
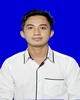
- Open Access
- Authors : Riyki Apriandi, Harus Laksana Guntur, Muhamad Nizar Zilmi
- Paper ID : IJERTV12IS110203
- Volume & Issue : Volume 12, Issue 11 (November 2023)
- Published (First Online): 08-12-2023
- ISSN (Online) : 2278-0181
- Publisher Name : IJERT
- License:
This work is licensed under a Creative Commons Attribution 4.0 International License
Design and Numerical Study Crashworthiness of Two Passenger Electric Vehicle Front Bumper System
Riyki Apriandi
Mechanical Engineering Institut Teknologi Sepuluh Nopember
Surabaya 60111, Indonesia
Harus Laksana Guntur Mechanical Engineering
Institut Teknologi Sepuluh Nopember Surabaya 60111, Indonesia
Muhamad Nizar Zilmi Mechanical Engineering
Institut Teknologi Sepuluh Nopember Surabaya 60111, Indonesia
Abstract In this research, a 3D model of the front bumper system for a two-passenger electric vehicle was designed, consisting of a bumper beam and a crash box. There are six crash box models designed by adding geometric imperfections to structural parts such as crash beads and triggers. Numerical studies were carried out to analyze the performance of the designed structure under impact loads based on crashworthiness assessment parameters. The crashworthiness assessment parameters consist of energy absorption (EA), specific energy absorption (SEA), initial peak force (IPF), mean crushing force (MCF), and crush force efficiency (CFE). The design of the crash box with the best crashworthiness will be assembled using the bumper beam model that has been designed, and then a numerical study will be carried out. The Hexagonal CBT type of crash box model has the best crashworthiness values with EA values of 10.23 kJ, SEA 90.59 kJ/kg, IPF 277,42 kN, MCF 233.76
kJ/mm, and CFE 84.26%. Based on the results of numerical simulations, the design of the front bumper system for a two- passenger electric vehicle that has been created is capable of absorbing kinetic energy of 12.21 kJ and can absorb 35.32% of the total energy in the system. This design plan aims to improve the crashworthiness of the front bumper system of two-passenger electric vehicles.
Keywords Front Bumper System, Bumper Beam, Crash Box, Crash beads, Triggers, Crashworthiness.
-
INTRODUCTION
Accidents that occur in vehicles can result in serious injury and material loss. Improving vehicle crashworthiness is essential to prevent serious injury to passengers during an accident [1]. In a car, the front bumper system consists of a bumper beam and the crash box is a structural component that acts as passive safety in a car during a frontal accident. The bumper system is designed to absorb kinetic energy without damaging the vehicle in low-speed collisions and to dissipate energy in high-speed impact conditions [2]. For high-speed impact, it is expected that the bumper system can absorb at least 15% of the total energy, while at low speeds, it should be able to absorb all the energy [3]. The efficiency of bumper beams and crash boxes depends on thickness, type of material,
dimensions of cross-section, and application of the joint system used [4].
In bumper systems, crash boxes are the main component part of energy absorbers that can absorb impact energy significantly through the process of plastic deformation [5]. The design of the crash box for crashworthiness, in addition to absorbing large energy, the crash box must also have a low initial peak force and high mean crushing force [6]. High initial peak force can threaten passenger safety. Controlling initial peak force can significantly increase crashworthiness in a crash box. The primary approach to reducing the initial peak force of thin-walled structures during axial compression is to add geometric imperfection to parts of the structure [7], such as corrugate patterns or crash beads and triggers. There has been some previous research related to a geometric imperfection design in thin-walled structures. Ming S et al. [8] perform numerical simulations and quasi-static experiments on long origami ending tubes with geometrical imperfections. Geometric imperfections on long origami ending tubes can improve energy absorption performance. Wang G et al. [9] designed a foam-filled crash box with partial filling combined with a trigger. A foam-filled crash box with partial filling combined with a trigger improves energy absorption and deformation stability. Nasir et al. [10] analyzed that using triggers in hexagonal crash box types can increase energy absorption capacity. Kumar M et al. [11] compared crash boxes with corrugate patterns or so-called crash beads with crash boxes without corrugate patterns. The crash box design with a corrugate pattern is better than a crash box design without a corrugate pattern because it absorbs lower stress. The reduction of initial peak force on the tube with the addition of a trigger was also studied and validated in several other previous studies [12], [13], [14].
In addition to being influenced by thickness, material type, and cross-sectional shape, the length of the total dimensions of the bumper system can also affect the performance in absorption impact energy. Electric vehicles with a capacity of two passengers have a relatively smaller front bumper system dimension when compared to the front bumper system in other vehicles with a capacity of four
passengers or more. The difference in the dimensions of the front bumper system of an electric vehicle with a capacity of two passengers, which has relatively smaller dimensions than other vehicle with a capacity of four passengers or more, will have different kinetic energy absorption performance and crashworthiness during collisions. In this study, the bumper beam and crash box of two-passenger electric vehicles were
designed as 3D models, and then numerical studies were carried out using ANSYS explicit dynamics software. The length of the bumper system dimensions is designed based on the total length of the bumper system for a two-passenger electric vehicle, as shown in Figure 2. The crash box is designed by adding geometric imperfections to the structure, such as the crash bead, and combining the crash bead and
Fig. 1. Chassis and bumper system of a two-passenger electric vehicle Fig. 2. The dimensions of the chassis of a two-passenger electric vehicle
Triggers
Crash beads
Fig. 3. Dimensions and design of the front bumper
Fig. 4. Crash box model design
R32.5
Fig. 5. Dimensions of crash box, crash beads, and triggers
trigger in one design, as seen in Figure 4. Numerical simulation test parameters are adjusted to the New Car Assessment Program (NCAP) test standards by the National Highway Traffic Safety Administration (NHTSA). This design plan aims to achieve a bumper beam and crash box design for a two-passenger electric vehicle that can better absorb kinetic energy to improve crashworthiness during full frontal impact collisions.
TABLE I. DESIGN PARAMETERS OF SOME CRASH BOX MODELS
Profile
Thickness (mm)
Length (mm)
Mass (kg)
Square CB
1.6
120
0.13267
Hexagonal CB
1.6
120
0.11494
Circular CB
1.6
120
0.10491
Square CBT
1.6
120
0.13134
Hexagonal CBT
1.6
120
0.11294
Circular CBT
1.6
120
0.1038
-
CRASHWORTHINESS ASSESSMENT Several parameters can be used to assess the
crashworthiness efficiency of various thin-walled structures under crushing load, namely energy absorption (EA), specific energy absorption (SEA), initial peak force (IPF), mean crushig force (MCF), and crush force efficiency (CFE). These parameters are used to assess crashworthiness performance in the bumper system (crash box and bumper beam) designed. Energy absorption (EA) is the capacity of energy absorption by structures during the collision process. In terms of mathematics, it can be formulated as the following:
(1)
Where s is crash displacement, and F is impact force.
Specific energy absorption (SEA) is the ratio of the amount of energy absorption to the mass of the structure used to characterize energy absorption in mass-dependent structures [15]. It can be calculated as:
(2)
Where EA is the absorption energy during the process, and M is the mass of the structure.
Initial peak force (IPF) is the maximum force transferred at the beginning of the impact during an accident. At this point, the structure can no longer withstand the force and begins to deform, or the structure folds. Larger IPFs show higher initial resistance of structures to buckling, leading to higher damage and more severe injury [15].
Mean Crushing Force (MCF) is another important index to indicate the energy absorption ability of a structure, which is the average value of all peak loads obtained on the force- displacement curve. It can be calculated as:
Crush force efficiency (CFE) is the peak resistance force (initial phase of loading) and mean force which are very important parameters because they directly affect the deceleration of passengers in the vehicle [15]. CFE is an indication of the stability of the structure during the destruction process. Mathematically, it can be expressed as:
(4)
Fig. 6. Force displacement graph
Impactor (Rigid Body)
Standard Earth Gravity
g = 9.8 m/s2
m = 275 kg v = 56 km/h
Fix Support
Base Plate (Rigid Body)
Fig. 7. Setup numerical simulation of crash box
TABLE II. MATERIAL PROPERTIES OF ALUMINIUM 6063-T6
Where EA is energy absorption and d is crushing distance.
Material Properties
Value
Density
2700 kg/m3
Youngs modulus
73000 MPa
Poissons ratio
0.3
Yield strength
206 MPa
Tangent modulus
28100 MPa
(3)
Fig. 8. Setup numerical simulation of bumper system
Fig. 9. Graph of energy conservation numerical simulation
-
METHODOLOGY
The length of the dimensions in the design of the front bumper system consisting of a bumper beam and crash box is based on the standard size of a two-passenger electric vehicle. The total dimensional length of the electric vehicle designed is 2695 mm, with chassis length including the front rail of 2520 mm, crash box of 120 mm, and bumper beam of 55 mm, which can be seen in Figure 2. Protection capacity, weight, material, and ease of manufacturing process are the main considerations in bumper system design. There are six crash box models designed, and numerical simulations are carried out to determine the crash box with the best crashworthiness. The crash box with the best crashworthiness will be assembled with a bumper beam design, and then numerical simulations are carried out to observe the total energy absorption in the bumper system.
-
Structural Design of Crash Box
The crash box is at the end of the vehicle chassis between the bumper beam and front trail, as shown in Figure 1. The front end of the crash box is welded on both sides of the bumper beam, with the rear of each crash box mounted on the front end of the front trail. Geometry, dimensions, imperfection geometric patterns, and material type are factors that influence crash box performance in energy absorption during impact [16]. Several crash box design models will be made with three different cross-sectional shapes. The cross- sectional shape of the crash box design consists of square, hexagonal, and circular. All cross-sections are made to be bordered with circles with a radius of 32.5 mm to maintain uniformity. The length of each crash box is 120 mm with a thickness of 1.6 mm, and there is geometric imperfection in the structure, as shown in Figure 5. The six crash box designs consist of three models with crash bead patterns on the side surface of the crash box, namely square crash beads (square CB), hexagonal crash beads (hexagonal CB), and circular crash beads (circular CB). Three models of crash beads pattern with additional triggers at the end of the crash box, namely square crash beads triggers (square CBT), hexagonal crash beads triggers (hexagonal CBT), and circular crash beads
triggers (circular CBT). The design of the crash box model is shown in Figure 4, and Table I shows the design parameters of the various crash box models.
-
Structural Design of Bumper Beam
Like crash boxes, bumper beams are one of the components of the bumper system that functions as an impact energy absorber, where the design model, dimensions, and type of material used also influence energy absorption performance. The dimensions of the length and width of the front bumper beam design are made to adjust the size of the length and width of the bumper system dimensions of the two- passenger electric vehicle. The cross-section of the bumper beam is rectangular with a size of 35 mm × 80 mm with a thickness of 2 mm, the total length of the front bumper beam is 1028 mm. The dimensions and design of the front bumper beam can be seen in Figure 3.
-
Numerical Simulation Method
Finite element software Ansys Explicit Dynamics solver Autodyna is used to analyze the behavior of crash boxes and bumper systems under impact load. Explicit dynamics analysis is a method of time integration for dynamic analysis that considers rapidly changing conditions and involves nonlinear dynamics such as free fall motion and high-speed impact. The thin-walled structure of the crash box and bumper beam is modeled as a shell element with a mesh size of 2 mm. The contact type between the body is modeled as bounded contact with penalty as contact formulation. Body interaction is modeled as frictionless. Boundary condition fix support is applied to the bottom of the base plate.
The impactor and base plate for numerical simulation setups on crash boxes and bumper systems are modeled as rigid bodies. The mass of the impactor is 275 kg, and the initial speed of the impactor is 56 km/h. The end time is 0.003 s for the observation time of the crash box and 0.005 s for the observation time of the bumper system. Impact mass and speed parameters are based on New Car Assessment Program (NCAP) testing standards by the National Highway Traffic Safety Administration (NHTSA). The numerical simulation
Fig. 10. Energy absorption graph of crash box
Fig. 11. Force displacement graph of crash box models
277.42
Crash Box Type
EA (kJ)
SEA
(kJ/kg)
IPF (kN)
MCF
(kJ/mm)
CFE (%)
Displacement (mm)
Fmax (kN)
Square CB
4.86
36.63
166.04
107.99
65.04
44.99
166.04
Hexagonal CB
9.77
85.05
274.45
224.44
81.78
43.55
274.45
Circular CB
6.91
65.88
189.8
138.33
72.88
49.96
189.8
Square CBT
6.53
49.76
180.87
145.98
80.71
44.76
180.87
Hexagonal CBT
10.23
90.59
233.76
84.26
43.76
277.42
Circular CBT
6.22
59.93
187.14
122.11
65.25
50.94
187.14
Fig. 12. Force displacement graph of crash beads models Fig. 13. Force displacement graph of crash bead triggers models TABLE III. RESULTS OF NUMERICAL SIMULATION ANALYSIS ON VARIOUS CRASH BOX DESIGNS
setup of the crash box and bumper beam is shown in Figure 7 and figure 8, respectively. The material for crash boxes and bumper beams is aluminum 6063-T6. Material properties data for Aluminum 6063-T6 based on previous research by Tan Hailun et al [17], are shown in Table II. Material plasticity models are modeled as bilinear isotropic hardening to observe materials under nonlinear behavioral conditions.
-
-
RESULT AND DISCUSSION
-
Validation of Numerical Model
To ensure numerical simulations predict accurate results, explicit solvers always check the total energy balance to monitor energy conservation to observe the energy equilibrium in the system. During explicit dynamics
simulations, the total energy of a system must always be conserved. In accordance with the law of conservation of energy, energy cannot be created or destroyed and can only be converted from one form of energy to another [18]. A system should always have the same amount of energy unless that energy is added or lost. The energy conservation graph from the numerical simulation is shown in Figure 9. During the impact process, kinetic energy decreases, and internal energy increases because kinetic energy is converted into internal energy during the impact. In addition to ensuring energy conservation during numerical simulations, hourglass energy must constitute a bit of the total energy. Therefore, it is necessary to ensure that hourglass energy should be at most 5% of total energy [16]. Figure 7 shows the conservation energy curve from the numerical simulation where the total hourglass energy value is 0.34% of the total energy in the system. The percentage value of the total hourglass energy value is a fraction of the total energy value in the system. Based on the energy conservation and the percentage of hourglass energy or numerical energy error in this numerical simulation, the numerical model setup and the results of
Fig. 14. IPF EA diagram of crash box models
Fig. 16. IPF EA diagram of crash box models
explicit dynamics numerical simulation can be categorized as entirely accurate.
-
Performance of Crash Box
The parameters used to assess the performance of various crash box designs made to improve the crashworthiness of the bumper system are energy absorption (EA), specific energy absorption (SEA), initial peak force (IPF), mean crushing force (MCF), and crush force efficiency (CFE).
-
Energy Absorption and Specific Energy Absorption
In a frontal collision system, impact energy is absorbed through the process of plastic deformation of the components and converted into internal energy [9]. Figure 6 shows the force-displacement curve, where the value below the force- displacement curve area is the total amount of energy absorbed, according to equation 1. Energy absorption and specific energy absorption for each crash box design model are shown in Table III. It can be seen in Figure 10 that a crash box with a hexagonal cross-section shape absorbs more energy during 0.003 s of observation time than a crash box with a
Fig 15. MCF CFE diagram of crash box models
Fig. 17. All crahsworthiness assessment diagram of crash box models
cross-section square or circular. In Figure 12 and Figure 13, the force versus displacement graph also shows that the crash box with a hexagonal cross-section shape has a larger curve area than the others. This means that a crash box with a hexagonal cross-section shape absorbs more energy during the crushing time. The hexagonal CBT crash box absorbs 10.23 kJ of energy, and the hexagonal CB absorbs 9.77 kJ. Adding triggers to the hexagonal CB crash box type increased EA by 2.3%. Square CB absorbs the smallest energy of 4.86 kJ. The addition of triggers can increase the EA on the CB square by 14.6%. Circular CB absorbs energy better than circular CBT, which is 6.91 kJ. In the circular CB type, adding triggers does not impact increasing EA and SEA. The circular CB type absorbs more energy than the circular CBT type, with a mass difference that is not too significant between the two. The highest SEA is also owned by crash boxes with hexagonal cross sections, namely hexagonal CBT of 90.59 kJ/kg and hexagonal CB of 85.05 kJ/kg. Adding triggers to the hexagonal CB type increased SEA by 3.2%. Likewise, adding triggers on the square CB type can increase SEA by 15.2%. Based on equation 2, the value of SEA is directly proportional to the amount of energy absorbed and inversely proportional to the amount of mass. At the same amount of energy absorption, structures with smaller masses have larger SEAs. The diagram in Figure 16 also shows that, in general, adding geometric imperfection triggers to the crash box structure can increase the SEA value because it can increase the EA value and reduce the mass of the crash box.
-
Initial Peak Force
In addition to energy absorption capacity, initial peak force is another parameter to consider in determining performance in crash boxes. Maintaining an initial peak force that is not too high with a large energy absorption is necessary for selecting a crash box design. The higher the energy absorption is usually followed, the greater the IPF value. This is because a high IPF value increases the area of the force- displacement curve. Crash boxes with designs without triggers have a smaller IPF value than those with triggers. This is because adding geometric imperfection triggers can increase the EA crash box value. The square crash box type without triggers (square CB) can reduce the IPF value by 4.3% compared with triggers (square CBT). The hexagonal crash box type without triggers (hexagonal CB) can also reduce the IPF value by 0.5% compared to triggers (hexagonal CBT). However, for the circular crash box type without triggers (circular CB), adding triggers does not increase the IPF value. The crash box type with a square cross-section has a smaller IPF value than a crash box with a circular or hexagonal cross- section. The type of crash box with a circular cross-section has a lower impact force resistance, so the circular crash box structure will be easily deformed. As a result, the displacement value will be higher than a crash box with a square or hexagonal cross-section. The displacement values and deformation patterns of the crash box can be seen in Table III and Figure 20. Figure 11 shows the force versus displacement graph during the impact process, where square CB and square CBT have lower initial peak force points. Figure 17 in the diagram shows that square CB has a lower IPF but a smaller EA value.
-
Mean Crushing Force and Crushing Force Efficiency
Mean crushing force also indicates the energy absorption ability of the structure, which is the average value of all peak loads obtained on the force – displacement curve. Crush force efficiency is an indication of the stability of the structure during the crushing process. MCF and CFE are calculated based on equation 3 and equation 4. Crash boxes with hexagonal cross-sections, namely hexagonal CB and hexagonal CBT, have higher MCF values than crash boxes with cross- sections square and circular. That is because of the larger energy absorption and smaller displacement that crash box models with hexagonal cross sections have. MCF hexagonal CB and hexagonal CBT values were 224.44 kJ/mm and 233.76 kJ/mm, respectively. In Figure 15 of the MCF – CFE diagram, the addition of triggers in the square CB crash box type and hexagonal CB can increase the MCF value. That is because dding triggers increases the EA value, even though the hexagonal cross-section can increase the displacement value. However, in the circular CB type, the addition of triggers does not increase MCF. That happens because adding triggers reduces energy absorption and increases the displacement value in circular CB. Likewise, the CFE value in the hexagonal CB and hexagonal CBT crash box models has a high CFE value compared to other models because the hexagonal CB and hexagonal CBT models have high MCF values even though they have higher maximum peak forces. The CFE hexagonal CB value and the hexagonal CBT value were 81.78% and 84.26% respectively. Square CB crash box models with
Fig. 18. Energy absorption graph of bumper system TABLE IV. ENERGY IN THE BUMPER SYSTEM RESULTS FROM
Energy parameters in the system (kJ)
Value
EA Bumper Beam
5.77
EA Crash Box Hexagonal CBT
6.44
Total EA Bumper System
12.21
Plastic Work
8.45
Hourglass Energy
0.120
Contact Energy
0.121
Total Energy System
34.57
NUMERICAL SIMULATION
triggers (square CBT) have better CFE values than circular CB and circular CBT crash boxes. That is because square CBT has a higher MCF value. A comparison of the CFE and MCF values of each crash box model in diagram form is shown in Figure 15.
-
Energy Absorption of Bumper System
-
After numerical simulations were carried out on several crash box design models based on crashworthiness assessment parameters, the hexagonal CBT crash box model performed better than other crash box models. Beside on the values of all the crashworthiness assessment diagrams in Figure 17, the hexagonal CBT crash box model has a large EA and SEA with not too high IPF values, as well as higher MCF and CFE values than other crash box models. The hexagonal CBT crash box model is assembled with a bumper beam model designed, and numerical simulation is carried out. The numerical simulation setup for the bumper system model is shown in Figure 8.
Table IV shows the energy in the system resulting from
the numerical simulation of the bumper system. The energy contained in a system in numerical simulation consists of internal energy or energy absorption, plastic work, hourglass energy, and contact energy. The total energy absorption bumper system is 12.21 kJ, each bumper beam absorbs kinetic energy of 5.77 kJ, and the hexagonal CBT crash box absorbs
6.44 kJ of kinetic energy. The total conservation energy in the system is 34.57 kJ. Based on these results, the ratio of total energy absorbed by the bumper system to total energy in the system was 35.32%. At high-speed collisions, bumper systems are expected to be able to absorb at least 15% of the total energy [3]. Figure 18 shows the curve of total energy absorption of bumper system components, namely bumper beam and crash box. Seen during impact, crash box hexagonal CBT absorbs more kinetic energy compared to bumper beam. The hexagonal CBT crash box absorbs 18.63% and the bumper beam absorbs 16.69% of the total energy of the impact. The deformation pattern of the bumper system structure can be seen in Figure 19.
Fig. 19. Deformation pattern of bumper system
Fig. 20. Deformation patterns from all crash box models
-
-
CONCLUSION
In this study, a 3D model of the front bumper system design of a two-passenger electric vehicle, namely a crash box and bumper beam, was made. Then, a numerical study was carried out to analyze the performance of the bumper system structure under impact load based on the parameters of crashworthiness assessment. This design plan aims to improve the crashworthiness of the front bumper system of two- passenger electric vehicles. There are several main points summed up in this work as follows:
-
Crash boxes with cross-section squares and hexagonal, adding geometric imperfection to the structure by combining crash beads and triggers can increase the EA, SEA, MCF, and CFE values and increase the IPF value.
-
Crash boxes with a hexagonal cross-section absorb impact energy better than a crash box with a cross-section square or circular.
-
Based on design planning that matches the crash box dimensions of a two-passenger electric vehicle, numerical simulation results show that the hexagonal CBT crash box type design has the best crashworthiness.
-
The two-passenger electric vehicle bumper system that was designed can absorb the kinetic impact energy of
12.21 kJ and can absorb 35.32% of the total energy in the system.
REFERENCES
[1] N. A. Z. Abdullah, M. S. M. Sani, M. S. Salwani, and N. A. Husain, A review on crashworthiness studies of crash box structure, Thin-Walled Structures, vol. 153. Elsevier Ltd, Aug. 01, 2020. doi: 10.1016/j.tws.2020.106795. [2] W. Johnson and A. C. Walton, An Experimental Investigation of The Energy Dissipation of a Number of Car Bumpers Under Quasi-Static Lateral Loads, 1983. [3] Tanlak N, Sonmez FO, and Senaltun M, Shape optimization of bumper beams under high-velocity impact loads, Eng Struct, vol. 95, pp. 4960, 2015. [4] L. Peroni, M. Avalle, and G. Belingardi, Comparison of the energy absorption capability of crash boxes assembled by spot-weld and continuous joining techniques, Int J Impact Eng, vol. 36, no. 3, pp. 498511, Mar. 2009, doi: 10.1016/j.ijimpeng.2008.06.004. [5] B. P. DiPaolo and J. G. Tom, A study on an axial crush configuration response of thin-wall, steel box components: The quasi-staticexperiments, Int J Solids Struct, vol. 43, no. 2526, pp. 77527775, Dec. 2006, doi: 10.1016/j.ijsolstr.2006.03.028.
[6] G. Lu and T. Yu, Energy Absorption of Structures and Materials, Energy Absorption of Structures & Materials, 2003, pp. 385400. [7] PH. Thornton and CL. Magee, The interplay of geometric and materials variables in energy absorption, J. Eng. Mater. Technol, vol. 99, pp. 114120, 1997. [8] S. Ming et al., The energy absorption of long origami-ending tubes with geometrical imperfections, Thin-Walled Structures, vol. 161, Apr. 2021, doi: 10.1016/j.tws.2020.107415. [9] G. Wang, Y. Zhang, Z. Zheng, H. Chen, and J. Yu, Crashworthiness design and impact tests of aluminum foam-filled crash boxes, Thin- Walled Structures, vol. 180, Nov. 2022, doi: 10.1016/j.tws.2022.109937. [10] N. Nasir Hussain, S. Prakash Regalla, and Y. V Daseswara Rao, Low velocity Impact Characterization of Glass Fiber Reinforced Plastics for Application of Crash Box, 2017. [Online]. Available: www.sciencedirect.comwww.materialstoday.com/proceedings [11] Kumar M and Patil V, Design and Crash Analysis of Automotive Crush Box, International Journal on Recent Technologies in Mechanical and Electrical Engineering (IJRMEE), vol. 4, no. 7, pp. 3541, 2017. [12] MM. Abedi, A. Niknejad, GH. Liaghat, and MZ. Nejad, Foam-filled grooved tubes with circular cross section under axial compression: An Experimental Study, Iran. J. Sci. Technol. Trans. Mech. Eng, vol. 42, pp. 401413, 2018. [13] A. Niknejad, M. M. Abedi, G. H. Liaghat, and M. Zamani Nejad, Prediction of the mean folding force during the axial compression in foam-filled grooved tubes by theoretical analysis, Mater Des, vol. 37, pp. 144151, May 2012, doi: 10.1016/j.matdes.2011.12.032. [14] A. Eyvazian, T. N. Tran, and A. M. Hamouda, Experimental and theoretical studies on axially crushed corrugated metal tubes, Int J Non- Linear Mech, vol. 101, pp. 8694, May 2018, doi: 10.1016/j.ijnonlinmec.2018.02.009. [15] A. Mortazavi Moghaddam, A. Kheradpisheh, and M. Asgari, A basic design for automotive crash boxes using an efficient corrugated conical tube, Proceedings of the nstitution of Mechanical Engineers, Part D: Journal of Automobile Engineering, vol. 235, no. 7, pp. 18351848, Jun. 2021, doi: 10.1177/0954407021990921. [16] C. Y. Wang, Y. Li, W. Z. Zhao, S. C. Zou, G. Zhou, and Y. L. Wang, Structure design and multi-objective optimization of a novel crash box based on biomimetic structure, Int J Mech Sci, vol. 138139, pp. 489 501, Apr. 2018, doi: 10.1016/j.ijmecsci.2018.01.032. [17] H. Tan et al., Crashworthiness design and multi-objective optimization of a novel auxetic hierarchical honeycomb crash box, Structural and Multidisciplinary Optimization, vol. 64, no. 4, pp. 20092024, Oct.2021, doi: 10.1007/s00158-021-02961-9.
[18] [M. Guru Vishnu, Proving the Law of Conservation of Energy Using the Properties of Parallelogram, Int J Sci Eng Res, vol. 7, no. 11, 2016, [Online]. Available: http://www.ijser.org