
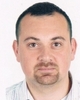
- Open Access
- Authors : Moez Youssef , Fethi Aloui , Chokri Boubahri , Seifallah Fetni
- Paper ID : IJERTV9IS070530
- Volume & Issue : Volume 09, Issue 07 (July 2020)
- Published (First Online): 27-07-2020
- ISSN (Online) : 2278-0181
- Publisher Name : IJERT
- License:
This work is licensed under a Creative Commons Attribution 4.0 International License
Design of DC-DC Converter Bench Controlled by an Arduino Microcontroller
Moez Youssef 1
1 Associate Professor,
Department of Electromechanical Engineering, Military Academy, Foundouk Jedid, Nabeul, Tunisia.
Chokri Boubahri 3
3 Assistant Professor,
Department of Electromechanical Engineering, Military Academy, Foundouk Jedid, Nabeul, Tunisia.
Fethi Aloui 2
2 Assistant Professor,
Department of Electromechanical Engineering, Military Academy, Foundouk Jedid, Nabeul, Tunisia.
Seifallah Fetni 4
4 Assistant,
Department of Electromechanical Engineering, Military Academy, Foundouk Jedid, Nabeul, Tunisia.
Abstract The main purpose of this paper is to design a DC- DC converter bench controlled by an Arduino board. This DC- DC converter bench is dedicated to the teaching of Power Electronics Labs. Several DC-DC converters topologies can be studied. Proteus simulations were carried out for the different structures.
KeywordsDC-DC converters; Arduino; Proteus simulations
-
INTRODUCTION
A power converter circuit manages the flow of electrical energy between a source and a load. Until a few years ago, their primary use was in supplying motors in industrial applications and in electric traction systems. Nowadays, in addition to those fields, they are employed in very wide range of applications including domestic applications, renewable energy systems, FACTS (Flexible Alternating Current Transmission System), automotive
Innovations in the field of power converters are taking place on several axes: new generation of power semiconductors, more and more new configurations of power converters, the use of digital devices such as microcontrollers, FPGA (Field Programmable Gate Arrays) in control circuits.
Modern power converters offer a high grade of precision, flexibility, communication capability, reliability to the end user, with smaller sizes.
This paper presents the design of DC-DC converter bench controlled by an Arduino card. Experiments and Proteus simulations are carried out for elementary structures of DC- DC converters such as buck, boost, buck-boost converters.
A block diagram of the experimental bench is shown in Fig.1. A DC power source, mostly battery is used to power the DC-DC converter. The pulse needed for switching the semiconductor is generated from the Arduino UNO. The code is written with the open-source Arduino Software (IDE). The measurement of the different currents and voltages can be done either by the Arduino card or by an oscilloscope.
DC Power Source
DC-DC
converter
Load
DC Power Source
DC-DC
converter
Load
Arduino controller
Arduino controller
Computer
Computer
Fig.1: Block diagram
-
CONTROL CIRCUIT The control circuit is shown in Fig.2.
Vcc
Vcc
Power MOSFET
Power MOSFET
R
R
R
T
vGS
5V
0
From PIN 7
of the arduino
R
T
vGS
5V
0
From PIN 7
of the arduino
vin
vin
Fig.2: Control circuit
R2(1)
R2(1)
The type and the values of the components used are as follows:
DUINO1
DUINO1
RESET
RESET
AREF
PB5/SCK 13
PB4/MISO 12
AREF
PB5/SCK 13
PB4/MISO 12
microcontrolandos.blogspot.com
microcontrolandos.blogspot.com
TABLE I. components of the control circuit
T: NPN transistor
2N2222
R: resistor
1k
Vcc: DC source
15V
R2
1k
T: NPN transistor
2N2222
R: resistor
1k
Vcc: DC source
15V
R2
1k
~PB3/MOSI/OC2A 11
~ PB2/SS/OC1B 10
~ PB1/OC1A 9
~PB3/MOSI/OC2A 11
~ PB2/SS/OC1B 10
~ PB1/OC1A 9
A
A
PB0/ICP1/CLKO 8
PD7/AIN1 7
PB0/ICP1/CLKO 8
PD7/AIN1 7
R1
1k
R1
1k
Q1
2N2222
Q1
2N2222
B
B
A0
A0
~PD6/AIN0 6
~PD6/AIN0 6
C
C
A1 PC0/ADC0
A1 PC0/ADC0
~ PD5/T1 5
~ PD5/T1 5
A2 PC1/ADC1
A2 PC1/ADC1
PD4/T0/XCK 4
PD4/T0/XCK 4
D
D
A3 PC2/ADC2
A3 PC2/ADC2
~ PD3/INT1 3
~ PD3/INT1 3
ANALOG IN
ANALOG IN
1121
ATMEGA328P-PU
1121
ATMEGA328P-PU
Vin is the voltage delivered by the PIN7 of the Arduino. Vin is a square-wave voltage, the low level is 0V and the high level is 5V. In order to have a square-wave voltage with a frequency f=1kHz and a duty cycle D=0.6, the following code must be written with the Arduino Software (IDE).
Fig.3: Arduino code
When Vin is at the low level (0V), the transistor T is OFF (open), then vGSVcc=15V (for R=1k , the voltage across the resistor R can be neglected).
When Vin is at the high level (5V), the transistor T is ON (saturated), then vGS0V.
Fig.4 shows a simulation of the control circuit on Proteus.
A4 PC3/ADC3
A5 PC4/ADC4/SDA PC5/ADC5/SCL
PD2/INT0 2
TX PD1/TXD 1
RX PD0/RXD 0
A4 PC3/ADC3
A5 PC4/ADC4/SDA PC5/ADC5/SCL
PD2/INT0 2
TX PD1/TXD 1
RX PD0/RXD 0
ARDUINO UNO R3
ARDUINO UNO R3
DIGITAL (~PWM)
DIGITAL (~PWM)
Fig.4: Proteus simulation of the control circuit
The result of the control circuit simulation is as follows.
Fig.5: control voltage simulation
After simulation, the complete control circuit has been tested, the following result is obtained:
Fig.6: control voltage measured
-
POWER CIRCUIT
Experiments are carried out for three DC-DC converters structures that are: Buck converter, Boost converter and Buck- Boost converter.
The type and the values of the components used are as follows:
TABLE II. Components of the power circuit
M: MOSFET
IRF540
D: Diode
BYY56
R: Resistor
25
L: Inductor
0.1H
C: Capacitor
54µF
VS: DC source
15V
A. Buck converter
The buck converter is shown in Fig.7. It operates by periodically opening and closing an electronic switch (MOSFET). It is called a buck converter because the output voltage is less than the input.
M
i
u(t) VS
u(t) VS
t
t
D.T
T
D.T+T
D.T
T
D.T+T
i(t)
i(t)
t
t
D.T
T
D.T+T
D.T
T
D.T+T
Fig.9: Theoretical waveforms of the buck converter
u(t) and i(t) are output (load) voltage and current. The average of the output voltage u(t) is given by:
VS D
u L
D is the duty cycle.
R B. Boost converter
= .
(1)
Fig.7: Buck converter
S
S
D
D
In practice, the following configuration (Fig.8) is preferred. Its main advantage is the common ground for both control and power circuits.
i
V
u/p>
L
i
V
u
L
R
R
M
M
Control
voltage
Control
voltage
Fig.8: Buck converter with common ground
Theoretical waveforms for buck converter are as follows:
The boost converter is shown in Fig.10. It is called a boost converter because the output voltage is larger than the input.
L
vL
D
L
vL
D
M
M
Control voltage
Control voltage
u
u
V
V
vM
vM
C R
C R
S
S
Fig.10: Boost converter
In theory, the capacitor C is considered so large that the output voltage u is held constant at = .
The analysis proceeds by examining the inductor voltage (vL) and the switch voltage (vM) for the switch closed and again for the switch open.
L
vL U
VS vM
Fig.11: Equivalent circuit for the switch closed
When the switch is closed:
(2)
(2)
=
{ = 0
L
vL
VS
vM
U
vL
D
C R
L
vL
VS
vM
U
vL
D
C R
M
M
VS
VS
L
L
u
u
Control voltage
Control voltage
Fig.12: Equivalent circuit for the switch open
When the switch is open:
=
{ = (3)
Theoretical waveforms for boost converter are as follows:
()
()
t
t
D.T
T
D.T+T
D.T
T
D.T+T
()
()
t
t
D.T
T
D.T+T
D.T
T
D.T+T
Fig.13: Theoretical waveforms of the boost converter
The average inductor voltage must be zero for periodic operation, then:
Fig.15: Buck-boost converter with common ground
In theory, the capacitor C is considered so large that the output voltage u is held constant at = .
L
L
C R
C R
The analysis proceeds by examining the inductor voltage (vL) for the switch closed and again for the switch open.
vL
VS
vL
VS
U
U
Fig.16: Equivalent circuit for the switch closed
When the switch is closed:
= (6)
Which gives:
. + (1 )( ) = 0 (4)
vL
C R
vL
C R
VS
VS
L
L
U
U
= (5)
1
Since 0 1, then
C. Buck-boost converter
L
L
L
L
C R
C R
The buck-boost converter is shown in Fig.14. The output voltage of the buck-boost converter can be either higher or lower than the input voltage.
M
v
D
VS
M
v
D
VS
u
u
Fig.14: Buck-boost converter
In practice, the following configuration (Fig.15) is preferred. Its main advantage is the common ground for both control and power circuits.
Fig.17: Equivalent circuit for the switch open
When the switch is open:
= (7)
Theoretical inductor voltage for buck-boost converter is as follows:
()
()
t
t
D.T
T
D.T+T
D.T
T
D.T+T
Fig.18: Theoretical inductor voltage for buck-boost converter
The average inductor voltage must be zero for periodic operation, then:
Which gives:
. + (1 ) × () = 0 (8)
= .
1
(9)
If 0.5 < , > : the output voltage is larger than the input.
If < 0.5 , < : the output voltage is smaller than the input.
-
SIMULATIONS AND RESULTS
In this section, Proteus simulations and real measurements are shown for the three configurations of DC-DC converters.
-
Buck converter
The complete buck converter circuit (control + power) is simulated using the Proteus software. Simulation is carried out for the practical values.
Fig.21: Measured load current and voltage for buck converter
-
Boost converter
The complete boost converter circuit (control + power) is simulated using the Proteus software. Simulation is carried out for the practical values.
A
A
B C
D
L1
100mH
D1
DIODE
B C
D
L1
100mH
D1
DIODE
R3
25
V1
15V
R3
25
V1
15V
DUINO1
DUINO1
R2(1)
DUINO1
R2(1)
R2
1k
R2
1k
AREF
PB5/SCK 13
PB4/MISO 12
AREF
PB5/SCK 13
PB4/MISO 12
Q2
NMOSFET
Q2
NMOSFET
RESET
RESET
microcontrolandos.blogspot.com
microcontrolandos.blogspot.com
RESET
~PB3/MOSI/OC2A 11
~ PB2/SS/OC1B 10
~ PB1/OC1A 9
~PB3/MOSI/OC2A 11
~ PB2/SS/OC1B 10
~ PB1/OC1A 9
A B C D
microcontrolandos.blogspot.com
microcontrolandos.blogspot.com
AREF
PB5/SCK 13
PB4/MISO 12
~PB3/MOSI/OC2A 11
~ PB2/SS/OC1B 10
~ PB1/OC1A 9
1121
ATMEGA328P-PU
1121
ATMEGA328P-PU
PB0/ICP1/CLKO 8
DIGITAL (~PWM)
DIGITAL (~PWM)
ANALOG IN
ANALOG IN
R1
R2(1)
R2
1k
Q1
C1
54uF
D1
DIODE
R3
25
Q2
NMOSFET
L1
100mH
V1
15V
PB0/ICP1/CLKO 8
PD7/AIN1 7
PB0/ICP1/CLKO 8
PD7/AIN1 7
R1
1k
R1
1k
Q1
2N2222
Q1
2N2222
DIGITAL (~PWM)
DIGITAL (~PWM)
1121
ATMEGA328P-PU
1121
ATMEGA328P-PU
PD7/AIN1 7
2N2222
ANALOG IN
ANALOG IN
A0 PC0/ADC0
A0
A0
~PD6/AIN0 6
~PD6/AIN0 6
A1 PC1/ADC1
A1 PC0/ADC0
A1 PC0/ADC0
~ PD5/T1 5
~ PD5/T1 5
A2 PC2/ADC2
A2 PC1/ADC1
A2 PC1/ADC1
PD4/T0/XCK 4
PD4/T0/XCK 4
A3 PC3/ADC3
A3 PC2/ADC2
A3 PC2/ADC2
~ PD3/INT1 3
~ PD3/INT1 3
A4 PC3/ADC3
A5 PC4/ADC4/SDA PC5/ADC5/SCL
A4 PC3/ADC3
A5 PC4/ADC4/SDA PC5/ADC5/SCL
PD2/INT0 2
TX PD1/TXD 1
RX PD0/RXD 0
PD2/INT0 2
TX PD1/TXD 1
RX PD0/RXD 0
A4 PC4/ADC4/SDA A5 PC5/ADC5/SCL
ARDUINO UNO R3
~PD6/AIN0 6 1k
~ PD5/T1 5
PD4/T0/XCK 4
~ PD3/INT1 3
PD2/INT0 2
TX PD1/TXD 1
RX PD0/RXD 0
ARDUINO UNO R3
ARDUINO UNO R3
Fig.19: Proteus simulation of the buck converter
Fig.20: Proteus waveforms
The yellow waveform represents the load current and the red waveform represents the load voltage.
Practical Measurements are in accordance with theory and simulation as shown in Fig.21.
Fig.22: Proteus simulation of the boost converter
Fig.23: Proteus waveforms of the boost converter
The yellow waveform represents the switch voltage and the red waveform represents the load voltage . Since the capacitor C has a finite value (C=54µF), the output voltage u is not constant (it has a ripple). Practical measurements confirm Proteus simulation as shown in Fig.24.
Fig.24: Measured load and switch voltages for boost converter
-
Buck boost converter
D
D
L1
100mH
L1
100mH
V1
15V
V1
15V
microcontrolandos.blogspot.com
microcontrolandos.blogspot.com
The complete buck-boost converter circuit (control + power) is simulated using the Proteus software. Simulation is carried out for the practical values
D1
<>D1
A
DIODE
A
DIODE
B
C
C1
54uF
R3
25
B
C
C1
54uF
R3
25
DUINO1
R2(1)
DUINO1
R2(1)
R2
1k
R2
1k
A4 PC3/ADC3
A5 PC4/ADC4/SDA PC5/ADC5/SCL
PD2/INT0 2
TX PD1/TXD 1
RX PD0/RXD 0
A4 PC3/ADC3
A5 PC4/ADC4/SDA PC5/ADC5/SCL
PD2/INT0 2
TX PD1/TXD 1
RX PD0/RXD 0
ARDUINO UNO R3
ARDUINO UNO R3
AREF
PB5/SCK 13
PB4/MISO 12
AREF
PB5/SCK 13
PB4/MISO 12
Q2
NMOSFET
Q2
NMOSFET
RESET
RESET
~PB3/MOSI/OC2A 11
~ PB2/SS/OC1B 10
~ PB1/OC1A 9
PB0/ICP1/CLKO 8
~PB3/MOSI/OC2A 11
~ PB2/SS/OC1B 10
~ PB1/OC1A 9
PB0/ICP1/CLKO 8
R1
R1
PD7/AIN1 7
PD7/AIN1 7
Q1
2N2222
Q1
2N2222
A0
A0
~PD6/AIN0 6 1k
~PD6/AIN0 6 1k
A1 PC0/ADC0
A1 PC0/ADC0
~ PD5/T1 5
~ PD5/T1 5
A2 PC1/ADC1
A2 PC1/ADC1
PD4/T0/XCK 4
PD4/T0/XCK 4
A3 PC2/ADC2
A3 PC2/ADC2
~ PD3/INT1 3
~ PD3/INT1 3
DIGITAL (~PWM)
DIGITAL (~PWM)
ANALOG IN
ANALOG IN
1121
ATMEGA328P-PU
1121
ATMEGA328P-PU
[1] R. Saravanamoorthi, P. Rathinavel, E. Sandhya and K.M. Manu, Arduino Based Pwm Output Voltage Control of a DC-DC Boost Converter, International Journal of Engineering Research &
Technology (IJERT), Vol. 6 Issue 03, March-2017, pp. 348-350.
[2] C. Buccella, C. Cecati and H. Latafat, Digital Control of Power ConvertersA Survey, IEEE Transactions on Industrial Informatics, VOL. 8, NO. 3, August 2012, pp. 437-447.
[3] S.A. Lopa, S. Hossain, M. K. Hasan and T. K. Chakraborty, Design and Simulation of DC-DC Converters, International Research Journal of Engineering and Technology (IRJET), Vol. 03 Issue 01, Jan-2016, pp. 63-70.
[4] T. Bouguettaya and N. Obeidi, Commande dun Moteur à Courant Continu Alimenté par un Hacheur avec la Carte Arduino, Department of electrical engineering, El-Oued University, Algeria. Submitted for the requirements for the Degree of Master in Electric Control, May- 2016.
[5] [Online]. Available: https://www.f-legrand.fr/scidoc/index.html. [6] M. H. Rashid and F. L. Luo, Power Electronics Handbook: Devices, Circuits and Applications, 2nd ed. New York: Elsevier Academic, 2006.
[1] R. Saravanamoorthi, P. Rathinavel, E. Sandhya and K.M. Manu, Arduino Based Pwm Output Voltage Control of a DC-DC Boost Converter, International Journal of Engineering Research &
Technology (IJERT), Vol. 6 Issue 03, March-2017, pp. 348-350.
[2] C. Buccella, C. Cecati and H. Latafat, Digital Control of Power ConvertersA Survey, IEEE Transactions on Industrial Informatics, VOL. 8, NO. 3, August 2012, pp. 437-447.
[3] S.A. Lopa, S. Hossain, M. K. Hasan and T. K. Chakraborty, Design and Simulation of DC-DC Converters, International Research Journal of Engineering and Technology (IRJET), Vol. 03 Issue 01, Jan-2016, pp. 63-70.
[4] T. Bouguettaya and N. Obeidi, Commande dun Moteur à Courant Continu Alimenté par un Hacheur avec la Carte Arduino, Department of electrical engineering, El-Oued University, Algeria. Submitted for the requirements for the Degree of Master in Electric Control, May- 2016.
[5] [Online]. Available: https://www.f-legrand.fr/scidoc/index.html. [6] M. H. Rashid and F. L. Luo, Power Electronics Handbook: Devices, Circuits and Applications, 2nd ed. New York: Elsevier Academic, 2006.
Fig.25: Proteus simulation of the buck-boost converter
Fig.26: Proteus waveforms of the buck-boost converter
The yellow waveform represents the inductor voltage and the red waveform represents the load voltage . Since the capacitor C has a finite value (C=54µF), the output voltage u is not constant (it has a ripple). Practical measurements confirm Proteus simulation as shown in Fig.27.
Fig.27: Measured load and inductor voltages for buck-boost converter
-
-
CONCLUSION
In this project, a DC-DC converter bench is designed. This experimental bench is a multi-topology bench. It allows students to study the elementary DC-DC converters that are buck, boost and buck-boost converters. For this DC-DC converter, the pulse needed for switching semiconductor device is generated using the Arduino Uno.
Before performing experimental measurements, simulations with the Proteus software are carried out. The simulations results obtained are in accordance with measurements.
This project highlights that Arduino offers a simple and efficient way to control power converters.
REFERENCES