
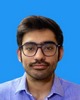
- Open Access
- Authors : Saksham Sangwan , Vishal Sharma , Karan Singh Bora
- Paper ID : IJERTV10IS040009
- Volume & Issue : Volume 10, Issue 04 (April 2021)
- Published (First Online): 13-04-2021
- ISSN (Online) : 2278-0181
- Publisher Name : IJERT
- License:
This work is licensed under a Creative Commons Attribution 4.0 International License
Development and Control of Modular 5 DoF Robotic ARM using ROS
1st Saksham Sangwan Department of Electrical EngineeringDelhi Technological University New Delhi, India
2nd Vishal Sharma
Department of Electrical EngineeringDelhi Technological University New Delhi, India
3rd Karan Singh Bora Department of Electrical EngineeringDelhi Technological University New Delhi, India
AbstractThis paper presents the design and development ofa robust 5-DoF robotic arm. Articulation of the robotic arm is achieved by linear actuators and DC brushed motors. The onboard processing is achieved by Nvidia Jetson Nano along with off-the-shelf motor drivers and microcontrollers for feedback and control. The safety of electronic components and battery management is also kept in mind while designing the sub-system. The software stack is based on Robot Operating System (ROS)to facilitate distributed computing.
Index TermsControl system, inverse kinematics, PID, Robot Operating System
-
INTRODUCTION
In this paper, a 5-DOF robotic arm is designed and devel- oped which capable of lifting objects and performing intricate tasks with high precision in sensitive work environments. The arm uses a combination of linear actuators and DC motors to operate its various links and joints. The end-effector uses DC motors for proper gripping motion using a 2-claw modular and adaptive gripper. All joints and movements are made precise by the use of closed-loop control, through implementation of potentiometer and rotary encoders. At the heart of the system, we have an Nvidia Jetson Nano along with several microcontrollers (Arduino Mega) sending signals to motor drivers for motor actuation. A robust and flexible software architecture has been developed upon the existing framework of Robot Operating System. Two digital cameras have also been deployed for providing necessary visual feedback.
OpenCV in conjunction with ROS has been used to compress and collect visual data from the cameras ensuring optimal FPS. OpenCV can also be utilised for object detection toprovide autonomous capabilities to the arm. A combination of forward and inverse kinematics has been implemented to ensure ease of control along with minimal computation power. The power distribution system is straightforward and efficient. A kill switch has also been implemented for safety purposes. Through proper commands and necessary modifications as per the task at hand, the arm can be used for a variety of real-world applications including assembly line in factories, astronaut assistance onboard a rover, and bomb defusal.
Our objective through this project is to develop a general- purpose robotic arm which can be utilized in various industrialas well as educational scenarios. It can also be seamlessly
Fig. 1. Final Developed 5 DOF Robotic Arm
integrated with several other sub-systems. The design has been kept modular for easy manufacturing and maintenance. The off-the-shelf products used are easily available, have proper documentation and support to speed-up the development pro- cess of the arm.
-
MECHANICAL SUB-SYSTEM
The robotic arm is designed to provide stability and keep the weight as low as possible. Carbon fibre tubes and aluminium links along with 3D-printed end-effector jaws are used. Low weight nylon gears are also used in place of mild steel, and a worm gear is attached at the base for 360 degree rotation ofthe arm.
Part(s)
Material
Reason for Selection
Links
Gripper, Joints Worm
Carbon Fiber
Aluminium Mild Steel
Excellent strength
to weight ratio Good strength ratio and cost efficient High strength and good machinability
Part(s)
Material
Reason for Selection
Links
Gripper, Joints Worm
Carbon Fiber
Aluminium Mild Steel
Excellent strength
to weight ratio Good strength ratio and cost efficient High strength and good machinability
TABLE I SELECTION OF MATERIALS
Fig. 2. Mechanical Design – Full Assembly
-
Link Selection
After extensive research and analysis, single tube type linksand orientation capability of 5- DOF has been finalized. Bend- ing and shear tests were the primary criteria for selecting the design and material. Carbon fiber links along with aluminum connectors have been incorporated in the design to maintain ideal strength to weight ratio. The thickness of the carbon fibertubes was selected after several iterations using Ansys 18.
Fig. 3. ACP Analysis of Carbon Fiber Links
-
Gripper Assembly
The mechanism of our gripper is based on lead screw mechanism to increase its gripping capabilities. The jaws of the gripper are made by 3D printed TPU along with spring capabilities which will further improve its grip. Nylon gears are used in the gripper to get required motion as it provides light weight and optimum strength for low torque operations.
-
-
ELECTRICAL SUB-SYSTEM
Our robotic arms electrical and electronic sub-system con- sists of linear actuators and DC brushed motors for actu- ation, microcontrollers, potentiometers for feedback, power electronics converters (DC-DC buck-boost converter and mo- tor drivers), battery, battery management circuits and safety circuits.
Fig. 4. Gripper Assembly
-
Motor and Actuators
We have used two heavy duty linear actuators with dynamic thrust of 800 N and static load of 2,225 N with a 4-inch stroke length. These actuators have a built-in 10K potentiometer that provides us absolute position feedback. The mounting points of linear actuators have been decided so that the shoulder joint has 90 degrees range of motion and elbow has 150 degrees range. We have a worm wheel on the swivel base, to provide the 360-degree rotation of the robotic arm.
Linear actuators have higher efficiency and precision when compared to DC Brushed motors. Thus the joints that expe- rience the most load i.e the elbow and shoulder, for them we used linear actuators. This drastically reduced the jitters and backlashes which were difficult to avoid if we used DC brushed motors. The built-in potentiometer was used to provide feedback of actuator length. DC brushed motors were used for base motor and all the end effector motion. The end effector can perform roll, pitch motion and gripping action. DC Brushed motors are not only easy to control but their controllers are low cost, require less size and easily available.
-
Control System
We have designed a custom control system to control position of linear actuators and DC brushed motors. The control system that we have designed is very simple and canbe divided into following parts:
-
Sensors
-
Microcontroller Unit
-
Actuator/Motor Controlling Unit
We are using Independent Joint Control Mechanism that further utilizes Inverse Kinematics to move all the joints in3D space simultaneously. Independent joint control (IJC) is a conventional and simple control mechanism for motion control of a joint. In our case we use each link of robotic arm independently,i.e, both the linear actuators and the base motor have their own control system loop.
Fig. 5. Assembled Robotic Arm
Fig. 6. IJC Mechanism Flow [1]
Variations and events like vibration in sensor mount, gear backlash and load changes cause unpredictable effects on control mechanism thatultimately can cause degradation in accuracy and performance of PID control [2].
-
-
Sensors
We used potentiometers to sense the position of the motor shaft and length of actuator stroke in the robotic arm. Actu- ators have inbuilt 10K potentiometer which requires 5V and ground input and gives analog linear output (0-5V) that is converted to digital signal when interfaced with MCU. The resolution of the potentiometer can be increased by using a MCU with higher order ADC. For example, in our case we used Arduino Mega which has 10 bit ADC, i.e., an input analog signal ranging from 0-5 V can be converted to digital signal ranging from 0-1023.
-
Microcontroller Unit
In this paper, we used Arduino Mega which has 8-bit ADC and plays a major role in processing the signal received from the potentiometer. For implementing PID algorithms efficiently, we made our own libraries that made our code efficient and fast. The PID coefficients were set by trial and error method. With its three-term functionality covering treat- ment to both transient and steady-state responses, proportional- integral-derivative (PID) control offers the simplest and yet most efficient solution to many real-world control problems.
Fig. 7. Base Motor Control Loop
-
Motor Controllers
The main controlling unit of motors are motor drivers. Based on the set reference values and the signal received from the sensors, a PWM signal and direction signal is generatedby the MCU, which is interfaced with I/O pins of the motor controller. Motor controllers generate a response accordingly and control the motors connected to output terminals. The microcontroller used has the ability to provide PWM signal with resolution up to 255 bits, which when interfaced with the motor driver is able to precisely control the motors speed and position. The motor drivers are selected on the basis of current and voltage rating of motors, battery used and MCU that is interfaced. We have used Cytron MD10A in our robotic arm considering parameters mentioned above.
-
Inverse Kinematics
We have implemented a combination of forward and in- verse kinematics in order to operate the Robotic Arm in the surroundings. Thus, it is easy for user to operate the arm and it does not load the CPU with complex matrix calculations as well. If we use a IK algorithm for higher DoF robotic arms then the matrix calculations get quite complex and requirehigh computational power. Hence, we use Inverse kinematics in 3 joints i.e., base, shoulder and elbow joints. In rest of the joints, we use forward kinematics.
-
Power Distribution System
Our power distribution model is simple but efficient. We have used buck-boost converters in order to distribute power from a single 24 V battery to different components which have different voltage requirements. We have used PDBs and XT60s that increase the reliability of the system with ease in changing connections or removing faulty modules over time. For accommodating the power requirements of other systems, UBECs (universal battery eliminator circuit) and buck-boost converters are used to convert the fed voltage to required voltage levels i.e.,
DC-DC Conversion to 12V rails and 5V rails. The 12V rails are used to isolate the 12V motors from any of the 12V electronics as they may experience malfunctions due to electromagnetic interference from the motor. UBECs are used for their high efficiency, easy handling
Fig. 8. Power Distribution Flowchart
and low rise in temperature while in use for a prolonged time.
Fig. 9. Power Distribution System in Final Developed Phase
-
Safety Methods
Following safety measures have been employed to ensure safety of our electrical/ electronic system:
-
Limiters:
We have designed a special safety circuit that cuts off current from motor drivers whenever a mechanical link collides with another link with the help of a limiter. However, if the user moves the arm away from thelink then the current is allowed to flow in the opposite direction. For this we have used a 10 A diode.
Fig. 10. Safety Circuit Schematics
-
Kill Switch:
-
The battery is connected to the rest of the power system through an emergency disconnect switch acting as a kill switch; easily visible and reachable in case of an emergency or power failure. Battery is also connected to low voltage buzzer alarms for notifying low levels.
-
-
SOFTWARE SUB-SYSTEM
The software architecture is modular and easy to understand. The arm is remotely controlled via joystick commands that send data over a network to the Jetson Nano. First, the joystick, which is connected to a base station laptop via USB, is mappedbetween threshold values via a python node integrated using ROS. The next python node converts the mapped value to
Fig. 11. Joy Node Terminal Logs
an integer between the threshold PWM values that can be provided to the motor (-255/255) and sends the command to the Jetson Nano for further communication via a dedicated and customized ROS message. This message is also used to send the exact location coordinates- if the arm is several meters away from the control station. The PWM signal is then sent to an Arduino-ROS node that further communicates the signal to the motor driver accurately for the movement of the particular joint. This flow of channel is within the ROS environment which makes it easier for us to integrate multiple hardware such as Nano and Arduinos along with scripts performing different actions in Python. The commands are encoded into a ROS message and sent over a dedicated ROS topic for latency- free, fast paced communication between the base station laptop and the Nano on the arm. There are multiple advantages linked to integrating the ROS [3] environment. This saves the computation power required for each signal and makesa strong connection following TCP/IP protocol. Also, the architecture is easily scalable to multiple robots moving in distinct environments. The environment uses a CLI that is user-friendly.
-
Camera and openCV
The robotic arm consists of two webcams for visual feed- back (Logitech C525 and Logitech C270). The feed is encoded
Fig. 12. Complete Control Flow of the Arm
Fig. 13. Interfacing Camera and OpenCV using ROS
and then transmitted via ROS to ensure optimal FPS. The cameras are connected to the Nano via USB for ease of use. OpenCV is an open-source stable library for 2D image processing, used in a wide variety of applications. Much of ROS makes use of 3D sensors and point-cloud data, but there are still many applications that use traditional 2D cameras and image processing for which OpenCV is ideal. The encoding and decoding of the video is achieved through OpenCV.
-
-
CONCLUSION
In this paper, we presented the process to develop the end-to-end system for a 5-DoF robotic manipulator. The armis made of carbon fibre and aluminium links. DC brushed motors and linear actuators are controlled by motor driversand Arduino microcontrollers. The main onboard processoris Nvidia Jetson Nano. Robot Operating System environment is implemented for better control and stability. Webcams are implemented on two locations on the arm for visual feedback. Closed loop feedback system along with PID control is implemented and the arm is operated with a mix of inverse and forward kinematics. The robotic arm can be operated wirelessly and is optimum for mobile deployment. It has
a wide range of applications in the industry such as bombdefusal, mars/moon rover and industrial automation.
Fig. 14. Arm Performing Precision Task
ACKNOWLEDGMENT
We would like to express our gratitude towards the Depart- ment of Electrical Engineering, Delhi Technological Univer- sity for their guidance and support.
REFERENCES
-
W. Chung, L.-C. Fu, and S.-H. Hsu, Motion Control. Berlin, Heidelberg: Springer Berlin Heidelberg, 2008 pp. 133159. [Online].
Available: https://doi.org/10.1007/978-3-540-30301-57
-
N. Shimkin, Nonlinear Control Systems. Berlin, Heidelberg: Springer Berlin Heidelberg, 2009, pp. 28862889. [Online]. Available: http://doi.org.https.nlic.proxy.nbdlib.cn/10.1007/978-3-540-29678-240 21
-
M. Quigley, K. Conley, B. Gerkey, J. Faust, T. Foote, J. Leibs, R. Wheeler, and A. Y. Ng, Ros: an open-source robot operating system, in ICRA workshop on open source software, vol. 3, no. 3.2. Kobe, Japan, 2009, p. 5.