
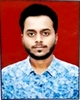
- Open Access
- Authors : Shashank P. Dashpute , Swapnil D. Shelar
- Paper ID : IJERTV10IS020194
- Volume & Issue : Volume 10, Issue 02 (February 2021)
- Published (First Online): 25-02-2021
- ISSN (Online) : 2278-0181
- Publisher Name : IJERT
- License:
This work is licensed under a Creative Commons Attribution 4.0 International License
Design and FEA Analysis of Fatigue Testing Machine
1. Shashank P. Dashpute
1.Engineering Student, Dept. Mechanical Engineering. Sinhgad Academy of Engineering
Pune, India
2. Swapnil D. Shelar
2. Engineering Student, Dept. Mechanical Engineering. Sinhgad Academy of Engineering
Pune, India
Abstract This project is based on the design & modification of major components of fatigue testing machine and also to reduce the vibration level in the machine. Major components such as spindle, coupling, base frame, chuck, weight hanger, bearing are to be redesigned, manufactured & selected from the standard catalogues. This work also focus on reduction of vibration level in the machine and the analysis of the machine is to be carried out by using the FEA software. Final assembly of the machine is to be carried out using standard assembly methodology and machine is to be calibrated for standard no. of cycles referring previous result. The testing of material aqua alloy 17 is to be checked using the standard specimens for particular loading conditions.
Keywords Fatigue Testing Machine, Fractography, Modal Analysis, FEA.
-
INTRODUCTION
Fatigue failure of engineering components and structures results from progressive fracture caused by cyclic or fluctuating loads. The magnitude of each individual load event is too small to cause complete fracture of the undamaged component, but the cumulative action of numerous load cycles, often numbering in the hundreds of thousands and millions, results in initiation and gradual propagation of a crack or cracks. Complete fracture ensues when the crack reaches critical size. Fatigue is an important potential cause of mechanical failure, as most engineering components or structures are or can be subjected to varying loads during their lifetime. This article focuses on fractography of fatigue. However, it should be noted that fractography is only part of the failure analysis of a fractured component. As with other fracture modes, proper identification of fatigue requires understanding of the fracture behaviour of the particular material subject to failure analysis. At least some knowledge of environmental and service conditions is usually necessary. Evaluation of loading conditions, often in conjunction with fractography, also provides useful information regarding the fundamental cause of failure.
-
METHODOLOGY
-
Preparation of manufacturing layout using CAD software
-
Selection of C-channel & vibration absorber for foundation
-
Selection of bearing, chuck, weight hanger etc. considering loading and operating conditions
-
Drawing of parts and assembly in CAD software
-
Analysis of various parts using FEA software
-
Manufacturing of parts
-
Assembling of all parts
-
-
DRAWBACKS OF EXISTING MACHINE
-
Alignment issues:-
-
Eccentricity was occurred in upper components as Drill Chuck was fixed with both driving and driven pulley.
-
Intense vibrations were produced during running of machine due to this misalignment.
-
Shaft gets buckled at the load points due to unnecessary long length of driving and driven shaft.
-
Base plates of motor were partially bolted and partially welded causing misalignment.
-
-
Structural issues:-
-
The supporting structure consisting of hollow square bar was not capable to carry static and dynamic load of upper components.
-
Due to absence of any damping material between structure and ground whole machine became highly unstable while running.
-
-
Modification Required:-
To minimize all this kind of faults, we design & modified the whole machine using following modifications:-
-
The shaft id threaded to allow for screwing of the specimen chucks, causing higher alignment between driving and driven shaft and drill chuck.
-
The optimized length of both shaft were selected and machined accordingly.
-
Base plate of motor has been fixed to structure using spot welding to give higher stability.
-
Motor has been fixed to base plate using both nut-bolts and spot welding to avoid any misalignment.
-
A heavy C-channel frame is installed at the base of structure to give higher stability to whole machine.
-
Vibration absorbers with higher damping coefficient are installed between machine and ground to minimize vibration and non-stability of machine.
-
IV. DESIGN AND SELECTION OF PARTS
-
Parts of Fatigue Testing Machine
-
Motor:-
The normal speed is 2880 RPM. The speed depends on the voltage. If the voltage of the supply line exceeds the proper amount of sliding rheostat in the base of the machine should be adjusted so that the speed cannot exceed 2880 RPM under ordinary conditions. Speeds in excess of the normal will cause no damage unless continued to long. In adjusting the speed take care that the contraction of the rheostat makes firm contact with the exposed portion of the winding. If it desired to run at speed below 2880 rpm, or gradually increase the speed from zero, a variable resistor can be placed in the motor lead wires by utilizing the plug type connector.
Selection of Motor:-
Model no. HMP-SR.NO.-3115-1HP
Type Electric Motor Rated Voltage 230 V AMP-5, WATTS-760
Phase – single phase Speed 2880 rpm Torque = 3315.72 Nmm
-
Bearing and its Housing Assembly:-
The particular bearing used in this project is the single row, deep groove bearing that can take both radial load and some thrust load. The bearing is shouldered in a housing made of cast iron to secure adequate support for the bearing and resist the maximum thrust load.
The bearings selected for the design were self sealed spherical roller bearings which have high load carrying capacity and it can accommodate misalignment and shaft deflections maximum of 0.5°. Bearings of 22mm bore diameter were selected for the design; it was ensured that the bearings would allow for the mounting of all components onto the shaft physically and that the mass of all components including the bearings was minimized.
The bearing housing is a cylindrical hollow shaped steel material possessing good strength and toughness. The housing design was implemented by selecting dimensions that will result in smaller minimum bending moment which is desirable or realistic shaft geometry in order to produce the required bending moment. The housing was bored to the size of the external diameter of the chuck which is 25mm. Two bearings were then forcefully inserted into the housing at both ends. The housing support was fabricated and then welded to the side of the housing so that it provides rigidity and support. The housing support on the right arm of the clamping system was firmly held by bolts on the frame with the intension of making it fixed so that it can only allow for rotating motion. The second housing on the left arm of the clamping system had supports which allows for flexible movement of the housing. The housing is held to the supports by the use of bolts and nuts in order to accommodate the flexibility required. Figure 4 shows the manner the shaft is inserted into the bearings.
Selection of Bearing Shaft diameter =20 mm Radial load, Fr = 2000 N L10h=20000
(V.B.Bhandari)
Bearing life in million revolution, L10= (60*n*l10h)/10^6
= (60*2880*20000)/10^6
= 3456 million of revolutions Dynamc load calculations Load, P= (xFr + yFa)S
=(1*2000+0)1.1
= 2200 N C=P(L10)1/b
= 2200 (3456)^1/3
= 33261.91 N
We select bearing no.6204 for diameter 20 mm. Type of bearing pedestal ball deep groove bearing, for easy mounting.
-
DESIGN OF BOLT
Two bolts are used to hold the shafts to the motor shaft.
For bolted joints we used MS10 Bolts do = 10mm
dc = do x 0.84 dc = 8.4mm
Shear Area = A = *(8.4)2 A = 55mm2
T = F/A
F = 2000N
T = 36.36 N/mm2
T on bolt<T i.e. 36.36 N/mm2 Hence design is safe.
-
WEIGHT HANGER ASSEMBLY
This consists of small bar made of cast iron, with a spring. The head of this bar is designed to be hanged on the loading hardness assembly. The spring is designed to absorb shock preventing any slight vibration of the housings on the dead weight. The choice of cast iron for the material for hanger is due to the fact that cast iron has the modulus of elasticity E as 60 to 90 mPa and can withstand the maximum weight of which the machine can carry.
-
DEAD WEIGHT
These are loads of different sizes and weight.
-
BEARING SPINDLE (Shaft):-
A medium MS material sourced locally was shafts of the machine. The fatigue resistance of the steel
was taken into consideration before selection. The machine design requires the use of two shafts electric motor and links the motor to system through the pulleys as shown. The function of the shaft attached to the electric motor is to transmit torque from the motor to the second shaft that anchors the bearings and bearing housing, clamping system and the specimen. The principal function of the second shaft is to rotate the specimen while it is under the action of bending moments from the dead weights applied at the left arm of the clamping system. The shaft is threaded to allow for screwing of the specimen chucks.
-
Design of Shaft/Spindle:-
(Reference: Design of machine element. V. B. Bhandari. Chapter 9. Shaft, key, couplings. 9.7) Shaft is made of MS. Standard values of MS are as follows.
Youngs Modulus of elasticity = E = 2.0 * Mpa. Mass density = = 7850 kg/m3
Yield stress = y = 250 Mpa & Sut = 841Mpa
Kb = Kt = 1.0
Permissible shear stress by shear stress theory 0.30 syt = 0.30 * 250 = 75 N/mm2
0.18 sut = 0.18 * 841 = 151.38 N/mm2
Tmax = 0.75 * 75 = 56.25 N/mm2 Torsional moment
Toque developed motor is directly transmitted to shaft, Mt = 3315.72 Nmm = 3.31572 Nm
Total length of shaft is 300 mm L = 300 mm
For cantilever shaft
Bending moment = Mb = F * L = 1000 * 300 Mb = 300000 Nmm
Mb = 300.000 Nm
Calculate the shaft diameter d = 20 mm
d = 20 mm for safe design and availability.
-
IR sensors with Arduino kit:-
While dealing with rotating fatigue testing machine, it can be important to know how many revolutions a motor is making. From here, you can infer the distance that your device has travelled, or any number of other important variables. In his setup, an IR emitter/receiver bounces light off a spinning object. When light reflects back, it opens the circuit, causing the output to be grounded via a pull down resistor, telling you that a revolution has been made.
-
DRILL CHUCK:-
The metal desk on which the system is assembled on is made with 3mm angle iron of mild steel and plain pan made of mild steel for the top. The length of the desk is 760mm; width and the height are respectively 210mm and 190mm. The desk is drilled at each point where parts are to fit with bolt and nut. A rectangular opening is found through which the hanger is passed; this is located at the top of the desk.
Selection of chuck
A three jaw drill chuck with threaded fittings was selected as the specimen clamp for the fatigue machine. The drill chuck was selected because it is durable and cheap to procure. The specimen clamp is expected to firmly grip the specimens without allowing for extraneous bending moments during operation of the machine. Also, the specimen must not rotate from the grip or be displaced vertically or horizontally.
The clamping mechanism allows for the specimen and chuck connection at the right arm of the shaft and bearing system to be fixed allowing for only rotating motion while the specimen and chuck connection at the left arm of the shaft and bearing system allows for both rotating and bending forces to act on the specimen by making the connection flexible as shown.
Three jaw chuck for drilling machine is the device which is used to hold the objects of a circular cross section. As we have selected the topic to clean the internal pipe we have a only option that we have to select a chuck, chuck is already available in the market, it is very easy to hold object in it and also easy to mount and rotate it on motor.
Size of chuck = 1.5-13 mm standard, Weight = 0.400 kg.
-
C-CHANNEL:-
A C-channel of mild steel material is installed at the base of structure to give more stability to machine. This c-channel is selected, cut and welded
according to the requirement of base frame. Due to this arrangement, additional mass in the form of this c-channel gives more weight to base structure as compare to upper structure of machine.
-
VIBRATION ABSORBERS:-
The term 'vibration absorber' is used for passive devices attached to the vibrating structure. Such devices are made up of masses, springs and dampers. From a control point of view, vibration absorbers can be considered as passive controllers. (The term 'passive' is used loosely here, meaning that the controller can be constructed using masses, springs and dampers).
For such controllers stability is not an issue, since the closed loop system is also a passive one. Vibration absorbers are devices attached to flexible structures in order to minimize the vibration amplitudes at a specified set of points. If the absorber is tuned so that its natural frequency coincides with the frequency of the external forcing, the steady state vibration amplitude of the main device becomes zero.
-
-
ASSEMBLY OF FATIGUE TESTING MACHINE:-
-
FINITE ELEMENT ANALYSIS
Two types of analysis are performed on Fatigue Testing Machine. As Machine undergo Vibrations due to Motor mounted on frame. It is essential to estimate natural frequencies of machine parts and vibrating bodies to avoid their resonance conditions and also to determine the displacements, stresses, strains, and forces in structures or components caused by loads that do not induce significant inertia and damping effects.
Types of Analysis performed are as follows:-
-
Static Structural Analysis
-
Modal Analysis
-
Static Structural Analysis:-
Figure 2 Total Equivalent Stress
Figure 2 Total Deformation
Figure 3 Meshing of Frame
Figure 4 Static Structural Analysis by applying boundary condition
-
Modal Analysis:-
-
Figure 4 Total Deformation Mode 1
Figure 5 Total Deformation Mode 2
Figure 5 Total Deformation Mode 3
Figure 4 Total Deformation Mode 4
Figure 4 Total Deformation Mode 5
Figure 4 Total Deformation Mode 6
Figure 4 Total Deformation Mode 7
Figure 4 Total Deformation Mode 8
Figure 4 Total Deformation Mode 9
Figure 4 Total Deformation Mode 10
-
-
RESULT
From the above numerical analysis it was observed that the stress and deformation occurred in the frame are within permissible limit.
-
Static Structural Analysis :-
Component
Stress
Deflection
Frame
2.5059 MPA
0.01184 MM
Mode No.
Frequency (HZ)
1
0
2
0
3
0
4
8.09E-02
5
0.10407
6
0.12794
7
60.023
8
70.212
9
117.58
10
151.43
Mode No.
Frequency (HZ)
1
0
2
0
3
0
4
8.09E-02
5
0.10407
6
0.12794
7
60.023
8
70.212
9
117.58
10
151.43
-
Modal Analysis :-
-
-
CONCLUSION
-
Fatigue is a failure of material or machine due to the action of repeated or fluctuating stress on a machine member for some number of times of revolutions.
-
This work is mainly focused on design and modification of critical parts of fatigue testing
machine, such as frame, electric motor, bearing and its housing, dimmer stat, nut-bolts.
-
This work also focuses on static and modal analysis on static and modal analysis of frame is carried out using Ansys V15. The results obtained are within safe limit.
-
-
REFERENCES
-
Samir Khoshaba A comparison of the fatigue calculation process according to Swedish and American textbooks for higher education Transactions on Engineering and Technology Education © 2006 UICEEVol.5, No.3, 2006
-
F.S. Silva, Fatigue crack propagation after overloading and underloading at negative stress ratios, International Journal of Fatigue 29 (2007) 17571771 Elsever2.
-
Kersnerb, V. B´lekc, Z. Kn´esla S. Seitla,Glass fibre reinforced cement based composite: fatigue andfracture parameters Applied and ComputationalMechanics 3 (2009) 363374Received 28 August 2009; received in revised form 2 December 2009
-
G.M. DomÃnguez Almaraz1, M. Guzmán Tapia2, E.E. Tapia Silva2 and E. Cadenas Calderón1,fatigue life prediction based on macroscopic plastic zone on fracture surface of aisi-sae 1018 steel, International Journal of Automotive and Mechanical Engineering (IJAME) ISSN: 2229-8649 (Print); ISSN: 2180-1606 (Online); Volume 1, pp. 29-37, January-June 2010 .
-
Fabio Marcelo Peña Bustos, design and construction of a torsional fatigue testing machine operated by inertial loads,CÉSAR AUGUSTO ÃLVAREZ VARGASReceived for review October 27 th, 2011, accepted December 3th, 2010, final version January, 4 th, 2011.
-
Sumit P.Raut1, Laukik P.Raut2 Review of Various Techniques Used for Shaft Failure Analysis, India. International Journal of Engineering Research and General Science Volume 2, Issue 2, Feb- Mar 2014, ISSN 2091-2730.