
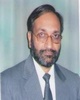
- Open Access
- Authors : Dr. J P Yadav , Dr. Devendra Kumar , Pratyush , Devendra Singh
- Paper ID : IJERTV11IS030129
- Volume & Issue : Volume 11, Issue 03 (March 2022)
- Published (First Online): 01-04-2022
- ISSN (Online) : 2278-0181
- Publisher Name : IJERT
- License:
This work is licensed under a Creative Commons Attribution 4.0 International License
Design, Fabrication and Performance Evaluation of Power Operated Groundnut Decorticator
2
Dr. J P Yadav1, Dr. Devendra Kumar
4
, Pratyusp and Devendra Singh
1,2 Professor, Faculty of Agril Engg & Tech, (C.S.A. Univ of Agri & Tech, Kanpur) Campus Etawah, U.P.
4 Faculty, Faculty of Agril Engg & Tech, (C.S.A. Univ of Agri & Tech, Kanpur) Campus Etawah, U.P.
3 Faculty, Department Civil Engineering, Kamla Nehru Institute of Technology, Sultanpur, U.P.
Abstract:- Groundnut cultivation in India is done by small scale farmers. The biggest problem in the production of groundnut in our country like India is the non-availability of better use of groundnut decorticating machines with the farmers. In this paper a low-cost groundnut decorticating machine has been designed and manufactured which will help small farmers to decorticate the finished groundnut and it can easily be manufactured by local artisans. This paper uses drums with rubber linings glued on the periphery of rotating drum or decorticating tool. Rubber pads/ linings are used for free crushing of groundnut to reduce the damage. This decorticator gives more output in less time with less effort. Machine performance was assessed in terms of decorticating efficiency, damage kernel percentage, unshelled pods percentage, and decorticating output. The main parts of the machine are hopper, crushing chamber, cylindrical tool, semi-circular sieve, kernel collecting tray and blower.
Key words: Groundnut, groundnut decorticator, decorticating efficiency, damage kernel percentage
-
INTODUCTION
Groundnut botanically known as Arachis hypogea belongs to the Leguminosae family. India is the second largest producer of groundnut after China. It is reported that South America was the site from which peanut cultivation began and spread to Brazil, southern Bolivia and north-western Argentina. Groundnut was brought from Brazil to West Africa and then to South-West India by the Portuguese in the 16th century. Groundnut is a major oilseed crop in India. Out of more than 18 million hectares of land under edible oil is available only from groundnut seeds. India is the largest producer of groundnut in the world (32% of world production). Between (19501951) and (199899) there has been a significant increase in crop area (68.5%) and production (63%). The maximum growth in area has been recorded in the decades (195051) and (196061) (43.8%), while the decades (1980
81) and (199091) have been very favorable in terms of production (50%). Crop area has increased at the cost of cotton, jowar, bajra and cotton. Groundnut is a popular crop of South India. The four peninsular states – Andhra Pradesh, Tamil Nadu, Karnataka and Gujarat together contribute to more than 80% of groundnut area and production in the country.
Andhra Pradesh is the third largest producer, accounting for 24.69 per cent of the country's total area and 18.79 per cent of the total crop production. Maharashtra ranks fifth in the
country in terms of area (7.07%) and production (10.04%) of groundnut. Madhya Pradesh contributes to the country's total area (3.19%) and groundnut production (2.77%). Groundnut is also produced in various states like Rajasthan, Uttar Pradesh, Orissa and Punjab. In addition to oil extraction ranked 6th in the world's oil production from vegetable and sea peanuts, groundnut kernels are used to prepare varieties of food for human consumption. Equally good number of groundnuts are used for breakfast; hence this crop is of vital importance in India. Decorticating groundnuts is a difficult and time-consuming process. The job of the decorticator is to remove the kernels from the pods. The mechanical decorticators thus developed were used in the oil milling industries where the broken kernels as well as the sound kernels were crushed to extract the oil. The general trend in the village was that the dried groundnut pods were crushed with a stone thus separating the husks and kernels. This practice damages the viability of seeds thereby affecting germination. The use of a suitable decorticator will reduce both the time and labor required to decorticate the kernels and increase the income of the farmers. Due to the lack of storage facilities and the simple way of processing groundnuts, large quantities of groundnuts were destroyed every year. The process of separating the kernel is called decortication. Groundnut should not be decorticated in places with high humidity. The moisture content of 9% (w.b.) was found to be suitable for decomposition by Bahera et al. (1995). The minimum clearance should be chosen in such a way that only the pods are deformed, not the kernels. Demonstrated automatic groundnut decorticator with 95% shelling efficiency and output range 20-25 kg/h, Singh et al. (1993). The reciprocating peanut sheller achieved 95.32% shelling efficiency, damaged seeds 6.12% and unshelled seeds 4.68%, according to Helmy et al. (2001). The manually operated roasted peanut seed peeler has a peeling chamber which greatly reduces the amount of breakage during peeling with 85% peeling efficiency, Ikachukwu et al. (2014). Kumar et al. (2018) researched on Elixir for Connect and Disconnect of Agriculture.The peanut pod and shell stripper removed barriers to open peanuts with a rotational mechanism, studied by Karthik et al. (2018). Pedal operated sheller can be used for groundnut decortication and is advantageous in view of low operating cost with shelling efficiency of 75-85% by Meshram et al. (2018). Electric powered peanut peeling machine saves electricity consumption and is easy to operate
and transport. The machine can be used for both domestic and industrial purposes (Vishwakarma et al. 2015). To simplify the removal of husk from groundnut pods, a simple mechanism-based machine was introduced in which the mode of operation can be manual and electrically. This machine has stable performance with long life, high shelling rate, high output, less damage and quality kernel. It can be suitable for processing various types and sizes of blanched peanut seeds. This work includes design and manufacturing of Power Operated groundnut (Peanut) Decorator which is powered by
0.50 HP, 1440 rpm electric motor.
-
MATERIALS AND METHODS
The machine was constructed with major components viz. Electric motor, pulley, shaft, bearing, supporting frame of power operated device, cylindrical device, sieve, decoration chamber and electric blower as shown in Fig. 1 to 4. An electric motor of 0.50 hp was installed on the angle frame to give power. A pulley D1 of 64 mm diameter was fixed along the motor shaft. One end of the middle shaft was attached with a pulley of size 228 mm in diameter (D2). Pulley D2 was connected with the motor shaft pulley D1 with the help of a V-belt to obtain motor power. The machine is fitted with a shaft which is supported by ball bearings. The cylindrical tool is made of mild steel and the length size is 559 mm. The tool is mounted on a transmission shaft of 965 mm in length and
25.4 mm in diameter. The decoration chamber is made up of a cylindrical drum of length 600 mm with a diameter of 410 mm. Power transmission system is fixed with suitable frame. The main frame is made of angle iron of size 40×40×5 mm. It provides a base made of two angles of 686 mm each width and 762 mm in length. All parts of the machine were supported on this angle iron frame. V-belts are chosen with the required length, width and height of 1778 mm, 12.7 mm and 7.9 mm. When selecting the belt, mainly considering the speed ratio of the pulley, the diameter of the pulley on the mchine shaft, the rotational speed of the pulley on the machine shaft, the diameter of the motor pulley, the rotational speed of the motor shaft and the power to be transmitted. Cylindrical tool is used for high production rates and uniform decortications with six toothed plates mounted in a cylindrical arrangement and made of mild steel. The plates are arranged in a cylindrical form with the help of two circular rings. The semi-circular sieve is one of the main parts that provides friction with the motion of the circular tool helping to remove the pods.
Semi-circular sieve is made of 1.5 mm thick slotted MS Sheet. The dimensions of the slotted sieve are 600×600 mm. The dimensions of each slot were 45×9 mm with approximately 2425 slots per 100 cm2 of area. There are two pulleys of different sizes on the machine. A 64 mm diameter pulley is mounted on the motor. The 228 mm diameter pulley is mounted on the transmission shaft. The required maximum tool shaft speed was 400 rpm, so to achieve 400 rpm speed from a 1440 rpm electric motor over the size of the required pulleys.
Fig. 1 Front view of groundnut decorticator Mk-I
Fig. 2 Side view of groundnut decorticator Mk-I
Fig. 3 Groundnut decorticator Mk-II
4. Pulley
Number of Pulley 2
Diameter of Driving pulley 64 mm
Diameter of Driven pulley 228 mm
5. Semi-circular
sieve or Net
Length
600 mm
Width
600 mm
Slots size
45×9 mm
6. Bearing
Type of beari
ng Ball Bearing
Number of be
arings 2
Diameter of b
earings 60/60 mm
7. Shaft
Number of sh
afts 1 (main transmission shaft)
Diameter of main shaft 25.4 mm
8. Electric blow
er
Blades size
406 mm
Speed
1440 rpm
9. Belt
Size
A70 (length 1778mm)
10. Hopper
Capacity
7 kg
11. Decorticating
Tool
Type
Cylindrical having six bars
Length
559 mm
Diameter
330 mm
12. Collecting ke
rnels tray
Length
720 mm
Width
530 mm
Fig. 4 Groundnut decorticator Mk-II
A transmission shaft size 25.4 mm in diameter and 850 mm in length is placed on the machine. The size of the shaft is selected according to the size, weight of the driven pulley. These were respectively 228 mm, 6.3617 N. Another criterion of selection was the tension of the belt coming from the IS (T1 = 77.784 N, T2 = 6.858N). The yield stress was 550 N/mm2 and the safety factor was considered to be 2, so the working stress was 270 N/mm2 and the permissible shear stress was 151.21 N/mm2. Two ball bearings were fixed on the machine.
The inner diameter of the ball bearing is 25.4 mm according to the shaft diameter. Wet lubrication is used to lubricate the bearings for smooth operation. A 0.50 hp single phase and 1440 rpm electric motor was used to operate the machine. The total power required by the machine was mainly considered during the selection of motor for Power Operated Groundnut Decorticator. Calculated speed of tool shaft and torque required on tool shaft for power consumption. According to the literature, a 227.54 W, 1.0 hp motor was selected for the total power. But 0.5 HP motor was selected in Modified Power Operated groundnut decorticator as the weight of the tool shaft was comparatively high and the blower unit operated through a separate motor. An electric blower was used to separate the groundnut kernels and husks. Blower size is 406 mm and speed are 1440 rpm. Casing was provided to prevent groundnut splatter.
Table 1: Specifications of Modified Groundnut Decorticator
Sl.
No.
Particulars
Specifications
1.
Type of machine
Power operated groundnut decorticator
2.
Overall dimension
Length
762 mm
Width
686 mm
Height
762 mm
Weight
96 kg
3.
Power Unit
Power Unit
Electric motor
Horse power
0.50 hp
Revolution per minute
1440 rpm
Mk-II
-
RESULTS AND DISCUSSION
The power operated groundnut decorticator Mk-I and Mk-II was tested for its performance observing Indian standard power thresher safety requirement (IS9020:2002) and following Indian Standard Groundnut decorticator – Test code (IS 11473:2002). The data obtained for decorticators (Mk-I &
II) are tabulated at tables 2 & 3.
The observation of Table-2 about groundnut decorticator Mk-I reveals the breakage varying from 4.19 to
4.95 % with an average value of 4.63%, while the decorticating efficiency varies from 92 to 94.15 % with an average value of 92.63%. The data is obtained with specified ambient condition and specific moisture content as per Indian Standard Groundnut decorticator Test code (IS-11473:202). The decorticating tool speed is maintained maximum to 400 rpm. The average capacity of power operated decorticator Mk-I is found to be 247.27kg/h.
The performance of groundnut Decorticator Mk-II is tabulated at Table 3 reveals the breakage varies from 3.65 to
-
% with an average value of 4.02% while average decorticating efficiency and capacity of decorticator is found to be 95.06% and 334.63kg/h respectively with varying speed of drum from 250 to 400rpm while the moisture content of the pods is between 10.5 and 22.5%. The energy consumption analysis is done for with-load and without load of both the machines for its decorticating capacities and is shown at table 4 & 5.
Table 2: Data obtained by power operated Groundnut Decorticator (Mk-I)
Sl.
No.
Qty. of groundnut, g
Time taken, s
Decorticated Kernel, g
Undecorticated Kernel, g
Broken Kernel, g
Breakage, %
Decorticating Efficiency, %
Capacity of decorticator, kg/h
1
350
5
160
35
7
4.19
90.00
252.00
2
450
7
288
33
15
4.95
92.67
231.42
3
550
8
360
40
17
4.51
92.72
247.50
4
650
9
393
38
20
4.84
94.15
260.00
5
750
11
450
48
22
4.66
93.60
245.45
Average value
4.63
92.63
247.27
Table 3: Data obtained by power operated Groundnut Decorticator (Mk-II)
Sl. No.
Moisture content, %
Qty. of groundnut, g
Speed of drum, rpm
Time taken, s
Decorticated Kernel, g
Undecorticated Kernel, g
Total husk, g
Unbroken Kernel, g
Broken Kernel, g
Breakage, %
Decorticating Efficiency, %
Capacity of decorticator, kg/h
1
10.5
1000
250
10.00
810
40
150
776
34
4.19
96.00
360.00
2
10.5
1500
200
18.75
1205
70
225
1161
44
3.65
95.33
288.00
3
10.5
2000
300
16.67
1600
110
290
1535
65
4.06
94.50
431.91
4
22.5
1000
350
13.00
775
55
170
735
40
3.84
94.50
276.92
5
22.5
2000
400
22.75
1590
100
310
1520
70
4.40
95.00
316.48
Average value
4.02
95.06
334.63
Table 4: Energy consumption by power operated Groundnut Decorticator (Mk-I)
Trial s
Without Load
With Load
Capacity of decorticator kg/h
Voltag
, e
Current in amp
Unit consumption kWh
Voltag e
Current in amp
Unit consumption kWh
Energy consumption kWh/kg
T-1
252.00
170
1.18
0.2006
170
2.48
0.4216
0.0011
T-2
231.42
220
1.61
0.3542
220
3.02
0.6644
0.0018
T-3
247.50
256
2.29
0.5862
256
4.21
1.0777
0.0027
Average unit consumption
0.38033
Average unit consumption
0.7212
0.0018
Table 5: Energy consumption by power operated Groundnut Decorticator (Mk-II)
Trials
Without Load
With Load
Capacity of decorticator, kg/h
Voltage
Current in amp
Unit consumption kWh
Voltage
Current in amp
Unit consumption kWh
Energy consumption kWh/kg
T-1
360.00
220
2.59
0.5698
220
4.69
1.0318
0.0017
T-2
288.00
170
1.80
0.3060
170
3.02
0.5134
0.0010
T-3
431.91
256
3.11
0.7961
256
5.98
1.5308
0.0022
Average unit consumption
0.5573
Average unit consumption
1.0253
0.0016
Table 6: Performance comparison of power operated Groundnut Decorticator (Mk-I & II)
Power operated Groundnut Decorticator
Breakage, %
Decorticating Efficiency, %
Capacity of decorticator, kg/h
Energy consumption kWh/kg
Mk-I
4.63
92.63
247.27
0.0018
Mk-II
4.02
95.06
334.63
0.0016
The performance comparison of groundnut decorticators with energy consumptions is shown at table 6. The machine performance data shown at table 6 reveals that the breakage in decorticator Mk-II is lesser than Mk-I because of modification of Mk-II with rubber shoes glued on the periphery of decorticating tools (rotating drum). The decorticating efficiency is also better than Mk-I because the
quantity of un-decorticated kernel to total weight of pods fed in the machine is also less. Similarly, the energy consumption of the groundnut decorticator Mk-II is lesser than Mk-I.
-
-
CONCLUSION
The power operated groundnut decorticator Mk-I and Mk-II were tested for its performance following Indian Standard –
Test code (IS 11473:2002) with following conclusions:
-
The performance of modified power operated groundnut decorticator (Mk-II) was better because the productivity increased and the total losses (damaged and un-decorticated kernels) decreased.
-
The power operated groundnut decorticator Mk-II was more (334.63kg/h) than power operated groundnut decorticator Mk-I(247.27kg/h).
-
The average breakage percentage of groundnut Decorticator Mk-II is 4.02% while average decorticating efficiency is 95.06%.
-
The energy consumption of the groundnut decorticator Mk-II is lesser than Mk-I
ACKNOWLEDGEMENT
The author is thankful to Er. Pankaj Sharma, Asstt. Prof. and
B. Tech. students, viz. Santosh Yadav, Arvind Maurya, Udai Bhan, and Shiv Mohan Singh Yadav from batch 2017; and Vishal Sharma, Upendra Singh, Bholanath, Kamla Kant, Rajan Kumar Patel, Rajnish Kr Tripathi, and Ankit Dixit from batch 2018, for their contribution in Design and fabrication of power operated Groundnut Decorticator, under my supervision.
CONFLICTS OF INTEREST
The authors declare that they have no conflicts of interest.
REFERENCES
[1]. Bahera, B.K., Das, D.K., Pradhan, S.C. and Mahapatra, M. (1995). Effect of machine and crop parameters on groundnut decortication. Agric Engg Today, 19(3-4): 27-32. [2]. Helmy, M. A. (2001). Evaluation of a reciprocating groundnut decorticator. AMA, 32(4):24:27, 35. [3]. Ikachukwu, C.U., Okegbile, O.J., Ikachukwu, I.B. and John, R.T. (2014). Design and development of manually operated roasted groundnut seeds peeling machine. International Journal of Recent Development in engineering and Technology, 2(4):30-35. [4]. Karthik, G., Balasankar, D., Rambabu, G., Nagabhushnam and Naidu, A.L(2018). Design and fabrication of groundnuts pods and shell stripper. International Journal of Engineering Trends and Technology, 58(2):60-64 [5]. Kumar, S.; Singh, R.; Rao, D. U. M. And Chauhan, J. (2018d). Information Needs of Indian Farmers: An Elixir for Connect and Disconnect of Agriculture. Indian Research Journal of Extension Education, 18 (1):37-44. [6]. Meshram, M., Sahu, C.L. and Kumar, A. (2018). Design and fabrication of pedal operated groundnut sheller cum cleaner machine. JETIR, 5(12):747-754 [7]. Singh, G. (1993): Development of a unique groundnut decorticator. Agriculture mechanization in Asia, Africa and Latin America 24(1): 55-59, 64. [8]. Vishwakarma, Arjun, Tandale, T. and Kekan, R.H. (2015). Design and fabrication of groundnut decorticator. IJMIT Vol. 2 issue 2(2): 138-143.Annexure A: Important formulae and parametric relations
1. |
Capacity of machine, C=W/t, kg/h where W= weight of groundnut pods fed in the machine, kg; and t= time taken for decortication, h |
2. |
Decorticating efficiency, percent = (1-Wu/w) x100 where Wu= weight of undecorticated pods, kg; and w = total weight of pods fed in the machine, kg |
3. |
Breakage, percent = Wb x1 00 Wg+Wb where Wb= weight of broken kernels, kg; and Wg= weight of good kernels, kg. |
4. |
Specific energy requirement, E = K/W, where E = energy requirement per kg of pods, kWh/kg; K = energy meter reading, kWh; and W = weight of pods decorticated, kg. |
5. |
Energy consumption, E = 1 [(P x n ) (P x n )] sp Q L L NL NL where Esp= specific energy for decortication, Wh/kg; Q = throughput of the machine, kg/h, PL = watt meter reading(average) at load, W; nL = efficiency of prime mover at load (assume 0.9); PNL = watt meter reading (average) at no- load, W; and nNL= efficiency of prime mover at no-load (assume 0.5) |
6. |
Volume of shelling chamber = r2h Determination of speed of driven pulley, N1D1 = N2D2 Angles of lap, 0 -1 = 180 – 2 sin [ 228.6-88.9)/2560] 1 Length of the belt, L=2x+ (D + D ) + (D1D2)2 2 1 2 4x Velocities of driving and driven pulley, V1 = D1N1/60, V2 = D2N2/60 |
7. |
D3 = 16/Ss[(Kb×Mb)2 +(Kt×Mt)2]1/2 Assuming, Kb, Kt as 2 and factor of safety 2 |
8. |
Power required to drive the threshing bar, PD = T× |
9. |
Power requirement of machine, PT=T× |