
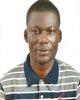
- Open Access
- Authors : Akande Stephen Oluwashola , Taiwo Victor Olamide
- Paper ID : IJERTV11IS060191
- Volume & Issue : Volume 11, Issue 06 (June 2022)
- Published (First Online): 25-06-2022
- ISSN (Online) : 2278-0181
- Publisher Name : IJERT
- License:
This work is licensed under a Creative Commons Attribution 4.0 International License
Design and Fabrication of Pedal-Powered Air Compressor
Akande Stephen Oluwashola1 Department of Mechanical Engineering Kogi State Polytechnic,
Lokoja, Nigeria
Taiwo Victor Olamide2
Department of Mechanical Engineering Kogi State Polytechnic,
Lokoja, Nigeria
Abstract Compressed air is an important medium for the transfer of energy in industrial processes, inflation of automobile tires and is used in pneumatic machines, and power tools such as drills, air hammers, and wrenches among others. Air is compressed by an air compressor. The compression process is normally powered by electric and fossil fuel motors. However, because of the increasing cost of fuel and electricity, there is a need to adopt a low-cost alternative power source for powering the compressor. The reduction in the use of fossil fuels will lead to a reduction in the carbon footprint of a nation. This paper describes the design, fabrication, and testing of a pedal- powered air compressor. The fabricated compressor does not use electric and fossil fuel motors as a source of power. Standard components such as chain, sprocket, pressure gauge, pneumatic pump, pressure hose, bicycle, and mild steel sheets were sourced from local shops. The supporting frames of the machine were made from mild steel sheets and pipes. Various parts were then assembled and joined by bolting and electric arc welding before painting to improve the aesthetic. The pedal-operated mechanism generates pressure for the receiver storage tank at the rate of 1925.675 Pa/s. The machine is easy to operate and inexpensive to fabricate as it cost forty-seven thousand seven hundred and fifty naira ($115). The generated pressurized air can be used in many applications such as inflating tires, paint sprayers, and flushing dust from generators and automobile air cleaners among others.
Keywords air compressor, pump, gear ratio, torque ratio, pedal-operated, pressure gauge
-
INTRODUCTION
Compressed air is the air that is pressurized to greater than atmospheric pressure. Compressed air is used around us in everyday life. It can be in the form of blowing air and is used in producing many things that we use. Compressed air is an important medium for the transfer of energy in industrial processes, and inflation of automobile tires and is used in pneumatic machines, and power tools such as drills, air hammers, and wrenches among others. It can also be used in the atomization of paint, automatic control, and propelling of vehicles. Compressed air is safe to use, easy to store, and has many versatile uses.
Usually, the air is compressed by an air compressor. The compressor draws in air through the inlet valve, the air is then compressed to the required volume before releasing the pressurized air through the discharge valve into a storage tank. There are two types of air displacement upon which a compressed air system may operate; these are positive displacement and dynamic displacement. A positive displacement compressor forces air into a confined space and
reduces the volume of the captured air by the movement of a mechanical device, unlike dynamic displacement compressors which speed up air to high velocity thereby building up air pressure. The compression process is normally powered by electric and fossil fuel motors. However, because of the increasing cost of fuel and electricity, there is a need to adopt a low-cost alternative power source for powering the compressor. There is also a need to reduce carbon footprint by reducing the use of fossil fuels in power generation as they are none renewable [1].
Pedal power is simple, efficient, and practical. Its most familiar use is the bicycle for personal or cargo transportation. But pedals can also power small stationary machines. A person can generate four times by pedaling than by hand-cranking with far less effort and fatigue [2]. Pedaling will therefore be adapted to power the proposed compressor in this research.
-
LITERATURE REVIEW
The pedal-operated cloth washing machine was worked on by some researchers [3, 4]. It was opined that washing is one of the essential parts of life but it is considered undesirable because of the involvement of the effort, time, energy, and cost which the fabricated machine addressed.
Rao and Naidu [5]designed and constructed a pedal- operated water pump that will be used in small-scale irrigation. The pump stand includes housing, in which a pedal and a rotating drive shaft were attached; it works on the principle of compression and sudden release of a tube by creating negative pressure in the tube. This vacuum draws water from the sump.
Akande and Mercy [6] designed and constructed a pedal-powered grinding mill. The machine chain drive mechanism is made up of sprockets, gear, pedal, chain, bearing, grinding disc shaft, and hopper for receiving the product to be milled. The pedal is used for generating torque for rotating the shaft and the grinding disc, this machine was designed as a low-cost solution for either no or inadequate electricity power supply from the public electricity distribution company in the rural area and some urban centers of Nigeria and other developing countries.
Subash, Meenakshi [7] did work on pedal-operated hacksaw machines which can be used for industrial applications and Household needs in which no specific input energy or power
is needed. This project consists of a crank and slider mechanism. In this mechanism, a pedal is directly connected to the hacksaw through a crank and slider mechanism to cut the wooden blocks, metal bars, and PVC materials.
Due to the rising cost of fuel, non-availability of gas stations in some rural areas, and climate warming as a result of the burning of fossil fuels there is a need to reduce carbon footprint by using a machine that does not use fossil fuels as a source of energy for powering the machine. Moreover, long- term dependency on fossil fuels raised issues such as pollution and global warming due to the amount of greenhouse gas emissions.
An alternative source of energy to power machine such as an air compressor for the purposes of inflating tires, atomizing of paint for applying aesthetic finishing to manufactured parts and other purposes where compressed air may be needed therefore exist. This research aims to design and fabricate a pedal-operated air compressor.
Figure3.1: Sprockets and chain
Eq.2
Where V.R velocity ratio
N2 = number of teeth on the driven sprocket, N1= number of teeth on the driver sprocket, n1= speed of driver sprocket (crank) in rpm, n2 = speed of driven sprocket (rpm), T2= torque of the driven sprocket (N-m), T1 = torque of the driver (N-m).
-
METHODOLOGY
-
Materials and Methods
The components that were used for the fabrication are presented in Table 1
Table 1 Materials for the fabrication
The driving sprocket pitch angle () is:
Thus, the chains pitch can be calculated as follows:
Where: P pitch; D Pitch circle diameter in meters The chains average velocity (v)
Eq.3
Eq. 4 Eq.5
S/n
Components
Description
Quantity
Materials
1
Bicycle frame
The major
component of the project
1
Steel
2
Sprocket
Driven sprocket Driver sprocket
2
2
Steel
3
Chain
Chain use / length Horizontal chain 48.6mm
Vertical chain 518.16mm
2
Stainless steel
4
Bearing
Roller bearing
1
Chrome steel
5
Cylinder
Air storage
1
Mild steel
6
Rotating disc/crank
Couple to sprocket for torque
transmission
1
Steel
7
Pressure gauge
To measure the air pressure
2
steel
8
Pneumatic pump
Compresses air
1
Steel
= Eq.6
C. Length of chain and center distance
To determine the length of the chain in a chain drive (see Figure 3.2).
Let, p = pitch of the chain, and x = centre distance
The length of the chain (L) is equal to the product of the number of chain links (K) and the pitch of the chain (p). Mathematically,
Eq.7
-
Design calculations
Sprocket/Gear ratio
The gear ratio or velocity ratio (V.R) is the ratio of the number of teeth of the driven gear and driver gear. It is also the mathematical representation of the mechanical advantage of a gear train system (see Figure3.1). It shows the change in speed between the sprocket of the pedal and the sprocket that is attached to the compressor gear.
Eq.1
Figure 3.2 Length of chain
The number of chain links may be obtained from the following expression, i.e.
Eq.8
The value of K obtained from the above expression must be approximated to the nearest even number. The center distance is given by:
Eq.9
Torque, T = Eq.10
Eq. 11 Eq.12
The average power produced by a healthy non- athlete man is from 30 W to 60 W and 50 rev/min was also recommended for daylong pedaling work [8]. This research will make use of 50 rev/min and 60 W.
The arrangement of the gear and chains in the machine is shown in Figure 3
Where, N3 and n3 are the numbers of teeth of driven sprocket 2 and the speed of driven sprocket 3 respectively
-
Storage volume of compressed air
The storage volume for compressed air can be determined using Boyle's Law [3]
Eq. 13
Pa = atmospheric pressure (N/m2); Va = volume of the gas at atmospheric pressure (m3)
Pc = compressed pressure (N/m2); Vc = volume of the air at compressed pressure (m3)
Driven gear 2
Driven gear 1
Vertical chain arrangement
Horizontal chain arrangement
The volume of free air in a storage volume
The amount of free air at atmospheric pressure in a given volume as cylinder storage can be calculated by, Va = Pc Vc / Ps
Rate of pressure increase = Total pressure/Time taken
-
Time measurement
Driver gear Time taken was measured using a stopwatch. Tests were carried out three times to determine when pressures in the pneumatic pump and receiver tank will rise from zero to a new value within an hour.
-
-
FABRICATION, ASSEMBLING OF
Figure 3 Power transmissions arrangement for the machine
Consider the speed of the pedal which is given as 50 rpm, therefore the speed of the sprocket driver is 50 rpm = n1 For horizontal torque transmission
Gear ratio or sprocket ratio = N2/N1= 18/46 = 0.391
The speed of the driven sprocket 1 (n2) is given as
(a)
(b)
For vertical torque transmission
COMPONENTS, AND THE PRINCIPLE OF OPERATION
A fully built bicycle was purchased from a local store. The rear wheel was then removed to join the supporting frame of the compressor, storage tank, gears, and crank mechanism.
Figure 4 (a) Installing chain and shaft on support (b) machine undergoing painting
Figure 5 the Air compressor complete assembly
The frame was fabricated by cutting and welding the square hollow pipe (see Figure 4) to provide the needed support for the compressor, vertical chain drive, and the crank mechanism that controls the reciprocating of the pump that produces the compressed air.
There are two chain drive mechanisms which are the horizontal and vertical drives mechanisms. The horizontal mechanism transmits torque from a driver gear to the driven gear at the rear of the wheel while the vertical mechanism transmits torque from the driven gear at the wheel to another vertically positioned driven gear, disk, and slider system that control the reciprocating motion of the pneumatic pump.
The pedaling by the user will lead to the compressor sucking in the air during the suction stroke; the air will then be compressed by reduction of the volume of the cylinder during the downward stroke of the plunger in the pneumatic pump as the slider and driven gear 2 mechanism are actuated. It is the slider that converts the rotary motion of the disc to the reciprocating motion of the compressor. The compressed air is then forced through an opening in the storage tank, where pressure builds up. The storage tank is fitted with a pressure gauge to monitor the pressure of the compressed air in the receiver tank (see Figure 5). The storage tank is also fitted with a delivery valve for the control of the usage of stored compressed air.
A. Construction cost analysis
Table 2 list of items with the cost implication
S/n
Component
Rate
Quantity
Total
1
Gear
N1000
4
N4000
2
Bicycle
N13,000
1
N13,000
3
square pipe
N3,500
2
N7,000
4
Cutting disc
N1,500
1
N1,500
5
Electrode
N700
½ pack
N700
6
Pneumatic pump
N2,500
1
N2,500
7
Sprocket
&chain
N3000
1
N3000
8
Hose
N750
3
N2,250
9
Cylinder
N1,500
1
N1,500
10
Gauge
N5000
1
N5000
11
Paint
N5000
1
N5000
12
Transportation
N3000
N3000
Total
N 47,750
-
RESULT AND DISCUSSION
-
Results
The result of the testing of the fabricated compressor is shown in as shown in Table 3. The pressure of the compressed air in the pneumatic pump and storage tank with the time taken in seconds to produce the compressed air is as presented.
Table 3 Pressure of the compressed air in the storage tank and pneumatic pump
S/N
pressure of compressed air in the pump (MPa)
pressure of compressed air in the tank (MPa)
Time spent for pump(sec)
Time spent for cylinder (sec)
1
0.196
0.095
52
48
2
0.196
0.095
54
51
3
0.196
0.095
53
49
Total
0.588
0.285
159
148
The rate of pressure increase for each case can be obtained by dividing the total pressure with time taken
The rate of increase of compressed air pressure in the cylinder is 1925.68 Pa/s while that in the pneumatic pump is
3698.11 Pa/s.
-
Discussion
From Table 2 the cost of fabrication of the compressor is forty-seven thousand, seven hundred and fifty naira only. The pedal-operated compressor will be affordable to most users for any application that required low to medium quantity compressed air. During the first trial after fabrication, the pressure generated in the pneumatic pump is 196,000 Pa in fifty-two seconds while that of the compressed air in the receiver storage tank is 95,000 Pa in forty-eight seconds. The pressure difference is due to the volume of the receiver storage tank, which is larger than that of the cylinder of the pneumatic pump as shown in Figure 5. The pressure increase rate for the cylinder is 1925.676 Pa/s and for the pneumatic pump is 3698.113 Pa/s when the compression system is operated by pedaling.
-
-
CONCLUSION
A pedal-powered air compressor has been designed, fabricated, and tested for producing compressed air. The compressor achieved a supply pressure of 95,000 Pa in forty-eight seconds of pedalling by humans. The pedal- operated mechanism generates pressure for the receiver storage tank at the rate of 1925.675 Pa/s. The use of human power eliminates the need for electricity or an internal combustion engine in powering the machine. The machine is easy to operate and inexpensive to fabricate. The produced pressurized air can be used in many applications such as inflating tires, paint sprayers, and flushing dust from generators and automobile air cleaners among others.
REFERENCES
[1] Biello, D., 10 solutions for climate change. Scientific American, 2007. 26. [2] Weir, A., The Dynapod: A Pedal Power Unit. 1980: Volunteers in Technical Assistance. [3] Bhatawadekar, G., et al., Design and fabrication of pedal powered washing machine. International Journal of Engineering Research and General Science, 2015. 3(1): p. 1307-1311. [4] Mushiri, T., T.J. Mugova, and C. Mbohwa. Design and fabrication of a pedal powered washing machine. in Proceedings of the International Conference on Industrial Engineering and Operations Management Bogota, Colombia. 2017. [5] Rao, P. and A.L. Naidu, Design and fabrication of pedal operator centrifugal pump. Open Journal of Technology & Engineering Disciplines (OJTED) Vol, 2015. 2: p. 25-39. [6] Akande, S.O. and A. Mercy. Design and Construction of a Pedal- Power Grinding mill. in Journal of Physics: Conference Series. 2019. IOP Publishing. [7] Subash, R., et al., Fabrication of pedal powered hacksaw using dual chain drive. International Journal of Engineering & Technology, 2014. 3(2): p. 220. [8] Tiwari, P., et al., Pedal power for occupational activities: Effect of power output and pedalling rate on physiological responses. International Journal of Industrial Ergonomics, 2011. 41(3): p. 261-267.