
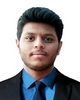
- Open Access
- Authors : Kshitij Kolhe , Omkar Ghanekar , Sharvari Jannawar , Pratik Dhane, Dr. D. M. Mate
- Paper ID : IJERTV11IS050140
- Volume & Issue : Volume 11, Issue 05 (May 2022)
- Published (First Online): 19-05-2022
- ISSN (Online) : 2278-0181
- Publisher Name : IJERT
- License:
This work is licensed under a Creative Commons Attribution 4.0 International License
Design and Fabrication of Rope Climbing Pick and Place Robot
Kshitij Kolhe
Department of Mechanical Engineering
JSPMs Rajarshi Shahu College of Engineering, Tathawade Pune, India
Sharvari Jannawar
Department of Mechanical Engineering
JSPMs Rajarshi Shahu College of Engineering, Tathawade Pune, India
Omkar Ghanekar
Department of Mechanical Engineering
JSPMs Rajarshi Shahu College of Engineering, Tathawade Pune, India
Pratik Dhane
Department of Mechanical Engineering
JSPMs Rajarshi Shahu College of Engineering, Tathawade Pune, India
Dr. D. M. Mate
Professor, Department of Mechanical Engineering JSPMs Rajarshi Shahu College of Engineering, Tathawade
Pune, India
Abstract With the advancement in mechatronics era the wireless communication will play a vital role in robotic applications. Throughout the history of robot development, most of the subjects are based on wheeled mobile robots and are moving on the floor. Here, a different kind of robot design i.e., rope climbing robot. In the past different engineers and researcher developed robots capable of climbing for various purposes. In this paper we have developed a robot capable of rope climbing in vertical direction and has ability to pick blocks with the help of aluminum jaws, the robot is capable of picking up objects. The Robot runs on Caterpillar Tracks which gives advantages like better floatation and smoother rides. The Robot is controlled manually with the help of 2.4 G Hz transmitter Receiver Pair. Hence the developed robot could be a good option for pick and place operations in warehouses.
Keywords Robotics, rope climbing mechanism, pick and place robot, Smartelex motor driver, FS-i6x, tri-pulley climbing mechanism, scissor based climbing mechanism, Johnson motor, lipo battery, wireless robot
-
INTRODUCTION
The objective here was to create a robot capable of climbing rigid or flexible elements such as ropes, pipes, etc. with the functionality to pick and place objects in correct space. The robot is to be controlled wirelessly by means of manual input via a transmitter. It has to be reliable and work effortlessly to achieve the users needs. In terms of application, a wiper mechanism can be mounted on the robot which can be used to clean surfaces. The developed robot could be a good option for pick and place operations in warehouses.
-
Receiver Flysky FS- iA10B
-
Power Source 1550mAh Li-Po 4 cell Battery
III. INITIAL DESIGN
Before beginning to design, many different designs were reviewed to select optimal type of mechanisms for the required purpose.
-
Pick and Place Mechanism
Assuming the weight to be carried will be below 0.5kg.
-
The object is grabbed with the help of gripper and lifted up using the arm collectively referred to as Pick and Place Mechanism.
-
To grab the object, we have used a two-finger claw driven by a 3-rpm plastic gearbox motor and interconnected with the help of 100 mm PCD Gear.
-
The arm is powered a 100-rpm Johnson motor with 103 N-cm torque.
-
The gripper fingers have small support fins at ends which helps to pick objects from a leveled floor and supports it adequately from below.
-
Lever Length (Arm): 195 mm
-
Finger Length: 155 mm
-
-
Robot Chassis
-
-
-
PARTS
-
End Effector Two finger Gripper
-
Robot Arm
-
Rope Climbing Mechanism
-
DC Motors Plastic gearbox motors, Johnson Motors
-
Motor driver SmartElex 15D Smart Motor Driver
-
Transmitter Flysky FS-i6X
Figure 1: Pick and Place Mechanism
-
Rope Climbing Mechanism
-
The rope is guided via a cavity made on the chassis into the Tri-Pulley locking mechanism.
-
There are small arms with bearings actuated by servos to guide and lock the position of rope as required during the motion.
-
Suitable positive locks have been added to these arms by use of servos and integrated design techniques.
-
The rope climbing mechanism consists of a movable arm actuated by 20 RPM DC Motor to squeeze the rope inside the Tri-Pulley locking mechanism.
-
The Tri-Pulley locking mechanism consists of three 200 RPM DC Motors. Two pulleys are placed on a vertical fixed plate and the third pulley on the movable arm.
Figure 2: Rope Climbing Mechanism
-
The rope is locked in place due to being sandwiched between these three pulleys.
-
Extra grips are provided on the wheels to ensure high friction during operation and avoid slippage.
-
-
Weight Distribution
-
As the bot hangs on a rope, weight distribution has to be optimized to maintain the orientation (pitch and roll) of the bot.
-
To throw the block, we need to swing the arm which requires space and is not possible in a centrally placed gripper.
-
Therefore, the gripper is placed in an offset position to the left which allows the arm to move freely as a result the center of gravity (CG) is shifted towards left.
-
To bring the CG as close to the climbing mechanism, weight needs to be added on the opposite side to counter the imbalance.
-
Hence, batteries are positioned in an offset position to the right.
-
On ground with zero payload, the bot is rear heavy but after lifting the block, the bot is fairly balanced in roll and pitch axes.
-
Robot weight (inclusive of batteries): 3.676kg
Figure 3: Top View of Robot
-
REVISED DESIGN
After the manufacture and testing of the initial design, some drawbacks were identified. They have been noted as follows:
-
Chassis not rigid enough.
-
Less controllability/ maneuverability due to absence of caterpillar tracks.
-
Side mounted gripper disturbs weight distribution of robot significantly during operation.
-
Climbing mechanism is not reliable and prone to failure.
-
Uncontrollable free rotation while hanging. Possible solutions for the listed drawbacks that were explored are as follows:
-
-
-
Designing a rigid chassis with I type cross section to avoid bending.
-
Designing climbing mechanism with better mechanical advantage and implement simplicity in design.
-
Implementing use of gyroscopic effect to control orientation of bot while hanging.
-
-
Pick and Place Mechanism
The older mechanism was heavy and placed with high amount of offset from its actuator, which caused bending the motor shaft (actuator). Due to the longer length of gripper fingers, and longer offset placement of arm, the work envelope of the robot had become significantly large, which increased the complexity of controlling the robot.
Figure 4: Revised Pick and Place Mechanism
-
Rope Climbing Mechanism
Previous mechanism consisted of three rollers with one attached on a arm actuated by a Johnson motor of speed 20 rpm and torque 328.3 N-cm. Due to very high requirement of torque and negligible mechanical advantage, the motor was prone to failure and made the climbing mechanism unreliable.
The new mechanism consists of scissor type mechanism actuated by a lead screw. This type of drive protects the motor in case of reverse torque.
Two long rollers with tapered surfaces as shown in the figure (figure 5) are used to sndwich two ropes at once to climb to reach in high up spaces. The use of two ropes facilitates the control of orientation while hanging by only allowing two positions 180o apart. This type of design is better than using gyroscopic effect as to implement such concept, the weight of the robot needs to increased significantly.
Figure 5: Revised Rope Climbing Mechanism
-
Chassis and Weight Disrtibution
Previous chassis used was of U cross section and was not able to appropriately support the weight of the robot. Due to this, the wheels moved outward due to a bending chassis and made it difficult to control the robot.
Figure 6: Revised Chassis
Figure 7: Tracked wheels and fender
The redesigned chassis has closed shape type cross section and hence is able to support the load by efficiently distributing the load in all parts of the chassis. This chassis also has been integrated with fenders used to keep the caterpillar tracks in place while in motion and also to act as a mounting surface for rope climbing mechanism.
Figure 8: Robot Top View
The complete redesign of chassis allowed for better suited placement of rope climbing mechanism, pick and place mechanism, control block and batteries. The pick and place mechanism could be moved forward resulting in shortening in the dimensions of gripper and providing with enough room for the placement of other components.
Figure 9: Revised design of robot
With the rope climbing mechanism on top, the space between chassis and rope climbing mechanism can used for control block which includes multiple motor driver PCBs and receiver. Additional space below the robot is also present and remains empty to add necessary circuitry in case of added functionalities explored later in this paper.
-
CONTROL AND ELECTRONICS
The robot is being controlled by wireless means by an operator. FS-i6X is a 10-channel transmitter that works on a frequency of 2.4 GHz. It has 2 joysticks with 2 channels each, out of which one joystick is used to control the robot in XY- plane. The other joystick is used to control the pick and place mechanism where one channel is used to elevate or lower the arm, while another channel is used to open and close the gripper.
It also has two 3-position switches, two 2-position switches and 2 potentiometers. The two 3-position switches are used to move the robot up and down while climbing rope and engaging/disengaging rope climbing mechanism respectively.
Figure 10: Transmitter FSi6X
The signals sent via the transmitter are received with help of Flysky FSiA10B receiver also operating on 2.4GHz frequency. Six channels out of ten have been used in this application which send signals to the motor driver.
Figure 11: Receiver FSiA10B
SmartElex 15D smart drivers are used to process the signals from the receiver and control the motors. One such PCB supports 2 such channels, hence three such boards are
used in combination to operate all of the motors present on the robot. This motor driver converts the PMM signal from receiver into PWM signal to control motors with high current consumption (up to 15A) by using MOSFETS. This type of control is energy efficient and creates less heat resulting in longer battery life and range of the robot.
Figure 12: SmartElex 15D
-
ESTIMATED COST OF PROJECT
This project involves the manufacture and testing of the robots. There are costs involved in procurement of material as well as processing/ machining costs, which are included with suitable assumptions.
Table 1: Estimated cost of project
Sr.
No.
Component Category
Description / Specification
Quantity
Price
1
Lead Screw
M6 Stud 20 cm Long
1
20
2
Lipo Battery
Ovionic 1550 mAh 4s 100c
2
4000
3
Motors
DC Johnson motors DC motors
4
1
1904
230
4
Motor Driver
SmartElex 15s,15D
3
5220
5
Aluminum Frame
160mm Wheel base
1
100
6
Flysky Transmitter And Receiver
Flysky FS-i6x Flysky FS-iA10B
2
2
9800
7
Switch
SPST
2
20
8
Gears
Plastic Spur Gears
2
200
9
Bearings
8*22*7 Rubber Sealed
4
100
10
Aluminum Rollers
2.5cm Diameter
2
200
11
Pulley Wheels
10cm Diameter
4
210
12
Velcro Straps
40cm Lipo Battery strap
Belt reusable cable tie
2
150
13
Fasteners and Miscellaneous Parts
M3, M4 nuts and bolts, Wooden parts, etc.
–
100
The cost estimate of such robot comes out to be roughly Rs.22254.00
-
APPLICATIONS
-
The robot is designed to be manually operated but if/ when integrated technologies such as Artificial Intelligence, Machine Learning and Internet of things it can be used more efficiently in every possible application without and need of human intervention.
-
By replacing the pick and place mechanism by window cleaning mechanism, the robot can be used to clean glass windows of high-rise buildings resulting reduction of exposure to danger for humans.
-
The mechanisms and chassis of this robot could be used individually to perform many tasks or build robots with different capabilities, for example, placement of a FPV camera as an end effector can create a robot with surveillance capabilities and the small size of robot can enable the robot to be used in tight spaces such as pipes for deep inspections.
-
The robot can be used as it is in direct line of sight environment, or with integration of smart technologies to manage inventory in ware houses and bring custom batches of parts to the assembly line or operator for his/her ease.
-
-
CONCLUSION
-
Over the years robots have proven to be an important helping hand for humans, reducing human effort. Robots have variety of applications in mechanical industry. Here we have studied and tried to design a robot which can climb ropes and transfer objects from one place to another. We designed two robots wherein in the first design we encountered difficulties and limitations with Climbing mechanism, Chassis strength, and Orientation of robot on rope. We fixed them in our revised design.
ACKNOWLEDGMENT
We take this opportunity to thank Dr. D. M. Mate for his valuable guidance and for providing all necessary facilities, which were indispensable in completion of this work. We are
thankful to all staff members of the mechanical engineering department. Finally, we are also thankful to my friends and well-wishers for their valuable suggestions.
REFERENCES
[1] Abdullah Aamir Hayat Dept. Of Engineering Product Development Singapore University of Technology and Design Subir Kumar Saha Dept. Of Mechanical engg [BE, M. TECH,Ph.D]Indian Institute of Technology Delhi, India , Design and Analysis of Spring-Based Rope Climbing Robot [2] K. Vidyasagar Dept. Of ECE, SSIT Sathupally, T.S, India Rope Climbing Robot International Journal of Computer Application (09758887) Volume 108 No 12, December 2014.
[3] Anna Maria Gil Fuster Department of Electrical Engineering Technical University of Denmark Gripper design and development for a modular robot Bachelor thesis, June 2015, DTU Electrical Engineering Automation and Control Technical University of Denmark. [4] Y.C. Koo, Elmi A.B., School of Aerospace Engineering, University Sains Malaysia Wan Amir Fuad Wajdi, School of Electrical and Electronic Engineering, University Sains Malaysia Piston Mechanism Based Rope Climbing Robot International Symposium on Robotics and Intelligent Sensors 2012 (IRIS 2012). [5] MechSE Illinois "Rope climbing robots" YouTube May 4, 2017 [6] Shishir D C "How to make a Rope Climbing Robot" YouTube. Sep 16, 2014 [7] SRM Robotics "Rope Climbing Robot concept" YouTube. May 23, 2016 [8] Techniche IIT Guwahati "Escalade, Techniche'12, IIT Guwahati"YouTube. Jul 14, 2013
[9] Hi Tech xyz "How to make a Roborace Robot at home" YouTube. Nov 4, 2019 [10] Brainergiser "How to control a DC motor by FlySky RC – FS i6x using Arduino" YouTube. May 6, 2020 [11] SwapnilNimbalkar "DIY 10 CH (iBus to PWM) Receiver for FlySky i6 and iA6b receiver" Dec 5, 2020 [12] Hi Tech xyz "Wireless Dc motor controller with Pwm & brake For Robowar, Roborace, Robosoccer, RC car & Robotics" YouTube. Feb 26, 2020