideration of storage system as a DG.
-
Consider other MPPT controllers for implementation.
-
Use other inverter configuration to get better result.
-
REFERENCES
[1] Shi, Wenbo, Xiaorong Xie, Chi-Cheng Peter Chu, and Rajit Gadh. "Distributed Optimal Energy Management in Microgrids." IEEE Trans. Smart Grid, Vol 6, pp. 1137-1146, 2015. [2] F. Moehrke and J. Myrzik, "Control methods for microgrids," 2014 49th International Universities Power Engineering Conference (UPEC), Cluj-Napoca, pp. 1-6, 2014. [3] T. C. Green and M. Prodanovic´, Control of inverter-based microgrids, Journal of Elect. Power Syst. Research, vol. 77, no. 9, pp. 12041213, Jul. 2007. [4] J. M. Guerrero, J. C. Vasquez, J. Matas, M. Castilla and L.G.Vicuna, Control Strategy for Flexible Microgrid Based on Parallel Line- Interactive UPS Systems IEEE Trans. On Industrial Electronics, Vol. 56, Issue 3, pp. 726 736, March 2009. [5] F. Katiraei and M. R. Iravani, Power Management Strategies for a Microgrid with Multiple Distributed Generation Units IEEE Trans. on Power Systems, Vol. 21, Issue 4, pp. 1821 1831, Nov. 2006. [6] C. K. Sao and P. W. Lehn, Control and Power Management of Converter Fed Microgrids IEEE Trans. on Power Systems, Vol. 23, Issue 3, pp. 1088 1098, Aug.2008. [7] J. C. Vasquez, J. M. Guerrero, A. Luna, P. Rodriguez and R.Teodorescu, Adaptive Droop Control Applied to Voltage-Source Inverters Operating in Grid-Connected and Islanded Modes IEEE Trans. on Industrial Electronics, Vol. 56, Issue 10, pp. 4088 4096,Oct. 2009.
[8] M. C. Chandorkar, D. M. Divan, and R. Adapa, Control of parallel connected inverters in standalone ac supply systems, IEEE Trans. Ind. Appl., vol. 29, no. 1, pp. 136143, Jan./Feb. 1993. [9] J. Holtz and K.-H. Werner, Multi-inverter UPS system with redundant load sharing control, IEEE Trans. Ind. Electron., vol. 37, no. 6, pp. 506513, Dec. 1990. [10] H. Van Der Broeck and U. Boeke, A simple method for parallel operation of inverters, in Proc. IEEE Telecommunications Energy Conference, 1998, pp. 143150. [11] H. Hanaoka, Development of a novel parallel redundant UPS, in Proc. IEEE Telecommunications Energy Conference, 2003, pp. 493 498. [12] M. Arias, D. G. Lamar, M. Rodriguez, M. Hernando, and A. Fernandez, Simple droop voltage control system for parallel operation of UPS, in Proc. IEEE APEC, 2004, pp. 19461951. [13] M. C. Chandorkar, D. M. Divan, Y. Hu, and B. Banerjee, Novel architecture and control for distributed UPS systems, in Proc. IEEE APEC, 1994, pp. 683689. [14] W. Yao, M. Chen, J. Chen, and Z. Qian, An improved multiple-loop controller for parallel operation of single-phase inverters with no control interconnections, in Proc. IEEE PESC, 2007, pp. 448452. [15] K. De Brabandere, B. Bolsens, J. Van den Keybus, A. Woyte, J. Driesen, and R. A. Belmans, Voltage and frequency droop controlmethod for parallel inverters, IEEE Trans. Power Electron., vol. 22, no. 4, pp. 11071115, Jul. 2007.
[16] L. Mihalache, Paralleling control technique with no intercommunication signals for resonant controller-based inverters, in Conf. Rec. IEEE IAS Annu. Meeting, 2003, vol. 3, pp. 18821889. [17] U. Borup, F. Blaabjerg, and P. N. Enjeti, Sharing of nonlinear load in parallel-connected three-phase converters, IEEE Trans. Ind. Appl., vol. 37, no. 6, pp. 18171823, Nov./Dec. 2001. [18] S. J. Chiang and J. M. Chang, Parallel control of the UPS inverters with frequency1dependent droop scheme, in Proc. IEEE PESC, 2001, pp. 957961. [19] K. Jaehong, J.M. Guerrero, P. Rodriguez, R. Teodorescu and N. Kwanghee, Mode Adaptive Droop Control With Virtual Output Impedances for an Inverter-Based Flexible AC Microgrid, IEEE Trans. on Power Electronics, vol.26, no.3, pp.689-701, March 2011. [20] C. Trujillo, F. Velasco, D. G. Garcera, E. Figueres and J.Guacaneme, Reconfigurable control scheme for a PV microinverter working in both grid connected and island modes IEEE Trans. on Industrial Electronics, 2012. [21] O. Wasynczuk, Dynamic behavior of a class of photovoltaic power systems, IEEE Trans. Power App. Syst., vol. PAS-102, no. 9, pp. 30313037, Sep. 1983. [22] R. Alonso, P. Ibáñez, V. Martinez, E. Román, and A. Sanz, An innovative perturb, observe and check algorithm for partially shaded PV systems, In proc. Power Electronics and Applications Conf., Spain, 2009, pp. 1-8. [23] N. Femia, G. Petrone, G. Spagnuolo, and M. Vitelli, A technique for improving P&O MPPT performances of double-stage grid-connected hotovoltaic systems, IEEE Trans. Ind. Electron., vol. 56, no. 11, pp. 44734482, Nov. 2009. [24] W. T. Chee, T. C. Green, and A. H.-A. Carlos, Analysis of perturb and observe maximum power point tracking algorithm for photovoltaic applications, In Proc. Power and Energy Conf., Malaysia, 2008, pp. 237-242. [25] A. Pandey, N. Dasgupta, and A. K. Mukerjee, High-performance algorithms for drift avoidance and fast tracking in solar MPPT system, IEEE Trans. Energy Convers., vol. 23, no. 2, pp. 681689, Jun. 2008. [26] E. Koutroulis, K. Kalaitzakis, and N. C. Voulgaris, Development of a microcontroller based, photovoltaic maximum power point tracking control system, IEEE Trans. Power Electron., vol. 16, no. 1, pp. 46 54, Jan. 2001. [27] H. Karimi, H. Nikkhajoei and R. Iravani, "Control of an Electronically- Coupled Distributed Resource Unit Subsequent to an Islanding Event," IEEE Trans. Power Delivery, vol. 23, no. 1, pp. 493-501, Jan. 2008. [28] R. Majumder, B. Chaudhuri, A. Ghosh, G. Ledwich and F. Zare, "Improvement of Stability and Load Sharing in an Autonomous Microgrid Using Supplementary Droop Control Loop," IEEE Trans. Power Systems, vol. 25, no. 2, pp. 796-808, May. 2010. [29] N. Pogaku, M. Prodanovic and T. C.Green, "Modeling, Analysis and Testing of Autonomous Operation of an Inverter-Based Microgrid," IEEE Trans. Power Electronics, vol. 22, no. 2, pp. 613-625, March 2007. [30] Y. W. Li and C. Kao, "An Accurate Power Control Strategy for Power- Electronics Interfaced Distributed Generation Units Operating in a Low-Voltage Multibus Microgrid," IEEE Trans. Power Electronics, vol. 24, no. 12, pp. 2977-2988, Dec. 2009. [31] J. A. P. Lopes, C. L. Moreira and A. G. Madureira, "Defining control strategies for MicroGrids islanded operation," IEEE Trans. Industrial Electronics, vol. 21, no. 2, pp. 916-924, May 2006. [32] Liserre, M., Sauter, T., Hung, J.Y. Future Energy Systems: Integrating Renewable Energy Sources into the Smart Power Grid Through Industrial Electronics. IEEE Industrial Electronics Magazine, 4(1), 1837, (2010). [33] Zamora, R., & Srivastava, A.K. Controls for Microgrids with Storage: Review, Challenges, and Research Needs. Renewable and Sustainable Energy Reviews, 14(7), 20092018, (2010). [34] Laaksonen, H.J. Protection Principles for Future Microgrids. IEEE Transactions on Power Electronics, 25(12), 29102918, (2010).