
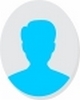
- Open Access
- Authors : Ahmad F. Tazay
- Paper ID : IJERTV10IS100132
- Volume & Issue : Volume 10, Issue 10 (October 2021)
- Published (First Online): 27-10-2021
- ISSN (Online) : 2278-0181
- Publisher Name : IJERT
- License:
This work is licensed under a Creative Commons Attribution 4.0 International License
Design and Implementation of Solar Powered Electric Vehicle for On-Campus University Applications
Ahmad F. Tazay1
1Assistnat Professor, Electrical Engineering Department, Al Baha University, Saudi Arabia.
Abstract:- The growing interesting in charging electric vehicle (EV) using renewable resources such as solar photovoltaic (PV) offers several technical, environmental, and economic chances. The objective of this paper is to improve efficiency, reduce greenhouse emissions, and increase driving range for the EV. The designing and implementing of a supportive renewable energy source to charge the EV are presented in this manuscript. The metrological data are measured in Al Baha University at Saudi Arabia to determine the optimal design of PV panels to operate the EV. The topology and sizing of each component of the system are provided in this paper. The modelling and designing of the developed PV system involve several procedures such as evaluating the dynamic load demand, analysing the power performance, and optimizing the size of PV system. The simulation results show that the modified EV could decrease the environmental emissions of Co2 by 420 Kg per year. The developed PV system can increase the driving range by 15 % at the heavy load demand. The experimental results show that PV system covers more than 70% of the total load demand and the battery banks required a single day to be fully charged. The developed EV system provides more reliability, sustainability, and environmentally friendly.
Keywords: Photovoltaic (PV), Electric Vehicle (EV), Co2 Emission, Driving Range Extension.
-
INTRODUCTION
The rapid development in manufacturing and production of electric vehicle (EV) gains more interesting in the future regarding environmental, technical, and economical opportunities. The impact of production of carbon dioxide (Co2) from fossil fuels on climate changes is currently one of the very high concern issues. Another issue is the economic challenges of using battery banks storage in automotive systems [1]. Renewable energy resources have been seen as a promising technology option for both EV's industry and transportation sector. The renewable resources contribute to charging of the batteries of EV which increases its lifetime and reliability. Using renewable resources instead of conventional electrical grid to operate the EV is conceived to improve the overall system efficiency and reduce the environmental harmful emissions [2].
Photovoltaic (PV) panels, comparing with other renewable resources, have been progressively recognized as competitive energy source technologies to charge EVs. Recently, PV systems have been used as a main source of energy to charge batteries due to several advantages such as lower maintenance and operation cost, low greenhouse gas emissions production, and energy independent capability [3]. Enormous research and technologies have been recently applied to charge EV using solar energy. large numbers of countries have been initiated
installation regulations and design standards for PV charging stations [4]. Authors in [5] addressed the present status and future challenging in the implementation of EV and charging systems. They also analysed the current challenging issues due to the massive deployment of EVs with several international standards and charging codes. Based on large number of applications and situations, batteries are charged by PVs charging station during the daytime when the EV is stopping in the parking area. This topology provides numerous benefits such as cost saving, shifting load demand, and low Co2 emissions [6]. The energy management strategy and designing of a closed-loop system controller were analysed in [7]. The authors did not mention the types of charging techniques and the influences on batterys behaviors. The control of a new topology of hybrid charge converter was presented in [8]. The hardware and software simulations were addressed and validated using vector control techniques to charge EVs battery. The disadvantages of charging EV using PV charging station include increasing the stress on the grid, limiting the EVs moving, and fluctuating charging duration.
Numerous aspects of EV charging techniques using PV energy supply were reported in literature. A review of different charging techniques for the EV using PV-gird connection and PV-standalone systems were presented in [9]. The designing of charging station at the University campus was presented in [10]. The authors evaluated the economic feasibility and system sizing of the charging station. However, the authors did not provide the hardware applications and the advantages of the proposed work. Tiano et al., evaluated the potential of install solar photovoltaic panels vehicle body [11]. The paper focused on only mathematical models and temperature impact without considering the collection of solar resource data. The experimental results and performance analysis of an electric golf cart with a 100W solar panel was given in [12]. The authors only implemented the experimental approaches without considering the simulation techniques.
This study addresses the following research shortage with regards to charging EV with PV panels for an educational campus. The paper designs and simulates the developed topology to meet the required load demand of the EV. The developed system is designed for use as an alternative transportation for students and employees at the campus of Al Baha University in Saudi Arabia. The motivation of this project is to integrate the PV panels onto the body of the EV to maximize the driving range and storages lifetime. The objective of this paper is to design and implement PV system
to charge and operate the EV instead of using conventional charging stations. The main advantages of this paper are to reduce energy demand on the grid, increase driving range duration of EV, and generate zero carbon footprint.
The rest of the paper is organized as follows. Section 2 provides the resources analysis and the system modelling. Section 3 addresses the simulation results of the developed model. It also indicates different case studies to validate the proposed system. Section 4 examines the developed system by applying the experimental results. The results and discussions are addressed in Section 5. The conclusion and remarks are provided in Section 6.
-
METEOROLOGICAL DATA AND SYSTEM ARCHITECTURE
The EVs system includes PV panels, DC/DC converter with charge controller, battery banks, and DC motor load. For the conventional golf cart system, the battery banks are charged using conventional AC/DC electric charger which is connecting to the main electric plug. The main problem of this procedure is that the charging socket is not available everywhere which limits operational and charging duration. This conventional model would limit the sustainability, and reliability of the EV. The developed model includes PV panels as a main energy source to charge the deep-cycle battery which improve the durational time and sustainability.
The main energy source is a monocrystalline solar PV panels which is used in this system because of its efficiency, lifetime, and economic advantages [13]. The frequent variation of sun irradiance and ambient temperature may affect the energy efficiency. Hence, DC/DC charge controller is used to maintain stable energy flow. The deep cycle batteries are also implemented as energy storage because of starting and running advantages. The block diagram in Fig. 1 shows the system structure of the EV.
Fig. 1. Schematic diagram of the EV (golf cart) using PV energy source.
-
METEOROLOGICAL DATA
The output power of PV panels depends on the amount and intensity of solar irradiance as well as the temperature degrees. These factors are varied due to the latitude location around the world, season, time of day, and altitude. The meteorological data for the selected location at Al Baha University are provided in Fig. 2 and Fig. 3. The location of the desired
campus at Al Baha University is Latitude 2011 N and longitude 41 38 E.
Fig. 2. Monthly average solar irradiation at the selected location.
The meteorological data for the campus of Al Baha university is obtained from NASA website and King Abdullah City for Atomic and Renewable Energy KACARE [14], [15]. The average monthly variation of solar energy is given in Fig. 2. The peak solar irradiation occurs during the summer season with almost 7.26 kWh/m2. The average monthly solar irradiation plays an important role in generating the required energy. The winter season shows the lower solar irradiance with almost 4.76 kWh/m2. Hence, the yearly average monthly solar irradiance at the selected location is 6.13 kWh/m2. Fig. 3 shows the average monthly temperature at the universitys campus. The average monthly temperature at Al Baha University is 25.16°C. The PV panels could produce maximum efficiency between 15°C and 35°C. So, the PV panels would produce the maximum efficiency during the months at selected location.
Fig. 3. Monthly average temperature at the selected location.
-
SOLAR PV PANELS
The PV panels absorb the solar irradiance and convert it into direct current to charge the battery banks. The PV current depends mainly on solar irradiance which is varied during the day while the temperature impacts on the voltage. So, the PV should operate at specific point called maximum power point (MPP). This operating point provides a maximum output power by regulating the voltage and current of the PV panels.
The selected PV panel is manufactured by Trina Solar company (TSM-350) with efficiency of 18%. The datasheet of the PV panel is provided in Table 1 [16]. At the standard test condition of irradiance 1000 W/m2, cell temperature 25 °C, and air mass AM1.5, the PV panel could generate of 350 W, 38.7 V, and
-
A. The PV characteristics at different irradiance is simulated in Fig. 4. The changes in solar irradiance result in
nonlinear behavior of both IV and PV curves. In order to generate the maximum power from the PV, there exists a single operating point that the PV should be operated on. Because of dynamics of solar irradiance, temperature, and loads, a maximum power point tracker (MPPT) is needed to ensure that the maximum power is extracted from the PV and the PV is operated at MPP.
Fig. 4. The behavior of a PV panel under varying irradiance and temperature:
-
The IV curves under varying irradiance and (b) the PV curve under different irradiance.
-
-
-
DC/DC CHARGE CONVERTER
A DC/DC charge controller is an electronic device that regulates the output dc power. The main function of a DC/DC charge controller depends on stepping up and down the output PVs voltage and current to regulate the output PVs power and achieve MPPT. Basically, buck-boost (step-up/step-down) DC/DC converter is used as a charge controlling device to regulate the maximum power output. The MPPT algorithm varies the electrical operating point at DC/DC converter to deliver maximum available power of PV panels. The DC/DC converter also measures the state of charge (SOC) of battery banks for protection of overcharging procedure. The advantages of charge controller include increasing power efficiency, improving system sustainability, and increasing batterys lifetime.
The solar irradiance is varied during the day which results in different power generation. This specific operating would
negatively effects on the batterys charging procedure and decreases its lifetime. So, MPPT algorithm is implemented to overcome the unstable PV panels energy. Various MPPT techniques are used, such as the perturb and observe (P&O) the incremental conductance (IC), and hill climbing (HC) [17]. IC among other MPPT methods has the benefits of fast dynamic performance [8]. In the relation between power/voltage of the PV, the MPP is located at the top of each plot when the gradient is zero. The derivation of IC algorithm (1) is given as:
= 0,
= + { > 0,
< 0,
(1)
The output power, voltage, and current are measured and used to implement the IC method. The output signal of the IC algorithm is used to regulate the switching transistor of the DC/DC converter. The output of the MPPT is a duty cycle D signal which further regulates the output dc voltage to achieve MPP. The detailed information of using MPPT algorithm is addressed in [8].
The DC/DC converter with charge controller is selected to be a buck-boost (step-up/step-down) type of converter. The DC/DC converter regulates the PV output voltage to 36 V which is the required batterys voltage. The rated power of the converter is 720 W with a maximum charging current of 30 Ah. The technical data of the DC/DC charge controller is given in Table 1 [18].
-
BATTERY BANKS
Battery banks are used for operating and running the motors load. A deep-cycle battery is used instead of conventional starting battery for the starting and running advantages. The deep-cycle batteries can provide a steady amount of current over a long period of time. They also have a long lifetime period even with repeatedly discharging and recharging procedures [19]. The size of the battery depends on the loads requirement. Since the rating power of a motor load is 2 Hp, the sizing of battery banks should be more than at least twice the rated load This is because the high rating of batteries would increase the driving range and cover the starting current of the
Table 1. System parameters and characteristics of the EV.
Component
Characteristics
PV
Company
Efficiency
Vmpp
Impp
Pmpp
Voc
Isc
TallMaxx TSM-350
18 %
38.7 V
9.04 A
350 W
47 V
9.6 A
DC Motor
Company
Class
V
I
Pmech
Pelec
Rating
Advanced DC Motors INC.
H
36 V
42 A
2 HP
1.5 kW
AU2500 Fleet Speed
Battery
Company
Type
Vrated
Inominal
Pnominal
Weight
Vcharged
AEC Deep Cycle
Sealed Lead Acid
12 V
100
Ah
1.2
kWh
28.5 Kg
13.6 13.8 V
DC/DC
Converter
Company
Type
Vrated
Irated
Prated
Efficiency
Temperature
LDSolar
buck-boost
36 V
30 A
720 w
99%
-40 to 70 C
motor. The optimal size of the batterys capacity of the is measured based on the total load demand, economic limitation, and discharge capability.
A sealed lead acid deep-cycle battery is used as battery bank to operate the motor load. Three batteries are connected in series as a battery bank with a rating of 12 V and 100 Ah So, the total
rating of a battery bank that feed the motor load is 36 V, 100 Ah, and 3.6 kWh. The characteristic of the selected battery is given in Table 1 [20].
-
DC MOTOR
The main element to drive the EV is a DC motor. The DC motor converts the electrical energy into mechanical energy to move the tires of the EV. The electrical energy is supplied from the battery banks while the mechanical energy is used for moving the EV. The relation between the electrical and mechanical energy is given in the followings [21]:
= 1 ( × )
(2)
= 1 ( × + × )
(3)
= ×
(4)
= ×
(5)
= 1 ( × )
(2)
= 1 ( × + × )
(3)
= ×
(4)
= ×
(5)
where, Ke (V/red/s) is an electromotive force constant; Kt (N.m/amp) is a motor torque; R () and L (H), are electric resistance and inductance, respectively; j (kg.m2) is moment of inertia of the rotor;
The 2008 E-Z-Go golf car is selected as EV for this project. The DC motor is driven by a 36V, 2 hp DC motor fed by 3 deep cycle batteries. The total load demand is represented by the DC brush motor output power and the auxiliary components. The DC motor consumes a large amount of the total energy while the gear controller is used to regulate the direction of the motors shaft. Hence, the motors controller regulates the wheel torque which decreases the velocity of the DC motor. Based on the manufacture of the EV, the DC motor has a maximum power of 1.5 kW and maximum velocity of 20 km/h.
SIMULATION RESULTS
To verify the robustness of the developed system, three case studies have been carried out. The developed system includes EV with 1.5 HP DC motor, PV panel, three deep cycle batteries, and DC/DC converter. The golf cart represents EV which is manufactured in 2008 by E-Z-Go company. The total weight of the EV is 360 Kg, and the electrical characteristics of DC motor load are 1.5 kW, 36V, and 42 Ah. The PV panel is the main source of energy which has a rating of 350 W, 38.7 V, and 9.04
A. The deep cycle battery bank consumes the output energy from PV to operate the motor load. The electrical ratings of the battery banks are 36 V, 100 Ah, 3.6 kWh. In order to generate the maximum power from the PV, DC/DC buck-boost converter is used to apply MPPT using IC algorithm.
The developed system is first simulated using computer-aid software before experimental applications. Hence, Matlab/Simulink is used to examine the MPPT algorithm, dynamic response of the load, and PV charging procedure. The screenshot of the system is shown in Fig. 5.
Fig. 5. Schematic diagram of the developed system of EV using Matlab/Simulink software.
-
CASE 1: PV WITH MPPT ALGORITHM
In the simulation model, PV panel generates a maximum power of 350 W when a solar irradiance is 1 kW/m2. The voltage and current at MPP are 38.7 V and 9.04 A, respectively. When the solar irradiance is varied during the day, the MPP is changed based on MPPT algorithm. The characteristic of the PV panel for the different solar irradiance is shown in Fig. 6. The role of MPPT algorithm is to follow the MPP for the different solar irradiance. Hence, the signal of the duty cycle is varied to regulate the switching signals of the DC/DC converter.
Fig. 6. The behavior of a charging the EVs battery banks using PV panel under varying irradiance and temperature: (a) The variation of solar irradiance during a day, (b) the output PVs power under different irradiance, and (c) the performance of batterys voltage.
The measurement of actual solar irradiance is first calculated on 17th of January 2021. The solar irradiance is then simulated using computer-aided software to examine the validation of MPPT method and charging dynamics of the battery. For the simplicity purpose, each hour of the selected day represents one interval second of the simulation software. Fig. 6 (a). shows the solar irradiance during the day when the daylight last for eleven hours. The solar irradiance of the system is started from 150
W/m2 until 80 W/m2 at the end of the day. The output power of the PV panel is varied regarding the variation of solar irradiance as can be seen in Fig. 6 (b).
Fig. 7. The dynamic performance of the EVs motor load: (a) dynamic behavior of the motors speed, (b) dynamic response of different the motors torque, (c) the output injected power from the battery banks, and (d) the SOC of the battery during charging and discharging modes.
The initial SOC of the battery is 50% where the voltage is 35.8
-
At the first second, the solar irradiance is almost zero and the PV system is not charging the batteries. After the first second, the solar irradiance is rising, and the PV power is increased. So, the SOC and voltage of the battery are increased as can be seen in Fig. 6 (c). and Fig. 6 (d). The battery voltage is increased from 35.8 V to 36.7 V while the batterys SOC is increased from 50% up to 50.04%. This charging procedure is occurred during the actual measuring power and solar irradiance at the selected day of the year. So, the PV system can provide almost 1.8 kW during the day to charge the battery. This power represents 50% of the batterys rating.
-
-
CASE 2: MOTOR DYNAMICS
The dynamic results of the DC motor load are simulated using computer aided Matlab/Simulink. The performance of charging battery banks with PV system has been tested with variation in speed and loads torque at t= 3, 6, 8, and 12 seconds. Before the EVs starting, the PV panel charges the battery banks with 350 W at 1 kW/m2. The torque and speed of the motor is zero because the EV is at standstill. During the high demand on the motors torque, the PV and batteries share the power to the load as can be seen in Fig. 7. At time t= 3 seconds, the motor is started at full speed with no torque which results a speed of 300 rad/sec. At this time, the PV panel still charging the battery since the torque is almost zero. The variation in load torque is shown in Fig. 7 (b) from initial value of 20 Nm, 40 Nm, and 60 Nm at time t= 6, 9, and 12 seconds, respectively. Since the motors load required more power than the output power from the PV during the high torque, the battery banks supply the load demand with 400, 1000, 1600 W at varied torques.
The batterys SOC is shown increasing during the charging period when the load is not running. However, Fig. 7 Shows that the SOC is decreasing during the increasing of the motors
load. At different torques, the SOC is decreasing with respect to the torque value. At starting speed of 50 rad/s at a torque of 45 Nm, battery shows a huge decrease in SOC because of the high armature current demand. The simulation results demonstrate a good dynamic response of the developed PV system performance even with the high load demand.
-
CASE 3: EV WITH AND WITHOUT PV PANELS
For a demonstration of important of PV source, this case study provide the advantages of installing PV panels to increase the charging range of the battery at different loads demand. The motors dynamic performance and batterys voltage with SOC are provided in Fig. 8. As shown, the simulation results with and without the PV panels are recorded and compared for this analysis. The batterys SOC runs at 80% with different torques modes. The PV panel charges the battery with a rated power of 350 W which increases the batterys voltage. When the motors demand is less than the PV power, the exceed power is used to charge the battery as given in Fig. 8 (b). However, the PV and battery share the moors demand when the load demand is more than the output power from the PV panel. This feature can preserve the batterys voltage and increase its lifetime. As shown in Fig. 8., the batteries continuously provide the loads power to the EV a significantly longer time due to the injected energy from the PV panel.
Fig. 8. The dynamic performance of the EVs using with and without PV source: (a) dynamic behavior of the motors speed, (b) dynamic response of different the motors torque, (c) the measured battery banks voltage, and (d) the SOC of the battery during charging and discharging modes.
When the PV panel is not connected, the battery banks are the only responsible to provide the required load demand. The batteries voltage level dropped about 15% faster when the PV panel was not connected. However, the PV continuous recharging of the batteries which prevented them from going into a deep discharging phase as can be seen at the SOC in Fig. 8 (c). The measured performance of the batterys voltage and SOC with and without the PV panel were compared in Fig. 8 (d). As shown, there is 15% increase in the batterys voltage a result of installing the PV panel.
IV. HARDWARE APPLICATIONS
The golf car is selected as EV to test the methodology and simulation approaches at the campus of Al Baha University. The EV is driven by 36V, 2 hp DC motor which is fed by 3 deep cycle, 12V sealed lead acid batteries. The PV panel is used as the main source to charge the battery banks by connected to DC/DC converter to implement MPPT algorithm. Several factors that impact on the total load which includes vehicles weight, the maximum starting and running speed, and the travelled distance per trip. The experimental application for the developed EV system is given in Fig. 9.
The implementation procedure of the modified EV is as:
-
Replace the EVs roof with PV panel.
-
Change the lead acid battery banks with deep cycle batteries.
-
Regulate DC/DC charger converter with MPPT feature to charge the batteries.
-
Calculate the total load consumption during the year.
The rage top of the EV is first replaced by the PV panel as the main source of energy. The sunroof top has a dimension of 2345 * 1172 mm with a weight of 15 Kg. The PV panel has dimension of 1960 * 992 mm with a weight of 26 Kg. Since the total weight of the golf car is 360 Kg, the PV panel will increase the total wight by 3% which has no significant impact on the motors torque.
Fig. 9. Hardware implementation of the modified EV.
Three deep cycle batteries are used to provide the required load demand. Each battery has a weight of 28.5 Kg that is a total battery banks of 85.5 Kg. The battery banks will increase the total weight of the EV by 23%. However, the high-power rating of the batteries would limit the modified weight enhancement since the battery rating is more than three times the required load demand. The three deep cycle batteries would increase the moving range by 50% since they can generate 3.6 kWh while the required load power is 1.5 kWh.
The moving range of the EV is measured for one year to examine the durability of the modified EV. The average daily use of the EV is about 1.73 kWh/day with a peak of 0.4 kW. The EV occurs between 7 AM and 5 PM when the students join their school while the employees go to their job. The annual
load demand is provided in Fig. 10 with a heavy load consumption occurs during the school semesters. However, the load consumption is decreased during the summer semester when the Universitys employees and staff are the only ones who use the EV.
The sunlight at the day of 17th January 2021 is last for 9 hours which is varied regarding to its solar irradiance. By converting the actual solar irradiance into energy at the selected day and location, the PV panel received about 6.094 kW/m2/day. Using the energy efficiency (18%) of the installed PV panel in Table 1, the actual output power from PV panel to charge the battery is 1.096 kW/day. The EV load demand is considerably less than the energy output of the PV panel. Since the load demand is about 1.73 kWh/day, the PV panel shares more than 70% of the total load while the battery contributes to sharing the rest required load demand. So, the extra energy produced by the PV panel was utilized to keep the battery fully charged which increase its lifetime. The developed model also increases the sustainability and durability of the EV since it does not need for external charging. The PV is connected to the battery banks via DC/DC charge controller to provide Maximum Power Point Tracking (MPPT). The charge controller is used to extract the maximum power and monitors the state of charge of the batteries as well as regulate the power flow.
Fig. 10. Yearly load demand at the selected location.
-
RESULTS AND DISCUSSIONS
The results of simulation and hardware implementation are addressed to test the performance of EV and power flow of the developed system. The dynamic response of the DC motor is compared with and without the PV system. The analysis of both systems with and without the PV panel shows that the batteries voltage level drops faster by 1.3 times. In contrast, the output power from PV panels extends the discharge time and prevent the battery banks from deep discharging period. When the sunlight is low or the batterys voltage is high, the DC/DC charge controller prevents battery banks from overcharge or discharge modes. The advantages of the PV system can extend the lifetime of the battery and increase its protection.
Table 2. Featured comparisons between conventional gold cart and modified EV.
Element
Conventional Golf Cart
Modified EV
Features
EVs structure
Weight
Roof
Weight
Roof
Increasing the total weight by 25% while providing shading advantages.
360Kg
Sunroof top
450 Kg
PV module
Charging source
Fossil fuel electric grid
Solar energy
Reducing Co2 emissions
Battery Banks
Three lead acid
Three deep cycle lead acid
Increasing moving range by 50%.
Charger
AC/DC converter
DC/DC converter with MPPT
Increasing energy efficiency and protection.
The modified EV uses PV panel as a main source of energy to charge deep-cycle batteries using DC/DC charge controller with MPPT features. Although the load demand of the EVs motor much higher than the charging power of the solar PV system with 1500 W comparing with 350 W, the total energy consumption is not very high due to the short intervals operations during the day. In addition, the EV depends on only the moving demand from point to point of the students and employees at the Universitys campus. The simulation and experimental results addressed that daily energy consumption is about 1.7 kWh. So, the roof top of the PV panel converts the solar energy into mechanical energy to run the EV. So, it can be concluded from the feasibility analysis that that the electrical energy generated from by the PV system can cover daily load demand for the EV users at the selected location. It can also charge the battery banks during the moving period. This procedure covers 70% of the load demand when the battery banks need only a single day to be fully charged. It is worth to mention that the meteorological data and experimental analysis are examined at the worst case of solar irradiation that is on 17th of January. This feature improves the moving range of the EV when the golf cart was running under the sunlght.
The environmental analysis of greenhouse gas emissions is compared with the charging of the EV using PV panel and external utility grid which is generated by fossil fuels. The annual load demand of the EV is first provided by external utility grid which generates 420 Kg/year of Co2 emissions. Using PV panel as the main source, this harmful can be reduce and the generated Co2 emission is zero. This advantages of the developed system for the EV will result in a significant annual emission reduction of Co2.
In comparisons between the conventional golf cart with the modified EV, Table 2 shows the features of implementing the PV system. The PV panel is mounted at the top of the EV which increase the moving range. It also can provide charging features while the car is moving as well as offering sunlight shading advantages to the passengers. As provided in Table 2, the EV generates zero Co2 emissions since it can be powered by PV panel only. The solar irradiation at the selected university continues for about 9 hours each day. The extra PV energy charges the battery banks. So, the PV system would increase the moving range without the need for external charge stations.
-
CONCLUSION
A 2 HP golf cart represents the EV to be used for students and employs at the campus of Al Baha University, Saudi Arabia. The solar system includes PV panel, three deep-cycle battery banks, and DC/DC charge controller with MPPT features. The metrological data are analysed by considering solar radiation and temperature at the desired location. The dynamic
performance of the modified EV is simulated using Matlab/Simulink with experimental applications. Three case studies have been examined to validate the dynamic performance of the system. A 350 W of PV panel is mounted at the top of the EV to charge three deep-cycle battery banks with a rating of 3.6 kWh.
The analysis results show that the PV system installed on the EV can produce enough electrical energy to power the car under the different weather conditions. The PV system can also increase the moving range and limits the charging periods. It also increases lifetime of batteries and improve the overall sustainability. The environmental results show that the PV system can reduce 420 Kg of greenhouse Co2 emission since it does not require external charge from fossil fuels. It can be concluded that the modified EV is technically viable, reliable and environmental friendly.
REFERENCES
-
Schwarz, M., Auzepy, Q., & Knoeri, C. (2020). Can electricity pricing leverage electric vehicles and battery storage to integrate high shares of solar photovoltaics?. Applied Energy, 277, 115548.
-
Shariff, S. M., Alam, M. S., Ahmad, F., Rafat, Y., Asghar, M. S. J., & Khan, S. (2019). System design and realization of a solar-powered electric vehicle charging station. IEEE Systems Journal, 14(2), 2748- 2758.
-
Khan, S., Ahmad, A., Ahmad, F., Shafaati Shemami, M., Saad Alam, M., & Khateeb, S. (2018). A comprehensive review on solar powered electric vehicle charging system. Smart Science, 6(1), 54-79.
-
Madhu, G. M., Vyjayanthi, C., & Modi, C. N. (2019, July). A Novel Framework for Monitoring Solar PV based Electric Vehicle Community Charging Station and Grid Frequency Regulation using Blockchain. In 2019 10th International Conference on Computing, Communication and Networking Technologies (ICCCNT) (pp. 1-7). IEEE.
-
Habib, S., Khan, M. M., Abbas, F., Sang, L., Shahid, M. U., & Tang, H. (2018). A comprehensive study of implemented international standards, technical challenges, impacts and prospects for electric vehicles. IEEE Access, 6, 13866-13890.
-
Khalid, M. R., Alam, M. S., Sarwar, A., & Asghar, M. J. (2019). A Comprehensive review on electric vehicles charging infrastructures and their impacts on power-quality of the utility grid. ETransportation, 1, 100006.
-
Savio, D. A., Juliet, V. A., Chokkalingam, B., Padmanaban, S., Holm- Nielsen, J. B., & Blaabjerg, F. (2019). Photovoltaic integrated hybrid microgrid structured electric vehicle charging station and its energy management approach. Energies, 12(1), 168.
-
Tazay, A., & Miao, Z. (2018). Control of a three-phase hybrid converter for a PV charging station. IEEE Transactions on Energy Conversion, 33(3), 1002-1014.
-
Ramadhani, U. H., Shepero, M., Munkhammar, J., Widén, J., & Etherden,
N. (2020). Review of probabilistic load flow approaches for power distribution systems with photovoltaic generation and electric vehicle charging. International Journal of Electrical Power & Energy Systems, 120, 106003.
-
Abdelsalam, M. A., Obaid, W., Ahmad, F. F., Hamid, A. K., & Ghenai,
C. Modeling and Simulation of a Solar Powered Golf Cart Charging
Station in Sharjah. In 2020 Advances in Science and Engineering Technology International Conferences (ASET)(pp. 1-4). IEEE.
-
Tiano, F. A., Rizzo, G., Marino, M., & Monetti, A. (2020). Evaluation of the potential of solar photovoltaic panels installed on vehicle body including temperature effect on efficiency. eTransportation, 5, 100067.
-
Guha, B., Haddad, R. J., & Kalaani, Y. (2015, April). Performance impact analysis of solar cell retrofitted electric golf cart. In SoutheastCon 2015 (pp. 1-2). IEEE.
-
Tazay, A. F., Samy, M. M., & Barakat, S. (2020). A techno-economic feasibility analysis of an autonomous hybrid renewable energy sources for university building at Saudi Arabia. Journal of Electrical Engineering & Technology, 15(6), 2519-2527.
-
Atmospheric Science Data Center [Internet]. NASA Langley Research Center; c2020 [cited 2020 December 18]. Available from: https://eosweb.larc.nasa.gov
-
Tazay, A. (2021). Techno-Economic Feasibility Analysis of a Hybrid Renewable Energy Supply Options for University Buildings in Saudi Arabia. Open Engineering, 11(1), 39-55.
-
TrinaSolar TallMaxx Plus [Internet]. TrinaSolar; c2020 [cited 2020 October 10]. Available from: https://www.trinasolar.com/us
-
Venkatramanan, D., & John, V. (2019). Dynamic modeling and analysis of buck converter based solar PV charge controller for improved MPPT performance. IEEE Transactions on Industry Applications, 55(6), 6234- 6246.
-
LDSOLAR TD2310 [Internet]. LDSOLAR; c2020 [cited 2020 October 10]. Available from: https://www.enfsolar.com/pv/charge-controller- datasheet
-
Chian, T. Y., Wei, W. L. J., Ze, E. L. M., Ren, L. Z., Ping, Y. E., Bakar,
N. A., … & Sivakumar, S. (2019). A Review on Recent Progress of Batteries for Electric Vehicles. International Journal of Applied Engineering Research, 14(24), 4441-4461.
-
AEC AEC12V-100Ah [Internet]. AEC; c2020 [cited 2020 October 10].
Available from: https://www.aecups.com
-
Sider, A., Amiri, A., Hassan, M. K., Radzi, M. A. M., & Toha, S. F. (2015). Mathematical design and analysis of anti-lock brake system for electric vehicle based on brake-by-wire technology. International Journal of Electric and Hybrid Vehicles, 7(4), 303-322.
-
Hafizah S, Ariffin S, Muazzah N, Latiff A, Khairi MHH, Ariffin SHS, et al. A Review of Anomaly Detection Techniques and Distributed Denial of Service (DDoS) on Software Defined Network (SDN). Technol Appl Sci Res [Internet]. 2018;8(2):272430.