
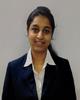
- Open Access
- Authors : Prarthana Hegde , Diksha Kadam , Akhilesh Kamtikar , Jahida Subhedar
- Paper ID : IJERTV10IS060316
- Volume & Issue : Volume 10, Issue 06 (June 2021)
- Published (First Online): 29-06-2021
- ISSN (Online) : 2278-0181
- Publisher Name : IJERT
- License:
This work is licensed under a Creative Commons Attribution 4.0 International License
Design and Implementation of Metal Waste Sorting using Microcontroller and IoT
Prarthana Hegde
B.Tech Mechatronics Engineering Symbiosis Skills And Professional University
Pune, India
Akhilesh Kamtikar
B.Tech Mechatronics Engineering Symbiosis Skillls And Professional University
Pune,India
Diksha Kadam
B.Tech Mechatronics Engineering Symbiosis Skillls And Professional University
Pune,India
Professor Jahida Subhedar
-
ech Mechatronics Engineering Symbiosis Skills and Professional University Pune, India
Abstract There are many environmental and healthcare challenges when it comes to Waste Management. As urban population increases the waste generated also increases day-by- day (About 50% of waste is dumped in landfill sites). One of the major problems with waste management is sorting of the waste that is dumped. The waste in dumping grounds is sorted manually which leads to a lot of sorting issues like Metal and Non-metal (plastics, rubbers etc.), medical, home waste not segregated properly along with health risk of the workers. This paper presents the implementation of waste sorting system using Internet of things (IoT) and microcontrollers. The system being developed will help in this regard by sorting the metallic waste from the non-metallic waste, which can then be sent for recycling. Also, as an incentive, we have added an IOT system which recognizes the amount of material recycled and a proportional number of benefits can be provided to the respective location (areas). The main idea of our project is to design and fabricate a small and simple conveyor belt system, and automate the process of metal sorting system using IOT. The automated sorting machine is able to separate metal objects and at the same time move objects automatically to the container with an inductive proximity sensor to detect a range of objects. When waste is disposed of or recycled in a safe, ethical, and responsible manner, it helps reduce the negative impacts on the environment. Therefore, in the future, it is expected that this project can help people manage their waste in a better way with more interest and reduce the damage and risk of environment and health respectively.
Keywords Waste management, Conveyor belt, Internet of things (IoT), microcontrollers.
-
INTRODUCTION
Sorting is a process which is used to separate two or more things according to the requirements of the process. Here we are taking the example of waste management system to separate metals and non-metals. The non-metallic part is disposed in the dumping ground using a conveyor belt system that is controlled by a DC motor. The mechanism used to sort metal and non-metal is by using a Servo motor which will actuate the pusher based on input from microcontroller. The
non- metallic object falls down into a container and the metal (when detected by inductive proximity sensor) moves forward.
The control systems for the project consists of RFID (Radio Frequency Identification) Scanner (EM18) which scans the card to identify the area from where the waste has originated. The signal goes to ATMEGA controller to identify the area the waste is from and then it sends signal to NodeMCU to reflect this on the IOT interface. Then the sorted waste is sent for recycling and the benefits of the recycled waste are reflected on the interface in that particular area using Internet of Things (IOT) concepts.
-
LITERATURE REVIEW
Waste sorting, especially e-waste and metal sorting as well as their recycling is a major problem for the world today [3]. However, the waste sorting systems currently in place are ill- equipped to tackle this problem efficiently [9]. One of the best ways to tackle this problem is to build a conveyor-based system that can seamlessly sort metal and non-metal and at the same time be flexible enough to accommodate any changes in the sorting mechanism [10]. The inductive proximity sensor is a convenient tool for sensing metals and it can be used as a control for the sorting process [1], [3]. IOT is an upcoming field in which it is easy to provide quick information to any device anywhere in the world provided that the device is connected to a network [5]. A properly designed IOT interface helps in flawless communication and ensures proper flow of information [5], [6]. Servo and DC motors are simple yet effective tools to sufficiently run a conveyor system [8], [9]. To control all this hardware various microcontrollers can be used. Atmega328P and NodeMCU are two such microcontrollers [3], [4]. The ESP8266 Wi-Fi module is a device which is used by NodeMCU to connect to the internet to facilitate internet connectivity. Blynk app is used to make the IOT interface. The simplicity of the app is that it can form easy connections with almost any device through the cloud [16].
-
PROPOSED SYSTEM
Fig. 1 given below shows the block diagram of the system as a whole. In the system, the waste is placed on a conveyor and conveyor is started. Before this step, we scan the RFID card on the scanner to recognize the area from which the waste has come. The waste goes to the sorting mechanism, for which an inductive proximity sensor has been used, and is sorted according to metal and non-metal. Moreover, as soon as the sensor sense any metal the digital counter is incremented and this gets reflected in the user interface with the help of IOT. To be precise, the data is collected by sensor and passed along to NodeMCU. From here, it goes to the Blynk servers in the Cloud, and from there to the IOT interface on mobile phone.
Fig 1: Overall system configuration
-
The conveyor system
When the power is switched on, the first step is to scan the RFID card in the scanner. Every area has been assigned a RFID scanner tag and it must be read in the scanner. The moment the scanner identifies the tag, data is sent to the interface and the corresponding text is updated in the interface. After this, the DC motor starts. The waste that was dumped on conveyor starts moving and sensor begins sensing the waste. If it senses metal, the counter value is increased and the servo motor remains off. The metal proceeds along the conveyor and goes to the recycle container. If sensor senses a non-metal, the servo motor switches on and the non- metal is dumped into the waste container. Fig. 2 below shows the flow chart for this
Fig 2: Convyor system block diagram
-
The control system
The RFID scanner sends data to the microcontroller (ATMEGA 328P). This microcontroller also gets data from the sensor, whether the material is metal or non-metal. It also calculates the counter value. All this data is sent to NodeMCU. From here, using the ESP8266 module connected to the internet the data is sent to the Blynk server. The Blynk server stores this data in the Cloud. We access this data using internet on the mobile phone. Hence, we can see the interface on the screen. The required coding is done in the NodeMCU and the interface is designed on Blynk itself. As shown in Fig. 3 below, two microcontrollers are used. One for controlling the sorting system and another for implementing IOT.
Fig 3: Control system block diagram
-
-
SEQUENCE OF OPERATIONS
First the power is switched on. At this point, the RFID scanner (EM 18) switches on and the card is swiped. We must ensure that the required material that is to be sorted is on the conveyor at this point. As soon as card is swiped, the microcontroller sends a signal to the motor driver and starts the DC motor. The materials on the conveyor belt approach the snsor. At the same time, the counter is reset to zero and name of the area corresponding to the scanned RFID card goes to the microcontroller. Using relays, the microcontroller sends this data to a cloud server from where it can be accessed at any time using the internet. Now, the sensor sense whether the object is metal or non-metal. If the object is a metal, the inductive proximity sensor sends a signal to the microcontroller, and it in turn sends it to the NodeMcu. The counter value is increased by one and this is reflected immediately to the device connected to the cloud server. If the object is a non-metal, the servo motor running the pusher sends the object to the waste bin. The NodeMCU multiples the counter value with a constant to get an understanding of the benefit received by the particular area
-
RESOURCES AND MATERIALS USED The project can be divided into three parts:
-
Mechanical structure and hardware:
The basic mechanical unit is a conveyor belt. It is made up of stainless steel and the dimensions are: 0.762 m * 0.2032 m * 0.4572 m. The conveyor belt is made up of Rexine cloth with dimensions: 2.54 m * 0.1016 m. The dimensions of the metal cube that will be sorted is 0.0381 m * 0.0381 m * 0.0831 m. Three PCB boards have been used in the project one each for microcontroller, NodeMCU, and relays. The dimensions of the PCB board are as follows: 0.1 m * 0.15 m. The conveyor system can be seen in Fig. 4 below. The components in Fig. 4 were designed in NX Siemens software
Fig. 4.1: Conveyor System in NX Siemens
Fig 4.2 3-D model of conveyor
-
Electronic components
-
Inductive Proximity Sensor: A inductive proximity sensor can detect metal targets approaching the sensor, without physical contact with the target. In the project, it has been used to sense metal from non-metal.
Fig 5: Inductive Proximity Sensor
-
Relays: Relay is an electrically operated switch. It consists of a set of input terminals for a single or multiple control signals, and a set of operating contact terminals. The switch may have any number of contacts in multiple contact forms, such as make contacts, break contacts, or combinations thereof. It was used in this project to connect the two microcontrollers operating at different voltages and also the sensor that operates at a higher voltage than the microcontroller.
Fig 6: Relay
-
DC motor: A DC motor is an electrical machine that converts electrical energy into mechanical energy. In a DC motor, the input electrical energy is the direct current which is transformed into the mechanical rotation. In this project it was used to run the conveyor belt.
Fig 7: DC Motor
-
Motor driver L293D: L293D is a typical Motor driver or Motor Driver IC which allows DC motor to drive on either direction. L293D is a 16-pin IC which can control a set of two DC motors simultaneously in any direction.
8. NodeMCU (ESP8266): NodeMCU is an open- source Lua based firmware and development board specially targeted for IOT based Applications. It includes firmware that runs on the ESP8266 Wi-Fi SoC from Espressif Systems, and hardware which is based on the ESP-12 module.
-
-
Programming
Fig. 12: NodeMCU
Fig. 8: Motor Driver
-
Servo motor: A servomotor is a rotary actuator or linear actuator that allows for precise control of angular or linear position, velocity and acceleration. It consists of a suitable motor coupled to a sensor for position feedback. It also requires a relatively sophisticated controller, often a dedicated module designed specifically for use with servomotors. In this project it was used to actuate the pusher mechanism to sort the metal and non-metals.
Fig. 9: Servo motor
-
ATMEGA328P Microcontroller: ATMEGA328P is high performance, low power controller from Microchip. ATMEGA328P is an 8-bit microcontroller based on AVR (Alf-Egil Bogen Vegard Wollan RISC (Reduced Instruction Set Computer)) architecture. It is the most popular of all AVR controllers. It is used in this project to control the conveyor and the sorting process.
Fig. 10: ATMEGA328P chip
-
RFID Scanner (EM-18): EM-18 RFID Reader is a module which reads the ID information stored in RFID Tags. This ID information is unique for every Tag which cannot be copied. It was used to assign various areas to the different cards and scan them to identify the area accordingly.
Fig. 11: EM-18 RFID scanner
There are two types of programming in this project. Number one is the microcontroller programming done in ATMEGA328P for interfacing the motors, sorting mechanism and RFID scanning (this signal goes to the NodeMCU for communication with IOT interface). Number two is the IOT programming done in NodeMCU for taking all the data from sensor and RFID scanner and storing it in a server. From the server the phone or any device can access this data using the internet. The cloud server used for this project is the BLYNK could server.
Blynk is a hardware-agnostic IOT platform with white-label mobile apps, private clouds, device management, data analytics, and machine learning.
Fig. 13 Blynk software
-
-
RESULTS AND CONCLUSION
-
Mechanical
-
The conveyor was successfully implemented. The metal was transported to recycle container according to the area while the non-metal was transported to the waste container using servo motor.
Fig. 14 Fabricated conveyor system
-
We can conclude from this that the metal sorting system was successfully implemented. This particular system runs on 30 rpm and it can manage sizes of upto 0.0381 m * 0.0381 m * 0.0831 m. For
other speeds and sizes, the system will have to be adjusted accordingly.
-
-
Electronic
-
All the circuitry was connected to PCBs and soldered. The Atmega328P received signal from sensor and through relays sent it to NodeMCU. From there we can see that the counter value is increased and benefits are reflected on the IOT interface.
Fig 15. Clockwise from left- PCB with NodeMCU, Inductive proximity sensor, PCB with Relay Circuitry, PCB with Atmega328P, EM 18 RFID Scanner. Below: RFID cards.
-
For the specifications of the components used, the system works efficiently and has no errors. We may increase the range of sensing by using an inductive proximity sensor with larger sensing distance and use more RFID cards if required.
-
-
IOT Interface
-
When NodeMCU, receives data from Atmega328P, it sends this data to the cloud via the internet service or Wi-Fi that it is connected to.
-
From the cloud, in this case the Blynk servers, the data is sent to the project we have created in the Blynk application on our phone.
-
There we can see on an LCD display, the various changes in area and corresponding benefits given to that area based on the number of metals from that area.
Fig. 16 Count of metal parts from area of Wakad
Fig. 17 Benefit awarded for area of Wakad
Fig. 18 Count of metal parts from area of Baner
Fig. 19 Benefit awarded for area of Baner
-
The number of benefits can be adjusted by changing the multiplier in the code, which is, for now, 10.
-
We can also keep other ways of estimating benefits, like percentage of metal waste, weight of metal waste or time spent by waste on conveyor.
-
-
-
APPLICATIONS
-
Today, a lot of metallic waste is found in local landfills and garbage dumps. This includes e-waste and other heavy metals which can be very harmful to the environment. These must be properly disposed as burning or burying them cause huge amounts of air and soil pollution.
-
Moreover, recycling waste is the need of the hour. Producing new products is time consuming and it also affects the environment in a drastic way. E- waste generation is increasing as we depend more and ore on technological devices for day to day working. Hence these must be recycled to reduce load on the non-renewable supply of metal in Earths crust.
-
Hence, this project aims to help sort and recycle the metallic waste in garbage dumps and landfills. This is still not done properly in many areas of India (rural and urban) and even if it is, improper and inefficient methods like manual sorting are used.
-
As an incentive to encourage people to recycle waste, an IOT system has been added. This system recognizes the amount of material recycled by a particular user/ area/ industry and can be programmed to give a proportionate number of rewards (like money or benefits) to that particular entity.
-
Extensions of this project can be used in security systems, where metallic parts must be kept separate from non-metallic parts, and a particular labelling has to be done for each batch.
-
It can also be used as quality maintenance system, by changing the sorting system to one that can detect deformities (by changing the sensor), the system will work to select only top-quality material and then using IOT, one can estimate the total production done and choose which batch is needed.
-
-
FUTURE SCOPE
-
HMI can include more options for better ergonomics.
-
We can improve the mechanism by adding pneumatic cylinder instead of mechanical pusher.
-
We can implement this prototype for variable size of the object.
-
We can also implement this for separation of non- metal like rubber, plastic etc.
-
-
ACKNOWLEDGMENT
We would like to take this opportunity and express our gratitude towards our college for this project and to give us a chance to apply our theoretical knowledge practically. We would like to thank Director of Mechatronics Dr. Santosh Sonavane for guiding us throughout the project. Special and sincere thanks to our guide and mentor Professor Jahida Subhedar who guided us to work on the right path and complete this project and also other staff of the department. We would like to thank our family and friends who encouraged and helped us throughout the project.
-
REFERENCES
-
-
Kadiyam Sasidhar, Shaik Faiz Hussain, Syed Ali Safdar and Mohd Aleem Uddin, Design and Development of a PLC Based Automatic Object Sorting, International Journal of Research and Scientific Innovation (IJRSI), Volume IV, Issue XII, pp 10-13, December 2017.
-
Alhade A. Algitta, Mustafa S., Ibrahim F., Abdalruof N. and Yousef M., Automated Packaging Machine Using PLC, International Journal of Innovative Science, Engineering & Technology (IJISET), Vol. 2 Issue 5, pp 282-288, May 2015.
-
Prof B H Band, A Bhandurge, S Wath, S Duryodhan and V Ughade, Microcontroller Based Separation of Metal from Garbage Waste, International Journal for Scientific Research & Development (IJSRD), Vol. 7, Issue 02, pp 1057-1059, 2019.
-
Mahmudul Hasan Russel, Mehdi Hasan Chowdhury, Md. Shekh Naim Uddin,Ashif Newaz and Md. Mehdi Masud Talukder, Development of
Automatic Smart Waste Sorter Machine, International Conference on Mechanical, Industrial and Materials Engineering (ICMIME), unpublished.
-
Krishna Jadhav, Gaurav Chaudhari, Abhishek Jadhav, Shubham Kondekar and Prof. Nagre V.L., IOT Color Based Product Sorting Machine, International Research Journal of Engineering and Technology (IRJET), Volume: 06 Issue: 01, pp. 4211-4244, February, 2019.
-
D A Jakkan, Chaugule Bharat Sudhakar, Jagtap Sanket Vilas and Khan Umar Aslam, Color Based Product Sorting Machine using IOT, Journal of Embedded Systems and Processing, Volume 4, Issue 3, pp. 25-29, 2019
-
Raihan Bin Mofidul, Md. Shahadath Hossain Sabbir, Amit Kumer Podder and Mohammad Shaifur Rahman, Design and Implementation of Remote Controlling and Monitoring System for Automatic PLC Based Packaging Industry, International Conference on Advances in Science, Engineering and Robotics Technology (ICASERT), 2019
-
M Eriyadi, S B Mulia and R Purnomo, Automatic metal sorting conveyor machine based on Programmable Logic Controller, International Symposium on Materials and Electrical Engineering (ISMEE), 2020
-
R.Aravind, M.Arun Kumar, S.Dharshan Manjunath and R.Kalaiselvan, Automatic Metal Separation and Packaging Using PLC, International Journal of Innovative Science, Engineering & Technology (IJISET), Volume 5, Issue 2, pp. 125-133, February 2018.
-
T. Valerio, METHOD AND APPARATUS FOR SORTING METAL, US 7,674,994 B1, March 09, 2010. Available: https://patents.justia.com/patent/20100224537#history, Accessed:
January 23, 2021
-
P.Thirumurugan, R.Aravind, M.Arun Kumar, S.Dharshan Manjunath, and R.Kalaiselvan, Programmable Logic Controller Based Metal Segregation in Steel Industry, International Journal of Advanced Research in Electrical, Electronics and Instrumentation Engineering (IJAREEIE), Vol. 7, Issue 2, pp. 578-583, February 2018.
-
Kunhimohammed C. K, Muhammed Saifudeen K. K, Sahna S, Gokul
M. S and Shaeez Usman Abdulla, Automatic Color Sorting Machine Using TCS230 Color Sensor And PIC Microcontroller, International Journal of Research and Innovations in Science and Technology (IJRIST) Volume 2, Issue 2, pp. 33-38, 2015.
-
Pradip Baishya, Shanjenbam Brojendro Singh , and D.K. Mahanta, Fabrication & testing of dry waste sorting machine, International Research Journal of Engineering and Technology (IRJET), Volume: 02, Issue: 09, pp. 2248-2251, December 2015
-
Rohit R. Yadav, Shubham S. More, Onkar N. Mutekar, Aditya L. Mogal and Rayappa S. Mahale, Multilevel Object Sorting System using PLC Controller, International Research Journal of Engineering and Technology (IRJET), Volume: 06, Issue 05, May 2019.
-
Jaswandi G. Joshi and Prof. D.D. Ahire, A BRIEF SURVEY ON PROGRAMMABLE LOGIC CONTROLLER AND ITS VERSATILE APPLICATIONS USING SCADA SYSTEM, International Journal of Advance Research and Innovative Ideas in Education (IJARIIE), Vol. 1, Issue. 4, pp. 517-521, 2015.
-
Ermi Medias, Syufrijal, and Muhammad Rifan, (2019), Internet of Things (IoT): BLYNK Framework for Smart Home in 3rd UNJ International Conference on Technical and Vocational Education and Training 2018, KnE Social Science, pages 579586. DOI 10.18502/kss.v3i12.4128