
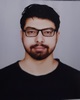
- Open Access
- Authors : Sunil D. Chougule , Kunal Kaul
- Paper ID : IJERTV10IS050440
- Volume & Issue : Volume 10, Issue 05 (May 2021)
- Published (First Online): 03-06-2021
- ISSN (Online) : 2278-0181
- Publisher Name : IJERT
- License:
This work is licensed under a Creative Commons Attribution 4.0 International License
Design of Electric Cycle (Complete Design and Analysis of 2 Electric Cyclce Models)
Kunal Kaul
Department of Mechanical Engineering, Vishwakarma Institute of Technology, Pune, India
Prof. Sunil D. Chougule Department of Mechanical Engineering, Vishwakarma Institute of Technology,
Pune, India
AbstractThe research paper revolves around the concept of Electric cycle and how to make it as cheap as possible adding only necessary electronics in the circuit .Our aim was to create a working prototype which can compete in the E-cycle market on efficiency as well as in price. Two E-cycle models are present in this research paper. One contains Lead Acid battery pack and other contains Li Ion battery pack. This is done to create a comparison between both packs and arrive at a conclusion.
KeywordsBattery Management System, Lead Acid, Li Ion, Parallel, Series,
-
INTRODUCTION
The research paper contains complete design and creation of two E-cycle models, one with Lead Acid battery pack and other with Li-Ion battery, for factory workers as well as lower middle class. To do that we need to physically test and conclude which type and arrangement is best for our cycle for our requirements. By the end of this paper, there would be conclusion regarding the type, arrangement and battery type of this electric cycle. [2][3]
-
NEED FOR SUCH ANAYSIS
The need for such analysis is very much evident once we look at our heavy dependence on fossil fuels and pollution that conventional vehicle causes. [2][3] This cycle contains a certain particular objective that is to be as cheap as possible as this cycles targeted customers are the daily wage and industry workers who cannot afford a twenty thousand worth electric cycle. This cycle being cheap will help them in travel and transport without using much for their time, energy and money. Our main focus is to make it appealing to these workers as well as lower middle class. To do that we need to physically test and conclude which type and arrangement is best for our cycle for our requirements. By the end of this paper, there would be conclusion regarding the type, arrangement and battery type of this electric cycle pack. The two models will have different arrangements and specifications. These specifications will be used to derive a conclusion for electric cycle solutions for daily wage workers and lower middle class people.
This comparison to conclude contains various parameters such as cost, design, aesthetics, efficiency, safety.
-
CYCLE COMPONENTS
-
DC MOTOR 24V 250W
-
LEAD ACID (26V 18Ah)
-
FREE WHEEL (18 teeth)
-
SPROCKET (9 teeth)
-
Switch
-
Complete circuit formation
-
BATTERY CHARGER 44V 4.2A constant charge
-
Li ION batteries(60 cells)
-
Li ION Battery Management System(2*3S)
-
Lead Acid Battery Charger 45V 5A constant charge
-
Wires for Connection
-
RX-TX connector
-
Battery Indicator(12V)
-
Li Ion Battery Management System(6S)
-
Cycle Chain
-
1.5×2.5 ft 3mm thick Steel sheet
-
1×1 ft 1mm thick Steel Sheet
-
Spray Paint
-
Soldering Iron
-
-
USING THE TEMPLATE
From above,
We can conclude that; Motor specification=250 W, 24V, Battery pack capacity=18-22Ah (for speed 20-22km/hr), Range Produced=40km.
If using a Li Ion battery pack, No of cells in series=6, No of parallel branches=10, total no of cells=60
Li ION configuration comes out to be 6S10P [1] [4] [5]
-
PROTOTYPE1
The prototype 1 contains Lead Acid battery pack. This battery pack is of good quality, contains 1 year waranty and has good life cycle. The battery pack contains 2 Lead acid batteries of 18Ah and 12 V connected in series to get a pack of 24V and 18Ah.[5][6]
Cost of Pack =4000/-
The prototype specifications: [5]
-
Range = 40km (verified by Google fit)
-
Max speed= 22km/hr
-
Battery charging time= 2hrs
-
Battery capacity = 18 Ah
-
Battery voltage= 25.5 V
-
Motor voltage= 24 V
-
Motor power= 250W
-
Sprocket reduction=1:2
The picture of the Prototype 1 is given below:
-
-
BATTERY MANAGEMENT SYSTEM
The Li-ion cells or battery pack of such cell require a battery management system while charging, discharging and normal operation. This BMS is very important part of a battery pack. It helps the battery pack to increase its life and also prevents overcharging and deep discharge. The overcharging is prevented by the BMS by absorbing the extra charge to a certain limit which is specified in its manual after which it gets shot and breaks the circuit. Even if the circuit remains after the BMS shorting, the sound and smoke of shorting act as signal to the user that overcharging is happening and charging need to be stopped. Deep discharge happens when the battery packs terminals get connected by some mistake. In such case also the BMS behaves similarly as it behaved in case of overcharging. It basically acts like a protective circuit. During normal operation, the BMS redistribute the voltage coming from each battery in such a way that the charge depletion happen equally in all cells and thus improving the life of the battery pack. [2][3]
For a 6S configuration, the BMS must be connected as follows:
-
LI-ION PACK DESIGN
As discussed before, the pack configuration of Li Ion is 6S10P, the below image gives us a clear description: [4] [5]
The specifications for prototype 2: [5]
-
Range = 20km (verified by Google fit)
-
Max speed= 20km/hr
-
Battery charging time= 2hrs
-
Battery capacity = 18 Ah
-
Battery voltage= 23.5 V
-
Motor voltage= 24 V
-
Motor power= 250W
-
Sprocket reduction=1:2
This drop in range is a result of quality of Li Ion battery pack and the heat it generates also causes some discomfort to the rider.
-
BLOCK DIAGRAM
-
-
-
PROTOTYPE 2
The second prototype contains the above battery pack and has different body design to accommodate ease and comfort of use as factors for selection. Due to small size of Li ion packs, they are easy to mount. The pack uses the Li ion cells from a local vendor, thus quality is big question. The cells from a good quality authorized vendor will make the pack out of budget and this prototype model will get rejected on the basis of cost. The Li ion cells are more efficient than Lead acid but of same quality level.
The following is a picture of the prototype:
Prototype 1:
Prototype 2:
-
COMPARISON BETWEEN PROTOTYPES
PROTOTYPE1
-
Better Range
-
Better Quality
-
Bigger Size
-
More Bulky
-
Body Design not appealing
-
Safer
-
Less efficient than similar quality Li Ion packs
-
Cheaper than similar quality Li Ion packs
Comments-The Prototype 1 body design needs to change and a better arrangement need to be figured out. This prototype fulfills all the required technical criteria. This prototype can be considered.
PROTOTYPE2
-
Range is not enough
-
Improving quality will increase range
-
Improving quality will increase cost, make it out of budget.
-
Portable
-
Less safebut addition of BMS improves its safety.
-
Body Design better
-
Less efficient, needs a better quality battery pack.
-
Bit complicated circuit.
Comments-The prototype 2 body design is better and more appealing. However, it fails to meet the technical requirements due to bad quality of Li Ion cells from a local vendor. We can meet the technical requirements by using a better quality Li Ion battery pack but that will increase the cost significantly out of budget. This prototype with current status cannot be considered. However, its body design can be used further.
-
-
FINAL CONCLUSION
As discussed and compared earlier, we conclude that prototype 1 must be considered for creation of a model. Current Li Ion pack is must less efficient than the Lead Acid pack due to quality difference but prototype 1 body design is not ideal.
Its body design needs to change for that we have considered, deriving a design from prototype 2 body:
The derived design layout looks like:
The Final Model Specification: [5]
-
Range = 40km (verified by Google fit)
-
Max speed= 22km/hr
-
Battery charging time= 2hrs
-
Battery capacity = 18 Ah
-
Battery voltage= 25.5 V
-
Motor voltage= 24 V
-
Motor power= 250W
-
Sprocket reduction=1:2
-
-
BATTERY BOX DESIGN
As we can observe that a new component is added in the desired final layout that is a Battery box, so we need to design a battery box according to the given specifications for the electric cycle.
The battery box mount has 3 important parts:
Part 1:
This part is long rectangular base welded to carrier from middle and its end hinged in downward direction.
This part will be free to move from end but welded from middle.
The hinged ends will contain two 4mm holes each. These holes need to be aligned well with each other.
Here is a diagram of how the part should look;
Part 2:
This part will be exact opposite to Part1. It will be a rectangular base welded to the base of battery box from middle and its end hinged in upward direction.
This part will be free to move from end but welded from middle.
The hinged ends will contain two 4mm holes matching part1.
The battery box will have 2 bolts on each sides with 4mm diameter welded to it.
The holes from part1 must match to these bolts such that the ends can be folded into these bolts.
Here is a diagram of how the part should look;
Final Part:
Finally, the third part is the assembly. The assembly of these parts will be relatively easier to understand and perform. Part1 is attached to the carrier and Part2 is attached to box both and the middle.
Both these parts have hinged, free to move ends, these ends have matching holes of 4 mm which also match to a 4 mm bolt.
Both the ends are kept at the middle position and are just bolted together using two 4mm bolts at each side. Since, the battery box is welded to middle of Part2 it also gets attached but using bolts.
This ensures that box is detachable.
When box is detached, the part1 ends go downwards and hence will not harm or create any problems for the rider
Part2 ends can be again folded into 4 mm bolts of battery box as seen in Part2 diagram.
Here is a diagram, depicting the final assembly:
-
FINAL CONCLUSION BASED ON COST
Cost is big factor in this research project. Our aim in this paper is to provide a cheaper solution for the 20,000 rupees e- cycle available in the market by removing or replacing some features of less importance but providing similar efficiency. The efficiency part has been achieved by our final model and this section shows how much the cost was reduced.
-
Material +Labour Cost(hourly basis)=1500/-
-
Motor Cost=2000/-
-
Battery Cost=2*2025=4050/+1year Warranty
-
Cost of Assembly= 300/-
-
Chain, Sprocket and Other Miscellaneous Cost=200/-
-
Cycle Cost=3000/- Total Cost= 11050/-
Total Cost with 10%GST= Rs.12155/-
Price Reduction percentage= (20000-12155)*100/20000 =
40%
We can observe that in the final model the price was reduced by 40% of the market price for similar performance parameters.
Hence, we can conclude that the final model satisfies our research purpose by all the standards; cost, technical as well as aesthetics.
-
-
ACKNOWLEDGMENT
-
We wish to express our gratitude to Prof. (Dr.) Rajesh M. Jalnekar, Director, Vishwakarma Institute of Technology , Pune for providing the facilities of the Institute and for his encouragement during the course of this pandemic period for this research paper.
-
We also want to express our deepest gratitude to Prof. (Dr.) Mangesh B. Chaudhari, Head of Mechanical Engineering Department, Vishwakarma Institute of Technology, Pune for his guidance and support.
-
-
REFERENCES
-
Zorn, W.: Bicycle speed and power calculator.
-
Tab Green Guru, Build Your Own Electric Cycle, eBook.
-
Jim Turner, The Electric Bike, Book
-
1St Edition by Krishnan, Pearson India, Electric Motor Drives:
Modelling, Analysis, And Control, Book
-
Edmount India Pvt. Ltd., Electric Car Design, Course
-
Udemy, Introduction to Hydrogen fuel based and Electric Vehicle, Course.