
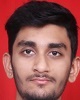
- Open Access
- Authors : Ayush Munot, Adarsh Bhavsar, Vaishnavi Wadhi, Y.A Kadam
- Paper ID : IJERTV13IS040104
- Volume & Issue : Volume 13, Issue 04 (April 2024)
- Published (First Online): 22-04-2024
- ISSN (Online) : 2278-0181
- Publisher Name : IJERT
- License:
This work is licensed under a Creative Commons Attribution 4.0 International License
Design and Manufacturing of a 4 Wheel Drive Gearbox of an off-road Vehicle (Atv)
Ayush Munot, Adarsh Bhavsar, Vaishnavi Wadhi, Y.A Kadam
Student, Department of Mechanical Engineering P.E.Ss Modern College of Engineering Pune, Maharashtra, India
Assistant Professor, Department of Mechanical Engineering P.E.Ss Modern College of Engineering Pune, Maharashtra, India
ABSTRACT
The purpose of this project is to conceptualize, design, and manufacture an advanced Four-Wheel Drive (4WD) system for an All-Terrain Vehicle (ATV), enhancing its off-road performance and maneuverability. The ATV is intended for recreational and utility purposes in diverse terrains, including rough trails, mud, sand, and rocky surfaces.
The proposed 4WD system aims to optimize traction, stability, and control by distributing power to all four wheels, thereby improving the vehicle's overall off-road capabilities. The design process involves a comprehensive study of existing ATV drivetrain technologies, a detailed analysis of terrain requirements, and the incorporation of innovative engineering solutions.
Key components of the project include the development of a robust transfer case, differential mechanism, and drive shafts to seamlessly transfer power from the engine to each wheel. Emphasis is placed on creating a system that adapts to varying terrain conditions, ensuring optimal torque distribution for improved traction without compromising on efficiency.
Computer-aided design (CAD) tools are employed for the creation of 3D models, allowing for virtual prototyping and
simulations to validate the system's performance under different scenarios. Finite Element Analysis (FEA) is utilized to assess structural integrity and durability, ensuring the 4WD system can withstand the harsh conditions associated with off- road use.
The manufacturing process involves the selection of high- quality materials and precision machining techniques to achieve the desired strength-to-weight ratio and durability. Prototypes are rigorously tested in controlled environments to validate the design's functionality and performance.
The successful implementation of the 4WD system is expected to result in an ATV with superior off-road capabilities, offering users a versatile and reliable vehicle for various recreational and utility applications. This project contributes to the advancement of ATV technology, showcasing innovative solutions for enhancing off-road mobility and expanding the range of activities achievable with these vehicles.
Keywords: Research Paper, Technical Writing, Science, Engineering and Technology
I. INTRODUCTION
The design and manufacturing of a Four-Wheel Drive (4WD) system for an All-Terrain Vehicle (ATV) represents a pivotal project aimed at elevating off-road mobility to new heights. The significance of 4WD technology in off-road vehicles cannot be overstated, as it plays a fundamental role in enhancing traction, stability, and maneuverability across diverse terrains.
This project undertakes a comprehensive exploration of the engineering intricacies involved in creating a cutting-edge 4WD system, from conceptualization to prototyping and validation.
Off-road enthusiasts and utility operators demand vehicles that can navigate challenging terrains with finesse. The conventional Two-Wheel Drive (2WD) systems often fall short in providing the necessary traction on uneven surfaces, limiting the ATV's overall off-road potential.
The implementation of a 4WD system aims to address these limitations by distributing power to all four wheels, thereby improving grip and control.
1.1 Objectives:
The primary objective of this project is to design and manufacture a 4WD system that not only meets but exceeds the expectations of off-road enthusiasts and utility users. Key objectives include optimizing power distribution, ensuring adaptability to varying terrains, enhancing vehicle stability, and incorporating intelligent control systems for dynamic performance adjustments.
contact the conference publications committee as indicated on the IJRSET website. Information about final paper submission is available from the IJRSET website.
-
KEY COMPONENTS OF THE 4WD SYSTEM:
-
Transfer Case: The transfer case serves as the core component responsible for directing power from the engine to the front and rear axles. Its design focuses on efficiency, durability, and the seamless transition between 2WD and 4WD modes.
-
Gears and Gear Train: The gearbox incorporates a complex arrangement of gears and a gear train to transmit power from the engine to the wheels. These gears are meticulously designed to provide the necessary torque and speed ratios required for various driving conditions. Gear ratios can be adjusted to optimize performance for tasks such as climbing steep inclines, traversing rough terrain, or achieving higher speeds on flat surfaces.
-
Differential Mechanism: The differential is engineered to manage torque distribution between the front and rear wheels. A limited-slip differential is integrated to accommodate varying wheel speeds, preventing wheel slippage and optimizing traction.
-
Input and Output Shafts: The input shaft connects the gearbox to the engine's crankshaft, transmitting power into the gearbox. The output shafts extend from the gearbox to the front and rear axles, delivering power to the wheels. These shafts are essential for ensuring a direct and efficient transfer of torque, contributing to the vehicle's overall responsiveness and drivability.
-
Drive Shafts: Precision-engineered drive shafts transmit power from the differential to each wheel, ensuring a direct and efficient power transfer while accommodating suspension movements.
-
-
COMPUTER-AIDED DESIGN (CAD) AND SIMULATION:
Advanced CAD tools are employed to create detailed 3D models of the 4WD system. Simulation techniques, including Finite Element Analysis (FEA), are utilized to assess the structural integrity and performance of the components under different loads and terrain conditions.
-
Adaptive Control System: Intelligent control systems, driven by data from sensors such as accelerometers and wheel speed sensors, enable real-time adjustments to the 4WD system. This adaptive control enhances traction, stability, and responsiveness, contributing to an optimal off-road driving experience.
-
Manufacturing Process: The manufacturing process involves selecting high-strength materials and utilizing precision machining techniques. Prototypes undergo rigorous testing to validate the design's functionality, structural integrity, and durability, ensuring the final product meets the demands of off-road environments.
-
Sealing and Durability: Given the demanding nature of off-road driving, 4WD gearboxes are designed with robust sealing mechanisms to prevent the ingress of water, mud, and other contaminants. Additionally, they undergo rigorous
testing to ensure durability under extreme conditions, including temperature variations, shocks, and vibrations.
-
-
PROBLEM STATEMENT.
Design a robust, efficient 4wd powertrain for a 10bhp BAJA ATV, including gearbox, differential and propeller shaft. The design should have optimized power transfer, adaptablity to off-road terrain, durability and acceleration.
ENGINE RPM: – 3800RPM ENGINE TORQUE: – 18.69 N/mm TARGET SPEED: – 58KM/HR
-
SCOPE:
-
Sustainable Consideration: Explore opportunities to make the transmission system more energy efficient.
-
Continual Improvement: Consider opportunities for future enhancement and refinement to the 4WD transmission system. Stay updated with technological advancement in the field
-
Lightweight Material: Integrating lightweight material like advanced composites, aluminium alloys, into the transmission system can reduce overall vehicle weight leading to full efficiency and performance.
-
-
Methodology:
Designing a 4WD gearbox for an off-roading vehicle involves defining specific requirements, selecting an appropriate transmission type with suitable gear ratios for diverse terrains, and incorporating a transfer case for varied gearing options. Material choice is crucial for durability, considering the challenging conditions off-road vehicles face. Implementing effective sealing, ensuring torque handling capacity, and conducting rigorous testing and simulation are vital steps. A well-designed cooling system is necessary for heat management during extended off-road use. Considerations should include weight, cost, and prioritizing maintenance and serviceability to ensure a robust and practical gearbox design.
-
-
CALCULATIONS: –
Engine Rpm = 3800 rpm
Consider the target speed = 56km/hr = 15.56m/s Dimension of wheel = 23×7-10
Wheel end RPM = = x15.56
=508.7
-
Continuous Variable Transmission (CVT) Low end Ratio:- 3.9
High End Ratio:- 0.9
-
Gear box Ratio :- = = 8.29 No. of Stages of Gearbox = 2
By taking square root, Stage 1 = 2.879
Stage 2 = 2.879
Maximum Engine Torque = 18.69 Nm
=18690 Nmm
Final Drive Ratio = Low end ratio x Gearbox Ratio
= 3.9 x 8.29
= 32.331
Torque on input shaft (Tin) = 18690 x 3.9 [Engine Torque x Low end ratio] = 72891 Nmm
-
Material Used: – 20MnCr5
-
Lewis form factor Y=0.484 – = 0.3405
Y=0.3405
-
Beam Strength Where, m=module
B=face width=10m
= Sut/3, Permissible Bending Stress N/mm2 Y = Lewis form factor
Q=
K = 0.16 x[ ] 2 = 0.9840
-
Wear strength
-
-
Sw = b x Q x dp x K [dp = PCD of pinion = zp * m]
Sw = 1170.64512 N
For Input Shaft :-
Pt=
20MnCr5 steel is commonly used in the production oWf here, Pt=Tangential Component gears due to its ability to be case-hardened and itPs r = Pt * tan
excellent wear resistance. This makes it well-suited for
gears that are exposed to high levels of wear and tear.
= 3644.55 x tan20
= 1326.507 N
Sut = 980 N/mm2 Syt = 750N/mm2 BHN = 248
Where,
Sut = Ultimate tensile strength Syt = Yield strength
Consider module of spur gear (m) = 2mm & No. of Teeth on Pinion (Zp) = 20
No. of teeth on gears (Zg) = Zp x Stage 1 ratio
= 20 x 2.8979
Where, Pr = Radial Component For Stage 1 [For spur gear]
Zp = 20
Zg = 58
m = 2
Similarly, for Stage 2 Zp = 20
Zg = 58
m = 2
As the ratio is same for stage 1 and stage 2
Zg = 58
= 57.58
Now,
Torque on Intermediate Shaft (Tint)
Let,
= 72891 x 2.879
Pressure Angle =
= 200 — (
) =209853.1789 Nmm
Pt =
Pr = Pt x tan(20) = 38190.157
Bevel Gear Calculation :-
Consider module =3mm
Zp = 16
Going by the ratio of 1.25
Zg = 20
Material used is same
Sut = 980 N/mm2 Syt = 750N/mm2
on pinion]
on gear]
Consider = 20 ——–[Pressure angle] [V.B
Bhandari]
Pitch Cone Distance Ao =
=
[Pitch cone angleAo = 38.41 mm
or 10m
=12.80 or 30
[Pitch cone anglCe onsidering smaller valueB = 12.80 13mm
Fb = ——————
Zp = = 20.48 [virtual number of teeth on pinion]
Zg = = 32.01 [virtual number of teeth on gear]
Fb = 2897.58N
Yp = 0484 – = 0.3438 — [Lewis form factor on Virtual
-
Wear Strength: –
number of teeth]
dp = m x zp =48 dg = m x zg = 60
Ratio Factor (Q) =
Load Stress Factor (K)
= 0.16 2
Pt = where Tp = Torque on Int (Pinion) Rpm Mean Radius of
Fw =
Pinion.
Rpm = 19.94 mm , Tp = 209853.189 Nmm Pt = 10524.23N
Separating Force = 3830.50 N
Pa = 2392.38 N (Axial Component)
Pr = 2991.53 N (Radial Component)
Pa = 10524.23 N (Tangential Component)
RPM =
Pr = Pt x tan x cos N
Pa = Pt x tan x sin N
-
INPUT SHAFT :-
*(Dimensions are in mm)
Pt = 3644.55 N Pr = 1326.50 N Total Length (L) = 14+20+20+4+14+14+93
=179 mm
Material used :- 20MnCr5
Sut = 980 N/mm2 Syt = 750N/mm2
Kb = 2.0 [Combined shock and fatigue factor applied to bending] Kt = 1.5 [Combined shock and fatigue factor applied to torsional moment]
Possible Shear Strength
0.3 x Syt = 225 Mpa
0.18 x Sut = 0.18 x 980 = 176.4 Mpa
Material selected is 10C4
Choosing the lower value,
Force Analysis
= 132.3 N/mm2
For Output Shaft
Torque on output shaft =Mt=604166 Nmm Diameter of Shaft at gear location = 35 mm Hence Sq. key dimension of shaft =b x h=16 x10
-
For vertical plane – For horizontal plane Ra = 480.287 N Ra = 1319.578 N
Rb = 846.22 N Rb = 2324.972 N
Mmax = 17771 Nmm Mmax = 48824 Nmm Resultant
Ra = = 1404.2655 N
Rb = = 2474.1833 N
Mmax = = 51957.592 N
Moment Torsional: –
Mt = Mt = 72891 Nmm
-
Diameter of Shaft
d3 =
=
d3 =5806.681
-
-
Design of Key
-
Intermediate Shaft :
Torque on Intermediate shaft = Mt = 209853 Nmm.
As face width of our gear is 20mm and length of the key is approx. 61 mm
-
-
Bearing Selection :-
-
For Input Shaft:
From SKF Catalogue, available bearings (DGBR) for bore diameter 20 mm are : 6004,6204,6304,6404
-
Selection Procedure for B1 :
As the gear is spur gear, there will be no axial forces acting on the bearings.
Hence, Pe = x * Fr where x = 1
Pe = 1 * 1404.2655 Fr = Ra
= 1404.265 N
L10 = ————- L10h range (12000-20000 h
V.B Bhandari
= n = Input shaft RPM
For square key dimension of the key for shaft diameter (3038)mm
= 935.376 rev
B x h = 10 x 8
Now, C = Pe * (L10)1/P P = 3 for ball bearing
=
= 13733.39 N = 13.73 kN
From SKF Catalogue , Bearing no. 6304 has C = 16.8 kN. Thus , selecting 6304 for bearing B1
B1 = 6304
-
-
-
Selection Procedure for B2 :
Hence, Pe = x * Fr where x = 1
Pe = 1 * 2474.18 Fr = Ra
= 2474.18 N
L10 = 935.376 rev From previous calculation C = Pe * (L10)1/P P = 3 for ball bearing
=
= 24196.91 N = 24.196 kN
= 79084.88 N = 79084.88 kN
From SKF Catalogue, Bearing no. NJ 2307 ECP has C = 106 kN. Thus , selecting NJ 2307 ECP for bearing B2
B2 = NJ 2307 ECP
-
-
DESIGN AND ANALYSIS
<>From SKF Catalogue, Bearing no. 6404 has C = 30.7 kN. Thus , selecting 6404 for bearing B2
B2 = 6404
For Output Shaft :-
From SKF Catalogue, available bearings (DGBR) for bore diameter 35 mm are : N 207 ECM, N 307 ECM, NJ 2307 ECP
-
Selection Procedure for B1 :
As the gear is spur gear, there will be no axial forces acting on the bearings.
Hence, Pe = x * Fr where x = 1
Pe = 1 * 6723.01 Fr = Ra
= 6723.01 N
L10 = ————- L10h range (12000-20000 h
V.B Bhandari
= ———– n = Input shaft RPM
= 488.64 rev
Now, C = Pe * (L10)1/P P = 10/3 for ball bearing
=
= 43078.48 N = 43.078 kN
From SKF Catalogue , Bearing no. N 207 ECM has C = 56 kN. Thus , selecting N 207 ECM for bearing B1
B1 = N 207 ECM
-
Selection Procedure for B2 :
Hence, Pe = x * Fr where x = 1
Pe = 1 * 12342.319 Fr = Ra
= 12342.319 N
L10 = 488.64 rev From previous calculation C = Pe * (L10)1/P P = 10/3 for ball bearing
=
Figure 2: – Part assembly of gearbox
Fig 3 :- Part assembly of gearbox with bevel gear
Fig 4:- Stress concentration of Spur gear
Fig 5:- Total deformation of Spur gear
Fig 10 :- Differential assembly
Fig 6:- Stress concentration of Output shaft
Fig 7 :- Total deformation of Output shaft
Fig 8 :- Total deformation of Intermediate shaft
Fig 9:- Stress deformation of Gearbox Casing
-
-
CONCLUSION :-
At this stage we are done with the designing, modelling and analysis of 4WD gearbox of an off road vehicle. We are planning to start our manufacturing phase in the last week of December. We have set January 30th as the deadline of our manufacturing phase and are planning our activities accordingly.
-
REFERENCES :-
-
V.B Bhandari 4th Edition.
-
Design and analysis of 4WD 2-stage reduction gearbox for mBAJA buggy using finite element method (FEM). Sudhanshu Maurya1, Vineet Gupta2, Mukesh Yadav
-
Design, analysis, and simulation of a four-wheel-drive transmission for an All-terrain vehicle.
C. Kannan School of Mechanical Engineering (SMEC), VIT University, India
B. Ashok VIT University, India
Harshad Dighe, Saksham Agarwal, Devansh Kapoor, Akshat Kasana, and Amal Mathew School of Mechanical Engineering (SMEC), VIT University, India
-
Differential Transfer Cases in AWD/4WD Vehicles: Comparative Analysis SOHAM S. KULKARNI Department of Mechanical Engineering, PVG COET, Pune-3.
-
Automotive Transmissions by Wolfgang Novak.
-
Textbook of Machine Design by R.S.Khurmi and J.K.Gupta.
-
Mechanical Engineers Handbook by Dan.B.Marghitu.
-
Machine elements in Mechanical Design by Robert.L.Mott.
-
Tune to Win by Carroll Smith.
-
Strength of Material by S. Ramamrutham
IJERTV13IS040104
(This work is licensed under a Creative Commons Attribution 4.0 International License.)