
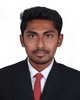
- Open Access
- Authors : B. Prem Kumar , I. Mohamed Akbarali , M. Santhosh
- Paper ID : IJERTV9IS020216
- Volume & Issue : Volume 09, Issue 02 (February 2020)
- Published (First Online): 25-02-2020
- ISSN (Online) : 2278-0181
- Publisher Name : IJERT
- License:
This work is licensed under a Creative Commons Attribution 4.0 International License
Design Modification and CFD Analysis of Two-Cylinder Four Bleeder Valve Brake Caliper for Banjo Bolt
Mr. B. Prem Kumar1, Mr. I. Mohamed Akbarali2, Mr. M. Santhosp.
Department of Mechanical Engineering.
Government College of Technology, Coimbatore.
Tamil Nadu.
Abstract-Brake caliper plays a vital role in hydraulic braking system. The main components of the brake caliper are cylinder, piston, brake pad, banjo bolt, banjo hose and bleeder valve. Generally, one bleeder valve brake caliper or two bleeder valve brake caliper are available in our market. While using these calipers universal mounting is difficult. To overcome that we aimed to make a caliper with four bleeder valves. It is helpful for universal mounting. It is available in foreign markets. If we want four-bleeder valve brake caliper we need to import it. If we make that caliper in India, we can avoid the import cost. In addition to that, we change the shape of banjo bolt from circular shape to diffuser shape to increase the fluid pressure. We design the new four bleeder valve brake caliper using CATIA V5 software and analyses the design using ANSYS 16.2 software. It can be used in commercial vehicle cars as well as in student formula cars.
Keywords:- Four bleeder valve brake caliper, design modification, modelling, CFD analysis.
-
INTRODUCTION
A Caliper is an important part of the disc brake system. When we press the brake pedal, the brake fluid flows from the master cylinder to the brake caliper. Brake fluid then applies the pressure on the piston inside the caliper, pushing the brake pads against the rotors to slow or stop the vehicle. The disc caliper is further classified as floating and fixed caliper. This type of brake uses only a single piston to squeeze the brake pad against the rotor. The reactive force shifts the caliper housing and presses opposite side of braking pad against the rotor. Sameer Ingale et al., [1] investigated that safety aspect in automotive engineering is of prime importance. Effective Braking system along with good suspension systems, good handling and safe cornering is very important for determining the performance of the vehicle. The objective of this work is to design, analyze and investigate the strength and stiffness of the brake caliper during braking operation using ANSYS Workbench 15.0. Rathin Shah et al., [2] explained effective braking is a critical factor determining the performance of any vehicle. With enhancement in the performance, need of an effective braking system increases. Brake caliper being the heart of a braking system, the whole system is built considering its strength. An optimized design of a brake caliper thereby ensures reduced size of wheel assembly, reduced weight and effective braking. Dhananjay Phad et al.,
[3] found that effective braking is a critical factor determining the performance of any vehicle. With enhancement in theperformance, need of an effective braking system increases. This paper studies a conceptual design of a brake caliper for an All-Terrain Vehicle (ATV), primarily focusing on reducing the size and weight without compromising its strength, stiffness and low piston drag. Pravin Mohan Patel et al., [4] justified that the following work-studies a conceptual design of a disc brake system. Disc brakes offer higher performance braking, simpler design, lighter weight, and better resistance to water interference than drum brakes. Dr.A. Satyanarayana Reddy et al., [5] explained this work deals with the study of the existing braking component and designs new braking components using SOLID WORKS to do stress analysis and temperature developed during panic braking. The analysis was done on brake disc of three different materials using ANSYS workbench. The dimensions are taken from existing MARUTI 800. Sarvendra Kumar Mehra et al., [6] described this work is aimed to study the tribological properties difference of potentially new designed non-commercial brake pad materials with and without asbestos under various speed and nominal contact pressure. Sunkara Sreedhar et al., [7] found that the disc brake is a device for slowing or stopping the rotation of a wheel. Friction causes the disc and attached wheel to slow or stop. Brakes convert friction to heat, but if the brakes get too hot, they will cease to work because they cannot dissipate enough heat. This condition of failure is known as brake fade. Aman Singh et al., [8] described the paper deals with the designing and modeling of light floating caliper for two wheelers without interfering with the performance. This would be done without affecting the manufacturing cost, which is a highly challenging point, at the selected position. A physical model is built to evaluate the FE-model with practical tests. The aim is to keep the manufacturing costs low, which is solved by using the same material and shape that follows the same machining steps. To make the caliper lighter it is necessary to remove material.
-
MATERIALS AND METHODOLOGY
The material of a brake caliper body must be rigid to allow less deflection, and should be light to reduce the final weight of assembly. However, most important property considered for selection of the material is the modulus of elasticity as, for a caliper, stiffness is more important than strength. Most of the commercial vehicles use brake calipers made of cast iron because of low cost, high modulus of elasticity (200-
210 GPa) and good machinability. Aluminium can also be used for the manufacturing of caliper considering its lower weight, but modulus of elasticity in this case is less (72-80 GPa). Also, metal matrix composite (MMCs), with base material as Aluminium or Beryllium, reinforced with ceramic fibres which are aligned in proper direction to obtain required strength and stiffness along that particular direction. These MMCs have modulus of elasticity of about 180 GPa.
Table 1: Aluminium Material Properties
Material
Al-7075
Density
2700 Kg/m3
Youngs modulus
72 GPa
Yieldtensile strength
503 MPa
Ultimatetensile strength
590 MPa
Material
Silicon Carbide
Density
3100 Kg/m3
Poissons ratio
0.14
Co-efficient of thermal expansion
4 x 106 /
Elastic modulus
410 a
Material
Silicon Carbide
Density
3100 Kg/m3
Poissons ratio
0.14
Co-efficient of thermal expansion
4 x 106 /
Elastic modulus
410 a
Table 2: Silicon Carbide Material properties
Pistons can be made of Aluminium alloys its properties are shown in table 1. But, thermal conductivity of Aluminium is high, around 200-250 W/mK, which causes the heat generated due to the friction between rotor and friction pads to be transmitted through piston. This leads to decrease in disc temperature, but as the heat is transmitted to the brake fluid, it may increase the temperature of fluid. Higher fluid temperatures may cause changes in compressibility and evaporation of the brake fluid. To overcome this problem, small titanium blocks can be used in between the backing plate of friction pad and he piston surface The five most important characteristics that are considered when selecting a brake pad material are asfollows. The material's ability to resist brake fade, the effects of water on brake fade (all brakes are designed to withstand at least temporary exposure to water), the ability to recover quickly from either increased temperature or moisture.
The material used for brake pad are non-metallic material, semi- metallic material, fullymetallicmaterial, ceramic material. In that, we selected the Silicon Carbide Ceramic material and its properties are in table 2. It has low thermal expansion, high strength even at 1600.
Fig.1. Methodology of work
-
DESIGN CALCULATIONS
a. Design Calculation for new caliper
Kinetic energy (KE)
Mass of the vehicle (m) = 800 kg Velocity of the vehicle (v) = 50 km/hr Stopping Distance (s) = 10 m
KE = ½* m * 2
= ((1)2)*800*192.3
KE = 77060 J.
F = KE / s = 77060 / 10 N.
Pedal Ratio p =((L1+L2)) 2
= (0.12+0.6)2 =0.36.
Master Cylinder Input Force:
F1 = ((driver foot input force) (2)) *P
= ((490.5) (2) *0.36) F1=88.29 N.
A1=1.96 * 103 2.
P1 =F1A1=88.29 ((103*1.96)) P1 = 45045.9 N/m2.
For Normal Caliper,
D2 = 60 mm = 0.06 m A2= 0.0113 2 F2=((F1) (A1) *A2)
= 509.018 N
For New Caliper,
Small diameter d2 = 0.048 m Large diameter D2 = 0.06 m. A2=(0.00723 + 0.0113)2 A2= 0.009267 2.
F2=(88.290.00196) 0.009269 F2 = 417.44 N. P2=417.440.009269
P2 = 45045.9 N/m2
-
DESIGN MODIFICATION AND CFD ANALYSIS
-
Design of existing caliper
Normally the existing brake caliper comes under either fixed caliper or floating caliper. The brake caliper used in most of the vehicles has one bleeder valve or two bleeder valves and the shape of the cylinder in the brake caliper is in circular shape. The banjo bolt is normally in the shape of bolt with hexagon head on it. Below the head, small hole is placed in a parabolic region. In that, initially the pressure is developed, and it flows through the hole and forces the piston to squeeze the brake pad. To connect banjo bolt and brake hose, banjo hose is required. We designed the existing brake caliper using CATIA V5 and analyzed the design using ANSYS 16.2 shown in fig.2.
Fig 2: Design of normal caliper
-
Design of newcaliper
In our new design we change the shape of the banjo bolt as diffuser shape, we also modify the shape of the caliper cylindrical shape as conical shape. The general working of the diffuser is to increase the pressure, likewise the pressure builds in the banjo bolt increase and it forces the brake pad to squeeze the disc brake with more amount of fluid pressure. Therefore, the braking time and braking distance will consequently reduce. We also increase the number of bleeder valve for universal mounting. It will minimize the assembly line timing while manufacturing as shown in fig. 3 to fig.6.
Fig 3: Brake caliper with four bleeder valve
Fig 4: Diffuser shape banjo bolt
Fig 5: Conical cylinder shape of caliper
Fig 6: Conical cylinder and diffuser shape banjo bolt
-
CFD analysis for existing caliper
We used the Ansys16.2 software to analyses the existing design as shown in fig.7. For analysis we need to import the file in IGS format. Then in the meshing category we need to
give the mesh element size according to our requirements, here we choose it as 1mm. Then we choose the input and output body elements. After that in the setup category we selected the scale in terms of mm, the medium is Ethyl glycol because it is the primary component of the DOT 4 brake fluid. The material for the body is Aluminium. Then we give the input parameter as pressure. The value of the pressure given is 2400 N/m2. The output value is also measured in terms of pressure. After given the number of iterations as 300 we get the result.
Fig 7: CFD analysis of cylinder arrangement
-
CFD analysis for new design
Fig 8: Analysis of diffuser shape banjo bolt
Fig 9: Analysis of conical cylinder shape of caliper
Fig 8: Analysis of diffuser shape banjo bolt
Fig 9: Analysis of conical cylinder shape of caliper
We used the Ansys16.2 software to analyses the existing design as shown in fig.8 to fig.10. For analysis we need to import the file in IGS format. Then in the meshing category we need to give the mesh element size according to our requirements, here we choose it as 1mm. Then we choose the input and output body elements. After that in the setup category we selected the scale in terms of mm, the medium is Ethyl glycol because it is the primary component of the DOT 4 brake fluid. The material for the body is Aluminium. Then we give the input parameter as pressure. The value of the pressure given is 2400 N/m2. Input and output values of pressure shown in table 3.
Fig 10: Analysis of conical cylinder and diffuser shape banjo bolt
Table 3: Input and Output value of pressure
Design shape
2
Pressure value (N/m )
Diffuser shape banjo bolt brake caliper
2446
Conical cylinder shape brake caliper
2548
Conical cylinder and diffuser shape banjo bolt brake caliper
2410
The input value of pressure for all designed shapes is -2400 N/m2.
-
-
CONCLUSION
In this project, we studied about the conceptual design, analysis and optimization of a brake caliper system. Here an attempt was made to design a fixed brake caliper with four bleeder valves considering various parameters and was analyzed for its performance at normal conditions and we changed the shape of banjo bolt in order to improve its efficiency. Finally, in India our brake caliper with four bleeder valve may use in future. Therefore, the import cost and time can be reducing for the four- bleeder valve brake caliper. Our plan to increase the pressure in the brake caliper by changing the shape of the banjo bolt which is not effective as much as our expectation because the Pascal law does not depend on the shape of the cylinder. However, the diffuser shape banjo bolt approximately gives the same pressure as the existing design, so our design change can be able to reduce production time and cost of the banjo bolt for same efficiency.
Table 4: Comparison between existing banjo bolt and new banjo bolt shape
Existing banjo bolt shape |
Modified banjo bolt shape |
Brass rod is used as a raw material |
Hollow pipe is used as a raw material |
Banjo hose and copper washer are required |
No need for banjo hose and washer |
Turning, threading and drilling operations should be carried out |
Turning and threading operations should be carried out. |
REFERENCES
-
Rudolf Limpert, Brake Design and Safety (Second Edition) ISBN1- 56091-915-9.
-
Sameer Ingale, Sanket Kothawade, Aditya Patankar and Rohit Kulkarni, Design and Analysis of a Brake Caliper – Volume 7, Issue 4, JulyAug
2016, pp.227233, Article ID: IJMET_07_04_024; ISSN Print: 0976-
6340 and ISSN Online: 0976-6359.
- p>Rathin Shah, Chinmay Shah and Swapnil Thigale, Design and Analysis of a Hydraulic Brake Caliper – Volume 8, Issue 5, May 2017, pp. 33 41, Article ID: IJMET_08_05_004; ISSN Print: 0976-6340 and ISSN Online: 0976-6359.
-
Dhananjay Phad, Tejas Auti, Rucha Joshi, Swapnil Jadhav and Sagar Devasthali, Design and Analysis of a Brake Caliper – ISSN(P): 2277- 4785; ISSN(E): 2278-9413; Vol. 5, Issue 5, Oct 2015, 1-10.
-
Pravin Mohan Patel, Sudheendra S, Design and Analysis of Titanium Brake Caliper- 2017 IJEDR | Volume 5, Issue 1 | ISSN: 2321-9939.
-
Dr.A.Satyanarayana Reddy, Shaik Mudassir Mohiddin, Syed Uzair Ul Hasan and Syed Sajjad Ali Anas, Design and Analysis of Disc Brake and Caliper of Four Wheeler – Volume 3 | Issue 08 | February 2017; ISSN (online): 2349-784X.
-
Sarvendra Kumar Mehra, A Review of Experimental Study of Brake Pad Material – Issue 3, Vol.6 (November 2013); ISSN 2249-6149.
-
Sunkara Sreedhar, Parosh.G, Design and Structural Analysis of Disc Brake by using CATIA and Ansys-Workbench – Volume: 04 Issue: 09 | Sep -2017; e-ISSN: 2395-0056; p-ISSN: 2395-0072.
-
Aman Singh, Aadhar Bisht, Design and Analysis of Floating Caliper for Two wheelers – ISSN: 2321-9653; IC Value: 45.98; SJ Impact Factor
:6.887, Volume 5 Issue XII December 2017.
-
Dhir, Daanvir Karan. "Thermo-mechanical performance of automotive disc brakes." Materials Today: Proceedings 5.1 (2018): 1864-1871.