
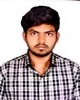
- Open Access
- Authors : Rudduru Sanjay Krishna , Ajmeera Ramesh
- Paper ID : IJERTV11IS030061
- Volume & Issue : Volume 11, Issue 03 (March 2022)
- Published (First Online): 21-03-2022
- ISSN (Online) : 2278-0181
- Publisher Name : IJERT
- License:
This work is licensed under a Creative Commons Attribution 4.0 International License
Design and Simulation of an Electrical Submersible Pump
Rudduru Sanjay Krishna Department of Petroleum Engg & Petrochemical Engineering JNTUK, Kakinada, Andhra Pradesh, India |
Ajmeera Ramesh Department of Petroleum Engg & Petrochemical Engineering JNTUK, Kakinada, Andhra Pradesh, India |
Abstract – Artificial lift methods are used for the enhancement of productivity from oil wells. This study has been conducted on the electric submersible pump (ESP), an analysis of production system that is used to identify the potential of any well, a description of ESP components and installation, a comparison of different productive wells and a discussion of a cases study of oil wells for a design ESP throughout the different parameters. These methods use artificial means to increase well production and ultimately oil recovery. One of these artificial lift methods is the use of ESP that has an efficiency and consistency for wells with a moderate to high production. PROSPER is a well performance, design and optimization computer software for modelling most types of well configurations. This study major focuses on the design and simulation of an ESP system for wells having different productivity index using the PROSPER software.
Keywords: Artificial lift methods, Electrical submersible pump, PROSPER software, Well performance.
-
INTRODUCTION
The artificial lift system of a well resembles the human heart which pumps the high volumes of reservoir fluids to the surface in low producing wells. These methods are employed in oil wells whose energy from the reservoir is insufficient to lift the fluids to the surface. Most of the producing wells in the world nearly 90 % are presently working on the artificial lift system from early stages. Among the available artificial lift methods, the electrical submersible pump (ESP) system is very effective in wells with low bottom hole pressure, low gas to oil ratio, low bubble point pressure, high water cut, and deviated wells [1].
Electrical Submersible Pump System
History and origin:
A Russian engineer named Armais Arutunoff in 1911 invented an electric motor that can be worked on the water. By the addition of a drill and centrifugal pump to the motor, he invented an electrical submersible pump. Later he improves the system and invented the Russian Electrical Dynamo of Arutunoff for which Schlumberger is currently acting as a service provider [1].
Some of the ESP System Service Providers are listed: Schlumberger- REDA, Weatherford, Baker Hughes- Centrilift, Wood Group ESP, ALNAS.
Components:
The components of an ESP System can be categorized into surface and downhole components are listed [2]: a). Surface
Components: Transformers, Motor controllers, Junction box, Well Head. b). Downhole Components: Electrical Cable, Cable Protectors, Pumps, Gas Separator, Seal section, Motor, Pump intake, Drain valve, Check valve. The ESP System along with its components labelled is shown in Fig.1.0.
Working Principle of ESP System:
Electrical Submersible Pumps are the vertical alignment of centrifugal pumps in the borehole which accelerates the velocity of fluids by impellers. The kinetic energy produced by the impellers is converted into pressure energy by the diffuser and pumps the fluid. An Electrical Submersible Pump is a multi-stage stacked centrifugal pump whose stages are determined by bottom hole pressure and desired flow rate. The arrangement of each stage of an ESP System consists of an impeller and diffuser. When the fluid enters the impeller of the first stage, it centrifuges the liquid radially outward and increases the velocity of the fluid. Now the fluid enters the diffuser from the sharp edges of the impeller where the kinetic energy of the fluid is converted into pressure energy. The pressure gained by the fluid in the first stage and enters the next stage where the pressure is increased slightly than the first stage. As the stages are increase, the pressures are gaining incrementally in each stage to desired discharge pressure and designed head of the pump [1].
Figure 1.0: ESP System and its components
Advantages, Disadvantages, and Industrial applications of ESP system:
The major advantages of an ESP system [3,4,5]:
-
Capable of pumping high viscous crude oils to the surface.
-
It can be applied to well having low bottom hole pressure.
-
ESP System has a low tendency of scale forming operating conditions.
-
It has a capacity to produce high volumes of fluids up to 18,000 barrels/day to surface.
-
High efficiency and low operating costs. The major disadvantages of an ESP system [3,4]:
-
It can take high repair and maintenance costs.
-
It is not applicable to high GOR producing wells.
-
The efficiency of the motor is reduced in sand producing wells and sand producing wells will cause mechanical repairs to wells.
-
ESP System installation is very critical in highly deviated and dogleg severity wells.
-
Special equipment is needed for the repair of the ESP system in deviated wells.
-
It is not applicable to the high temperature and deep wells.
The Industrial applications of an ESP system [3, 4, 5]:
-
High productive index wells.
-
Offshore wells.
-
Mostly deviated and horizontal wells.
-
ESP is also used for the dewatering purpose of the wells.
Economic analysis of an ESP system:
The better economic evaluation of an ESP System is carried out through the PROSPER software and production can be forecasted in different scenarios for 5-6 years. ESP generates higher gross profits because it produces high potentials of reservoir fluids. On other hand it can also have high operating expenses due to high water cuts and the replacement of failed pumps.
-
-
DESIGN AND SIMULATION STUDIES ON ESP SYSTEM USING THE PROSPER SOFTWARE
PROSPER is a production optimization software used to models the well completions configuration and design artificial lift methods. It predicts the reservoir fluid properties as a function of temperature and pressure. It simulates the optimized results for the particular artificial lift method based on input data. PROSPER distinctive matching options that tune PVT, multi-phase flow correlations and IPR to match measured field information. It is accustomed style and optimize well completions as well as multi-lateral, multi-layer and horizontal wells, conduit and pipeline sizes [6,7,8].
Stepwise Procedure for Design of ESP System Using PROSPER Software
-
First click on file option and select the new file.
-
Now in the system summary, water and oil with Black Oil model options are chosen for fluid description and choose Electrical Submersible Pump for artificial lift method.
-
Enter the PVT parameters in the PVT input data window and match data with correlations to get the least deviation.
-
After matching PVT data, input reservoir operating parameters in the IPR window to develop the inflow performance relation (IPR) curve and determine the absolute open flow.
-
Enter deviation survey data, downhole equipment data, surface equipment data, (if available) and geothermal gradient data in their respective windows.
-
Enter desirable design parameters and calculate the output design parameters and generate a plot based on output design parameters.
-
From the plot generated, choose the optimum operating design of ESP System.
-
We consider two wells having different productivity index wells (i.e. High and Low) for the design of the ESP System. Design of ESP System for low productivity index of a well:
The following table 1 delineates the reservoir and fluid input data for the PROSPER software to design the ESP System for the low productivity index of a well.
Table 1: Reservoir and Fluid Input Data
Reservoir and Fluid Input Data
Reservoir pressure
4000 psi
Bubble point pressure
2500 psi
Reservoir Temperature
2000F
GOR
400 scf/stb
Water cut
0 %
Oil API
300API
Gas specific gravity
0.75
Water salinity
80000 ppm
Oil FVF
1.2 bbl/stb
Oil viscosity
0.31 cp
Productivity index
2 stb/day. psi
After giving the reservoir and fluid input data to the software, inflow performance relation (IPR) curve is generated and the absolute open flow (AOF) of the well is determined. The Fig. 2.0. Illustrates the IPR curve for low productivity index well with AOF.
Figure 2.0: IPR curve of a low productivity index well According to the absolute open flow rate, give the desirable design parameters to software as shown in table 2 and generate calculated output design of ESP System as shown in table 3.
Table 2: Input Design Data
Table 3: Calculated Design Data
Input data
Pump depth(measured)
7000 ft
Operating frequency
60 Hz
Maximum pump outside diameter
6 in
Length of cable
7000 ft
Design rate
11000 stb/day
Water cut
0%
Top node pressure
250 psig
Calculated Design Data
Pump Intake Pressure
2088.75 psig
Pump Intake Rate
12935.9 Rb/Day
Free GOR Entering Pump
67.5125 scf/STB
Pump Discharge Pressure
3206.38 psig
Pump Discharge Rate
12756.5 Rb/Day
Total GOR Above Pump
400 scf/STB
Average Downhole Rate
12808.7 Rb/Day
Head Required
2669.17 ft
Pump Inlet Temperature
199.180F
Figure 4: ESP Design plot for low productivity index well Design of ESP System for high productivity index of a well:
The following table 5 below represents the reservoir and fluid input data for the PROSPER software to design ESP System for low productivity index of a well.
Reservoir and Fluid Input Data
Reservoir pressure
4490 psig
Bubble point pressure
1958 psi
Reservoir Temperature
2190F
GOR
507 scf/stb
Water cut
16 %
Oil API
34.2 API
Gas specific gravity
0.92
Water salinity
220000 ppm
Oil FVF
1.42 bbl/stb
Oil viscosity
0.5 cp
Productivity index
6.5 stb/day. psi
Table 5: Reservoir and Fluid Input Data
On the basis calculated design data, select the better downhole equipment like pump, motor and electrical cable for well having low productivity index (PI = 2) available in the software. For the selected equipment generate optimum output results are presented in table 4 and the design plot of a ESP system as shown in Fig. 3. 0. From the plot generated the best efficiency and better operating conditions of system.
Results
Number of Stages
65
Power Required
393.76 HP
Pump Efficiency
62.3434 %
Pump Outlet Temperature
203.03 0 F
Current Used
94.614 amps
Motor Efficiency
88.0176 %
Power Generated
393.76 HP
Motor Speed
3512.01 rpm
Voltage Drop along Cable
210.999
volts
Voltage Required at Surface
2671 volts
Table 4: Results for selected Equipment
After giving the reservoir and fluid input data to the software, an inflow performance relation (IPR) curve is generated and the absolute open flow (AOF) of the well is determined. The figure 4 delineates the IPR curve for the high productivity index well with AOF.
Figure 4: IPR Curve for high productivity index well
Based on the absolute open flow rate, give the desirable design parameters to software as shown in table 6 and
generate calculated output design of ESP System as show in table 7.
Table 6: Input Design Data
Input data
Pump depth(measured)
10330 ft
Operating frequency
60 Hz
Maximum pump outside diameter
6.18 in
Length of cable
10430 ft
Design rate
12000 stb/day
Water cut
16 %
Top node pressure
350 psig
Table 7: Calculated Design Data
Figure 5: ESP Design plot for high productivity index well
Calculated Design Data
Pump Intake Pressure
2880.93 psig
Pump Intake Rate
14061.8 Rb/Day
Free GOR Entering Pump
52.73 scf/STB
Pump Discharge Pressure
4857.03 psig
Pump Discharge Rate
13934.4 Rb/Day
Total GOR Above Pump
507 scf/STB
Average Downhole Rate
13993.9 Rb/Day
Head Required
5866.49 ft
Pump Inlet Temperature
209.3990F
Comparison between the High Productivity and Low Productivity Index of Wells:
The following table 9 represents comparison of results of low productivity index well and high productivity index well which are taken as case studies.
Table 9: Comparison of results of two wells
Parameters
Low Productivity Index Well
High Productivity Index Well
Pump setting depth
Low
High
Design Rate
Low (11000
STB/Day)
High (12000 STB/Day)
Water cut
High (0 %)
Low (16%)
Pump Intake Pressure
Low
High
Pump Intake Rate
Low
High
Pump discharge Rate
Low
High
Head Required
Low
High
Number of Stages
Low
High
Pump efficiency
Low
High
Voltage Drop along Cable
High
Low
Based on calculated design data, select the better downhole equipment like the pump, motor, and electrical cable for well having high productivity index (PI = 6.5) available in the software. For the selected equipment generate optimum output results are shown in table 8 and the ESP Design plot as depicts in figure 5. From the plot generated the efficiency and better operating conditions are determined.
Results
Number of Stages
120
Power Required
776.196 HP
Pump Efficiency
66.9641 %
Pump Outlet Temperature
217.366 0F
Current Used
112.42 amps
Motor Efficiency
82.83 %
Power Generated
508.79 HP
Motor Speed
3441.53 rpm
Voltage Drop along Cable
509.07 volts
Voltage Required at Surface
3344.07
volts
Table 8: Results for selected Equipment
-
-
CONCULSION
From the Design of ESP Systems of two wells, we studied that a greater number of stages of pumping and high head is required for low productive well, due to these factors the pump efficiency is decreased. More over Pump intake pressure and Pump discharge pressure are decreased because of its low producing rates. The same conditions are vice versa for high productive wells.
-
ACKNOWLEDGMENT
I would prefer to specific my profound sense of feeling to guide Mr, Ajmeera Ramesh, Asst. Professor, Department of Petroleum Engineering and Petrochemical Engineering, JNTUK, Kakinada, for his or her skillful steerage, timely suggestions and encouragement in finishing this paper.
-
REFERENCES
the Gyda field, Master thesis, 2009.
[8] Imran A. Hullio*, Sarfraz A. Jokhio, Khalil Rehman Memon, Sohail Nawab and Khair Jan Baloch, Design and Economic Evaluation of the ESP and Gas Lift on the Dead Oil Well International Journal of Current Engineering and Technology,2018.