
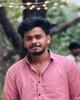
- Open Access
- Authors : Ms Rifa Ibrahim, Mr Shahir, Mr Muhammed Anshad T, Ms Salma Abdul Aziz Kormath, Mr Riyas P
- Paper ID : IJERTV14IS030069
- Volume & Issue : Volume 14, Issue 03 (March 2025)
- Published (First Online): 20-03-2025
- ISSN (Online) : 2278-0181
- Publisher Name : IJERT
- License:
This work is licensed under a Creative Commons Attribution 4.0 International License
Design and Fabrication of Portable CNC Laser Engraving Machine
Ms Rifa Ibrahim
Dept Of Electrical and Electronics Engineering
MEA Engineering College
Mr Shahir
Dept Of Electrical and Electronics Engineering
MEA Engineering College
Mr Muhammed Anshad T Dept Of Electrical and Electronics Engineering
MEA Engineering College
Ms Salma Abdul Aziz Kormath
Assistant Professor
Dept Of Electrical and Electronics Engineering MEA Engineering College
Mr Riyas P
Assistant Professor
Dept Of Electrical and Electronics Engineering MEA Engineering College
AbstractLaser engraving technology has gained significant attention due to its precision, efficiency, and versatility in various industries, including manufacturing, art, and personalization. However, conventional laser engraving machines are often bulky, expensive, and stationary, limiting their accessibility and usability for small-scale users and mobile applications. This paper presents the design and fabrication of a portable laser engraving machine, aimed at providing a compact, affordable, and user-friendly solution. The proposed system integrates a diode laser module, stepper motors for motion control, and an Arduino-based microcontroller running GRBL firmware for precise operation. The mechanical structure is designed using lightweight materials such as aluminum and acrylic, ensuring portability without compromising stability. The engraving process is controlled via USB or wireless connectivity, allowing seamless operation from a computer or smartphone. Performance tests demonstrate the machine's ability to engrave various materials, including wood, acrylic, and leather, with satisfactory accuracy and speed. This study highlights the feasibility of low-cost, portable laser engraving machines and discusses potential improvements in power efficiency, cooling mechanisms, and engraving precision.
-
INTRODUCTION
Laser engraving is a precise and widely used technique for marking, etching, and cutting various materials, with applications in industries such as manufacturing, arts, and product customization. However, most conventional laser engraving machines are bulky, expensive, and stationary, making them less accessible to hobbyists and small-scale users. To address these challenges, this project focuses on the design and fabrication of a portable laser engraving machine that is compact, affordable, and easy to use. The proposed machine features a 1-watt diode laser module, capable of engraving materials like wood, leather, and acrylic, making it suitable for small-scale applications. Unlike traditional metal- framed engravers, this machine has a wooden chassis, which ensures lightweight construction while maintaining adequate structural stability. The motion system is driven by stepper motors, controlled by an Arduino-based microcontroller running GRBL firmware, ensuring precise laser movement. The machine operates through a USB connection, allowing users to control it via software such as Laser GRBL or
LightBurn. The primary goal of this work is to develop a cost- effective and user-friendly engraving solution that can be easily fabricated and used by individuals and small businesses. This paper discusses the design considerations, fabrication process, and performance evaluation of the machine, highlighting its capabilities and potential improvements.
-
LITERATURE REVIEW
Laser engraving technology has seen significant advancements with the introduction of CNC-based control systems, open- source electronics, and portable fabrication techniques. Various researchers have explored different aspects of laser engraving machine design, focusing on hardware optimization, control algorithms, and material considerations. The following literature review presents an overview of key studies related to CNC-based laser engraving machines, open- source controllers, and portable fabrication techniques.
One study investigated the implementation of open- architecture control systems for CNC machines, leveraging open-source electronics to provide flexibility and modularity. The research emphasized how open-source control systems, such as Arduino and GRBL firmware, offer cost-effective solutions while maintaining customization capabilities. Another study introduced new interpretation modules for open-architecture CNC systems, enhancing tool path calculations and enabling precise motion control for engraving applications [1,6].
Several studies have focused on Arduino-controlled laser engraving machines, emphasizing affordability and ease of implementation. One study designed a CNC laser engraving system using Arduino Uno, demonstrating how GRBL firmware efficiently controls stepper motors and laser intensity. It highlighted the effectiveness of using an open- source platform to make CNC-based laser engraving more accessible. Another study developed a CNC laser engraver, optimizing the firmware to enhance motion precision and engraving resolution. The study compared different laser power levels, concluding that 1W to 5W diode lasers are suitable for engraving materials such as wood and acrylic [2,3].
Portability in laser engraving machines has been a growing area of research due to its practical applications for small businesses and personal use. Some studies explored the design and fabrication of portable laser cutting and engraving machines, focusing on chassis weight, stability, and material choice. They demonstrated that wooden and aluminum chassis provide a balance between weight, durability, and affordability, making them ideal for portable engraving systems. The studies also emphasized the importance of using compact stepper motors and lightweight components to ensure easy transportability [4,9].
Research on open-source CNC laser engravers has provided valuable insights into hardware and software optimization, including stepper motor tuning, GRBL firmware settings, and power management techniques. Findings suggest that DIY laser engravers offer a cost-effective alternative to commercial engraving machines while maintaining competitive engraving quality. Additionally, challenges related to power-efficient laser modules and extended operation without overheating were addressed [5].
Another study examined tool path computation in CNC-based laser engraving, showing how efficient tool path algorithms reduce engraving time while improving accuracy. It demonstrated how STEP-NC enabled CNC machines enhance precision and repeatability in laser engraving applications. Similarly, research on microstructure modifications in ceramic materials using laser engraving highlighted the importance of precise laser control in high-speed applications. The findings suggest that optimizing laser intensity and exposure time improves engraving quality on heat-sensitive materials [8,10]. Further research explored various design and fabrication techniques for laser engraving machines, analyzing motion control systems, laser power efficiency, and chassis durability. Studies compared the performance of different stepper motors and drivers, concluding that NEMA 17 stepper motors with A4988 drivers provide a good balance between cost and performance for small-scale engraving machines. The importance of proper cooling mechanisms for extended laser operation was also emphasized [7].
-
PROPOSED MODEL
-
Hardware Implementation
The portable laser engraving machine is designed with a wooden chassis, ensuring a lightweight, durable, and cost- effectie structure that supports the laser module and motion system while maintaining stability. It features a 1-watt diode laser operating at 450nm (blue laser), which is suitable for engraving materials like wood, leather, and acrylic, making it an ideal choice for hobbyists and small-scale users. To prevent overheating and ensure continuous operation, the laser module is equipped with a heat sink and cooling fan. The motion system consists of stepper motors with A4988 drivers, which provide precise control along the X and Y axes, allowing for accurate and high-quality engravings. A belt-driven mechanism ensures smooth movement, while limit switches define home positions and prevent over-travel, enhancing system reliability. The entire machine is controlled by an Arduino-based microcontroller running GRBL firmware, which processes G-code commands received from a connected
computer and translates them into motor movements, ensuring precise laser positioning. For communication and control, the machine relies on a USB interface, eliminating the need for wireless connectivity and ensuring stable, interference-free operation. Users can design engravings using software like Laser GRBL or Light Burn, which converts images or vector designs into G-code instructions for seamless execution. The power system includes a 12V DC power supply, with a buck converter regulating voltage to maintain stable operation. Safety features are integrated into the design, including a laser shield to minimize direct exposure to laser radiation, an emergency stop button for quick shutdown in case of system failure, and recommendations for protective eyewear and proper ventilation to enhance user safety. The combination of affordable materials, precise motion control, reliable power management, and essential safety measures makes this portable laser engraving machine a practical and efficient solution for engraving applications, offering an excellent balance of cost-effectiveness, functionality, and ease of use.
Fig.1 Block Diagram
The above block diagram (Fig 1) represents the hardware architecture of the portable laser engraving machine, detailing its major components and their interactions.
-
PC (Personal Computer)
The PC serves as the control interface, where the user designs the engraving pattern using software such as LaserGRBL or Light Burn. The software converts the design into G-code commands, which are then sent to the Arduino Uno via a USB connection.
-
Arduino Uno (Microcontroller Unit)
The Arduino Uno (Fig 2) is the core controller of the system. It processes G-code instructions received from the PC and controls the movement of the stepper motors as well as the laser module. It runs GRBL firmware, an open-source motion control software that interprets the G-code and generates precise motor control signals.
Fig 2. Arduino Uno
-
Stepper Motor Driver
The stepper motor driver (Fig 3) is responsible for controlling the two stepper motors, which drive the X and Y axes of the engraving machine. It regulates the current supplied to the motors, ensuring smooth and accurate motion for precise engraving.
-
Stepper Motors
Two stepper motors (Fig 3) are used to move the laser head along the X and Y axes. These motors provide high precision and repeatability, allowing detailed engraving patterns to be produced. The motors are connected to a belt-driven mechanism that facilitates smooth movement.
Fig 3. NEMA 17 stepper motor
-
Laser Control Board
Fig 4. CNC Shield v3
The laser control board (Fig 4) manages the power and modulation of the laser module. It receives control signals from the Arduino and adjusts the laser intensity, ON/OFF timing, and pulse width to achieve the desired engraving effect. This replaces the relay module, providing more precise and stable laser control.
-
Laser Module
The 1-watt diode laser module (Fig 5) performs the actual engraving process. It emits a focused high-energy laser beam that burns or vaporizes the materials surface, creating the desired design.
Fig 5. Laser module
Fig 6. Circuit Diagram.
Working Principle
The PC sends engraving commands in the form of G-code to the Arduino Uno, which processes these instructions and moves the stepper motors accordingly. The relay module controls the laser, ensuring it turns ON or OFF at the right moments to engrave the desired pattern. The motion system precisely guides the laser over the material, creating a high- accuracy engraving based on the provided design.
-
-
Software Implementation
The software implementation of the portable laser engraving machine involves firmware programming, motion control algorithms, and user interface development. The system is controlled using an Arduino Uno, which runs GRBL firmware, an open-source CNC controller designed for controlling stepper motors and laser modules. GRBL interprets G-code commands received from a computer and converts them into precise motor movements for engraving operations.
To operate the machine, G-code generation software such as Inkscape with the J-Tech Photonics plugin, LaserGRBL (Fig 7), or LightBurn is used to convert images or vector graphics into machine-readable G-code. The generated G-code is then transmitted to the Arduino Uno (Fig 8) via USB using LaserGRBL or Universal G-code Sender (UGS). These software tools allow users to adjust parameters such as engraving speed, laser power, and resolution before executing the engraving process.
The stepper motors, responsible for the X and Y-axis movements, are controlled using GRBL motion commands, ensuring precise positioning of the laser head. The laser control board regulates the laser's power and activation, turning it on and off based on the engraving pattern. The firmware settings, including $100, $101, and $102 parameters, are configured to calibrate the steps per millimeter for accurate motion control.
Fig 7. Laser GRBL Layout
During operation, real-time monitoring of the engraving process is possible through LaserGRBL's graphical interface, which provides visual feedback on progress. Error handling mechanisms in the firmware prevent overheating or misalignment, ensuring smooth operation. The system does not include wireless connectivity, so all commands and adjustments must be made through a wired USB connection. Overall, the software implementation focuses on efficient motion control, precise laser activation, and user-friendly operation. The integration of GRBL firmware with G-code generation software ensures that the engraving machine operates with high accuracy and smooth performance, making it an effective and affordable solution for laser engraving applications.
Fig 8. GRBL Program For Arduino
-
-
RESULTS AND DISCUSSIONS
The portable laser engraving machine was successfully designed, fabricated (Fig 9), and tested for engraving (Fig 10) various materials, including wood, acrylic, and cardboard. The system operated with high precision, achieving smooth and consistent engraving patterns based on the input G-code. The use of GRBL firmware with an Arduino Uno enabled efficient motion control, while the laser control board effectively regulated the lasers power, ensuring optimal engraving depth and clarity.
During testing, the stepper motors demonstrated accurate X-Y axis movement, allowing for detailed engravings without significant misalignment. The 1W laser module proved effective for engraving thin and moderately thick materials, though it required multiple passes for deeper engravings. The system's wooden chassis provided stability, but minor vibrations were observed at higher speeds, which could be improved with additional reinforcements.
The USB-based control system ensured reliable data transfer, though te lack of wireless connectivity limited flexibility. The machine successfully interpreted G-code instructions generated from LaserGRBL and Inkscape, producing engravings with minimal errors. However, variations in engraving quality were observed depending on material type, speed settings, and laser intensity.
Overall, the results indicate that this low-cost, Arduino-based laser engraving machine is suitable for small-scale engraving applications. Future improvements could include chassis reinforcement, a more powerful laser module, and advanced cooling mechanisms to enhance performance and durability.
Fig 9. CNC Laser Engraving Machine
Fig 10. Engraved Product
-
CONCLUSION
The design and fabrication of a portable laser engraving machine were successfully implemented using an Arduino Uno, GRBL firmware, stepper motors, and a 1W laser module. The system effectively performed precise engraving on materials like wood, acrylic, and cardboard, demonstrating accuracy and reliability. The wooden chassis provided a lightweight and cost-effective structure, though minor vibrations were observed at higher speeds. The integration of
GRBL-based motion control and a laser control board ensured smooth operation and consistent engraving quality.
Despite the absence of wireless connectivity, the USB-based control system allowed for stable communication and easy operation. The machine successfully processed G-code instructions from LaserGRBL and Inkscape, producing clear and well-defined engravings. However, improvements such as chassis reinforcement, a higher-power laser module, and better cooling mechanisms could further enhance performance.
Overall, this low-cost, Arduino-based laser engraving machine provides an efficient and accessible solution for small-scale engraving applications. With further refinements, it has the potential to be used for customization, hobby projects, and small business applications, making laser engraving more affordable and practical.
REFERENCES
-
Correa J, Toombs N, Ferreira PM. Implementation of an open- architecture control for CNC systems based on open- source electronics. Proceedings of the ASME 2016 IMECE 2016.
-
Mr. D. O. Shirsath et.al CNC Machine based on LASER Engraver using Arduino UNO IJSTE – International Journal of Science Technology & Engineering | Volume 3 | Issue 09 | March 2017 ISSN (online): 2349- 784X.
-
Jayaprasad V C et.al Design and Development of CNC Based Laser Engraver International Journal of Scientific & Engineering Research Volume 11, Issue 6, June-2020 ISSN 2229-5518.
-
P. Jamaleswara Kumar, M. Gowtham Design and fabrication of portable laser cutting and engraving machine International Journal of Engineering & Technology, 7 (1.1) (2018) 570-573.
-
Kamal Prasath Balaji et.al A Build-YourOwn Open Source CNC Laser Engraver Machine Version 2.0, December 2016
-
Yusri Yusof, et.al New Interpretation Module for Open Architecture Control based CNC Systems 12th global conference on sustainable manufacturing, Pocedia CIRP 26 (2015) 729- 734.
-
Ginna Vaishnavi et.al Design And Fabrication Of Laser Engraver International Research Journal of Engineering and Technology (IRJET) e- ISSN: 2395-0056 pISSN: 2395-0072 Volume: 07 Issue: 05 | May 2020.
-
S. Cuenca, et.al Hardware approach to tool path computation for STEP- NC enabled CNC: A case study of turning operations. Computers in Industry 62 (2011) 509518.
-
P. Thamma Rao et.al Design and fabrication of portable laser cutting and engraving machine International Journal of Engineering & Technology, 7 (1.1) (2018) 570-573.
-
T. Douillard et.al Microstructure And Hydrothermal Ageing Of Alumina-zirconia Composites Modified By Laser Engraving Journal of the European Ceramic Society Volume 40,Issue 5, May 2020, page 2077- 2089