
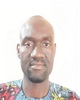
- Open Access
- Authors : I.G. Okoli , U. C. Okonkwo
- Paper ID : IJERTV10IS120004
- Volume & Issue : Volume 10, Issue 12 (December 2021)
- Published (First Online): 15-12-2021
- ISSN (Online) : 2278-0181
- Publisher Name : IJERT
- License:
This work is licensed under a Creative Commons Attribution 4.0 International License
Design of an Improved Double Barrel Cassava Grating Machine
1I.G. Okoli, 2U. C. Okonkwo
(1, 2) Department of Mechanical Engineering, Nnamdi Azikiwe University, Awka Nigeria.
.
Abstract This work presents the design of an improved double barrel cassava grating machine. The need for ease and hygienic processing of cassava has made researchers sought for better and faster way in processing cassava. Hence, for a smooth cassava processing system, a proper design that can guarantee capacity and efficiency should be available for fabricators. Research so far have shown that there are more of single barrel cassava grating machine. In other to obtain the same quantity of grated cassava, an increased number of barrels have been designed. The design made use of Autodesk inventor professional software to produce the CAD model of the machine. Result of the fatigue simulation on the grater shows damage percentage of 1.667e-03 at a maximum 6.000e+07 life cycle. Statice analysis on the structural base shows a small deflection 0.01074 at the load of 1094N. Rigidity of the machine frame was found to be 104.7 × 106N\m
KeywordsCassava, Computer Aided Drafting (CAD), Grating
-
INTRODUCTION
In developing countries, cassava has become a major staple food providing the basic diet for over half a billion of world population (Grubben et al., 2014; Onokwai et al, 2019). The root starch for cassava which has been the core for its cultivation, is mainly used as food (48%) and feed (34%), feedstock (18%) and for biofuels and as well as biochemicals (FAO, 2008). Of all root tubers, cassava has been the most perishable and when the tubers are separated from the main plant and turns out to be unpleasant within two to three days after harvest thereby undergoing post-harvest physiological deterioration (Adjekum 2006; Okonkwo et. al, 2019). Hence, it is necessary to process the crops within three days after harvest. Processing the tubers into pulp form is known as grating (FAO 2005).
Various traditional methods of grating fresh cassava includes; pounding with pestle and mortar, and also the use of hand graters. Making use of hand graters is quite laborious, time-consuming and also dangerous. Cassava grating machines have been designed and also made available on the market. Some of these grating machines include pedal operated engine, dual operational mode machines, the International Institute of Tropical Agriculture (IITA) 202, the Jahn type grater, the GRATIS Foundation (GF) IITA 202- and the Double-barrel cassava grating machine, (FAO, 2005). However, these machines have been widely regarded as inefficient (Kolawale et al., 2010). Due to poor quality of the products, and low efficiency of the technologies which is a
major constraint to the inefficiency of the machines (Quaye et al., 2009). A modern approach which responds quite well to the necessity of mankind is necessary for modern agriculture. This makes it necessary for an advanced mechanized grating machine which will really help in producing sufficient quantity and quality of cassava pulp that will meet market demands and standards.
This study was carried out in order to design and improve a double barrel cassava grating machine. The study was achieved through the study and developing a mechanism of a double barrel cassava grating machine and developing a 3D CAD Model of double barrel cassava grating machine using Autodesk Inventor Professional.
In this work, an improved double barrel cassava grating machine will be designed. The study will be achieved through the development of mechanism of a double barrel cassava grating machine and developing a 3D CAD Model of double barrel cassava grating machine using Autodesk Inventor Professional.
-
LITERATURE REVIEW
Over the years, the need to transform cassava root to pulp for garri production has led to invention of several cassava grating machines available today. Hence the trend of consistent research works has characterized the progressive development of the grating machine. This machine consists of machine frame, electric motor, Chute, Grater, pillow block bearing, hopper etc. These research works and investigations have the common objective of providing optimum cassava grating machine suited for garri processing and which offer the most favorable collection efficiencies at minimum cost.
In other cater for the group of garri producers who have no access to electricity and/or lack the resources or know- how, Odigboh (1984) designed A Manually Operated Cassava Grating Machine. Also, Ndaliman, (2006) focused on power failure problems by developing a grating machine that can be powered either electrically or manually. Adetunji, & Quadri, (2011) Design and Fabricated an Improved Cassava Grater. The work modified the design of the existing cassava grater (dimensions) to the home use-small scale sizes and to change the crude wooden drums used in cassava grating machines to lasting stainless steel and galvanized pipe.
Ajao, et al. (2013) worked on Design and Fabrication of a Home Scale Pedal Powered Cassava Grater. Erratic power supply, scarcity and high cost of petroleum products necessitate the need to address the issue of cassava grating to a certain extent by developing a mechanism that will make life easier in food processing for rural dwellers and improve their economic wellbeing. With the concept of commercializing grating of cassava, Oriaku, et al. (2015) Design and Evaluateed the Performance of a Double Action Cassava Grating Machine, while Okonkwo et al. (2020), optimized a similar system with the aim of achieving a very high throughput in cassava grating and at a reduced grating time.
between the grating barrels and hopper plates through the inclined exit channel and then into the receiver.
DESIGN CONSIDERATIONS
The consideration for the design is to attain light weight with high rigidity, easy installation such as assembly, disassembly and operation, and cost reduction and also to achieve reduced grating time with high throughput.
DESIGN APPROACH
Conceptual drawing
Conceptual drawing
Final design
-
METHODOLOGY
Description of the designed Double Action Grating Machine:
The double barrel grating machine consists of; (1) Structural base, (2) Discharge chute, (3) Inlet hopper, (4) Bearing (Plummer block), (5) Grating Shaft, (6) V Belts,
(7) Pulleys and Idler, (8) Bolts and Nuts, (9) Electric motor,
-
Rivet pin, (11) Barrel, (12) Perforated stainless mesh. The overall length of the machine is 962.086mm, width of 520mm and height of 908.877mm. The large trapezoidal hopper has a large area of 330 x 963.622mm, the base area of 330 x 532mm and the height of 348.716mm. The grating barrel diameter 182mm and a length of 300mm. And the structural frame was made with 60 x 60 x 5mm thick angle iron of top length 528.493mm, base length 738.148mm, slant length 619.565mm, width of 450mm and height of 624.428mm.
Table 1: Materials used in the design of the Cassava Grater.
S/N
Name
Materials Used
1
Structural base
Mild Steel
2
Discharge chute
Stainless Steel
3
Inlet hopper
Stainless Steel
4
Bearing (Plummer Block)
Cast Iron
5
Grating Shaft
Cast Iron
6 V – Belts
Polyester Fibre
7
Pulleys and Idler
Mild Steel
8
Bolts and Nuts
Mild Steel
9
Electric motor
Cast Iron with windings
10
Rivet pin
Stainless Steel
11
Barrel
Oak Wood
12
Perforated Stainless Mesh
Stainless Steel
PRINCIPLE OF OPERATION
The primary rotation of the electric motor is essential for the powering of the grating machine. The two grating barrels rotate in the same direction which is clockwise. The motions of the grating barrels are transmitted through the V belt, pulleys, shafts and bearings by the torque of the electric motor. The shaft is attached to the grating barrel and peeled cassava is fed into the machine through the hopper which makes contact with the rotating grater barrel. The rotating grater then reduces the cassava tuber into pulps. The grated pulp drops through the little gaps
Sketch
Sketch
Design calculations
Design calculations
CAD drawing Working drawing
Fig 1: Design approach for double barrel cassava grating machine
Design OF Machine Components Grating Barrel:
Fig 2: CAD model of the grating barrel (10.75kg)
Centrifugal Force (Fc) developed by the electric
(1)
Where, = mass of belt used for the drive r = Radius of pulley
Mass of Belt ):
Mass = cross-sectional area of belt x density x belt length: = Ab x x Lb1
Cross Sectional Area of Belt (Ac):
15mm a
b 10mm
h 12mm
Fig 5: Bending moment diagram
Fig 3: Cross sectional area of belt
The dimension of a section of the belt is shown above. The trapezoidal cross-sectional area is thus calculated as
(2)
Angular Velocity () of Rotation:
(3)
Force due to grater Fg
Fg = Mg x g
Force due to cassava loaded Fm
Fm = Mm x g
The total force Fb due to grater and cassava loaded into the machine is
Fb = = 354.5 N
Bearing reactions on the shaft (R1 and R2)
Fc (375.81N) Fb (354.5 N)
0.1m 0.21m 0.21m
R1 R2
Figure 3.5: The schematic representation of forces acting on shaft.
From the evaluation of the forces, determination of the bearing reactions, maximum bending moments (Mmax) and others stress analysis of the shaft were performed using inventor professional software (educational license) and are shown in the figures below.
Fig 4: Shear force diagram
Fig 6: Deflection
Fig 7: Ideal diameter
Design calculation and specification of inlet Hopper:
Fig 8: CAD Model of the Inlet Hopper
Where V = volume of the hopper
A = Area of trapezium + Area of triangle b = breath of the hopper
Fig 9: Sheet metal flat pattern of the inlet hopper
Structural Base:
Structural base was designer for high stability and rigidity using 60 x 60 x 6 mm Angle iron
Pulley and Belt Drive:
The belt and pulley drive system will involve four pulleys (3 pulleys and 1 idler pulley) and 2 belts.
1
3
1
3
2
2
4
4
Figure 11: Pulleys connected by a belt.
The velocity ratio between two pulleys transmitting torque is given as (Avallone and Baumeister, 1997);
(5)
Where:
1 = angular velocity of the last driven pulley 4 = angular velocity of driver pulley
N4 = rpm of driver pulley
N1 = rpm of the last driven pulley D4 = diameter of driver pulley
D1 = diameter of driven pulley
= angle of lap between belt and pulley
-
Tensions on Belt (T1 and T2):-
-
For belt transmission between two pulleys, the following equations by Hall et al., 1961 are used
T1/T2 = eµ
Also
And Tc = mv²
3.11
3.12
(6)
Fig 10: CAD Model of the Structural Base
Rigidity of the frame
This is the measure of the resistance offered by an elastic body to deformation. It is calculated using the expression: (4)
Where K = Stiffness (Rigidity) (N\m)
F = Total force on the frame (N)
= maximum deflection on the frame (m)
Tc = T1/3 i.e. 3Tc = T1 3.13
Where T1 = tension on tight side of belt T2 = tension on slack side of belt Tc = centrifugal tension
1 = angular velocity of driver pulley
2 = angular velocity of driven pulley V = linear velocity of belt
The power transmitted with the belt is given as P= (T1 T2) v
In this equation the power (P) is in watts, when T1 and T2 are in Newton and belt velocity is in metre per second. When the tensions are in Newton and the velocity in metre per second,
the horse power (HP) transmitted is given in watts or kilo watts.
1HP = 0.746 kw
Belt Length (L):-
The belt length will be determined using trigonometric ratio, Pythagoras theorem and cosine rule.
Where:
L = length of belt
(7)
= centre distance between pulley 1 and pulley 2 (idler)
= centre distance between pulley 3 and pulley 2 (idler)
= centre distance between pulley 1 and pulley 4
= radius of pulley 1 = radius of pulley 2 (idler)
= radius of pulley 3 = radius of pulley 4
Fig 12: 3D CAD Model
Fig 13: 3D Explosive CAD Model DISCUSSION
Most mechanical systems have many standard components that makes up the machine. Hence, it becomes imperative to use Computer aided engineering software for the design and optimization of mechanical components. Autodesk Inventor professional which is equipped with component generators like Shafts, bearings, gears, belt and pulley. The use of such component generators aid in the proper designing of machines.
From the frame design, it was observed that the maximum load which can be loaded on the machine can have insignificant effect on the frame thereby making the machine to highly rigid and will minimum vibration effect.
S/N
Component
Symbol
unit
Value
1
Electric motor Pulley diameter
d
100
mm
2
Cross-sectional area of belt
A
0.00015
m
3
Mass of belt
Mb
0.16296
Kg
4
Motor Speed
N
1450
Rpm
5
Angular velocity
w
151.86
rad/sec
6
Centrifugal force
375.81
N
7
Force due to grater
Fg
104.5
N
8
Force due to cassava load
Fm
250N
N
9
Total force
Fb
354.5
N
10
Volume of hopper
V
74,220,960
mm3
11
Load overcome
F
1093
N
12
Targeted weight
W
74
kg
S/N
Component
Symbol
unit
Value
1
Electric motor Pulley diameter
d
100
mm
2
Cross-sectional area of belt
A
0.0015
m
3
Mass of belt
Mb
0.16296
Kg
4
Motor Speed
N
1450
Rpm
5
Angular velocity
w
151.86
rad/sec
6
Centrifugal force
375.81
N
7
Force due to grater
Fg
104.5
N
8
Force due to cassava load
Fm
250N
N
9
Total force
Fb
354.5
N
10
Volume of hopper
V
74,220,960
mm3
11
Load overcome
F
1093
N
12
Targeted weight
W
74
kg
Table 2: Technical specification of the machine
-
-
CONCLUSION
In this study, an improved Double barrel cassava grating machine has been designed. Materials used were carefully selected with reference to the best global health practice. With the careful utilization of Autodesk inventor professional CAD Software, and application of the basic engineering design principle, the machine was design to grate cassava in minimum time with high throughput and also experience minimum vibration when in operation. The design also ensured easy of assembling and disassembling thereby making easy to be used.
REFERENCES
-
Adetunji, O. R. & Quadri, A. H. (2011). Design and Fabrication of an Improved Cassava Grater. The Pacific Journal of Science and Technology. vol 12:2 pg 120 129
-
Adjekum, A. (2006). Cassava Processing and Marketing, Experiences From Ghana. Regional initiative workshop. Accra, Ghana.
-
Ajao, K. R., Ayilara, S. O. and Usman, I. O. (2013). Design and Fabrication of a Home-Scale Pedal-Powered Cassava Grater. International Journal of Engineering. Vol 3 pp 61 64.
-
FAO (2008) Food insecurity: when people live with hunger and fear starvation. The State of Insecurity in the World, Food and Agriculture Organization (FAO) of the United Nations, Rome
-
Food and Agricultural Organization, FAO. (2005). Cassava Development in Ghana. A Review of Cassava in Africa with Country Casa Studies in Nigeria, Ghana, The Republic Of Tanzania,
Uganda and Benin. pp357
-
Grubben, G., Klaver W. and Nono W. (2014). Vegetables to Combat the Hidden Hunger of Africa. Retrieved 28th April, 2015
-
Ndaliman M. B. (2006). Development of Cassava Grating Machine: A Dual-Operational Mode. Leonardo journal of sciences, 103-110.
-
Odigboh, E. U. (1984). A Manually Operated Cassava Grating Machine. Nigerian Journal of Technology VOL. 8, NO. 1. Pp15- 18
-
Okonkwo U. C., Onwukwe M., Oriaku E. C., Okafor C. E. (2016) Performance Evaluation and Optimization of Single Barrel Cassava Grating Machine on Selected Fresh and Stored Cassava Species. IOSR Journal of Mechanical and Civil Engineering. 13(4)VI:31-38.
-
Okonkwo U. C., Onokwai A. O., Okeke C. L., Osueke C. O. (2019). Investigation of the Effect of Temperature on the Rate of Drying Moisture and Cyanide Contents of Cassava Chips Using Oven Drying Process. International Journal of Mechanical Engineering and Technology (IJMET). 10(1) 1507-1520
-
Onokwai A. O., Okonkwo U. C., Okueke C. O., Ezugwu C. A., Eze
N. C. (2019). Quantifying Cassava Waste Generation and Biogas Production in Eha-Alumona Grinding Mills. International Journal of Civil Engineering and Technology 10(1) 2032 2043.
-
Oriaku, E. C., Ossai, E. N., & Agulanna, C. N. (2015). Design and performance evaluation of a double action cassava grating machine. Journal of Emerging Trends in Engineering and Applied Sciences, 6(3), 196-203.