
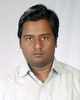
- Open Access
- Authors : Shailesh Madan Rawool , Vallurupalli Murali Mohan
- Paper ID : IJERTV11IS040016
- Volume & Issue : Volume 11, Issue 04 (April 2022)
- Published (First Online): 12-04-2022
- ISSN (Online) : 2278-0181
- Publisher Name : IJERT
- License:
This work is licensed under a Creative Commons Attribution 4.0 International License
Design of Active Suspension System for Quarter-Car Model using Linear Quadratic Regulator (LQR)
Shailesh Madan Rawool
Department of Mechanical Engineering, Finolex Academy of Management and Technology,
Ratnagiri, Maharashtra-415639, India
Vallurupalli Murali Mohan
Department of Mechanical Engineering, Finolex Academy of Management and Technology,
Ratnagiri, Maharashtra-415639, India
Abstract This paper presents designing of an optimal state feedback controller, Linear Quadratic Regulator (LQR), for a quarter-car suspension system. The suspension system dictates the dynamic behaviour of the vehicle arising from the road interactions and body forces. The performance of a suspension system is indicated by the occupants comfort, suspension deflection, and vehicle handling on the road. Conventional passive suspensions system compromise comfort and road handling. Thus, using external force actuation, active suspensions are proven to be superior in retaining suspension performance for a wider range of operating conditions. Control strategy determines the performance of active suspensions. In this study, an LQR controller is designed that minimizes the suspension deflections with the application of optimal control effort. The system response can be tuned by varying the values of weighting factors. A method to determine these weights is demonstrated to yield feasible results while reducing the number of trials required. A simulation study of the system response to different weighting factors is conducted and changes in the suspension characteristics are illustrated graphically. The simulation results demonstrate that a finely tuned LQR controller retains excellent comfort and handling characteristics compared to the passive counterpart.
Keywords Active Suspension System; LQR; Quarter-car model.
-
INTRODUCTION
The vehicle suspension system governs the dynamic behaviour of the vehicle, owing to road disturbances and body forces acting on the vehicle. The suspension system connects wheels and the vehicle body, which supports the body mass and transmits the forces between road and body. A well-designed suspension system isolates the vibrations arising from the road surface irregularities and various internal sources, thus providing better comfort. Also, the suspension system aid in maintaining adequate contact forces between road and wheels to provide proper road handling which ensures drive safety [1]. Passive suspension systems consist of spring and shock absorber arrangements, which have a fixed spring stiffness and damping coefficient, respectively. For better isolation from the road-induced vibrations, a soft damper is required. However, soft damping causes large suspension deflections, lowering the contact forces. Conversely, for better road adhesion a hard damper is recommended, which restricts the excessive suspension deflection. However, hard damping induces high- frequency vibrations in the vehicle, lowering the comfort [2]. Thus, comfort and road safety are conflicting criteria in
suspension system design, and a passive suspension system design is a compromise between comfort and safety.
An active suspension system resolves the conflict between comfort and safety using an external force actuator. The actuator creates the desired control force for isolation and damping, irrespective of suspension deflection. Thus, the active suspension provides superior comfort and handling compared to passive systems. The active suspension uses sensors that measure the motion of the vehicle body and suspension components. The data is then fed to the control system that computes the control signal for the actuator input. Actuators require a significant amount of energy, which necessitates the computation of minimal control force input [3]. Insights into active suspension design, control strategies, and their implementation are found in [4]-[6].
The performance of the vehicle suspension system is measured using different parameters needed to be optimized. These parameters are as follows:
-
Ride Comfort depends on the vibrations and harshness experienced by the occupant, hence measured using the vertical acceleration sensed by the occupant.
-
Suspension Deflection is the measure of vehicle body displacement relative to the wheel. It is also a design constraint that depends on available workspace or rattle space.
-
Road Handling depends on the adhesion between the wheel and the road surface. The adhesion is characterized by the contact forces and measured as the tire deflection.
An optimal state feedback controller optimizes the actuator input by minimizing the cost function. The cost function is expressed in terms of system states and control input, for the system expressed in state-space form. The states represent the suspension characteristics in comfort and handling, to be minimized. A detailed account of the vehicle dynamics applications of the optimal control is found in [7], while [1], [3], [8], and [9], study the application of LQR in active suspension design.
In this study, we design a Linear Quadratic Regulator (LQR) controller for an active suspension system, based on a 2- DOF quarter car model of the vehicle. The controller performance is investigated in a simulation environment using MATLAB/Simulink. A simulation study features the performance of the controller for different tuning factors. This information is used to tune the controller to obtain the required
suspension characteristics. Further, the effectiveness of the designed controller is studied in comparison with the passive suspension.
-
-
MATHEMATICAL MODELLING
-
Quarter-Car Model
The ride dynamics of a typical vehicle are modelled using linear components assuming small deflections and velocities about equilibrium positions. In actual testing, [10] has proven an excellent correlation between the measured and the simulated results. Thus, a simple linear model becomes suitable for the preliminary study of the performance and benefits of a proposed control strategy. A linear quarter car model is preferred in literature for the investigation of lateral dynamics.
For the quarter-car model shown in Fig. 1, the description of the notations used in the model is mentioned in Table I. The values for the suspension elements are used for the simulation study. A 2-DOF quarter car model shown in fig. 1, models the vehicle mass as sprung mass and unsprung mass. The suspension components like spring, damper, and actuator are positioned between two masses. The tire dynamics are modelled as spring with tire stiffness. The disturbances are carried through the tire to the system and conversely, the contact forces are applied by the system to the tire.
Equations of motion for the 2-DOF model are as follows:
+ ( ) + ( ) =
+ ( ) + ( ) + ( ) =
TABLE I. NOTATIONS AND CORRESPONDING VALUES FOR QUARTER-CAR MODEL
Notation
Description
Values
Units
ms
Sprung (body) mass
350
Kg
mu
Unsprung (wheel) mass
45
Kg
ks
Spring stiffness
30e3
N/m
cs
Damping coefficient
1200
N.s/m
kt
Tire stiffness
350e3
N/m
Fc
Control force
N
xb
Vehicle body displacement
m
xw
Wheel/axle displacement
m
zr
Road profile
m
xb – xw
Suspension Deflection
m
xw – zr
Tire Deflection
m
-
State-Space Representation
For the design and implementation of the LQR controller, the system dynamics are described in a state-space form. The dynamic behaviour of the system is described using the state vector, inputs matrix, outputs matrix, and dynamics matrix. [11] A state-space form of a linear time-invariant (LTI) system is represented as follows:
() = +
= +
For an LTI system, matrices A, B, C, and D, are constant.
Matrix A models the dynamical behaviour of the system, Matrix B models the input behaviour, matrix C controls the output components, and matrix D models the feedthrough components. The state of the system is defined by vector x and input variables are defined by vector u.
Multiple input and multiple-output (MIMO) dynamics are conveniently modelled in state-space form. The states define the suspension performance characteristics to be optimized. The four state variables and two inputs are as follows:
= [ ] = [ ]
Fig. 1. 2-DOF Model of the Vehicle Dynamics
The first state represents the suspension deflection, the
second state represents the vertical velocity of the vehicle body, the third state represents vertical deflection in the tire and the fourth state represents the vertical velocity of the tire. The first input is the road disturbance in the form of vertical velocity. The second input is the control force. The two outputs are sprung mass deflection and acceleration, measured using
sensors attached to the system. However, in this study, we assume that the information about all the states of the system is known. A state observer is used to retrieve this information from sensor measurements.
The matrices of the state-space form, evaluated from equations of motion (1) and (2), are as follows:
0 1 0 1
0
=
0 0 0 1
[]
0 0
1
0
= 1 0
1
Fig. 2. Schematic of LQR control.
[ 0 ]1 0 0 0
= {()() + ()()}
(8)
= [
0 0
0
]
0
Matrices Q and R weights the deviation of the states from
the origin and the control input value, respectively. The weighting matrices, control the rate of convergence of states to
-
Stability
= [0 1 ] (5)
-
-
CONTROLLER DESIGN
the origin, as the control cost minimizes. Thus, weighting matrices function as tuning variables.
The linear quadratic regulator (LQR) control law that minimizes the quadratic cost function is given by,
In state-space form, the stability of the system can be determined by eigenvalues of system matrix A. The eigenvalues of the system matrix are equivalent to the poles described in the conventional control.
() = {( ) = 0, } (6) Let, k be k eigenvalues of system A. For the system to be
stable, all the eigenvalues must have the negative real part, Re(k)<0.
-
Controllability
The controllability of a linear system determines the capability of the input to drive the system to any state in the space and is determined through a controllability matrix.
= [ 2 ] (7) The controllability of the system depends on the rank of the
controllability matrix, which must be the same as the number of states.
-
Linear Quadratic Regulator (LQR)
For a controllable linear system, the state feedback controller gain is evaluated by optimization of the quadratic cost function. The controller gain, to be evaluated minimizes the cost function that represents the measured states of the plant and control input. The states and the inputs are weighted according to their relative importance. Mathematically, the quadratic cost function is as follows:
= (9)
The optimal controller gain for the quadratic cost function
is evaluated analytically as follows,
= 1 (10)
P is the solution to the algebraic Ricatti equation [11],
+ 1 + = 0 (11) The controller gain K is evaluated using MATLAB inbuilt
function, lqr (). The derivations for algebraic Ricatti equation, stability criteria, and controllability are covered in [11] [12].
Applying the LQR control law in (9) to the system model described in (3), the closed-loop system is obtained.
= + () = ( ) (12)
The above equations represent a dynamic system for closed-
loop control, whose stability can be determined using eigenvalues of the matrix (A-BK).
-
Determinating Weighting Matrices
Determination of the weighting matrix is a crucial step in designing the LQR controller. The weighting matrix Q can be decomposed in the following form.
= 0 (13)
Matrix Q0 represents the initial estimates of weights
obtained through Inverse Square of the state variables maximum operating limits, set for the suspension system.
1 2 1 2 1 2
1
0 = diag ((( ))
, ( )
(2)
, , ( ) ) (13)
()
Variables x1, x2, , xn, represent the states of the system.
Matrix Q0 normalizes these state variables. The matrix W is used to impose weights on these normalized state variables. The velocity-dependent variables' weights are set at lower values. For initial results, matrix W is set to identity matrix and subsequently modified using trial and error method, until required performance is obtained.
-
-
SIMULATION RESULTS
The controller design and simulation are done in the MATLAB/Simulink environment. A MATLAB script is used for controller design. The system model is checked for stability and controllability conditions. The initial values for the weighting matrices are determined using the maximum limits of the state variables. Finally, LQR controller gain is evaluated. In the Simulink environment, the closed-loop control of the Active Suspension system is simulated for the dynamic response of the system to a deterministic disturbance input, as shown in Fig. 3. The Simulink model is depicted in Fig. 4, uses the feedback gain K obtained using the MATLAB code, as mentioned in the previous section. In an iterative process, the system is simulated several times for tuning the weighting matrices to obtain desired suspension performance. A comparative study between the designed control system and passive suspension is then performed to determine the effectiveness of the proposed control strategy. The simulation model uses the feedback gain K obtained using the MATLAB code, mentioned in the previous section. In an iterative process,
Fig. 3. Road disturbance (input) signal
the system is the simulated number of times for tuning the weighting matrices to obtain desired suspension performance. A comparative study between the designed control system and passive suspension is then performed to determine the effectiveness of the proposed control strategy.
The problem in controller design is the evaluation of the weighting matrices for the required suspension performance. The initial values of Q0 ae set according to (13) with the state variable limits for suspension deflection and tire deflection set at 0.01 m and 0.05 m, respectively, while initial values of velocity-related states are set at 0.001. The values for W and R, are set initially at identity. Using the trial-and-error method, changes in the system response are evaluated by varying the weighting matrix W. The effect of different weights on the system response is shown in the eigenvalue plot, in Fig. 5., changes in the system response are evaluated by varying the weighting matrix W. The effect of different weights on the system response is shown in the eigenvalue plot, in Fig. 5.
In Fig. 5, it is observed that the open-loop eigenvalues move towards the left as tuning weight W is increased. This increases the overall damping in the system. However, as the weight W is increased further, the leftwards movement of eigenvalues stops, as seen in the cluster of eigenvalues towards the right of
Fig. 4. Simulink model for Active Suspension System simulation
Fig. 5. Eigenvalue plot for the closed loop control. (Solid dot: open-loop eigenvalues, X: closed-loop eigenvalues, diamond: eigenvalues for selected feedback K) Eigenvalues shift from right to left as weight on matrix Q is increased.
open-loop eigenvalues. This point limits weighting as a further increase in W destabilizes the system. Thus, the plot gives a fair amount of information about the approximate location of the tuning weights. The weights are thus selected for the best- observed performance, from a series of trial-and-error experiments.
Fig.6. Control force or actuator input
Fig. 7 and Fig. 8, show the results of the comparative study between the designed active suspension system and the passive system. location of the tuning weights. The weights are thus selected for the best-observed performance, from a series of trial-and-error experiments. Fig. 7 and Fig. 8, show the results of the comparative study between the designed active suspension system and the passive system.
From the results in Fig. 7 and Fig. 8, it is observed that the motion of the vehicle body in active suspension is significantly damped as compared to the passive suspension. A significant decline in suspension deflection is observed which improves
Fig. 7. Comparison of dynamic behaviour of active and passive suspension system
Fig. 8. Comparison of vertical displacements in vehicle for designed active suspension and passive suspension.
the ride comfort. There is less tire deflection implying road handling characteristics are retained. The vehicle bodys vertical acceleration in active suspension is reduced over the span compared to the passive suspension. It should be noted that the presence of direct feed from the actuator to the sprung mass causes vibrations as control effort increases.
The actuator effort for the LQR control is shown in Fig. 6. The control force affects sprung mass acceleration due to the direct-feed present in the system model. These effects can be seen in Fig. 6 and Fig. 7, with similarities in the control effort and sprung mass acceleration graphs. The feed-through component acts as a limiting condition as increasing controller effort contributes to increased sprung mass acceleration. Thus, the problem requires designing the LQR controller that can minimize the state as well as the sprung mass acceleration.
CONCLUSION
In this paper, an LQR based control strategy for an active suspension system is designed. A brief theoretical study of the control strategy provides the necessary preliminary understanding. The paper provides a methodology to design an active suspension system using the LQR control strategy for a quarter car model, which provided ease in modelling and implementation of the control strategy. The problem in LQR design to estimate weighting matrices is addressed through initial approximations, using inverse-square of state variable limits. This significantly reduced the number of iterations and eventually the time consumed in designing the controller. The controller is then tuned by varying the weighting matrices for acceptable suspension performance.
The simulations results for the designed controller of the active suspension system show a significant decline in suspension deflection, which assures ride comfort. The road handling characteristics are maintained as there is no notable change in tire deflection. Thus, the proposed active suspension
control strategy provides better ride comfort while retaining road handling characteristics. The effects of the feed-through term in the system and its effect on the output were observed. This leads to examining the control strategy that can minimize the body acceleration.
The study uses a deterministic model that restricts the scope of comparison between the active and passive systems. Better quantitative analysis can be achieved with stochastic disturbance models and statistical analysis. Further, this study can aid in the design of Linear Quadratic Gaussian (LQG) control strategies, which implement a state observer.
ACKNOWLEDGEMENT
The work in this paper was presented at the International Conference on Innovation Challenges and Advances in Engineering & Technology A Road to Self-Reliant India (ICAET 2021).
REFERENCES
[1] Daniel Fischer, Rolf Isermann, Mechatronic semi-active and active vehicle suspensions, Control Engineering Practice, Vol. 12, pp. 1353- 1367, Nov. 2004. [2] Rajamani R., Design and Analysis of Passive Automotive Suspensions, In: Vehicle Dynamics and Control. Mechanical Engineering Series, Springer, Boston, MA, 2012. [3] E. Esmailzadeh & H.D. Taghirad, Active Vehicle Suspensions with Optimal State-Feedback Control, International Journal of Modelling and Simulation, vol. 18:3, pp. 228-238, 1998 [4] H. Eric Tseng & Davor Hrovat, State of the art survey: active and semi- active suspension control, Vehicle System Dynamics, vol. 53:7, pp. 1034-1062, 2015. [5] Dongpu Cao, Xubin Song & Mehdi Ahmadian, Editors perspectives: road vehicle suspension design, dynamics, and control, Vehicle System Dynamics, vol. 49:1-2, pp. 3-28, 2011. [6] Aboud, W.S., Haris, S.M. & Yaacob, Y., Advances in the control of mechatronic suspension systems. J. Zhejiang Univ. – Sci. C 15, pp. 848 860, 2014. [7] R. S. Sharp & Huei Peng, Vehicle dynamics applications of optimal control theory, Vehicle System Dynamics, vol. 49:7, pp 1073-1111, 2011. [8] Hrovat, D., "Applications of Optimal Control to Advanced Automotive Suspension Design." ASME. J. Dyn. Sys., Meas., Control.; vol. 115(2B): pp. 328342, June 1993. [9] D. A. Wilson, R. S. Sharp & S. A. Hassan, The Application of Linear Optimal Control Theory to the Design of Active Automotive Suspensions, Vehicle System Dynamics, vol. 15:2, pp 105-118, 1986. [10] Healey, A. J., Nathman, E., and Smith, C. C. (December 1, 1977). "An Analytical and Experimental Study of Automobile Dynamics With Random Roadway Inputs." ASME. J. Dyn. Sys., Meas., Control.; vol. 99(4), pp. 284292, December 1977. [11] Johan Ã…ström, Karl and Murray, Richard M., Feedback Systems, Princeton: Princeton University Press, pp. 95-198, 2010. [12] Brunton, S., & Kutz, J. (2019). Data-Driven Science and Engineering: Machine Learning, Dynamical Systems, and Control. Cambridge: Cambridge University Press, pp. 323-362, 2019.