
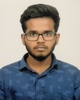
- Open Access
- Authors : E. Shiva Shanker Kumar
- Paper ID : IJERTV11IS010073
- Volume & Issue : Volume 11, Issue 01 (January 2022)
- Published (First Online): 22-01-2022
- ISSN (Online) : 2278-0181
- Publisher Name : IJERT
- License:
This work is licensed under a Creative Commons Attribution 4.0 International License
Design of Single Speed FR-Reduction Bevel Gear Box
(For Low Speed Vehicles)
E. Shiva Shanker Kumar
Automobile Engineering Department
Maturi Venkata Subba Rao (MVSR) Engineering College Hyderabad, Telangana(S), India.
AbstractGear boxes are designed for variable speeds and torque applications for different drives. Differential is an important component which splits the drive during turns and variable loads conditions. Differential is an expensive component which adds to the cost of the vehicle. In low-speed vehicles used for sprinkler vehicles, grass cutters etc.., introducing a differential will increase the cost and complexity of the vehicle. Finding an alternate for replacement of differential which serves the same purpose at low speeds will be of great advantage in reducing the cost, complexity, construction and maintenance. Hence this paper is aimed at making an attempt to find a similar type of alternate mechanism replacing differential with gear box.
KeywordsFR (Forward & Reverse) Reduction Gear Box, Bevel Gears, Low speed Vehicles, Single Speed.
-
INTRODUCTION
Design of reduction gear train for low-speed applications is very essential to overcome the effects of sudden and variable torque. This concept of reduction gear train is considered to replace the differential with reduction gear box with a provision of reverse drive. In low-speed vehicles used for sprinkler vehicles, grass cutters etc.
.
The gear train is designed for an output torque of 57.6 N-m at a gear reduction ratio of 1:3.6 Taking in to account the design considerations for gears and gear trains, the proposed train has been designed.
Applications of this proposed gear box are
-
Agricultural applications for weed cutting machinery
-
Lawn moving vehicles
-
Grass cutters
-
Flour mills
-
Paper mills
-
Lathe machines
-
Milling machines
-
Conveyer belts
-
-
LITERATURE REVIEW
Concept of gear development, classification of gears [3], [4], [5], gear nomenclature, gear materials applications of gears
[1] [5], design and development of gear trains [2] [6] are the concepts derived from standard references [1] [2]-
RECOGNITION OF NEED
Low speed vehicles generally dont need differential and hydrostatic gear box which adds to the complexity of vehicle and increase of cost factor. An alternative to replacement of these is of great advantage which reduces the complexity and cost factor has led this work.
-
INPUT PARAMETERS
S. No
Functional Design Parameters
Value
1
Vehicle gross weight
220 Kg
2
Max. Speed
45 kmph
3
Max. Power
10 HP
4
Max. Torque
16 N-m
5
RPM
3400
6
Acceleration
2.5 m/s2
Table 2.1 Functional Design Parameters
-
SELECTION OF MATERIAL AND BOM
S. No
Name of the component
Material
Quantity
1
Bevel gears
316 alloy steel
03
2
Shafts
EN19
02
3
Gear box casing
Al alloy
01
4
Ball bearing
6305 2RS
03
Table 3.1 BOM
-
DESIGN OF DRIVE AND GEAR ELEMENTS
4.1 Design of drive
-
Required force to overcome inertia
F = ma + Fr + Fs + Fd Fr = Crr*N, Fr = 15N
Fp = ma = 220*2.5 = 550N.
Total force F = 550 + 20 = 570N. We know that
Power = Force * Velocity
F = Power/Velocity = 74475/12.5 F = 596.56 N engine force.
{Engine force > required force}
Gear ratio
Engine RPM = 3400rpm Wheel RPM= 940 rpm
Gear ratio = engine rpm / wheel rpm = 3400/940 = 3.6:1 @ 45kmph
-
Design of shaft
D = Diameter of shaft
Torque transmitted by driven puts T = P*60/2N2, 62.8*103 N-mm
Also
Te = /16**D3
767.28*103 = /16*320 N/mm2*D3
D = 23mm shaft
-
Selection of bearing T = 70 N-m. Tangential force
WT = T/RM
RM = [70-34/2] sin60 RM = 45.89
-
Axil force and radial force
RA = WR sinp1 = WT tan . sin RR = WR cosp1 = WT tan . Cos WT = T/RM
WT = 70/50 N-m = 70*103/50 N-mm = 1400N
RA = 1400*tan60*sin60 = 1790 N RR = 1400*tan30*cos30 = 682.23 N WR = 682.23 N, WA = 1790 N
Life = 20,000 hours
Life in revolutions
L = 60*N*LH = 60*1300*15000
6
Figure 4.1 Dimensions
Vi) Design of gear.
Dp = 63mm Dg = 220mm Np = 8
Ng = 30
m = 7.75
Pitch angles of gears
p1 = tan-1 ( Ng / Np ) = 150 p2 = 300.
-
-
RESULTS
FOLLOWING ARE THE RESULTS OBTAINED GEAR TERMINOLOGY VALUES
= 1170*10
Basic dynamic radial load W = X.V.WR + X.WA
X = WA/WR>er = WA/C0 Then X = 0.56, Y =1.2
X = 0.56, Y = 1.2
rev
S.No
Nomenclatures
Values
1
Pitch
24.3 mm
2
Addendum
7.75 mm
3
Dedendum
9.3 mm
4
Module
7.75
5
Clearance
1.15 mm
6
Working depth
15.5 mm
7
Thickness
12.17 mm
8
p1
150
9
p2
300
S.No
Nomenclatures
Values
1
Pitch
24.3 mm
2
Addendum
7.75 mm
3
Dedendum
9.3 mm
4
Module
7.75
5
Clearance
1.15 mm
6
Working depth
15.5 mm
7
Thickness
12.17 mm
8
p1
150
9
p2
300
Table 5.1 Gear nomenclatures values
-
WORKING
This gear box is compatible in working with IC-engine and
W = 0.56*1*682.23 + 1.2*1790
= 0.56*1*682.23 + 21348
= 382.0488 + 2148
W=2530.488N
-
Basic dynamic load ratios
C = W[L/106]1/K = 2530.5[1170*106/106]1/3 C = 26.664 N
C = 26.6 KN
For C = 26KN C0 = 17.6KN
d = 25mm, D = 62, b = 17mm. C = 26; C0 = 13.4
Bearing No = 6305 ETN9 Or) = 6305-2z less
Or) = 6305 2RSI
electric drive with automatic clutch.
Power from the source is transmitted to pinion as input. From pinion the power takes a right-anled turn to the gears-1 and gear-2 which will be in mesh with the pinion. These gears transmit the proportionate amount of power to the road wheels.
The gear-1, and gear-2 are mounted on the shaft and can slide over the shaft manual.
Meshing of pinion with gear-1 facilitated forward drive and meshing of pinion with gear-2 facilitates reverse drive.
Figure 5.1 Cut section of assemblage of gear train in casing
Figure 6.1 Forward drive mesh
Figure 6.2 Reverse drive mesh
-
-
MODELING TOOL USED:
Solid works modeling tool of release 2021 is used. Basic features are,
-
Extruded Boss Feature.
-
Fillet Features.
-
Revolved Boss Feature.
-
-
CONCLUSION
The proposed reduction gear box for low-speed vehicles has been designed satisfactorily as per the requirement to suite for the real time working environment.
Design parameters with calculated valued are identified using the standard relations which helped in manufacturing of the components of the gear box.
-
REFERENCES
-
Budynas-Nisbett Shigleys Mechanical Engineering Design,
Eighth Edition, 2008; Pg. 746-47
-
Gitin M. Maitra: Handbook of gear design, 1994 Stephen, P. Radzevich; Dudleys Handbook of Practical Gear Design and Manufacture, Second Edition, 2012.
-
Kapelevich, A. and McNamara, T., Direct Gear Design for Automotive Applications, 2013
-
Milosav Ognjanovicl Miroslav Milutinovic2, Design for Reliability Based Methodology For Automotive Gearbox Load Capacity Identification, 2012
-
R.S. Kurmi, Theory of Machines, 14th Revised Edition, 2004.
-
R.S. Kurmi, J.K.Gupta Machine Design, Eurasia Publication House, 2005