
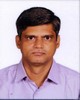
- Open Access
- Authors : Dr.K.Ragu
- Paper ID : IJERTV14IS010013
- Volume & Issue : Volume 14, Issue 1 (January 2025)
- Published (First Online): 13-01-2025
- ISSN (Online) : 2278-0181
- Publisher Name : IJERT
- License:
This work is licensed under a Creative Commons Attribution 4.0 International License
Design and Development of an Automated Module for Brazing the Rotor Elements of a Pump
Dr.K.Ragu Ph.D.
Department of Mechanical Engineering PSG College of Technology, Coimbatore, India
Abstract Borewell submersible pumps are normally driven by squirrel cage type of induction motors. The rotors of these motors are manufactured by inserting copper or aluminium bars through laminated sheets and short circuiting these bars at the ends using a brazing process. The brazing process at the pump manufacturing industry entails exposure to elevated temperatures for both components and workers. Manual brazing of rotor components using an induction type of heaters causes health hazard to workers and reduce productivity. To address these challenges, a development of an automated module for replacing the existing brazing machine is attempted in this article. This module aims to eliminate human intervention as much as possible, thus reducing exposure to heat while significantly enhancing productivity. Automating the brazing process results in improved safety standards, increased efficiency and minimized downtime.
Keywords brazing; induction heating; automation
-
INTRODUCTION
Squirrel cage induction motors are widely used in the industry as they are simple, rugged and self-starting. The rotors of these induction motors are constructed by inserting a certain number of copper or aluminium bars through the slots of cylindrical laminated core and joining two short circuiting end rings at both the ends. Brazing is widely used to join these two end rings with the conducting bars. Brazing involves heating of materials to a suitable temperature and the utilization of a filler metal (referred to as braze) with a liquidus temperature above 450ºC and below the solidus temperature of the base material. The filler metal is drawn into the joint gap by capillary action, requiring metallurgical compatibility between the filler and parent materials, as well as a minimum gap design for optimal joint formation. Heat required for carrying out brazing can be derived from many sources and induction heating is one of them. Induction heating has several advantages which includes localized heating, temperature control, energy saving and pollution free. Induction heating systems can be easily integrated into series production lines. This allows quick and easy implementation of complex processes and technologies. Amount of energy applied to joining parts can be quite precise controlled by using induction systems. A temperature profile can be easily defined to fulfill process requirements in closest shape possible [1]. Yankang Tian et al. [2] had analysed heating schemes and process parameters of induction heating for preparing aluminium sheets for hot stamping operation. It was numerically demonstrated that the temperature during induction heating for this operation rises upto 525°C. Current study pertains to heating the parts of a rotor of an induction motor for the purpose of joining them using brazing. As the brazing operation requires the filler material to be heated upto its liquidus temperature, the induction heater which is to be
employed for the current study has to generate heat to reach the liquidus temperature of 450°C. The industrial workers who are employed to carry out this brazing operation are hence exposed to high heat environment. The most serious form of heat stress is heat stroke, which can cause irreversible damage to the heart, lungs, kidneys and liver [3]. Thus, a need arises to automate the brazing operation carried out on the rotors of the induction motors. The following chapters give the details of the developed module.
-
STUDY OF EXISTING PROCESS
Current study pertains to rotor manufacturing in a pump making industry. The brazing process which is currently being followed by the industry is observed to ascertain the scope for its automation. The sequence of activities performed in the industry for joining the parts using brazing is as follows. A worker physically loads the rotor onto an induction heating machine. The rotors are pre-fitted with conducting bars. Filler metal and a short circuiting end ring are placed over the rotor which has been positioned in a vertical direction. The induction coil of the heating machine is positioned around the top edge of the rotor in such a way that the conducting bars and end ring are simultaneously heated upon switching on the power supply. The filler metal melts under the heat and flows through the gap due to capillary action. The power supply is switched off and the parts are allowed to cool in the machine itself until the filler metal solidifies. Thus a brazed joint is made between conducting bars and short circuiting end ring. The worker lifts the induction coil and inverts the rotor for performing brazing operation on the other end of the rotor in a similar way. The brazed rotor is unloaded by the worker and next rotor is placed on the heating machine and the cycle continues.
Following are the shortcomings which have been identified on observing the existing process.
-
Employees of brazing section are exposed to elevated temperatures.
-
As they handle the rotors manually for loading, unloading and inverting, they show early signs of fatigue.
-
The productivity of brazing section is not in line with other sections of the industry due to longer cycle time of existing brazing operation.
-
-
CONCEPTUAL DESIGN 1
Considering the issues that have been identified during the brazing process, a rough concept of the automated module is developed in the initial stage, which has been further improved later. Fig.1 shows the assembly drawing of the
Conceptual Design 1. Three dimensional modals of the overall assembly and subassembly of the gripper are shown in Fig.2 and Fig.3 respectively.
The Conceptual Design – 1 has two stations as shown in the figure. Indexing between Station 1 and Station 2 is effected by a gear mechanism located underneath the circular base plate.
STATION 1
STATION 2
Rotor
Gripper
Gear assembly
Bearing assembly
Rack and pinion
Pneumatic cylinder
Stepper motor
Fig. 1 Assembly Drawing of Conceptual Design 1
Fig. 2 Three dimensional model of Conceptual Design 1
Fig.3 Sub Assembly of Gripper
The gripper is connected to the pinion of a rack and pinion mechanism through a shaft which is supported using a ball bearing. While brazing is being carried out in Station 1, loading and unloading actions are taking place in Station 2, resulting in the reduction of cycle time. On completion of brazing at one end of the rotor, the gripper that holds the rotor is rotated by 180° by the rack and pinion mechanism and brazing is carried out at the other end of the rotor. The base plate is then indexed and the next rotor arrives at Station 1. The finished rotor is unloaded and a new rotor is loaded at Station 2. The sequence of operations that are taking place at the two stations are tabulated in Table 1. The cycle time for brazing a rotor is 215 seconds and the time taken to accomplish each of these operations are shown in Fig.4. It can be observed from the figure that brazing and solidification of joints by cooling takes longer duration than any other operation.
S.No.
Station 1
Station 2
1
Lifting the rotor to bring its end nearto the induction
heating coil.
Idle
2
Brazing and cooling
Unloading the finished rotor
3
Lowering the rotor
Idle
4
Rotating the rotor by 180 degrees
Idle
5
Lifting the rotor to bring its
other end near to the induction heating coil.
Idle
6
Brazing and cooling
Loading a new rotor
7
Lowering the rotor
Idle
8
Indexing the base plate
Idle
TABLE I. Sequence of operations at the two stations
STATION 2
8.Idle 1.Idl e
7.Idl e
2.Unl oad
6.Loa d
3.Idle
5.Idl e
4.Idle
Fig.4 Split-up of cycle time of the two stations
-
CONCEPTUAL DESIGN 2
Conceptual Design 2 is an improvised version of the earlier design. Conceptual Design – 1 is found to be having few drawbacks due to the following reasons.
-
The largest variant of rotor which the automated module has to handle weighs around 40 kgs. Gripper cannot be used to hold the rotor throughout the cycle time.
-
Probability of pneumatic cylinder failure is high due to heavy load (nearly 200 kgs) acting upon it.
-
The forces acting on the pneumatic cylinder might be unbalanced while rising and lowering.
Addressing the aforementioned shortcomings, Conceptual Design – 2 has been developed. The assembly is shown in Fig.5 and sub-assemblies are shown in Fig.6 and Fig.7. Pneumatic
Fig.5 Three dimensional model of Conceptual Design 2
Fig.6 Sub-assembly of indexing mechanism
Fig. 7 Sub-assembly of rotor invertor mechanism
chucks are employed as work holding devices. Three numbers of pneumatic chucks are placed at 120° apart on a round indexing table. There are three stations and the rotors are sequentially moved through each station by the indexing table. Brazing is carried out at Station 1 and the rotors are inverted upside down at Station 2. Loading and unloading operations are carried out at Station 3. The details of operations carried out on the rotors at each station is listed in Table 2. It is worthwhile to mention that the entire subassembly of indexing mechanism alongwith the rotors is raised to bring the edge of the rotor of Station 1 near to the heating coil of that station for carrying out brazing operation on that particular rotor. After the brazed joint cools down, the subassembly is lowered and the table is indexed through 120 degrees. Thus the table is raised and lowered for every indexing movement of the table. The cycle time for brazing a rotor using this module is 231s.
i-th rotation
Position of indexing table (in degrees)
Status of the workstations
Station 1 (Brazing)
Station 2 (Inversion of rotors)
Station 3 (Loading and Unloading)
1
0
Off
Off
Load Rotor 1
120
On
Off
Load Rotor 2
240
On
On
Load Rotor 3
2
360
On
On
Unload Rotor 1 and
Load Rotor 4
TABLE II. OPERATIONS CARRIED OUT ON THE ROTORS AT THE THREE STATIONS FOR EVERY POSITION OF THE INDEXING
120
On
On
Unload Rotor 2 and
Load Rotor 5
240
On
On
Unload Rotor 3 and
Load Rotor 6
3
360
On
On
Unload Rotor 4 and
Load Rotor 7
.
.
.
.
.
.
.
.
4
.
.
.
.
-
-
RESULTS AND DISCUSSIONS
The brazing process carried out on the ends of the rotors of an induction motor has been automated by developing a module in this study. While using the non-automated module, the industry workers who were engaged in brazing the rotors were exposed to high heat. They also showed early symptoms of physical fatigue due to manual handling of the rotors. Hence a need arises to automate the existing brazing process. Two models namely Conceptual Design 1 and Conceptual Design 2 have been developed in this study. It takes 215 seconds for completing brazing operations on both sides of a rotor upon using Conceptual Design 1 whereas the cycle time for Conceptual Design 2 is 231 seconds. Though the Conceptual Design 2 takes longer time to complete brazing on each rotor, it is sturdier and the sub assembly of indexing table is better balanced. Brazing and subsequent cooling consumes most of the cycle time, and hence steps have to be taken to improve these two operations to reduce the overall cycle time of the module for further improving the developed model.
REFERENCES
-
Dragomir Niklaev Grozdanov and Nikolay Lyuboslavov Hinov, Industrial application of induction brazing ystesms, Proceedings of
XXV International Scientific Conference Electronics – ET2016, Sozopol, Bulgaria, September 12 – 14, 2016.
-
Yankang Tian, Libo Wang, Gerald Anyasodor, Zhenhai Xu and Yi Qin, Heating schemes and process parameters of induction heating of aluminium sheets for hot stamping, Manufacturing Review, vol.6, No.17, 2019, pp.1-11.
-
Kramer et al., Sun safety at work Canada: a multiple case-study protocol to develop sun safety and heat protection programs and policies for outdoor workers, Implementation Science Vol.10, No.97, 2015, pp. 1-18.