
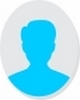
- Open Access
- Authors : Weizheng Li , Donghui Wang , Ziyu Hu
- Paper ID : IJERTV10IS050065
- Volume & Issue : Volume 10, Issue 05 (May 2021)
- Published (First Online): 22-05-2021
- ISSN (Online) : 2278-0181
- Publisher Name : IJERT
- License:
This work is licensed under a Creative Commons Attribution 4.0 International License
Design and Simulation of Offshore Platform Quadruped Working Robot
Weizheng Li, Donghui Wang, Ziyu Hu
Mechatronic Engineering
Tianjin University of Technology & Education Tianjin, China
AbstractAccording to the typical operation requirements and environmental characteristics on the deck of the offshore platform, a quadruped working robot is designed from the perspective of The overall structure model of the robot is built, and the key mechanisms such as the robot body, leg and manipulator arm are described in detail. The forward kinematics of the robot is analyzed, A simplified robot model and simulation program are built, and the performance of the robot in various motion modes is simulated to verify the stability of the robot The research content provides a reference for exploring the operation of grinding, spraying and cleaning the deck of offshore platform by machine instead of manual work.
Keywords:- Offshore quadruped working structural motion simulation
. INTRODUCTION
At present, the grinding, spraying, cleaning and other operations of offshore platform wall are mainly completed by manual work. which has the problems of low efficiency, high risk, high intensity and so on. The development and application of robotics show that the above problems can be effectively solved by robots instead of manual operation.
Quadruped robot is designed based on bionic principle, which is a typical and mature structure mode of ground operation robot. The most representative products, such as "Big Dog" [1]and "Spot Mini" [2] invented by Boston Dynamics in the United States. They have good adaptability to the complex field geographical environment,and have a strong self-adaptive balancing ability, load capacity and obstacle surmounting ability, which can realize reconnaissance, transportation and other operations.The representative ones in China are "laikago" of Unitree Robotics [3], "Jue Ying" and "Red Rabbit" of Zhejiang University [4], which can realize various gaits such as walking, trotting and running ,they can be used for security, rescue and other operations.These common quadruped robot mechanisms are mainly used for land walking and operations, but they are not suitable for offshore platform operations. When they are used for warking and operations on the deck of offshore platform, the influence of wind and waves, platform shaking and slippery conditions on the stability of robot walking and operations should be considered.
In view of the above problems, this paper puts forward a design scheme of quadruped working robot based on the current research achievements in the field of quadruped robot, and verifies it by simulating the motion posture of the robot, so as to provide a reference for exploring the feasibility of the robot to replace manual grinding, spraying and other operations on the offshore platform.
. STRUCTURAL DESIGN AND MODELING OF QUADRUPED WORKING ROBOT
The deck operation robot of offshore platform needs to meet the requirements of flexible walking, stable landing, easy control, diversified operation and light weight. In order to meet the above requirements, a quadruped robot mechanism is designed as shown in Fig.1.
a3-D model of quadruped working robot |
bAdaptive electromagnetic adsorption structure |
Fig. 1. Structure diagram of quadruped working robot. Notes:1-Oil barrel, 2-Steering gear pan tilt, 3-Mechanical arm, 4- Universal end effector, 5-Grinding wheel, 6-Main body, 7-Steering engine, 8-Thigh,9-Crus, 10-Adaptive electromagnetic adsorption structure, 11-Hexagon socket bolt, 12- Electromagnet fastener, 13-Compression spring, 14-electromagnet. |
Fig. 1. (a) shows that the robot is mainly composed of a body, four groups of leg and foot mechanisms, and a mechanical
arm mechanism,etc.
Body belongs to the robot carrier of the connection of each structure, in order to reduce the weight of the robot, and make it has a certain carrying capacity, the body structure is designed as a framework and shell structre.The framework is composed of aluminum alloy profiles, and the shell is made of acrylic plate production. The above structure with the corresponding carrying capacity, and greatly reduce the weight of the robot design.Inside the body, the space is used to install the robot control box.
In order to meet the needs of walking, steering and obstacle surmounting of quadruped robot under complex environment conditions on the platform deck of the quadruped robot, the leg foot mechanism of the robot is designed with four degrees of freedom, among which the lateral swing joint, hip joint and knee joint are the active degrees of freedom, and the ankle joint is the passive degree of freedom. The legs are arranged in full elbow style to ensure no movement interference between the front and rear legs. In order to ensure the stability of the robot in the process of walking and operation, the foot of the robot is designed as an adaptive electromagnetic adsorption structure as shown in Fig. 1 (b). After the robot lands, through the compression of the spring and the adaptive rotation of the ankle joint, the full contact between the foot surface and the deck surface can be ensured, the adsorption force generated by the electrization of the electromagnet after the foot is contacted with the deck of offshore platform , the stability of the robot walking on the deck and the operation process can be ensured in this way,.
The robot manipulator is designed as a three degree of freedom mechanism, which can meet the requirements of left and right swing operation, through the control of two joint steering gear of the manipulator, the three dimensional operation requirements of the manipulator end can be met.The end of the working arm is designed as a replaceable structure, which can meet the flexible operation requirements of the robot by replacing the end actuators such as grinding, spraying (the oil barrel on the back of the robot can provide oil), cleaning and so on, So as to realize the diversified operation of the robot.
. KINEMATICS ANALYSIS OF QUADRUPED WORKING ROBOT
In order to verify the kinematic performance of the designed robot, the coordinate system of the quadruped robot (as shown in Fig. 2) is established based on the Denavit-Hartenberg (D-H) method [5-6], and the joint coordinate system and joint parameters are analyzed. The coordinate system {0} is the world coordinate system. The coordinate system {b} is the body coordinate system. The coordinate system {1} is the coordinate system at the side swing joint. The coordinate system {2} is the coordinate system at the front swing joint of the thigh. The coordinate system {3} is the coordinate system at the front swing joint of the crus.The coordinate system {4} is the coordinate system of h point, which is the central point of the end of the foot . In the robot coordinate systerm, the origin of coordinate system {0} coincides with the origin of coordinate system {1}.
Zb
Yb
Xb
Y
Y
X0
Y0 1
Z0 l1
l2
X1
Z1
Y2
X2 Z2
.
.
X3 Z3
l3 h Y3
X4 Z4
Y4
Fig. 2. Robot coordinate system
According to the robot coordinate system established in Figure. 2, the D-H parameters of the robot in swing phase are shown in Table 3.
Table 2: D-H parameters of left foreleg
Joint |
li |
i |
i |
i |
1 |
l1 |
90° |
0 |
1 |
2 |
l2 |
0 |
0 |
2 |
3 |
l3 |
0 |
0 |
3 |
i
i
In Table 2, li is the linkage length, i is the joint torsion angle, di is the joint distance, i is the joint angle.The D-H transformation matrix from the coordinate systerm {i} to coordinate systerm {i-1} is i-1T, and its expression is as follows:
ci
si 0
ai 1
s c
c c s
s d
i 1T i i 1
i i 1
i 1
i 1 i
(1)
i s s
c s c
c d
i i1
i i1
i1
i1 i
0 0 0 1
From Equation (1), it can be concluded that the position and pose transformation matrix of the h point at the end of the robot leg relative to the coordinate system {0} is as follows:
c1c23
c1s23
s1 c1 l1 l2c2 l3c23
s c s s c s l l c l c
0T 0T 1T 2T 3T 1 23 1 23 1 1 1 2 2
3 23
(2)
4 h
1 2 3 4
s c 0 l s l c )
23 23 2 2 3 23
0 0 0 1
in (2), si=sini , ci=cosi , sij=sin(i+j) , cij=cos(i+j). The same below.
The forward kinematics equation of the robot legs can be obtained as follows:
nx ox ax hx
n o a h
y y y y 0T h
(3)
n o a h 4
z z z z
0 0 0 1
Where [nx ny nz]T is the cosine value of the Angle between the X-axis direction vector of the foot coordinate system {4} and the three axis direction vectors of the coordinate system {0}.[ox oy oz]T is the cosine of the Angle between the Y-axis direction vector of the foot coordinate system {4} and the three axis direction vectors of the coordinate system {0}.[ax ay az]T is the cosine value of the Angle between the Z axis direction vector of the foot coordinate system {4} and the three axis direction vectors of the coordinate system {0}.[hx hy hz]T is the coordinate of the h-point in the coordinate system {0}.
simultaneous formulas (2) and (3), [hx hy hz]T can be expressed as follows:
hx c1 l1 l2c2 l3c23
h s l
-
l c
-
l c
(4)
y
1 1 2 2 3 23
hz l2c2 l3c23 )
According to the robot designed in this paper, the position and pose of the h point of the end of the robot leg can be calculated by forward kinematics analysis after given the spatial rotation Angle [1 2 3]T, under the conditions of corresponding D-H parameters given.
. ROBOT MOTION SIMULATION
In order to facilitate the motion simulation in Matlab / Simulink, some structural accessories and parts on the robot are removed and simplified into a rigid body model with similar structure and shape to the actual model for simulation. In order to ensure the accuracy of the simulation results, physical parameters such as density, volume and mass of the material with the actual model are added to the simplified model, and the final simplified model is imported into Simulink to obtain the simulation model as shown in Fig. 3.
Fig. 3. Simplified model diagram in Simulink |
The driving functions of each joint are written in Matlab function and the motion signal are added [7], so that the robot can realize trot, lateral movement and working (slow walking) gait. Set the total simulation time to 25s, the first 0 ~ 6s is the trot movement time, 6 ~ 13s is the lateral movement time, and 13 ~ 25s is the slow walking gait time.
Fig. 4 to Fig. 9 show the displacement and velocity curves of the robot in x direction, y direction and z direction.The x direction is the forward direction of the robot's centroid, Y direction is the lateral move direction of the robot's centroid, and z direction is the direction of the robot's centroid moving up and down (perpendicular to the body).
Fig. 4. Displacement of body centroid in x direction |
Fig. 5. Velocity of body centroid in x direction |
Fig. 6. Displacement of body centroid in y direction |
Fig. 7. Velocity of body centroid in y direction |
Fig. 8. Displacement of body centroid in z direction |
Fig. 9. Velocity of body centroid in z direction |
From the displacement curves in three directions, in the whole simulation time, the robot moves forward about 7m ,and moves laterally about 2.5m.The robot's centroid in a small range near 0 in the z direction, and the fluctuation changes obviously in the lateral movement, but it has no obvious effect on the robot motion.When the robot is moving in x direction or y direction, there is no displacement accumulation, and it can keep walking in a straight line in its direction of motion.
From the velocity curves of the three directions, the velocity fluctuation of the centroid in x direction and y direction is very small, and there are occasional velocity mutations in both of them in the slow walking gait, which has no obvious influence on the robot motion. Therefore, this paper will not do research on this.The velocity fluctuation in the z direction is small in the trot and slow walking gait, but it is larger in the lateral movement, which indicates that the robot stability in the lateral movement needs to be further strengthened.From the whole simulation process, the robot can realize stable walking, which verifies the rationality of the robot structure design, and also verifies the correctness of the kinematic analysis.
. CONCLUSIONS
Aiming at the requirements of typical operation on the deck of an offshore platform, a quadruped robot mechanism is designed, and the performance of the robot is analyzed by modeling and simulation. The conclusions are as follows:
(1) The body of the robot is a skeleton structure, which has the corresponding carrying capacity and greatly reduces the design weight of the robot.Robot body internal integrated control system, the structure of the robot is compact.
-
The robot adopts a quadruped mechanism, and the foot end is designed with an adaptive electromagnetic adsorption mechanism ,realize the robot's functions of walking, steering and overcoming obstacles on the platform deck, and ensure the stability of the robot during works and operations.
-
The multi DOF Manipulator ensures that the robot can work in three-dimensional space, and provides convenience for multi-functional flexible operation.
-
The rationality of the structure design and the stability movement of the robot are analyzed through the motion simulation.
. REFERENCES
-
Marc Raibert, Kevin Blankespoor, Gabriel Nelson, Rob Playter, BigDog, the Rough-Terrain Quadruped Robot, IFAC Proceedings Volumes,Vol41, pp 10822-10825, February 2008
-
PEEL B, DYNAMICS B, SPOTMINI. New Robot, SpotMini, Foiled By Banana Peels.
-
Junjie Yang, Hao Sun, Changhong Wang, Xiaodong Chen.Review of Quadruped Robot Research. Navigation Positioning and Timing,Vol 6, pp 61- 73(in chinese), January 2019
-
Chuan Li. Motion Planning and Control for Jumping and Runing of Quadruped robot. Zhejiang University (in chinese), January 2017
-
Chen J, San H, Wu X, Chen M, He W. Structural design and characteristic analysis for a 4-degree-of-freedom parallel manipulator. Advances in Mechanical Engineering, Vol 11, pp 1-12, November 2019
-
N. Meng and W. Xiaodong, "Kinematics analysis and simulation of quadruped robot. International Conference on Fluid Power and Mechatronics, pp 816-821, August 2011
-
Rong X, RuiS, Li B. Simulation for sagittal plane motions of a quadruped robot using MATLAB and Simulink. Journal of information and computational science, Vol 9, pp 2165-2173, August 2012