
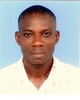
- Open Access
- Authors : Peter. O. Ohiero , Essien Michael Ime , Iyaji S. Ogbaji , Philip. O. Odey
- Paper ID : IJERTV12IS010066
- Volume & Issue : Volume 12, Issue 01 (January 2023)
- Published (First Online): 28-01-2023
- ISSN (Online) : 2278-0181
- Publisher Name : IJERT
- License:
This work is licensed under a Creative Commons Attribution 4.0 International License
Design and Implementation of Automatic Electric Water Pump Controller for Reduction of Water Wastage and Electricity Consumption
Peter. O. Ohiero
Department of Electrical and Electronic Engineering, Cross River University of Technology,
Calabar, Nigeria
Essien Michael Ime
Department of Electrical and Electronic Engineering, Cross River University of Technology,
Calabar, Nigeria
Iyaji S. Ogbaji
Department of Electrical and Electronic Engineering, Cross River University of Technology,
Calabar, Nigeria
Philip. O. Odey
Department of Electrical and Electronic Engineering, Cross River University of Technology,
Calabar, Nigeria
Abstract Wastage of water and electricity as results of overflow of water from water storage tank during pumping of water using electric water pump is a serious challenge in the conservation and storage of water for domestic, industrial and commercial future use. To solve this problem, this paper presents a design and implementation of an automatic electric water pump controller using ultrasonic sensor and microcontroller. The ultrasonic sensor is proposed to be installed in the cover of the storage tank on the side facing the water level. The microcontroller is programed with hex file from Arduino Uno to utilise the time taken for the sound waves from the sensor to travel and return from the water level to determine the distance between the sensor and the water level. The distance is then compared with the pre-set distance and give the corresponding digital output to give an indication of the status of the water level in the storage tank and automatically turn ON and OFF the water pump when the water level is low (pre-set minimum level) or high (pre-set maximium level). The implementation of the designed system was implemented in Proteus software. The control command was written in Arduino Uno and the hex file used to run the microcontroller (Arduino microntroller). A 1k potentiometer is connected to the ultrasonic sensor to emulate the level of water in the storage. When the potentiometer is at 5% which means the level of water is close to the sensor, the Liquid Crystal Display indicated water is full and the controller turned OFF the water pump and when the potentiometer is varied up to 28%, the Liquid Crystal Display indicated water is low and the water pump was turned ON and vice versa. The results show that the designed automatic water pump controller can automatically turn ON and OFF when the water level in storage tank is at the pre-set low and high level respectively. This designed system can be constructed, tested for physical use.
Keywords Water pump, ultrasonic sensor, microcontroller, protoeus, arduino uno liquid crystal display
1.0 INTRODUCTION
Electric water pump is used to transmit water from a source of water for immediate use or storage in reservoirs, dams, overhead or underground tanks for future use. Storage of water for future use is necessary due to its necessity, high demand and scarcity of its supply[1].
Nowadays, many homes in developing countries have boreholes where water is pumped using hand pump [2-4] or submersible and surface electric water pump into overhead tanks for storage to be used immediately or in future [5, 6]. Hand pump or mechanical or manual pump uses man or animal power to extract water from a water source; a well or borehole. There are the most economical and simple way of providing water in rural and suburban areas but has the challenge of requiring physical exertion by man which is slow and inefficient. Electric water pump on the other hand is more convenient and efficient and does not require physical exertion of power.
In electric water pump, electricity is used to power a water pump to transmit water to storage tank. The electric water pump requires a control usually a switch to turn it ON and OFF when the water level in the tank is low and filled respectively. The existing switch/control requires human intervention/the present of an operator and in the absence of the operator, is either water is not pumped or it overflows when the storage tank is filled until someone turns the pump OFF resulting to wastage of water, flooding of the environment, waste of electricity and increase in electricity consumption and bills. In most cases the continuous running of electric pump results to overheating, break down, reduction in the life span of the water pump and increase in maintenance and replacement cost.
Automatic control of the operation of electric water pump is an important aspect of water management and conservation and this has been investigated by various researchers. Different methods have been used to stop overflow and wastage of water when the storage tank is filled and pump water when the water level is low. Some of these methods involves the use of ball valve, float switch, and electronic controllers [7]. In [8] it was presented a microcontroller based automatic water level control system. The studied system utilises the conductivity property of water. It uses comparator circuits with copper conductors as the water level sensor. When water touches the copper sensor at a particular level in the tank, the circuit is completed and voltage is transferred to the copper which in turn is transferred to the comparator circuit from where it is processed. The LM324 comparator
was used to compare the inputs from the electrode in the tank with the pre-set resistance and output a HIGH or a LOW with respect to the results of the comparison. The HIGH or LOW is fed into a microcontroller which uses this to control the water pump and display the appropriate status on the LCD screen. The design and implementation of a smart system that will be connected to ioT (internet of Things) was presented by [9], this enable the user to control the operation of water pump from anywhere using his/her mobile phone. This requires the controller Wi-Fi module to make connection with the IoT. The challenge with this system is the additional cost required to obtain a Wi-Fi module and the continuous subscription for internet data to keep the system in operation. In [10] it was presented a design of a microcontroller-less overhead controller for a solarised homes. The design uses the utility voltage condition, solar generation status, reservoir water availability and water content of the overhead tank operate water pump. In [11] float switch and arduino microcontrollers were utilised to control the operation of water pump. In the designed system, three float switch were connected to Arduino pin 1 to 3 using 10k resistors. The arduino microcontroller was programmed to give control signals to a transistor biased relay to turn off water pump.
The use of electronic circuits with conducting metal rod (electrode) sensors are used to determine water level and provide control to water pump. In electronic circuit with conducting metal rods, the metal rods are immerse in water at
2.0. THEORETICAL BACKGROUND OF ULTRASONIC SENSOR
An ultrasonic sensor consists of two main components namely a transmitter and a receiver. The transmitter emits sound using piezoelectric crystal while the receiver receives the sound after it has travelled and returned from the target. The ultrasonic sensor is a convenient way of measuring distance from an object. The sensor possesses high accuracy within the range of 2cm to 500cm from the target object with a resolution of 0.3cm. The sensor transmits ultrasonic sound pulse of 20kHz to 40kHz frequency square wave through the transmitter; the reflected echo received due to the target is then picked-up by the receiver module, te receiver then produce a signal wave form with a time period that is proportional to the distance of the object from the sensor. The ultrasonic sensor uses the time taken for the sound to travel to and fro the receiver to calculate the distance from the target by equation (1). A suitable microcontroller is used to interpret the received signal and provide a control signal to the relay driving a switch or contactor to control the operation of the water pump.
With regards to the level of water in a storage tank, it is determined by the distance between the sensor and the level of the water by which the reflection occur. As the level of the water decreases, the distance between the sensor and water level increases. Hence, the distance between the sensor and the level of the water is given by;
different level and through the conductivity of current in water, gives indication of the water level using level indicators. Level indicators have been applied as a way to
D T S
2
(1)
monitor the level of water in the tank in an effort to prevent overflow and wastage, but this requires the presence of an operator to manually turn OFF the pump when the tank is filled. This results to additional cost and does not fill the requirement of turning OFF the water pump by itself. The use of conducting metal rods in contact with water on the other hand poses a lot of challenges such corrosion of the metal rods, causing water contamination and impurity, decomposition of water into chemical elements, changing the quality of water. With the conducting metal rod or electrodes sensors, ripples on the surface of water can cause rapid switching of the relay. In other to eliminate these challenges, it is necessary to provide a reliable, economical and intelligent way of controlling pumping of water into storage tanks. Recent review by [12] shows that liquid level measurement technology using ultrasonic sensor have high accuracy for the measurement of liquid level and control of water or liquid pump.
The design and implementation of automatic water pump controller using ultrasonic sensor is proposed and discussed in this paper. An automatic water pump controller is an intelligent system designed to turn ON and OFF electric water pump when the water level in the storage tank is at low and high level respectively. The rest of the paper is divided as follows. In section II, the theoretical background of ultrasonic sensor and control are described. The design and implementation of the automatic water pump controller is explained in detail in section III. In section IV, modelling and
Where, D is the distance, T is the time and S is the speed of sound which is approximately given 340ms-1. The distance D, and T changes as the level of water go closer or far away from the ultrasonic sensor.
3.0. DESIGN OF THE RELAY SWITCHING CIRCUIT The relay switching circuit is a very important component of the automatic water pump control system. It carries out the command from the microcontroller. The relay switching circuit consists of a relay, a diode, a transistor and a resistor as shown in Fig. 1.0. During switching of the relay, the current through the relay coil changes quickly leading to large transient voltages. The diode reduces this transient and sparking of the relay coil when it opens while the microcontroller controls base voltage of the transistor between 0V and 5V to put the transistor in blockage or saturation respectively. The operation of the relay switches a water pump ON or OFF. In the design of the relay switching circuit, accurate selection of values of the Transistor, Q1 and resistor, R1 is important to for effective performance of the switching.
In order to select accurate transistor, the voltage used in the controlling circuit of 12V which is also the relay voltage, is applied. Taking the resistance of the relay coil,
to be 100, the current flowing into the relay coil is given by;
simulation of the proposed system is discussed in detail. Section V concludes the paper.
IRL1
VRL1
RRL1
(2)
IRL1
VCC VCE
RRL1
(3)
R 9.3V 84
B 0.11A
IRL1
12V 1V 100
0.11A
R1 = RB= Therefore, a standard value of 100resistor was used for R1.
4.0 MATERIALS AND METHOD
The method used in this research a contactless means of
Since the current consumption of the relay is 0.11A and the
maximium collector current must be greater than the load (relay) current, therefore a general purpose 2N2222 transistor with a collector current of 0.8A was selected for this project design and it has the following specifications:
lc (max) = 0.8A, hfe= 100 300, VCEO(Max) = 40V, VCBO=75V,
Frequency = 300MHz,
VCE(sat) = 1V, Power dissipation = 0.4W,
Vmin = ±5V, VBE = 6V, operating junction temperature range from -650C to 1500C.
Therefore, the selection of the value of the resistor, R1 to limit the current flowing the transistor to prevent it from damage can be obtained as;
detecting the level of water in a reservoir/storage tank by using an ultrasonic transceiver sensor HC-SR04 and microcontroller programmed to automatically turn ON and OFF water pump when the water level in the storage tank is low and full respectively. The ultrasonic sensor is used with other materials such as microcontroller (Arduino Uno microcontroller), Single Pole Single Throw (SPDT) Relay, Diode, Resistor, Liquid Crystal Display (LCD), and Power pack.
To detect the level of water in the reservoir/storage tank, the ultrasonic sensor HC-SR04 is transmits short, high- frequency pulses at regular intervals, and these pulses propagate in air at the velocity of sound (340ms-1). The
Vcc Vce sat 12 1V
11V
microcontroller process the data send to and received from
Ic( sat )
RRL1
100
0.11A 100
the ultrasonic sensor. In other to carry out its function, the microcontroller is programmed using arduino Uno to send ultrasonic signal at 40 kHz frequency through its digital
IC (sat ) 110mA
But,
IB
Ic
hfe
(4)
output pin that are connected to two trigger pin of the ultrasonic sensor for the overhead reservoir and receive the reflected signal from the echo pins of the sensor, process the data and compute the corresponding level of the water in the reservoir. The program helps the microcontroller to define the limits of the water level, lower level, medium level and
I 0.11A 1.1mA
B 100
Fig. 1 Relay switching circuit
The DC base bias voltage of the transistor is 10V, the base current is 1.1mA and the base-emitter voltage drop is 0.7V. Therefore, the base bias resistor can be obtain using;
maximum level. When the water level is at lower level, the microcontroller gives output signal to actuate the relay that will operate a contactor to turn ON the water pump and when the water level reaches the maximium level, it automatically turn OFF the water pump to avoid overflowing. The microcontroller also gives signal about the level of water in the overhead tank or reservoir and the state of the pumping machine and display on a 16×2 alphanumeric liquid crystal display (LCD).
4.1 Modelling and Simulation Control of Water Pump The designed microcontroller and relay circuits are modelled and simulated in Proteus and the output validated. The program was written on the Arduino sketch and compiled into a hex file and was uploaded to the proteus. Fig. 2 and Fig. 3 show the simulation circuits which the water pump is turn ON and OFF. The circuit is simulated with a 1k potentiometers which served as the liquid level of the overhead tank and the desired output obtained when it is
VB IBRB VBE
B
R VB VBE
IB
R 10V 0.7V
B 0.11A
9.3V
0.11A
(5)
(6)
varied in increasing step and vice versa. The water pump in
this test is represented by a DC motor. The choice of the type of pup whether DC or AC does not matter, the controller is only acting as an automatic switch to the water pump circuit. When the potentiometer value is low, example when it is set to zero, it means the storage tank is full and the LCD displayed LEVEL FULL, MOTOR OFF. On the other hand, when the potentiometer value is high, it means the storage tank is low and the LCD displayed LEVEL LOW, MOTOR ON.
Fig. 2 Simulation of automatic water pump controller model when the water pump is turn OFF at pre-set high water level
Fig. 3 Simulation of automatic water pump controller model when the water pump is turn ON at pre-set high water level
Table 1 The relationship between the resistance of the potentiometer, motor (water pump) voltage, current and status of the motor when the storage tank is been emptied.
1k-Potentiometer (%) |
0 |
5 |
10 |
15 |
25 |
28 |
50 |
100 |
DC Voltage (V) |
0 |
0 |
0 |
0 |
0 |
310 |
310 |
310 |
Current (A) |
0 |
0 |
0 |
0 |
0 |
3.52 |
3.52 |
3.52 |
Power (W) |
0 |
0 |
0 |
0 |
0 |
1091.2 |
1091.2 |
1091.2 |
LCD |
Water Full, Motor OFF |
Water Full, Motor OFF |
Water Full, Motor OFF |
Water Full, Motor OFF |
Water Medium, Motor OFF |
Water Low, Motor ON |
Water Low, Motor ON |
Water Low, Motor ON |
Table 2 The relationship between the resistance of the potentiometer, motor (water pump) voltage, current and status of the motor when the storage tank is been filled.
1k-Potentiometer (%) |
100 |
50 |
28 |
25 |
15 |
10 |
5 |
0 |
DC Voltage (V) |
310 |
310 |
310 |
0 |
0 |
0 |
0 |
0 |
Current (A) |
3.52 |
3.52 |
3.52 |
0 |
0 |
0 |
0 |
0 |
Power (W) |
1091.2 |
1091.2 |
1091.2 |
0 |
0 |
0 |
0 |
0 |
LCD |
Water Low, Motor ON |
Water Low, Motor ON |
Water Low, Motor ON |
Water Medium, Motor OFF |
Water Full, Motor OFF |
Water Full, Motor OFF |
Water Full, Motor OFF |
Water Full, Motor OFF |
5. RESULTS AND DISCUSSION
Table 1 and table 2 show the relationship resistance of the potentiometer (the distance between the water level and sensor), voltage, current and power of the DC motor (water pump). Table 1.0 show results when an existing filled storage tank is emptied, that is increasing the resistance which tallies with increasing the distance between the water level and the sensor. While table 2.0 is when the water pump is turned ON to fill an emptied tank. It can be seen that as the potentiometer value increases, the corresponding distance between the water level and the sensor also increases proportionally. In table 1.0, between 0% to 25% of the value of the potentiometer, the distance between the water level and sensor is short indicating that the water in the storage tank is still enough, and the LCD displayed Water Full, Motor: OFF. And the reverse is the case when the value of the potentiometer decreases from higher value emulating that the water level is low and the water pump is turned ON.
6.0 CONCLUSIONS
In this work, an unmanned automatic electric water pump controller using ultrasonic sensor and microcontroller is designed and implemented. It is capable of monitoring the water level and automatically control the pumping of water to storage tank. It turns OFF water pump when the level of water is at the pre-set high level and turns ON water pump when the water level is at pre-set low level. It also gives indication of the status of the water level and pump in the liquid crystal display. It can be seen from the results that this is a suitable replacement of the existing switch that is manually turned ON or OFF. The advantages of this system are the reduction of wastage of water and electricity due to continuous overflow of water when the storage tank is filled, elimination of human resources and errors associated with human operations. It reduces breakdown and maintenance cost and increase the life span of the pump. It is cheap and can easily be constructed.
REFERENCES:
[1] I. R. Abubakar, "Strategies for coping with inadequate domestic water supply in Abuja, Nigeria," Water international, vol. 43, no. 5, pp. 570-590, 2018. [2] A. Toyobo and N. Tanimowo, "Evaluation of rural water supply schemes in selected communities in Oke-Ogun Area, Oyo State, Nigeria," Global Journal of Science Frontier Research, vol. 11, no. 9, pp. 1-6, 2011. [3] R. C. Carter and I. Ross, "Beyond'functionality'of handpump- supplied rural water services in developing countries," Waterlines, pp. 94-110, 2016. [4] P. MartÃnez-Santos, M. MartÃn-Loeches, S. DÃaz-Alcaide, andK. Danert, "Manual borehole drilling as a cost-effective solution for drinking water access in low-income contexts," Water, vol. 12, no. 7, p. 1981, 2020.
[5] V. Boscaino, G. Cipriani, G. Drago, V. Di Dio, and M. G. Ippolito, "Design, modeling, and simulation of a photovoltaic water pumping system," in 2018 IEEE International Conference on Industrial Technology (ICIT), 2018: IEEE, pp. 938-943. [6] M. A. Mossa, O. Gam, N. Bianchi, and N. V. Quynh, "Enhanced Control and Power Management for a Renewable Energy-Based Water Pumping System," IEEE Access, vol. 10, pp. 36028-36056, 2022. [7] G. Dinesh Kumar, K. Karthikeyan, and C. Sathishkumar, "Study and Testing of Pneumatic Control of Ball Valve Using Actuator," in Advances in Materials Research: Springer, 2021, pp. 1199-1211. [8] K. S. Kumar, G. Mukesh, and K. Deepti, "Microcontroller based Automatic Water level Control System," International Refereed Journal of Motorering And Science (Irjes) Volume, vol. 4, 2015. [9] A. Al-Refaei, A. Al-Enezi, and T. Al-Azem, "Smart Domestic Water Management System," 2021. [10] S. J. Sarkar, S. K. Sahoo, T. K. Panigrahi, P. S. Patro, B. C. Kumar, and C. K. Sahoo, "Designing of a microcontroller-less overhead tank controller for solarised homes," in 2022 International Conference on Intelligent Controller and Computing for Smart Power (ICICCSP), 2022: IEEE, pp. 1-6. [11] O. Akinwole, "Design, simulation and implementation of an Arduino microcontroller based automatic water level controller with I2C LCD display," International Journal of Advances in Applied Sciences (IJAAS), vol. 9, no. 2, pp. 77-84, 2020. [12] P. Mohindru, "Development of liquid level measurement technology: A review," Flow Measurement and Instrumentation, p. 102295, 2022.