
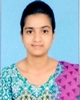
- Open Access
- Authors : S. Navaneetha , P. Venkata Ramana
- Paper ID : IJERTV10IS030104
- Volume & Issue : Volume 10, Issue 03 (March 2021)
- Published (First Online): 19-03-2021
- ISSN (Online) : 2278-0181
- Publisher Name : IJERT
- License:
This work is licensed under a Creative Commons Attribution 4.0 International License
Design and Fabrication of A Robot for Scrap Collection
S. Navaneetha, P. Venkata Ramana
Department of Mechanical Engineering (Mechatronics), Mahatma Gandhi Institute of Technology
Gandipet, Hyderabad-500075 Telangana, India.
Abstract:- With the rapid growing need of humans, robotics and automation play a vital role throughout the world. Earlier, communications were restricted to wired networks but as the technology stepped for further advancement wireless communication came into picture. Wireless communication first took place via Wi-Fi, Bluetooth, RF (Radio Frequency).
The primary task is to structure a programmed piece gathering robot which is designed to expel scraps from any territory with the assistance of sheet metal. The utilization of this mechanized robot framework lessens human endeavors and the odds of danger. This machine comprises of DC motors associated with metal sheet which can expel the wastage from floor. The robot is employed with DTMF (Dual Tone Multiple Frequency) which gives guidelines from portable. It utilizes IP camera for live gushing.
Microcontroller frames the controlling module and it is the core of the robot. The framework is put on surface. The robot moves in various bearings dependent on the guidelines given from telephone associated with DTMF in the robot area. DC Motor alongside the driver is interfaced to the microcontroller. The controlling gadget for the automated controlling in the venture is a Microcontroller. Microcontroller peruses the information from DTMF and chooses the course and works the DC motors associated with it in like manner. To play out this canny undertaking, Microcontroller is stacked with a program written in installed 'C' language.
-
INTRODUCTION
The main objective of this project is eliminating the need to manually collecting the scrap from different places. For the purpose, an automatic scrap collecting vehicles running automatically is designed. In the available methods of scrap collecting, manpower and fuel power vehicles are used. In this project, a battery-operated automatic scrap collecting robot with DTMF (Dual Tone Multi Frequency) signaling is developed. The battery used here is a rechargeable battery where it can be used multiple times by charging it when required.
The fundamental of the task is to plan an automatic scrap gathering robot which is manufactured to expel scraps from any zone with the assistance of sheet metal. The utilization of this computerized robot framework decreases human endeavors and the odds of peril. This machine comprises of simple H-bridge circuit which controls DC motor associated with a metal sheet which can expel the wastage from the surface. This undertaking utilizes DTMF (Dual
Tone Multi Frequency) correspondence to work the entire framework and it utilizes IP camera for live spilling. Conventionally wireless controlled robots use RF (Radio Frequency) circuits, which have drawbacks of limited working range and frequency range which can be overcome by using mobile phones.
Microcontroller forms the controlling module and it is the heart of the system. PIC16F72 Microcontroller with 28 pins is used. The robot moves in various ways depending on the guidelines given from the telephone associated with DTMF in the robot segment. This direction can be taken by the controller segment and it can work the motors. DC Motor alongside the driver is interfaced to the microcontroller. The controlling device for the automated controlling in the undertaking is a Microcontroller. Microcontroller pursues the information from DTMF and chooses the direction and works the DC motor associated with it in like manner. To perform this task undertaking, Microcontroller is stacked with a program written in embedded 'C' language.
-
LITERATURE REVIEW
The main aim of this work is to control the robot for collecting the scrap from different areas or surfaces automatically by monitoring and regulating the direction of a dc-motor with PIC16F72 Microcontroller remotely using mobile phone techniques and DTMF (Dual Tone Multi Frequency) signaling. Different functions of moving robot are controlled like moving forward, backward, left and right [1].
The aspect of the project is to build an actual robot that subjects wireless operation from a PC or a smartphone. The requirement of simplicity was set in order to focus on operability and functionality [2]. The cleanup is time consuming, and represents a potentially significant source of untapped recyclable materials. By developing an autonomous robot that can locate, sort, and separately store the different containers, the manpower needed for cleaning can be significantly reduced [3].
Vacuum cleaning system used in this robot is Cyclonic type filtration system which works under the principle of forced vortex flow same as in case of centrifugal pump. Centrifugal force will be created and all types of debris will be sucked in through pipe. The advantage of using this robot is saving in time, it will be very much useful for
people with mobility issues to clean the house without any difficulties [4]. The development of Autonomous Robot is divided into two main sections, the electronics design and mechanical design. The main component is PIC16F72microcontroller. The PIC16F72 can be programmed using the Pic Basic Pro compiler. The motor used is the Tamiya Twin-Motor Gearbox. The robot is equipped with the obstacle-avoidance ability which uses the infrared sensors. Then the robot can play pre-recorded messages. Those pre-recorded messages are stored in the Winbond ISD 2560 Chipcorder [5].
Mobile robotics is a relatively new research area that deals with the control of autonomous and semiautonomous vehicles. There are some important differences between the requirements of traditional fixed robotic installations and the requirements of mobile robotic systems. One of it is the environmental uncertainty in which the vehicle might operate in. For fixed robotic systems, a small workspace can usually be engineered to facilitate the task being undertaken. For mobile robotic systems, it is difficult to engineer the environment where the system needs to operate in because the world is dynamic and unpredictable. This required improved sensor technology and the ability for the system to cope with uncertainty. The design of mobile robotic systems considers the ability to carry all necessary resources such as power sources and all of the sensing and processing hardware within the mobile itself [6].
A tele remote is a remote control system which enables switching 'on' and 'off' of appliances through telephone lines. It can be used to switch appliances from any distance by just making a phone call. This system is designed to overcome the limitation of the range offered by infrared or wireless technology, by making use of the already available telephone lines, all over the world. The DTMF signals on telephone instrument are used as control signals. It decodes the DTMF tone from the keypad of telephone into its respective BCD code after the system receives the call. This BCD code is passed through a decoder which selects a particular D-flip flop. This activates a switching transistor, which in turn triggers the relay connected to the appliance [8-10].
-
PROBLEM STATEMENT
Collection of scrap from any surface or anywhere is being handled with human intervention in many places and companies throughout the world over past years which may be very hazardous or even danger for the mankind. As known, demand for automation is rising rapidly in recent times using the modern technologies, which also reduces the man power and risk-taking activities directly or indirectly. Complete automation is very complex; hence it can be performed using remote controls and network connections.
The current project is to reduce the time consumption and human risk while collecting the trash/scrap from a particular surface using a four wheeled robot with H-
Bridge circuit-controlled DC motors connected to a rotating sheet metal which collects the scrap together into one spot by following the directions given by the remote controls controlled with the microcontrollers. DTMF (Dual Tone Multi Frequency) based PIC16F72 microcontroller is used to control the directions and purpose of the robot in the required field. An IP camera is also used for live telecasting of the robot movement throughout the process.
-
DETAILS OF THE COMPONENTS
Figure 1: Block diagram of Scrap Collecting Robot
-
Microcontroller
A microcontroller is a programmable computerized processor with basic peripherals. Both microcontrollers and microprocessors are composite sequential digital circuits meant to carry out job affording to the program / commands. Sometimes analog input/output interface styles a part of microcontroller circuit of mixed mode (both analog and digital nature).
-
A smaller computer
-
On-chip RAM, ROM, I/O ports…
Sample: Motorolas 6811, Intels 8051, Zilogs Z8 and PIC 16X
Figure 2: Pin Diagram of PIC16F72 Microcontroller
-
-
Regulated Power Supply
A mechanism or systems that supply electrical or other sorts of energy to an output consignment or assembly of loads is called a power supply unit or PSU. The term is
typically practical to electrical energy supplies, less frequently to mechanical ones, and hardly to others. A power supply may comprise a power sharing system as well as primary or secondary bases of energy such as
-
Alteration of one form of electrical power to one more ideal form and voltage, classically linking converting AC line voltage to a well-regulated lower-voltage DC for electronic strategies. Small power, low power DC power supply units are typically included with the strategies they supply, such as processers and household electronics.
-
Batteries.
-
Chemical fuel cubicles and other method of energy storing systems.
-
Solar power.
-
Generators or alternators.
Figure 3: Block diagram of Regulated Power Supply
-
-
LED (Light Emitting Diode)
A light-emitting diode (LED) is a semiconductor luminosity foundation. LEDs are castoff as pointer lights in numerous strategies, and are ever more castoff for lighting. Launched as a useful electronic component in 1962, near the commencement LEDs emitted low- intensity red light, but recent images are accessible across the visible, ultraviolet and infrared wavelengths, with particularly high intensity.
The influence of a DC motor is current/voltage and its manufacture is torque (speed).
Figure 5: DC Motor
-
DC Motor Driver
The L293 and L293D stand quadruple high-current half-H drivers. The L293 is intended to run bidirectional drive currents of up to 1 A at voltages from 4.5 V to 36 V. The L293D is considered to afford bidirectional drive currents of up to 600-mA at voltages from 4.5 V to 36 V. Similarly, gadgets are intended to drive inductive loads, for example, transfers, solenoids, dc, and bipolar venturing engines, just as extra high-current/high-voltage tons in the positive- supply application.
Figure 6: Motor driver L293D IC
-
IP (Internet Protocol) Camera
An Internet Protocol camera, or IP camera, is a sort of computerized camcorder that gets switch data and coordinates picture information by means of the Internet. They are commonly utilized for examination. Unlike analog closed-circuit television (CCTV) cameras, they need no local recording device, but solitary a local area network. Maximum IP cameras are webcams, but the term IP camera or netcam frequently applies only to those castoffs for surveillance that can be unswervingly accessed over a network linking.
d) DC Motor
Figure 4: Parts of LED
A DC motor customs electrical energy to fabricate mechanical energy, very characteristically through the interface of magnetic fields and current- carrying conductors. The overturn technique, making electrical energy from mechanical energy, is talented by an alternator, generator or dynamo. Numerous categories of electric motors can be scuttle as generators, and vice versa.
Figure 7: IP Camera
Some IP cameras need support of a central network video recorder (NVR) to knob the recording, video and alarm managing. Others are able to function in a devolved manner with no NVR required, as the camera is able to record unswervingly to any local or remote storing media. The primary centralized IP camera was Axis Neteye 200, unconfined in 1996 by Axis Communications.
g) Battery
A rechargeable battery, storing battery, or accumulator is a type of electrical battery. It includes one or extra electrochemical cells and is a category of energy accumulator. It is known as a secondary cell because its electrochemical reactions are electrically revocable. Rechargeable batteries come in many dissimilar shapes and sizes, ranging from button to megawatt systems associated to steady an electrical circulation network. Numerous dissimilar combinations of chemicals are usually used, including acid, nickel (NiCd), nickel metal hydride (NiMH), lithium ion (Li-ion), and lithium ion polymer (Li- ion polymer).
Rechargeable batteries have the lower cost of use and environmental effect than nonrefundable batteries. Some rechargeable battery categories are accessible in the same sizes as disposable types. Rechargeable batteries have a higher initial cost but can be recharged very cheaply and used many times.
-
PROJECT DESIGN AND WORKING DESCRIPTION
Figure 8: Project Design
Figure 8 shows the project design and components of the microcontroller-based robot. The important components of this robot are DTMF decoder, PIC17F2 Microcontroller and motor driver. DC Motors controlled by the motor driver is connected to a rotating shaft of sheet metal. A rechargeable Internet Protocol (IP) Camera is used for live streaming of the robot. The Microcontroller is associated
with crystal oscillator, controlled power supply, resistors and motor drivers.
Figure 9: Schematic layout of scarp collecting robot
Figure 9 shows the schematic diagram and interfacing of PICF72 Microcontroller with each module.
-
Working Description
In this project, the robot is controlled by a mobile phone which makes call to the mobile phone attached to the robot. During the call duration, if any button is pressed, a tone corresponding to the button pressed is heard at the other end of the call. This tone is called Dual Tone Multi Frequency (DTMF). The robot receives this DTMF tone with the help of phone stacked in the robot.
The received tone is processed by the PIC16F72 Microcontroller with the help of DTMF decoder which decodes the tone to its equivalents binary digit and this binary number is send to the microcontroller. The microcontroller is preprogrammed to take a decision for any given input and outputs decision to motor drivers in order to drive the motors for forward or backward motion or a turn.
This robotic project does not require the construction of receiver and transmit unit as the mobile phone that makes call to the mobile phone stacked in the robot acts as a remote. Following the directions from the DTMF, the micro controller insists the motor driver to drive the DC Motor connected to the power supply which moves the 4 wheeled robot with rotating shaft with sheet metal collecting the scrap from the surfaces into one spot. The robot can perform actions like moving forward, bacwards, left, right and stop.
In DTMF there are 16 distinct tones. Each tone is the quantity of two frequencies: one from a low and one from a high-frequency group. There are four dissimilar frequencies in each collection.
The mobile phone only uses 12 of the conceivable 16 tones. There are only 4 rows (R1, R2, R3, nd R4) and 3
columns (C1, C2, and C3). The rows and columns choice frequencies from the low and high-frequency group respectively. The exact standards of the frequencies are listed below:
Figure 10: DTMF keypad
Thus, to decipher what tone frequency is related with a particular key, individual key is stated by its row and column locations. For example, the "2" key is row 0 (R1) and column 1 (C2) Thus by means of the above table, "2" has a frequency of 770 + 1336 = 2106 Hz the "9" is row 2 (R3) and column 2 (C3) besides has a frequency of 852 + 1477 = 2329 Hz.
The subsequent graph is an apprehended screen from an oscilloscope. It is a plan of the tone frequency for the "1" key. You can see that the DTMF created signal is very distinct and clear. The horizontal axis is in examples. The frequency of the tone is about 1900 Hz – close to the 1906 Hz.
Tone Generator
The DTMF generator circuit is straight advancing to the idea. Just 3 of the 5089's 4 segment pins (3,4,5) and each of the 4-push pins (11 to 14) were utilized. In this way, it utilizes just 12 of the 16 contact tones (simply like your telephone). In this representation, you'll note the "/" in front of column and row pin labels (e.g. /C1). This means that these pins are dynamic low.
In other words, a pin is permitted when it is grounded. When the circuit is power-driven on, these pins normally high (+5V) C1-C3 and R1-R4 are wired to an 8-position DIP switch. In a single package, this DIP comprises 8 single-pole-single-throw (SPST) changes. It is abundant cheaper to use than 8 real SPST switches. You slide a DIP location to uncluttered or adjacent its switch. At the point when shut that particular switch connects its connected section or column stick to ground and makes it dynamic.
Tone Decoder
The decoder circuit is also informal to construct. You will have to physically wire (by means of alligator clips for instance) the TONE OUT pin out from the originator to the TONE IN pin out of the interpreter.
When actually wired together, the 7-segment display will light up the number allied with the touch-tone you trigger with the DIP switch.
Figure 11: Tone decoder circuit
General Description
The HT8870 series are Twofold Tone Multi-Frequency (DTMF) receivers integrated with digital interpreter and band divided filter purposes. The HT8870B and HT8870D categories supply power-down mode and inhibit mode processes. All types of the HT8870 series usage digital counting methods to perceive and decode all the 16 DTMF tone pairs into a 4-bit code output. Highly precise substituted capacitor filter is working to divide tone (DTMF) signals into low and high group signals. A built-in dial tone refusal circuit is providing to eradicate the necessity for pre-filtering.
-
-
RESULTS
In this system, a proto type model of Automatic Scrap Collecting Robot is designed using PIC16F72 Microcontroller which is functioned using DTMF signaling. These signals act as remote controls for performing the robot actions like moving forward, backwards, right, left and stop. This DTMF decodes the program stacked in the microcontroller and runs the program. Accordingly, the driver-controlled DC Motors associated with the rotating sheet metal starts functioning and collects the scrap. Wide range of control is possible even from a far away distance as IP camera is also used. The use of this automated robot system decreases human efforts and the chances of hazard.
-
CONCLUSION
Automation represents one of the major trends of the 20th century. The drive to provide increased levels of control to electro-mechanical systems, and with it a corresponding distancing of the human from direct system control, has grown out of the belief that automated systems provide superior reliability, improved performance and reduced costs for the performance of many functions. Through the auspices of the technological imperative, automation has steadily advanced as means have been found for automating physical, perceptual, and, more recently, cognitive tasks in all kinds of systems.
Coordinating features of all the equipment segments utilized have been created in it. Nearness of each module has been contemplated out and put cautiously, in this manner adding to the best working of the unit. Also, utilizing exceptionally propelled IC's with the assistance of developing innovation, the undertaking has been effectively executed.
ACKNOWLEDGEMENT
The authors thank the management of Mahatma Gandhi Institute of Technology, Hyderabad for the support in carrying out this project.
REFERENCES
-
Rohidas Waykole, Vedang Pujari, Ajay Powar and Umakant Patil (2018) Electromagnetic Scrap Collecting Machine with Vacuum System, International Research Journal of Engineering and Technology (IRJET) Vol.5 (5).
-
Kazacos Winter, J. (2013). Android controlled mobile robot| (Master's thesis).
-
Nayak, S., Hood, B., Allen, O., Foskey, C., Stevens, R., Kallal, E. & Schwartz, E. M. (2009). TailGator: Design and Development of Autonomous Trash collecting Robot. In Florida conference on recent advances in robotics (pp. 1-12).
-
Shah, A., Pant, M., & Karamchandani, S. (2019, March). Unsupervised Maneuvering Robot for Scouring Application. In 2019 IEEE 5th International Conference for Convergence in Technology (I2CT) (pp. 1-5). IEEE.
-
Kee, G. M., Zain, Z. M., & Salimin, R. H. (2008, September). Design and Development PIC-Based Autonomous Robot. In 2008 IEEE Conference on Robotics, Automation and Mechatronics (pp. 1-5). IEEE.
-
Kee, G. M., Zain, Z. M., & Salimin, R. H. (2008, September). Design and Development PIC-Based Autonomous Robot. In 2008 IEEE Conference on Robotics, Automation and Mechatronics (pp. 1-5). IEEE.
-
Sharma, R., Kumar, K., & Vig, S. (2006, December). DTMF based remote control system. In 2006 IEEE International Conference on Industrial Technology (pp. 2380-2383). IEEE.
-
Luo, R. C., Chen, T. M., & Yih, C. C. (2000, December). Intelligent autonomous mobile robot control through the Internet. In ISIE'2000. Proceedings of the 2000 IEEE International Symposium on Industrial Electronics (Cat. No. 00TH8543) (Vol. 1, pp. PL6-P11). IEEE.
-
Sudip Das, Satadal Mal, Snehasish Pal, Debangshu Das (2013) An Approach for Automatic Generation Control by Stepper Motor Using With PIC16F72 MicrocontrollerInternational Journal of Advanced Research in Electrical, Electronics and Instrumentation Engineering Vol. 2 (12).
-
Agarwal, R., Sudhakar, R., & Agrawal, B. (1984). Multiplierless implementations of MF/DTMF receivers. IEEE transactions on communications, 32(7), 839-847.
-