
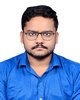
- Open Access
- Authors : Rudranath Saha , Dr. Biman Mukherjee
- Paper ID : IJERTV11IS070222
- Volume & Issue : Volume 11, Issue 07 (July 2022)
- Published (First Online): 15-08-2022
- ISSN (Online) : 2278-0181
- Publisher Name : IJERT
- License:
This work is licensed under a Creative Commons Attribution 4.0 International License
Determine the Settlement of Building Due to Tunnel Construction
Rudranath Saha
Civil Engineering Narula Institute of Technology
Kolkata, India
Dr. Biman Mukherjee
Civil Engineering Narula Institute of Technology
Kolkata, India
AbstractTo achieve the goal of sustainable development, competition for surface space is intensifying every day, and the use of underground space is extremely important. Difficult and uneconomical underground structures were limited to special structures such as tunnels, hydropower plants, railroad platforms defences, and mining. However, nowadays, public buildings in some big cities are also being built underground for many reasons, the most common reason being the effective use of land and space. The construction of underground skyscrapers is equipped with pile foundations. However, in the future, this pile foundation will be very deep and could be affected by newly constructed tunnels passing nearby. This project primarily deals with the analysis of pile foundations of buildings under the influence of tunnels using PLAXIS 2D finite element analysis software. For analytical purposes, a fully developed model was created and simulated for various positions and diameters of the tunnel associated with the foundation of the building. Analysed the results and found changes in pile behaviour related to total displacement. A thorough analysis of the simulation results showed that the pile foundations of the building were affected by the tunnel only when the tunnel was close to the pile and negligible when it was far from the structure. The distribution of the internal force induced by the tunnel depends on the position of the pile concerning the horizontal axis of the tunnel. An important location in the tunnel corresponds to a pole with spikes just below the tunnel. If the tunnel depth is different, the change in total displacement due to the pile depth depends on the position of the tunnel and the top of the pile. The diameter of the tunnel also has a slight effect on the displacement of the pile. The displacement of the pile is also slightly affected by the diameter of the tunnel.
KeywordsClay, Complex Variable, Finite Elements, Model Test Ground Toss, The Settlement, Tunnel Construction.
-
OBJECTIVE OF RESEARCH WORK This study's primary goal is to-
-
To find settlement at the foundation level through FEM to find out the differential settlement of the building
-
Assess foundation settlement as a result of Tunneling.
-
Research the consequences of many factors that will be taken into consideration, such as the type of soil types (clay and sand), tunnel depth, and diameter that influence foundation settlement.
-
Settlement calculations will be made using mathematical formulas and the Code for the PLAXIS finite element due to tunneling in an urban region, providing direct formula. Where investigations of various loads and soil types were conducted.
-
-
INTRODUCTION
Along with a few modifications and changes to reflect, as far as possible, the feedback from ITA Member Nation representatives and discussions held within the Research Working Group. Our natural domain has been the ground's surface for hundreds of years. We have always sought to leave this place by utilizing the remaining dimension, whether it is above or downwards, driven by necessity and curiosity. We have always faced significant obstacles in these battles, especially when moving downward. Only the underground can offer us a location for the infrastructure or activities required in densely populated metro areas. Underground construction projects have historically been highly challenging. The recent century's fast economic progress, however, spurred us to delve further and more into the ground. Against open areas in recent years. In truth, this paucity of space above the surface affects practically all cities around the globe, not only big cities. We are forced to use the underground area more strategically and thoughtfully to take advantage of the locational advantage. ii. Isolation-related factors benefit greatly from the soil's complete opacity, virtually endless spacing, and advantages in terms of isolation. It can offer defence against severe weather, earthquakes, and other natural calamities. iii. Protection of the environment According to recent research, there are different underground building scenarios. The annual energy demand is below 10 kWh/m2, so we can almost consider such buildings as zero energy buildings. This is a crucial element in creating buildings that have less influence on the environment. The ground can also give us a range of benefits for protecting the environment, such as aesthetics or ecology. iv. Geographical factors for both highways and railroads, tunnels have been dug through mountains primarily in undulating terrain. In mountainous and densely populated locations, the use of tunnels promotes or makes possible several transportation choices, including roads, trains, canals, etc.
-
LITERATURE REVIEW
Even though FEM analysis programs PLAXIS 2D/2D, GEO5, and FLAC 2D are still relatively new in the field of geotechnical engineering, a substantial study has lately been done on tunnel-structure interaction, deep excavation defence, and underground structures. Here, a few of them are mentioned along with their research.
Mroueh H. and Shahrour I. (2002) examined the effects of urban tunnel development on nearby pile foundations. Elastoplastic three-dimensional finite element modeling is used to complete it. The application of the pile axial loading and the construction of the tunnel with pile foundations were
the subjects of two separate rounds of numerical simulations. Both individual heaps and groups of piles underwent analysis. According to the outcomes of numerical simulations, tunneling causes large internal forces to be generated in nearby piles. Analysis of the relationship between tunneling and a group of piles demonstrates a favourable group effect with a significant decrease in the internal forces in the rear piles.
Timo Schweckendiek (2007) investigated structural reliability analysis of deep excavations using the "Pro Box" general probabilistic toolbox for PLAXIS, which automates reliability analysis based on PLAXIS output. The influence coefficients that emerged from the investigation offer helpful data for both optimization and the physical comprehension of the behavior of the model close to failure.
Zhandos Y. Orazalin and Andrew J. Whittle (April 2014) carried out a finite element analysis of a complex excavation. The project involved a complex sequence of berms, access ramps, and phased construction of the concrete mat foundation. The non-uniform soil excavation resulted in the three-dimensional effects which were well-captured by the 2D model predictions. The analysis results show a good agreement with the measured data and provide keys to explain many features of the observed performance including the differences in diaphragm wall deformations associated with sections supported by tieback anchors. A general pattern of measured movements in the center the of wall typically corresponds to an initial cantilever movement of approximately 10-20 mm during the excavation to the first tieback support level.
Pornkasem Jongpradist ET all. (October 2012) performed numerical simulations of geotechnical works in Bangkok subsoil using advanced soil models available in PLAXIS. Three constitutive models with enhancing levels of complexity are used to simulate three types of geotechnical works(embankment construction, deep excavation, and tunneling) in subsoil conditions. All problems which are from well-documented case histories having reliable monitored data are analyzed AXIS 2D assuming plane strain condition with the appropriate analysis condition.
Movement of the ground results from tunnel excavation in soft ground. This movement may alter the surface in an urban area. While using a semi-empirical approach, deal with ground shifting as a result of tunneling beneath the Greenfield area (i.e. there are no structures. The settlement of structures as a result of tunneling cannot be predicted using these empirical methods.
The surface settlements brought on by the excavation of a shallow tunnel at a Greenfield site were the subject of numerous study studies. Greenfield settlement profiles can be predicted with great accuracy in rural areas. However, surface settlements that grow in metropolitan areas less are known about the locations where tunnels pass underneath structures. Field evaluations of There are buildings exposed to tunnel- induced settlements.
2012's Lee van Kessel and 2013 Mohammad Ghafoori Surface settlement profiles are revealed by field measurements to be a settlement on the Greenfield site is distinct. When creating a tunnel in an urban setting surface to prevent any
damage to the surface structure, settlement caused by digging must be anticipated. Construction.
Volume loss results from the difference between the volume the of lined tunnel that will be built in its place and the volume of dirt that had to be in told the tunnel. Depending on the tunneling method of excavation and the type of soil, the movement of earth surrounding the tunnel can compensate for this volume loss (Potts and Zdravkovic, 2001)
The empirical methodology relies on historical field findings, and settlement depends on a variety of construction techniques craftsmanship valid in cases where buildings are present above the tunnel in metropolitan areas
Analytical techniques can be used to predict settlements in an efficient and timely manner. Poulos and Davies (1980) provide a variety of analytical solutions where settlement prediction is caused by a point load in elastic half-space. By integrating the solution for a line load equal to the amount of material excavated, settlement is assessed. This method disregards volume loss.
Volume loss was taken into account by Chow's (1994) technique, which is based on compressible irrational fluid. Chow calculates the answer to the vertical settlement problem as,
Y is the transverse distance from the tunnel axis where S is the vertical settlement, D is the tunnel diameter, is the soil density, G is the shear modulus, and zo depth.
In a coin comparison between the analytical methods with Gaussian profile and field measurements from the Caracas Metro and M-40 Motorway in Madrid (Oteo and Sagaseta, 1996) for settlement predictions it is noted that analytical methods produce a wider settlement more than the Gaussian profile and case study data with the similar maximum settlement.
In their development of the Sagaseta approach, Celma and Izquierdo (1999) included the parameters that, respectively, took into account ground loss of circular tunnels and introduced an equation for settlement for an is tunnel radius
Pinto and Whittle (2011) additionally show soil plasticity (near the tunnel) affects the outcomes and created closed-form solutions for uniform convergence of a 3-D tunnel heading. Severalizeralizese studies, Pinto et al. (2011) contrasted 3-D tunnel analysis. For analytical methods that forecast settling without a field test for early designs under Greenfield conditions, a minimal number of input parameters are typically required. However, in urban locations, analytical methods that do not take building weight into account are inappropriate; instead, they must take building loads into account.
For engineering practices of numerical methods to determine settlements brought on by tunneling is increasingly crucial. Tunneling problems are calculated using finite element techniques.
Software is frequently used for studies of plane strain. The goals of tunnel settlement prediction were developed, and tools like PLAXIS, OXFEM, FLAC, ABAQUS, etc., were employed successfully. Finite elements are used for There are a variety of variables to take into account in modeling. It's been discovered that It is inappropriate to regard soil as a linear elastic material when displacements occurolleagues (1983), Rankin (1988), and Chow (1994). Models made of fully elastic linear plastic are created by Rowe et al. (1983), who discovered that they provide substantially more real surface information. Then elastic model settlements. Additionally, Chow (1994) points out that using linear elastic Results are improved by using a model where stiffness grows linearly with depth.
Gunn (1993) also utilized and combined Tresca yield criteria with nonlinear elasticity at modest strains to estimate ground loss values with larger troughs than the Gaussian contour.
In properties, numerical methods are utilized to generate utilize dimensions with an acceptable level of accuracy.
When it comes to the development of computer numerical methods, the finite element method (FEM) developed that address used these challenging issues. FEM can address issues such as complicated nonas linear stress-strain applications, starting in the middle 1 of 960's Arg1960sas well as Clough and Penzien (1993). FEM was first used to solve the problem of then the solution for the plane problems the development of computer numerical methods, the finite element method (FEM) developed that addressed these challenging issues. FEM can address issues such as border conditions ns that are complex and exhibit strain behaviour. Behaviour middle of the 1950s with the debut of the first piece by 1960 thes Argyri 1960s Clough and Penzien (1993).
-
METHODOLOGY
-
In the Model tab sheet keep the default options for Model (Plane strain), and Elements (15- node).
-
Set the model Contour to xmin = 0 m, xmax = 40 m, ymin = -40 m and ymax = 5 m.
-
Keep the default values for units and constants and press OK to close the Project properties window.
B. Define the soil stratigraphy
The soil profile indicates four distinct layers: The upper consists of soft clay-type soil with stiffness that increases approximately linearly with depth. Under the clay layer, there is a thick fine sand layer. This layer is used as a foundation layer for old piles on which traditional brickwork houses were built. The pile foundation of such a building is model to the tunnel. Displacements of these piles may cause damage to the building, which is highly undesirable. Below the sand layer, there is a deep clay layer and bellow layer there are deep sand layer .Also bill on the layer there are deep clay layer.
To define the soil stratigraphy:
-
Geometry
The tunnel considered in this has a diameter of 5 m and is located at an average depth of 17 m. The geometry of the tunneling
-
Create new project to create new project, follow these steps:
-
Start the Input program and select start a new project from the Quick start
-
In the Project tab sheet of the Project properties window, enter an appropriate title.
-
Click the Create borehole button and create a borehole at x = 0. The Modify soil layers window pops up.
The soil stratigraphy in the Modify soil layers window
-
Create the soil stratigraphy as shown.
-
Keep the Head in the borehole to 0 m. Create and assign material data sets
-
-
Four data sets need to be created for the clay and sand layers.
For the upper clay layer the stiffness and shear strength increase with depth. Therefore values for E'inc and su, Inc are entered in the advanced subtree. The values of E'ref and su, ref become the reerence values at the reference level yref. Below yref the actual values of E' and su increase with depth according to:
E (y) = Eref + Einc (yref y) su(y) = su, ref +su, Inc (yref y)
The data sets of the two lower soil layers include appropriate parameters for the tunnel interfaces. In the other data sets tunneling grace properties just remain at their default values. Enter four data sets with the properties and Material
Tangent stiffness for primary oedometer loading
Eoedref
25 · 103
42 · 103
kN/m2
Unloading / reloading stiffness
Eurref
75 · 103
126 · 103
kN/m2
Poisson's ratio
ur
0.2
0.2
–
Power for stress level dependency of stiffness
m
0.5
0.5
–
Shear modulus at very small strains
G0ref
80· 103
110 · 103
kN/m2
Shear strain at which Gs = 0.722 G0
0.7
0.2 · 10-3
0.13 · 10-3
–
Cohesion
c'ref
0
0
kN/m2
Friction angle
'
31
35
°
Mechanical
Dilatancy angle
1
5
°
Groundwater
Classification type
–
Standard
Standard
–
Soil class
–
Coarse
Coarse
–
Use defaults
–
None
None
–
Permeability in the horizontal direction
kx
1
0.5
m/day
Permeability in the vertical direction
ky
1
0.5
m/day
Interfaces
Strength determination
–
Rigid
Manual
–
Strength reduction factor
Renter
1
0.7
–
Initial
K0
determination
–
Automatic
Automatic
–
Pre-overburden pressure
POP
0
0
–
Over- consolidation ratio
OCR
1
1
–
properties of the sand layers, then assign them to the corresponding clusters in the geometry model.
-
The layers have the following properties
Property
Name
Clay
Deep clay
Unit
General
Soil model
–
Mohr-
Coulomb
Mohr-
Coulomb
–
Drainage type
–
Undrained (B)
Undrained (B)
–
Unsaturated unit weight
unsat
15
16
kN/m3
Saturated unit weight
sat
18
18.5
kN/m3
Mechanical
Young's modulus at the reference level
E' ref
3.4 · 103
9.0 · 103
kN/m2
Poisson's ratio
(nu)
0.33
0.33
–
Young's modulus increment
E'inc
400
600
kN/m3
Reference level
yref
3.0
-12
m
Undrained shear strength at the reference level
su, ref
5
40
kN/m2
Undrained shear strength inc.
su, inc
2
3
kN/m3
Reference level
yref
3.0
-12
m
Groundwater
Data set
–
Standard
Standard
–
Soil type
–
Coarse
Coarse
–
Use defaults
–
None
None
–
Permeability in the horizontal direction
kx
0.1 · 10-3
0.01
m/day
Permeability in the vertical direction
ky
0.1 · 10-3
0.01
m/day
Interfaces
Strength determination
–
Rigid
Manual
–
Strength reduction factor
Renter
1.0
0.7
–
Initial
K0
determination
–
Manual
Manual
–
Lateral earth pressure coefficient
K0,x
0.6
0.7
–
Table 1: Material proprties of the clay layers
Property
Name
Sand
Deep sand
Unit
General
Soil model
–
HS small
HS small
–
Drainage type
–
Drained
Drained
–
Unsaturated unit weight
unsat
16.5
17
kN/m3
Saturated unit weight
sat
20
21
kN/m3
Mechanical
Secant stiffness in
E50ref
25 · 103
42 · 103
kN/m2
Standard drained triaxial test
Table 2: Material properties of the sand layers
Define the structural elements
The tunnel and the building are defined as structural elements.
Define the tunnel
The tunnel considered here is modeling half of a circular tunnel. After generating the basic geometry, follow these steps to design the circular tunnel:
-
In the Structures mode click the Create tunnel button in the side toolbar and click at (0 -17) in the drawing area. The Tunnel designer window pops up displaying the
General tab sheet of the Cross-section mode.
-
Select the Circular option in the Shape type drop-down menu.
-
Select the Define right half option in the Whole or half tunnel drfavorablenu.
-
In the Offset to begin point group set Axis 2 to -2.5. No change is required for the orientation axes.
-
Click the Segments tab to proceed to the corresponding tab sheet.
A segment is automatically created. A new box is shown under the segment list where the properties of the segment can be defined.
-
In the Segment box set the Radius to 2.5 m. The geometry of the tunnel segment
Note: In the tunnel as considered here, the segments do not have a specific meaning as the tunnel lining is homogeneous and the tunnel will be constructed at once. In general, the meaning of segments becomes significant when:
-
It is desired to excavate or construct the tunnel (lining) in different stages.
-
Different tunnel segments have different lining properties.
-
One would consider hinge connections in the lining (hinges can be added after the design of the tunnel, in the general drawing area).
-
The tunnel shape is composed of arcs with different radii (for example NATM tunnels).
-
Click the Properties tab to proceed to the corresponding mode.
-
Right-click on the segment in the display area and select the menu Create > Create plate option in the appearing menu.
-
In Tunnel Designer go to the Material property in the Selection explorer and click the plus button to create a new material dataset. Specify the material parameters for the TBM according.
-
-
-
Material properties of the plates
Parameter
Name
TBM
Lining
Building
Unit
General
Material type
–
Elastic
Elastic
Elastic
–
Unit Weight
w
17.7
8.4
25
kN/m/m
Prevent punching
–
No
No
No
–
Mechanical
Isotropic
–
Yes
Yes
Yes
–
Axial stiffness
EA1
63·106
14·106
1 · 1010
kN/m
Bending stiffness
HI
472.5 · 103
143 · 103
1 · 1010
kNm2/m
Poisson's ratio
0
0.15
0
–
Table 3
-
A Cref value of 0.5% corresponds to a volume loss of 0.5% of the tunnel volume. The actual strain that is applied to the line is half the applied contraction. Hence, the resulting liner contraction is 0.25%.
-
The entered value of contraction is not always fully applied, depending on the stiffness of the surrounding clusters and objects.
-
Click on Generate to include the defined tunnel in the model.
-
Close the Tunnel designer window. Define building
The building itself will be represented by a stiff plate founded on piles.
-
From the sidebar, select Create line > Create plate and draw a plate from (5 3) to (15 3), representing the building.
-
Create a material set for the building according to and assign it to the plate. Do not forget to also create the material set for the tunnel lining.
-
From the sidebar, select Create line > Create embedded beam and draw two piles (embedded beam rows) from (5 3) to (5 -11) and from (15 3) to (15 – 11).
Generate the mesh
-
Create a material set for the foundation piles and assign it to the foundation piles.
-
-
Material properties of piles
Lateral resistance
Parameter
Name
Foundation piles
Unit
General
Material type
–
Elastic
–
Unit weight
7.0
kN/m3
Mechanical
Pile spacing
L spacing
3.0
m
Cross-section type
–
Predefined
–
Predefined cross-section type
–
Solid circular beam
–
Diameter
–
0.25
m
Stiffness
E
10 · 106
kN/m2
Axial skin resistance
Axial skin resistance
Linear
–
Tskin, start, max
1.0
kN/m
Tskin, end, max
100.0
kN/m
Lateral resistance
Unlimited
–
Base resistance
Fax
100.0
kN
Interface stiffness factors
Default values
Yes
–
Table 4: Material properties of piles
Note: A tunnel lining consists of curved plates (shells). The lining properties can be specified in the material database for plates. Similarly, a tunnel interface is nothing more than a curved interface.
-
Right-click the segment in the display area and select the Create negative interface option in the appearing menu.
-
Right-click the segment in the display area and select the Create line contraction option in the appearing menu. In the poly, curve properties specify a value of 0.5% for Cref. The tunnel model is shown.
Tunnel model in the Properties tab
Note: With the Default fixities used, a plate that extends to a geometry boundary that is fixed in at least one direction
obtains fixed rotations, whereas a plate that extends to a free boundary obtains a free rotation.
Generate the mesh
The default global coarseness parameter (Medium) can be accepted in this case. Note that the structural elements (plate and embedded beams) are internally automatically refined by a factor of 0.25.
-
Proceed to the Mesh mode.
-
Define and perform the calculation
-
Click the Generate mesh button in the side toolbar. For the Element distribution parameter, use the option Medium (default).
-
Click the View mesh button to view the mesh as shown.
The generated mesh
-
Click the Close tab to close the Output program. Define and perform the calculation
To simulate the construction of the tunnel it is clear that a staged construction calculation is needed.
Initial phase
-
Proceed to the Staged construction mode to proceed with the definition of the calculation phases.
Define and perform the calculation
The initial phase has already been introduced. Keep its calculation type as the K0 procedure. The water pressures can be generated based on a general phreatic level at a level of y = 0.0 m as already defined in the borehole. Make sure that the building, foundation piles, and tunnel lining are deactivated.
-
-
-
Phase 1: Building
The first calculation phase is used to activate the building.
-
Click the Add phase button to create a new phase.
-
In the Phases window rename the Phase ID as Building.
-
In the Deformation control parameters subtree select the Ignore under. Behaviour (A, B) option. The default values of the remaining parameters are valid for this phase.
-
In the drawing, the area activates the plate and the foundation piles.
-
-
Phase 2: TBM
-
Click the Add phase button to create a new phase.
-
In the Phases window selects the Reset displacements to zero option in the Deformation control parameters subtree.
-
In Staged construction multi-select the clusters inside the tunnel. In the Selection, the explorer deactivates the two soil clusters and set the Water conditions to dry.
-
Activate the circular plate that in this phase represents the Tunnel Boring Machine (and thus has the TBM material set) as well as the negative interfaces. Note that contraction is not active in this phase.
-
-
Phase 3: TBM conicity
-
Click the Add phase button to create a new phase.
-
Multi-select the plates. In the Selection, the explorer activates the contraction.
-
The contraction represents the effects of the cone shape of the TBM (the cutter head has a larger diameter than the tail).
-
The contraction of the tunnel lining by itself does not introduce forces in the tunnel lining. Eventual changes in lining forces as a result of the contraction procedure are due to stress redistributions in the surrounding soil or to changing external forces.
Execute the calculation
-
Click the Select points for curves button in the side toolbar.
-
Select some characteristic points for load- displacement curves (for example the corner point at the ground surface above the tunnel node 6130 and the corner points of the building node 9647).
-
Click the Calculate button to calculate the project.
-
After the calculation has finished, save the project by clicking the Save button.
Results
After the calculation, select the last calculation phase and click the View calculation results button. The Output program is started, showing the deformed meshes at the end of the calculation phases
Deformed mesh after construction of the tunnel (Phase 5; scaled up 20 times)
As a result of the second calculation phase (removing soil and water out of the tunnel), there is some settlement of the soil surface and the tunnel lining shows some deformation. In this phase, the axial force in the lining is the maximum axial force that will be reached. The lining forces can be viewed by double-clicking the lining and selecting force-related options from the Force menu. The plots of the axial forces and bending moment are scaled by factors of 5·10-3 and 0.2 respectively
Axial forces and Bending moments in the lining after the second phase.
The plot of effective stresses shows that arching occurs around the tunnel. This arching reduces the stresses acting on the tunnel lining. As a result, the axial force in the final phase is lower than that after the second calculation phase.
Effective principal stresses after the construction of the tunnel (Phase 2 TBM)
To display the tilt of the structure at the end of the lining installation phase:
-
Click the Distance measurement button in the side toolbar.
-
Click the node located at the left corner of the structure.
-
Click the node located at the right corner of the structure.
-
-
-
RESULT AND DISCUSSION
The piling foundation is impacted by tunnel construction; the maximum total displacements illustrated show the progression of foundation displacement after tunneling. Despite the minor displacement, it demonstrates that as a tunnel is created, each foundation's lateral displacement rises. Although it is well known that the existence of a tunnel causes a rise in pile displacement, the position of the tunnel can also affect this. Here, the tunnel won't produce additional displacement because it is entirely embedded in cracked basalt rock, whereas the tunnel is embedded in stiff clay and is situated extremely close to the tip of the pile, producing the most displacement. Even though the tunnel is situated on clayey soil, its distance from the pile's apex makes its displacement the lowest of all. Total pile displacement varies with depth due to tunnel 'A' different horizontal distances from the pile: Due to tunnel "A" being located at different horizontal distances from the pile, there is a displacement of the pile over its depth.
-
CONCLUSION
In a real-world scenario, a piling foundation is required to support the massive loads of multi-story buildings. However, because of the vast depth of this foundation and the possibility that a newly constructed tunnel may pass near it in the future,
it is now required to estimate how the tunnel will affect the building. This study focuses on the analysis of foundations affected by tunnels using the finite element analysis program PLAXIS2D. Following a detailed review of the simulation's outcomes, the following conclusions can be made:
-
Differential settlement of building between nearer and further column. Create additional reactive forces in form of BM and SF. If the building structure is capable of withstanding these additional forces, the building remains safe
-
Tunnel influence on a building's foundation only occurs when the tunnel is positioned very close to the pile; otherwise, its influence is minimal.
-
The placement of the pile tip about the tunnel's horizontal axis has a significant impact on how the internal forces caused by the tunnel are distributed. The essential arrangement resembles piles that have a point that is just below the tunnel. When a tunnel is positioned at different depths, the position of the tunnel and the tip of the pile determine how much total displacement varies with pile depth.
-
The diameter of the tunnel also has a negligible impact on pile displacement. The displacement of the pile similarly grows as the diameter does.
-
-
FUTURE SCOPE OF STUDY
To improve results, this work can be expanded in the following ways. The analysis is also possible for characteristics other than displacements, such as pile capacity and skin friction. If tunnel loads are also taken into consideration, these results will be improved. The vibration forces of the tunneling process and dynamic loading circumstances during traffic operations conditions were not taken into account when doing this analysis. To achieve good outcomes, the model can be made more realistic by considering these factors. Various pressures, such as grout pressure and TBM face pressure, can be considered while modeling the development of a Tunnel Boring Machine (TBM) with the tunnel slowly approaching the adjoining building.
-
REFERENCES