
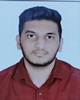
- Open Access
- Authors : Sanket Tukaram Tekade , Kaushik Kiran Dhomse , Varnit Ajay Kansara , Dr. Anand S. Relkar
- Paper ID : IJERTV11IS050251
- Volume & Issue : Volume 11, Issue 05 (May 2022)
- Published (First Online): 31-05-2022
- ISSN (Online) : 2278-0181
- Publisher Name : IJERT
- License:
This work is licensed under a Creative Commons Attribution 4.0 International License
Design and Fabrication of Portable Automatic Glass Wall Cleaner
Sanket Tukaram Tekade
Department of Mechanical Engineering SOET, Sandip University
Nashik, India
Kaushik Kiran Dhomse
Department of Mechanical Engineering SOET, Sandip University
Nashik, India
Varnit Ajay Kansara
Department of Mechanical Engineering SOET, Sandip University
Nashik, India
Dr. Anand S. Relkar
Professor, Department of Mechanical Engineering SOET, Sandip University
Nashik, India
Abstract The automatic machine plays every vital role in domestic life by overcoming human efforts in cleaning purposes, serving purpose etc. Today in modern period machines or robots are liable to perform surgery in hospital without wasting time in traveling of doctors and performing accurate function. The robots are also helping to catch ransacking peoples. In day to day life automated machines are making human life more comfortable than previous life. In this project the automatic cleaner will perform cleaning operation on window by climbing on it and going in scurry way. Todays machines performing these operation can be wired or wireless as per requirement from customer, there are many things that we should take care of it which will try to damage machine while it is in a function. The wall climbing cleaner should be light in weight and with high payload, reducing excessive adhesion and carrying instrumentation during navigation. According to locomotion type WCR are of three types: the crawler, the wheeled and the legged types. Based on the adhesion techniques it is classified into different types such as: Magnetic, Vacuum or Suction, Grasping Grippers, and the most modern adhesion technique based automated cleaner is biologically inspired robots. According to their works that has to be done they are made.
Keywords – Automatic, cleaner, robots, window, suction.
-
INTRODUCTION
There exists an increasing demand for the development of various service automatic machines to relieve human beings from hazardous jobs, such as cleaning glass surface of skyscrapers, fire rescue, mining etc. There have been many demands for automatic cleaning system on outside surface of buildings such as window glass by increasing of modern architectures. Some customized window cleaning machines have already been installed into the practical use in the field of building maintenance. However, almost of them are mounted on the building from the beginning and they need very expensive costs. Therefore, requirements for small, lightweight and portable window cleaning machine are also growing in the field of building maintenance.
As the results of surveying the requirements for the automatic window cleaner, the following points are necessary for providing the automated window cleaning machine for practical use:
-
It should be small size and lightweight for portability.
-
Sweep the windowpane continuously to prevent from making striped pattern on a windowpane.
-
Automatic operation during movement on the window.
-
Minimum time spent on cleaning of a surface with less cost as compare to other products that are available in the market.
The locomotion mechanism must be chosen to satisfy these demands, especially later two subjects. Here locomotion mechanism means the combination of traveling mechanism and a mechanism for changing a traveling direction. First requirement brought the following specifications for designing the automatic window cleaner. Weight: less than 5kg, including the weight of battery and washing water, Size: 700mm x 700mm. These were also defined by the results of surveying the demands from the cleaning companies. In previous researches, we have proposed outline of mechanical system for window cleaning machine for filling above mentioned demands. And we confirmed basic properties and its possibility by the experiments. Hence this mechanical system is based on a climbing robotic system aimed to clean glasses of high-rise buildings, using suction cups for adhering to the glass.
-
-
DESIGN OF AUTOMATIC GLASS WALL CLEANER All components designed using CAD package SolidWorks.
-
DC Motor
Motors are used for control of pulley which lead to effective control of the belt mechanism. DC Motors were used for the same. We used a DC motor RF500T 12560 for our project as shown in Fig.2.1. CAD Model of DC Motor Three-Digit Frame Number indicates an integral horsepower motor of 1 horsepower or greater. To calculate the D dimension, we divide the first two digits by 4. The D dimension of an RF500T 12560 frame motor is 50 divided by 4. As the D dimension increases, the physical diameter of the motor increases.
Fig.2.1 CAD Model of DC Motor
As the DC motor leads to precision rotations, it can be used for accurate movement control in case of Cleaning mechanism transverse and longitudinal feed.
-
Pulleys and Belt Transmission
Pulleys are used for transmission of torque from the motor to the belt such that the belt movement leads to the motion of the cleaning tool.
2.2.1 Timing Belt
A timing belt is typically rubber with high-tensile fibres (e.g. fiberglass or Twaron/Kevlar) running the length of the belt as tension members as shown in Fig.2.2.1 CAD Model of Timing Belt.
Specifications: Number of pulleys: 4 No. of Teeth: 20 Bore Diameter: 8mm
Body Diameter: 16mm Body Length: 16mm
-
Guide Bar
Vertical bars are used to support the transmission mechanism. These vertical bars act as guide ways for vertical and horizontal motion of the cleaning tool. The linear motion guideways provide a smooth and linear motion for the belt movement. The surface of guideways must have greater accuracy and surface finish. It ensures smooth movement and greater efficiency.
Fig.2.3 Vertical Guide Bars
Specifications :
Length: 700 mm
Diameter: 8 mm
Specifications:
Fig.2.2.1 CAD Model of Timing Belt
-
Slider
Sliders are used to move the cleaning tool along the two guideways. As shown in fig.2.4 the sliders consists of two parallelly drilled holes for the guide rods to pass through them.
Belt width: 6mm
Belt Length (Long): 142 cm Belt Length (Short): 132 cm Pitch: 2 mm
Tooth height: 0.76 cm Thickness: 1.52 cm
-
Timing Pulley
Timing pulleys are toothed pulleys which can accommodate timing belt fibres and create slip-free transmission as shown in Fig.2.2.2. Timing pulleys are specialized pulleys that have either teeth or pockets around the outside diameter of the pulley body.
Fig.2.2.2 CAD Model of Timing Pulley
Fig.2.4 Horizonatl and Vertical Slider Assembly
Components:
-
Rectangular slider with holes for guide bars and belt.
-
Bushes
-
-
-
ANALYSIS OF GUIDEWAYS
The simulation of guideways is carried out using Finite Element Analysis (FEA). It reduces the number of physical prototypes and experiments and optimizes the component in the design phase itself to develop a sustainable product.
The total deformation of the guideways was calculated by applying a force at the center of guide bars.
Fig.3 Bending Analysis of Guideways
The analysis gave us the results of the deflection at various points on the guide bars and the point of maximum deflection was obtained as shown in fig.3 bending analysis of guideways. A force of 5kg weight was applied at the center of the guide bars and the plot of defrmation was observed as above.
The maximum deflection was observed at the center having a value of 0.023123mm.
-
PNEUMATIC EQUIPMENTS
-
Directional Control Valve
It is a 5/2 DCV. As shown in fig.4.1 valve is a device that regulates the flow of fluid (gases, liquids, fluidized solids, or slurries) by opening and closing or partially obstructing passage ways.
Fig.4.1. 5/2 Directional Control Valve
A 5/2 way directional valve from the name itself has 5 ports equally spaced and 2 flow positions. It can be used to isolate and simultaneously bypass a passage way for the fluid which for example should retract or extend a double acting cylinder. There are variety of ways to have this valve actuated. A solenoid valve is commonly used, a lever can be manually twist or pinch to actuate the valve, an internal or external hydraulic or pneumatic pilot to move the shaft inside, sometimes with a spring return on the other end so it will go back to its original position when pressure is gone, or a combination of any of the mention above.
Specifications:
-
Techno pneumatic model 4v210-08
-
Pressure: 0.15-0.8 MPa
-
-
Vacuum Generator/Suction Generator
Vacuum generators provide the required vacuum. The vacuum is generated either pneumatically (ejectors) or electrically (pumps, blowers). Pneumatic vacuum generators as shown in fig.4.2 implement short cycle times and can be integrated directly into the system due to their compact and lightweight design. Ejectors offer intelligent functions for energy and process control.
Fig. 4.2 Vacuum Generator
Electrical vacuum generators are used in applications when compressed air is not available or if very high suction capacities are required.
-
-
ELECTRONIC EQUIPMENTS
-
Arduino UNO
The Arduino UNO is an open-source microcontroller board based on the Microchip ATmega328P microcontroller and developed by Arduino.cc. As shown in fig.5.1 the board is equipped with sets of digital and analogue input/output (I/O) pins that may be interfaced to various expansion boards (shields) and other circuits.
Fig.5.1 Arduino UNO
The board has 14 Digital pins, 6 Analog pins, and programmable with the Arduino IDE (Integrated Development Environment) via a type B USB cable.
-
Relays
Relays are the primary protection as well as switching devices in most of the control processes or equipment. All the relays respond to one or more electrical quantities like voltage or current such that they open or close the contacts or circuits. A relay is a switching device as it works to isolate or change the state of an electric circuit from one state to another.
Fig.5.2 2-Channel Relay
Specifications of Relay
-
Tongling (jqc-3ff-s-z)
-
Operating voltage 5V
-
-
-
CALCULATIONS
-
Motor calculations
-
Total load of the system is around 5 kg.
-
Therefore, we select motor of torque for weight of higher than 5 kg
-
Standard selection of motor according to requirement,
-
Torque: 4.2 kg-cm
-
RPM: 30
-
Shaft diameter: 8mm
-
-
Belt Calculation
-
The total length of 1st link is 1400 mm.
-
The center distance (C.D) is kept 700mm as per our setup. Refer Fig.6.2 Assembly.
-
The shaft of the motor will be acting like a pulley
-
Taking large pulley diameter as 15 mm
-
Smaller pulley diameter as 15 mm
-
C.D as 700 mm
Fig.6.2 Assembly
Length of belt (L) = 2 + 2(1+2) + (2 1)24
Notations: C is center distance
2 is larger diameter
1 is smaller diameter
Therefore,
belt length = (2×70)+2(1.5+1.5)+(1.51.5)24×100
L = 142 cm
Belt speed = 60
= ×1.5×3060
V = 2.35 m/min
-
-
Selction of Vacuum Cup Diameter
A graph is referred for considering the cup diameter which is provided below.
It is based on the body weight of the model which has to be sustained.
The robot is backed on the divider with a vacuum glass. There is a weight contrast between within the container and outside. This weight contrast delivers the power which holds the container and thus cleaner on the divider.
The power is given as: Pat Pin = F/A where,
Pat Atmospheric Pressure
Pin Pressure inside Vacuum Cup A Area of Vacuum Cup
= (Pat Pin)
The force which does not let the cup slide on wall is frictional
force.
=
Where,
F Reaction Force R Frictional Force
µ Coefficient of Friction between Pad and Wall
The forces acting on the Cleaner are shown in a free body diagram below :
Fig.6.3 FBD of Cleaner
= µ = µ(Pat Pin)
= W ()
=
= µ(Pat Pin)
= µ(Pat Pin) /
where,
W Weight of Robot
Angle of Inclination
As the wall is vertical, =90o
Therefore, R=W
Therefore, W= µF W= µ (Pat Pin)
W=
Where d is suction cup diameter
Now, weight to be carried W= 5 9.81 = 49.05 N
Fig.6.3.1 Graph of Load Bearing Capacity v/s Suction Cup Diameter
From graph for 5 kg load, Diameter d=30 mm
Now for glass rubber interface µ=0.5 Therefore, 49.05 = Considering FOS as 2,
= Pin = -0.1762 MPa
Which means, a negative pressure i.e. suction pressure needs to be given to the suction cups.
Presently the separation of focus of gravity from the glasses differs. The containers beneath the focal point of gravity obliges less compel than the mugs over the middle of gravity to keep the robot joined to the divider.
+F1d1 + F2d2+ F3d3 + F4d4 =
= ( F1d1 + F2d2+ F3d3 + F4d4)
Where, d1, d2, d3, d4 are the distance from center of gravity to
the center of the respective vacuum cups.
Suppose that the distance of cups from center of gravity is same then the above equation becomes the following equation.
= (F1 + F2 + F3 + F4)
The containers over the inside of gravity are at same stature
from focal point of gravity so the powers following up on these glasses can be included. Essentially powers following up on the containers underneath the focal point of gravity can be included.
Hence,
F1 = F2 F3 = F4 = ( F1 + F3) . Therefore,
5 9.81 h = – (2F1 + 2F3)30
From the above equation we choose appropriate suction cups by iterative method.
guide bars and this endplate is mounted on the end clamps using the nut bolts. One end of the end clamps holds the motor and the other end houses the suction cups.
Fig.7 CAD Assembly Model of Automatic Glass Wall Cleaner
Pneumatic System
The suction cups are provided at one end of the clamps. The suction hoses to these suction cups are joined through the suction generator which gets its input from the direction control valve. The direction control valve is controlled using the electronic system whose assembly is explained further. The assembly of all these systems is shown in the Fig.7 CAD Assembly Model of Automatic Glass Wall Cleaner.
VIII. WORKING OF MODEL
Translation System
Translation system deals with the employment of different adherence and translation mechanisms. This project employs use of suction cup and timing pulley and belt mechanism to move the tool as well as translate the mechanism to scale the span of the wall. The suction cups are controlled using the 5/2 DCV (Direction Control Valve) whose direction is controlled through the relay 5 which operates on pulse received from the Arduino board. Initially, the Arduino operates the relay 5 and gives signal to the pin 7 to switch on the DCV and creates suction for the suction cups mounted on the vertical slider assembly. Therefore, these sction cups adheres the vertical system to the wall and allow free movement of the horizontal assembly as shown in Fig.8.1 Actual working model mounted on glass.
In the second stage of translation, the horizontal slider assembly adheres to the wall using the other pair of suction cups. As the horizontal assembly has moved to a new position and adheres in a new position, the vertical assembly achieves translation of the whole mechanism. Thus, translation of mechanism is achieved by alternate movement of the slider assemblies.
Mechanical System
-
-
ASSEMBLY
The horizontal and vertical sliders will be joined using welding. The sliders are mounted such that the tool is attached to the vertical slider and the horizontal slider holds the vertical slider. LM8UU linear bearings are press fit in the holes provided. These linear bearings hold the vertical and horizontal guide bars. The end plate holds the ends of the
Fig.8.1 Actual Working Model Mounted on Glass
Fig.8.2 Actual Working Model
Cleaning Mechanism
Cleaning mechanism consists of a cleaning tool mounted on a tool holder as shown in Fig.8.2. cleaning mechanism of cleaner which is mounted on the slider assembly. The tool movement is achieved by moving the sliders first in vertical direction and then horizontal. The vertical motion of the sliders is achieved by the timing belt and pulley mechanism. The pulley is mounted on the DC motor. The Arduino board gives signals to the relay 1 and relay 2 to operate the motor 1 in clockwise direction. One end of the belt is fixed to the slider and hence the belt pulls the slider in vertically upward direction. This moves the tool vertically.
For movement of the tool in horizontal direction, the Arduino board stops the motor 1 using relays 1 and 2 and starts rotation of the motor 2 using relays 3 and 4. This moves the mechanism horizontally. This cycle is repeated until a rectangular space of the glass is cleaned.
Control System
The control system used for the automation of this project is the Arduino UNO control board. The Arduino UNO control board uses Atmega 328P as its microcontroller. The relays are operated using the control board. When board operates relay 1 and relay 2, it controls motion of motor 1. Similarly, when it operates relay 3 and relay 4, it controls rotation of motor 2. The board also controls the operation of the DCV using the relay 5. The Arduino IDE is user friendly software to load the code into the board. The code for the automation is as shown below. The explanation of each line in the code is written henceforth.
-
Arduino UNO Truth Table
TABLE I
Relay 1
Relay 2
Relay 3
Relay 4
Motor 1
Motor 2
1
0
1
1
Clockwise
Idle
0
1
1
1
Anticlockwise
Idle
1
1
1
0
Idle
Clockwise
1
1
0
1
Idle
Anticlockwise
ARDUINO UNO TRUTH TABLE
-
Arduino UNO Program const int relay1 = 3;//motor 1 const int relay2 = 4;//motor1
const int relay3 = 5;//motor 2 const int relay4 = 6; // motor2 int relay5 = 7; // dcv on off void setup()
{
Serial.begin(9600); pinMode(relay1, OUTPUT); pinMode(relay2, OUTPUT); pinMode(relay3, OUTPUT); pinMode(relay4, OUTPUT); pinMode(relay5, OUTPUT);
}
void loop()
{
digitalWrite(relay5, HIGH); delay(1000); digitalWrite(relay1, HIGH); digitalWrite(relay2, LOW); delay(20000); digitalWrite(relay1, HIGH); digitalWrite(relay2, HIGH); delay(1000); digitalWrite(relay1, LOW); digitalWrite(relay2, HIGH); delay(20000); digitalWrite(relay1, HIGH); digitalWrite(relay2, HIGH);
delay(2000);
IX.CONCLUSION
This report describes an application of small-size and light weight wall climbing machine for window cleaning. This project deals with overcoming a major drawback faced with most previously design systems. This window cleaning machine consists of timing belt and pulley mechanism, and two pairs of suction cups. Each pair operates alternately to provide clamping to vertical and horizontal guide bars. This enables the operation of vertical and horizontal motions in alternation leading to precise control. The area cleaned by the mechanism can be aggregated to be a rectangle, thus overcomes the disadvantage of failure of cleaning the corners.
This automated glass cleaner moves on the window smoothly with adhering by use of suction cups. Suction Cups provide adherence to the glass surface with minimum damage to it.
The automization of the cleaner will be achieved by controlling the system using the Arduino UNO Control board. The Arduino IDE provides a user friendly interface. A dual motor system is used to provide motion to the cleaning tool in horizontal and vertical directions which is further controlled by the relays through the Arduino control board. The automated cleaner scales the span of the glass walls by suction adhesion mechanism, thus overcomes the problem of translation faced by the previously developed cleaning systems.
Above mentioned automatic glass wall cleaner was prototyped and its mechanism and some of characteristics were illustrated. The components used in this work are simple
and cheap. The software programming is simple and can be modified and implemented easily. In general, the system works adequately as anticipated in the design process. The cleaning process takes about 2.5 minutes to finish a 1m2 glass window. This time depends on the speeds of the motors and the degree of dirtiness of the window. The automatic glass wall cleaner has been successfully designed and fabricated.
ACKNOWLEDGMENT
Gratitude is the hardest of emotion to express and often does not find adequate words to convey the entire one feels. It has been my good fortune to come so many good hardest people during my entire activity. Although it is as good as impossible to include the name of each of them here, I gratefully thank them for their invaluable help, precious time and guidance in making my project complete in all sense. Here I take opportunity to express my deep gratitude to project guide Dr. Anand S. Relkar who enthusiastically helped me a lot in various stages of my project. I sincerely thank my college for providing a platform where I could develop my project. Last but not the least I would like to thank all my friends who directly or indirectly contributed in my project work.
REFERENCES
[1] ALBAGUL*, A. ASSENI*, O. JOMAH**, M. OMER*, B. FARGE* *Control Engineering Department, The Higher Institute of Electronics, Baniwalid, Libya ** Faculty of Electrical, Engineering, Automatics, Computer Science and Electronics AGH University of Science and Technology, Poland. Design and Fabrication of an Automatic Window Cleaning Robot, 2019, (Page 208-212).
[2] Ori Barbut Supervisor: W.L. Cleghorn, Window Cleaning Robot, ASME Design Competition,2020, (Page 1-38) [3] Yanwei Liu, Shaoming Sun, Xuan Wu, Tao Mei, A Wheeled Wall Climbing Robot with Bio-Inspired Spine Mechanisms, Journal of Bionic Engineering, Volume 12, Issue 1, January 2015, Pages 17-28. [4] Pierluigi Rea, Erika Ottaviano., Design and development of an Inspection Robotic System for indoor applications, Robotics and Computer-Integrated Manufacturing, Volume 49, February 2018, Pages 59-75 [5] Luo Yiwen, Er Meng Joo, Ong Lok Ping Nanyang Technological University, Design and Development of a Glass Cleaning Robot., Fourth International Conference on Intelligent Systems Design and Engineering Applications, Singapore, 2013, (Page 225-218) [6] Thein Than Tun, Mohan Rajesh Elara, Manivannan Kalimuthu, Ayyalusami Vengadesh., Glass façade cleaning robot with passive suction cups and self-locking trapezoidal lead screw drive, 2019, (Page 180-188) [7] Houxiang Zhang and Jianwei Zhang TAMS, Department of Informatics University of Hamburg, Guanghua Zong Robotics Institute, School of Mechanical Engineering and Automation BeiHang University., Requirements of glass cleaning and development of climbing robot systems Conference: Intelligent Mechatronics and Automation,Proceedings, 2015, pp. 113-145
[8] Elias Matsas, George-Christopher Vosniakos, Dimitris Batras., Prototyping proactive and adaptive techniques for human- robot collaboration in manufacturing using virtual reality., Robotics and Computer-Integrated Manufacturing, Volume 50, April 2018, Pages 168-180.