
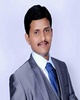
- Open Access
- Authors : N Shashikantha , Venkatesha Reddy , Dr. Sharanraj. V
- Paper ID : IJERTV11IS060080
- Volume & Issue : Volume 11, Issue 06 (June 2022)
- Published (First Online): 14-06-2022
- ISSN (Online) : 2278-0181
- Publisher Name : IJERT
- License:
This work is licensed under a Creative Commons Attribution 4.0 International License
Design of Pneumatic Drive Pick and Place Robot for Machining Steam Turbine Blades
N Shashikantha*1, Venkatesha Reddy2 Dr. Sharanraj.V3
*1Associate Professor, Dept of Mechanical Engg, Dr. Ambedkar Institute of Technology, Bangalore-56. 2Associate Professor, Dept of Mechanical Engg, Dr. Ambedkar Institute of Technology, Bangalore-56. 3Senior Grade Lecturer, Dept of Mechanical Engg. (W&SM), S.J. (Govt.) Polytechnic, Bangalore-01.
Abstract:- Robots are used today to do the jobs that are too dirty, dangerous or boring for humans, and to reduce human interventions in machining and other applications. This paper presents a design of pneumatic pick and place robot or pneumatic manipulator for handling variety of turbine blade profiles. After designing the robot completely, simulation was carried out. It was considered very hard to handle variety of turbine blade aero profiles at unloading end, with the help of specially designed robotic arm gripper unit, now it is easy to handle and perform variety of tasks. Pneumatic driven system is widely used in industrial automation, mainly for relatively simple tasks with open-loop control system. It is preferred when the Pay load is less, Precise Motion Control of Arm and end effectors without fluctuation, high repeatability and accuracy of picking and placing component, no leakage problems and maintenance cost is less. Pneumatic robots are traditionally used as air clamp to pick and place work parts on table because they can transfer a wide range of power at high response speed of the actuators, while limit switches, relay and PLC are used for accurate positioning control and acts as the basic requirements such as in process automation and robotics. These systems are driven by compressed air. Pneumatic-drive robots are usually small and have limited flexibility, but they are relatively inexpensive to build and use. The weight of the payload they can carry and the speed of their motion are limited by the compressibility and low operating pressure of air.
Key words Variety of blade profiles, pneumatic manipulator, pay load, flexibility.
INTRODUCTION
Pneumatic devices are traditionally used as air clamp to position worktable tools, because they can transfer a wild range of power at the high response speed of the actuators. While Program logic control systems are used in the areas where accurate positioning control are the basic requirements such as in process automation and robotics. There are two limitations in the use of pneumatic technology in these areas. The first one is the compressibility of the atmosphere, leading to difficulty of accurate positioning. The other is the few stop positions of the cylinder. The traditional pneumatic device can stop
Suitable only at the two ends of the cylinder requires that the cylinder stop at more than two positions, then the multi-position cylinder that must be used will increase the complexity of the whole mechanical and pneumatic system. The moving speed of the cylinder can be set by the throttle at configuration and cannot be regulated during operation. It is preferred when the Pay load is less, Precise Motion Control of Arm and end effectors without fluctuation, high repeatability and accuracy of picking and placing component, no leakage problems and maintenance cost is less [1].
The final user has to deliver all system information including system load, running speed of the cylinder, the damping of the system, the characteristics of friction of the cylinder, etc. to the manufacturer. The manufacturer then sets up the optimal parameters of state feedback control in the factory. Once the condition of system operation is changed, the optimal parameters of the state feedback control have to be re-adjusted in factory again. It is time-consuming and very uneconomical, restricts the application of Program logic control system.
Robots are being used increasingly in manufacturing applications for many reasons. In many situations, they have a number of advantages over employing humans or special purpose, hard or fixed automation. The important benefits from the use of robots are namely, robots can be built with performance capabilities superior to those of human beings in terms of strength, size, speed, accuracy and repeatability. Robots are better than humans to perform simple and repetitive tasks with better quality and consistency. Robots can replace humans in performing tasks that are difficult and hazardous because of factors such as size, weight, reach, precision or environment, dust, chemicals. Robots do not have the limitations and negative attributes of human workers, such as fatigue, need for rest, diversion of attention, absenteeism, need for refreshments etc. Robots can be used to perform tasks which human operators do not like to do jobs that are considered unskilled, demeaning, or low-paying or that involve poor working conditions.[3],[7].
Robots can reduce product cost, through reduction in usage of materials, through their efficiency and consistency. Robots become more economical as labour costs increase. Robots are flexible compared to hard automation since they can be reconfigured and reprogrammed. The output of the humans will depend upon the learning curve every time the job is changed. Thus robots can do jobs easier and faster to implement automation since they are more flexible. The flexibility is due to their reprogram ability. One can expect generally less down time with robots than complex hard automation in batch manufacturing operations. Although robots may have all these advantages, they are not always the best choice for all manufacturing applications. Even though they may have a wide range of capabilities, they still cannot match the unique combination of mental
skill and alertness and physical dexterity of a human operator. Robots, however, can supplement human operators to enhance their productivity [4].
PNEUMATIC DRIVE PICK AND PLACE ROBOT
The pneumatic drive picks and place robot has a Three Degrees of freedom (Fig.2). All Cylinders and sensors were manufactured by Festo Co., Germany. The major characteristics are: X, dia. of cylinder 25 mm, displacement 10 mm; Y, dia. of cylinder 40 mm, displacement 500 mm; Z, dia. of cylinder 25 mm, displacement 250 mm; Static positioning precision <0.05 mm; Dynamic positioning precision<0.5 mm.
Fig.2 Pneumatic drive pick and place robot with Three-degrees-of-freedom
The loading arm of robot will load the raw material and Unloading arm will unload the finished component. The raw material and finished turbine blade is shown in fig 3.
Fig.3 Raw material and Finished Turbine blade
The unloading arm is designed to handle variety of the turbine blade profile without any waiting time. The gripper is flexible to accommodate the variety of profiles.
Pneumatic driven system is widely used in industrial automation, mainly for relatively simple tasks with open-loop control system.
-
Pay load (Component mass) is less
-
Precise Motion Control of Arm and end effectors without fluctuation.
-
High repeatability and accuracy of picking and placing component.
-
No leakage problems
-
Operating and maintenance cost is less
DESIGN OF PICK AND PLACE ROBOT
Design of pick and place robot consists of four major units like
-
Design of Loading arm unit
-
Design of Unloading arm unit
-
Design of Indexing unit and
-
Design of Sliding unit.
-
1. Design of Loading Arm unit:
Fig.4 Loading arm unit with spring actuated parallel gripper
The loading arm unit is designed for a working air pressure at 5 bar and it is flexible to accommodate variety sizes of raw material, sizes varying from 19mm to 40 mm as shown in fig 4. Maximum weight of component is 0.5 kg. Gripping force required for holding the component is 62.5 N. Helical spring with ground and flat edge is used for actuating the gripper. Cylinder of diameter 25 mm and 10 mm stroke will actuate the cam and thus actuate the spring loaded gripper. The two parallel jaws are hinged, so that they provide flexibility during manufacturing. The arm is designed with a factor of safety 1.85.
1. 1.Downward force of component [FD] : 2.
FD = Mass * Acceleration FD = 0.5 * 9.81
FD = 5 N
-
2.Gripping force required to hold the component [FG]: 4.
From CMTI hand data book [2]
Coefficient of friction for steel µ (0.08 to 0.1) FG = FD / µ
FG = 5.0 / 0.08
FG = 62.5 N
The gripping force should be greater than 62.5 N for safer design 3. Cylinder force required for Gripping Component [F]:
Diameter of Gripping cylinder [D] = 25 mm Stroke length of cylinder [L] = 10mm Working pressure = 5 bar
Pressure = Force / Area Area = * D2 / 4
= * (.25)2 / 4
Area = 0.000491 m2
Force [F] = 5*105*0.000491
Force [F] = 245.43 N
Total cylinder force required is 245.43N.Since there are 4 grippers for loading arm, So, each cylinder force = F/4 = 61.36N.
-
Force due to wedge action [Fw]:
Fw / 10 = 61.36 / 3.12 Fw = 61.36*10/3.12 Fw = 196.66 N
-
Spring stiffness Force [Fs]:
Spring stiffness force should be lesser than 196.66 N Helical Spring index [C] = 6
No of active coils = 16
Outer diameter of helical spring = 20 mm Inner diameter of helical spring = 16 mm Length of spring = 50 mm
No of extra coils [ground and flat] = 2 Factor safety = 0.9
Fs = FW * 0.9
Fs = 196.66 * 0.9
Fs = 176.994 N
5. Force due to lever action [FL]:
FL * 39 = 176.994 * 25.5
FL = 176.994 * 25.5 / 39
FL = 115.72
Factor of safety = FL / FG FOS = 115.72 / 62.5
FOS = 1.85
Hence FOS is 1.85, design is safe.
2. Design of Unloading Arm unit:
Fig.5 Unloading arm unit with spring actuated V-Block gripper
The Unloading arm unit was considered very hard to handle variety of turbine blade aero profiles. With the help of specially designed robotic arm gripper unit, now it is easy to handle and perform variety of tasks. Which is designed work at an air pressure of 5 bar and is flexible to accommodate variety turbine blade aero profiles, as shown in fig 5. Maximum weight of component is 0.5 kg. Gripping force required for holding the component is 62.5 N. Helical spring with ground and flat edge is used for actuating the gripper. Cylinder of diameter 25 mm and 10 mm stroke will actuate the cam and thus actuate the spring loaded gripper. The V block are used for accommodating variety of turbine blade profiles and thus provides flexibility during manufacturing. The arm is designed with a factor of safety 2.82.
-
Spring stiffness Force [Fs]:
Spring stiffness force should be lesser than 196.66 N Helical Spring index [C] = 6
No of active coils = 16
Outer diameter of helical spring = 20 mm Inner diameter of helical spring = 16 mm Length of spring = 50 mm
No of extra coils [ground and flat] = 2 Factor safety = 0.9
Fs = FW * 0.9
Fs = 196.66 * 0.9
Fs = 176.994 N
-
Factor of safety [FOS]:
Factor of safety = Fs / FG FOS = 176.66 / 62.5
FOS = 2.82
Hence FOS is 2.82, design is safe [2].
3. Design of Indexing Unit:
Indexing unit is designed to rotate the arm unit 90º in CW and CCW respectively. Angle of rotation = 90º
Frequency of rotation [F] = 90º for 2 sec = 1/8 Time taken for rotation [t] = 8 sec
Radius of rotation [r] = 0.61 m
Mass of the gripper arm [m] = 40 Kg
Assuming it as a cantilever beam carrying a point mass 40 kg.
-
Tangential Velocity [V]:
Assuming it as an cantilever beam carrying a point load of 40 N V = 2**F*r
V = 2**(1/8)*(0.61)
V = 0.479 m/sec
-
Angular Velocity []:
= 2**F
= 2**(1/8)
= 0.785 rad/sec
-
Kinetic Energy Required [K.E]:
K.E = ½*m*v2
K.E = ½ *40*0.479
K.E = 4.58 kg – m
K.E=45.8 N-m [Minimum]
-
Cylinder force required for Gripping Component [F]:
Diameter of indexing cylinder [D] = 40 mm Stroke length of cylinder [L] = 250 mm Working pressure = 5 bar
Radius of rotation [r] = 0.0161m Pressure = Force / Area
Area = * D2 / 4
= * (.040)2 / 4
Area = 0.001257 m2
Force [F] = 5*105*0.001257
Force [F] = 628.50 N
-
Rotational Matrix in z axis [Rz]:
Angle of rotation = 90º
4. 6. Torque required for Indexing the arm unit [T]: 5.
T = F * r
T = 628.50 * 0.161
T = 106.10 N-m [Actual]
6. 7. Factor of safety [FOS]: 7.
Factor of safety = T / K.E FOS = 106.10 / 45.8
FOS = 2.31
Hence FOS is 2.31, design is safe [2].
4. Design of Sliding Unit:
-
Cylinder force required for sliding the unit [F]:
Diameter of indexing cylinder [D] = 40 mm Stroke length of cylinder [L] = 500 mm
Working pressure = 5 bar Pressure = Force / Area Area = * D2 / 4
= * (.040)2 / 4
Area = 0.001257 m2
Force [F] = 5*105*0.001257
Force [F] = 628.50 N
-
Sliding force required [Fs]:
FL *0.25 = 40 *10* 1.10
FL = 40 * 1.10 / 0.25
FL = 1760.0 N
From CMTI hand data book [2]
Coefficient of sliding friction for steel µ (0.1 to 0.15) FL = 1760.0 * 0.15
FL = 264 N
Factor of safety = F / FL FOS = 628.50 / 264
FOS = 2.38
Hence FOS is 2.38, design is safe [2].
CONCLUSION
This paper presents the complete design of pneumatic drive pick and place robot. Where Robotic grippers is flexible to accommodate varieties of turbine blades while manufacturing, reduce the manufacturing lead time and increase productivity there by reducing product cost.
REFERENCES
[1] Yang Yuan-Zhao, Study of Web-based integration of pneumatic manipulator and its vision positioning (September 2004). [2] CMTI Machine Tool Design Hand data book, Tata McGraw hill (2006). [3] M.P.Groover, Industrial Robotics Text book, (Volume 1, November 1980). [4] R.E. Compton, Robotic Material Handling Applications in a Flexible Manufacturing System, (June 2002). [5] M.P.Groover, Automation, Production Systems and Computer Integrated Manufacturing, Pearson education, (Third Edition, 2008) [6] L.J. George, Role of Robots in the Factory of the Future, (October 1999) [7] M.L.Fitzgerald, A low level control interface for robot manipulators, (June 2005).