
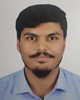
- Open Access
- Authors : Sumedh Joshi , Sanket Sathe , Sarvesh Joshi , Shubham Mhatre
- Paper ID : IJERTV9IS050667
- Volume & Issue : Volume 09, Issue 05 (May 2020)
- Published (First Online): 29-05-2020
- ISSN (Online) : 2278-0181
- Publisher Name : IJERT
- License:
This work is licensed under a Creative Commons Attribution 4.0 International License
Design, Development and FEA of 3-Point Actuated Digging and Conveyor System for Self-Propelled Onion Harvester
1Sumedh Joshi , 2Sanket Sathe , 3Sarvesh Joshi , 4Shubham Mhatre
1234Student, Mechanical Department, Dr. Vishwanath Karad MIT World Peace University Kothrud, Pune, India
Abstract – India is the second largest producer of onions in the world next to China. But the productivity of onions in India is very low i.e. 14.21 tons/ha. There is a huge requirement of man power and time, as harvesting of onions is a rigorous work. Our motive being to conceive, design, fabricate and develop "3-Point Actuated Self-propelled Onion Harvester" i.e. to develop a mechanized technique for onion harvesting which can run on vehicle power supply and won't require any other external power source. This system will have better performance in terms of productivity, fuel economy, operator comfort and reduce the damage to crops, human fatigue, and time. There are majorly two systems working simultaneously which are the digging system- to loosen the soil and get the onion bulbs out without damaging and conveying system that conveys the onion bulbs. Various factors are considered for designing such as type of soil, depth of onion bulbs, size of onion bulbs and damage to onion bulbs.
Keywords 1. 3 point actuator system 2.Self Propelled 3.Less damage to onion bulbs 4.Productivity 5.FEA Analysis
-
INTRODUCTION
Digging System scoops into the soil and pushes the onions and soil mass onto the conveying and windrowing system. This system loosens the soil and gets the onion bulbs out without damaging the onion. It consists of a trapezoidal scoop and V- shaped digging blade designed based on draft acting on it while harvesting the onion.
Conveying system was designed such that while the onion bulbs are segregated from soil mass while being conveyed at the end, to a predetermined height. The 3-point actitation system was designed to vary the digging depth of the system considering the variations in soil and onion bulb depth.
-
DIGGING SYSTEM
-
Digging Scoop
The digging scoop is a trapezoidal unit consisting of 10 evenly spaced blades. A brief study on onions led us to conclude that the average onion bulb diameter is around 60 mm. Hence, we selected out depth of digging operation as 80 mm ensuring that the onion doesnt get damaged. These factors were considered to design the digging scoop.
-
Shape and Shape Factor – Onions can be considered as oblate or prolate.
SF = Equatorial Diameter / Polar Diameter Shape Factor > 1 for Oblate Onions
Shape Factor < 1 for Prolate Onions
Here Equatorial diameter is the maximum diameter and polar diameter is the height of onion
-
Bulk Density – The weight of seed per unit volume BD = W/V
Where, BD = Bulk density, g/cm3 W = Weight of seeds, g
V = Volume of seeds, cm3
-
Coefficient of static friction –
The coefficient of static friction on mild steel for onion plant is equal to the tan of angle of static friction.
Coefficient of static friction = tan ø Where ø is the angle of static friction.
-
Crushing resistance of onion bulb – The resistance of onion bulbs to deform or crush due to force applied upon them is called as the crushing resistance of onion bulb.
-
Bulk density of soil – It is defined as the mass of the dry soil per unit volume denoted by p.
-
Cohesion and angle of internal friction -Cohesion is the property of materials to stick together to the same material. Angle of cohesion is found from the following equation
T = C + (sigma)tan Where, T = Shear stress
C = cohesion sigma = normal stress
= Angle of internal friction
-
Angle of soil metal friction – The angle at which the dynamic friction just starts between the metal and soil is defined as the angle of soil metal friction.
µ = tan Where, µ = friction coefficient
= Angle of soil-metal friction
Taking into account all the attributes, the blade geometry was selected with the help of (1)
2
2
Pp = z1 N + Cz1Nc + Caz1Nca + qz1Nq (1) Where,
Pp = Passive resistance of soil acting at angle of soil metal friction with the normal to interface (kg/m)
= bulk density of soil (kg/m2) z1 = depth of operation (m)
Ca = soil interaction adhesion (kg/m2)
q = Surcharge pressure on soil from surface above the failure plane (kg/m2)
N , Nc, Nq and Nca are the dimensionless less factor. These are the function of angle of shearing resistance of soil (), angle of soil metal friction () and geometry of loaded interface.
The corresponding assumptions were made
1. Avg. bulk density of Soil i.e. = 1450 kg/m3
-
Cohesion of Soil i.e. C = 30.18 kN/m2
-
Adhesion of soil can be taken as 0, i.e.
Ca = 0
-
Friction = 0 (as soil is scouring over the blade)
-
Surcharge of soil = 0, i.e. q= 0
-
Rake angle of digger blades = 15-25 degree Hence, Equation (1) can be simplified as-
Pp = z1N + Cz1Nc (2)
The values of N-factor for inter-mediate degree of roughness of the interface were found by the equation
N = N = 0 (N=) ×
Where,
(=0)
N = the required value of the appropriate N-factors, N =0 and N = = the corresponding value of the N- factor at = 0 and = , respectively obtained from the appropriate chart = 15.64º
= 29º, = 20º
z1 = 0.8 m
From these values we calculated the following values
N = 1.55
N = 1.75
Nc = 1.65
Nc = 1.60
Substituting these values in (2), we obtained the value of Pp which comes out to be 4.02234 kN/m. The total width of the digger scoop was 0.85m so we found the effective Pp to be
3.419 kN/m.
The passive resistance Pp was acting at an angle of friction() with normal to the interface.
Therefore, Force component parallel to the digger scoop face – Pp1 = 4.022×cos (74.36) = 1.084 kN
Force component perpendicular to the digger scoop face Pp2 = 4.022×cos (15.64) = 3.8730 kN
These force components were used to design the digger scoop and the FEA was also performed.
The thickness of the digger scoop was decided by closely studying other agricultural diggers and a thickness range between 5mm to 8mm was obtained. Later, FEA was performed on these models and the digger scoop with 5mm thickness was selected. The 5 mm thickness model was lightweight and safe for the operation. A 1×1 m MS sheet was laser cut into the required shape and the blades were given an angle of 20o by hydraulic bending. This digger was then bolted to the side support members.
Fig (1) – Top View of the Digger scoop (dimensions are in mm)
Fig (2) – Blade Angle = 20o
Table (1) Digging System Specifications
Material
Mild Steel(ASTM 1006)
Number of Blades
10 (evenly spaced)
Blade Geometry
50×70×5 mm
Shear Blade Rake Angle
20o
Harvesting Width
850 mm
Depth of Digging
8
Thickness
5 mm
-
-
-
FEA Analysis of Digger Scoop
FEA of the Digger Scoop was performed and the most optimum design was selected. Scoop iterations of thickness 5cm, 6cm, 7cm and 8cm were selected ad the analysis was performed.
The analysis included the various factors like equivalent stress, total deflection and equivalent strain. Loads Pp1 and Pp2 were applied to the models and results were obtained. ANSYS® R18.2 version was used.
Table (2) Material Properties
Material
ASTM Steel 1006
Youngs Modulus (E)
200 GPa
Density
7896 kg/m3
Poissons Ratio
0.29
Shear Modulus
7.751E+10 Pa
Bulk Modulus
1.587E+11 Pa
Fig (3) Total Deformation Analysis for 5 mm Thickness
0.099
0.098
0.097
0.096
0.095
0.094
0.093
0.092
0.091
0.09
0.098
0.097
0.095
0.093
0.099
0.098
0.097
0.096
0.095
0.094
0.093
0.092
0.091
0.09
0.098
0.097
0.095
0.093
Strain Percentage (%)
Strain Percentage (%)
Fig (4) Equivalent Stress Analysis for 5 mm Thickness
Fig (5) Equivalent Strain Analysis for 5 mm Thickness
1.2
1
0.8
0.6
0.4
0.2
0
1.2
1
0.8
0.6
0.4
0.2
0
1.0782
1.0782
0.9132
0.9132
0.8437
0.6939
0.8437
0.6939
Deflection (mm)
Deflection (mm)
Analysis of all the models was done and the following results were obtained.
Scoop Thickness
Scoop Thickness
5mm
5mm
6mm
6mm
7mm
7mm
8mm
8mm
Fig (6) Variation of Deflection(mm) with Scoop Thickness (mm)
Equivalent Stress (MPa)
Equivalent Stress (MPa)
200
5mm 6mm 7mm 8mm
Scoop Thickness (mm)
5mm 6mm 7mm 8mm
Scoop Thickness (mm)
Fig (8) Variation of Equivalent Strain Percentage (%) with Scoop Thickness (mm)
Table (3) Variation of weight with thickness
Scoop Thickness
Weight
5 mm
14.92 kg
6 mm
17.9 kg
7 mm
20.88 kg
8 mm
23.87 kg
From the above results, the 5 mm thickness model of the digger scoop was selected. The 5 mm thickness model weighed less and could sustain the soil draft load without failing.
-
-
CONVEYING SYSTEM
The conveying system is used to transfer the onions from the digger scoop to the rear outlet of the system. This system consists of 2 EN8 shafts that were designed by ASME standards. A Stainless-Steel honeycomb mesh belt was used to convey the onions. This belt was selected by taking into account the extent of damage different honeycomb belts might cause to the onions and the maximum sustainable load that a belt can bear. The belt mesh spacing was about 3cm to ensure that the onions dont pass through it. The chain and sprockets were designed to sustain the maximum draft load of the soil and onions.
150
100
50
0
178.9
162.3 152.5 145.2
5mm 6mm 7mm 8mm
Scoop Thickness (mm)
Fig (7) Variation of Equivalent Stress (MPa) with Scoop Thickness (mm)
Fig (8) – Onion Harvester Assembly
The conveyor was designed to work at an angle of 17o to ensure maximum efficiency and minimal damage to the onion bulbs.
Table (3) Conveying System Specifications
Term
Specification
Conveyor Belt Material
Stainless Steel
Shaft Material
EN8
Shaft Diameter
30 mm
Speed of Conveyor
3.13 m/s
Length of Conveyor
553 mm
Width of Conveyor
740 mm
Angle of Conveyor
17o
Material Handling Capacity
0.0993m3/s
Power Consumption
1.08 HP
Sprocket Pitch
12.7 mm
No. of chain links
56
-
3 POINT ACTUATED SYSTEM
The entire harvester system was made electrically adjustable with the help of 3 linear actuators. The average depth of the onion bulb inside the soil ranges from 6cm to 8 cm. To achieve maximum efficiency and to reduce the damage caused to the onion bulb, the depth of digging operation could be changed. These actuators were selected on the basis of maximum load capacity. An electronic framework was provided to control the motion of these actuators. The 2 front actuators were used to change the conveyor angle and all 3 were actuated to achieve height control. This system was powered from the vehicle battery.
Fig (9) Linear Actuator
JIECANG® JC35L18 actuators were selected for this purpose.
Table (4) Specifications of JIECANG® JC35L18
Load thrust
8000 N
Max. load pull
4000 N
Max IP rating
IPX6W
Stroke length
50-500mm(±2mm)8000N
Noise level
48dB(ambient level35dB)
Motor
24V DC permanent magnet
-
CONCLUSIONS
It is clearly evident that Indian farmers are facing a shortage of labor and efficient farming solutions. There are very less mechanized options in the onion sector. FEA of the digger scoop was performed and the most optimum and lightweight design was selected. The actuator system was tested and tuned for accurate response. Hence, the 3-point actuated self- propelling onion harvester was designed to modernize this
sector and increase the productivity while ensuring minimum damage to the onion crop.
-
ACKNOWLEDGEMENTS (OPTIONAL)
The author can acknowledge any person and authority in this section. This is not Mandatory
-
REFERENCES
-
Tapan Kumar Khura, Design and Development of Tractor Drawn Onion Digger, Division of Agricultural Engineering Indian Agricultural Research Institute, New Delhi. Year 2008.
-
Ashwini Talokar, Kanchan Wankhade, & V. P. Khambalkar, Design of Onion Harvester International Journal and Magazine of Engineering, Technology, Management and Research, Jan 2014.
-
Jafar Massah, Ahmad Lotfi, Akbar Arabhosseini, Effect of Blade Angle and Speed of Onion Harvester on Mechanical Damage of Onion Bulbs, Ama, Agricultural Mechanization in Asia, Africa & Latin America 43(3):60-63, June 2012.
-
O.A. Omar, Soha G. Abdel Hamid and G.A. El-Termzy, Development of an onion crop harvester,Misr J. Ag. Eng., 35 (1): 39 56, Jan 2018
-
Sungha Hong, Kyouseung Lee, Yongjin Cho, Wonyeop Park, Development of Welsh Onion Harvester for Tractor, Journal of Biosystems Engineering, Volume 39 Issue 4 / Pages.290-298 / 2014
-
Sunil Shirwal, Indra Mani, N. P. S. Sirohi & Adarsh Kumar Development & Evaluation of Carrot Harvester, Agricultural Mechanization in Asia, Africa & Latin America, Dec-2015.
-
Sunil Pareek, Sunil Sharma, Vinay Kumar, Narashans Alok Sagar, Onion (Allium cepa L.), Fruit and Vegetable Phytochemicals: Chemistry and Human Health, Edition: Second, Publisher: Wiley Blackwell, John Wiley & Sons Ltd., Editors: ElhadiM.Yahia, pp.1145-1161 (16), May 2017.
-
Pham Hoang, Design and simulation of micro-linear actuator, 2010 IEEE Conference on Robotics, Automation and Mechatronics, July 2010.
-
-
BIGRAPHIES
Sumedh P. Joshi, pursuing third year in Bachelor of Mechanical Engineering from Dr. Vishwanath Karad MIT World Peace University, Pune, Maharashtra, India.
Sanket N. Sathe, pursuing third year in Bachelor of Mechanical Engineering from Dr. Vishwanath Karad MIT World Peace University, Pune, Maharashtra, India.
Sarvesh P. Joshi, pursuing third year in Bachelor of Mechanical Engineering from Dr. Vishwanath Karad MIT World Peace University, Pune, Maharashtra, India.
Shubham K. Mhatre, pursuing third year in Bachelor of Mechanical Engineering from Dr. Vishwanath Karad MIT World Peace University, Pune, Maharashtra, India.