
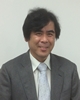
- Open Access
- Authors : Yuichi Hasuda , Keita Hirayama
- Paper ID : IJERTV10IS050076
- Volume & Issue : Volume 10, Issue 05 (May 2021)
- Published (First Online): 14-05-2021
- ISSN (Online) : 2278-0181
- Publisher Name : IJERT
- License:
This work is licensed under a Creative Commons Attribution 4.0 International License
Development and Usability Test of Pesticide Spraying Robot for Greenhouse
Yuichi Hasuda
Professor, Department of Information and Electronics Engineering, Teikyo University, Japan
Keita Hirayama
Engineer, TS TECH Co., Ltd., Japan
Abstract:- The purpose of this study is to introduce the development of a pesticide spraying robot to prevent the health hazards such as pesticide poisoning and heatstroke that occur during spraying pesticides in a greenhouse and to compensate the farmers' shortage due to the aging and decrease of farmers. This robot is autonomous and can be operated unmanned. It moves between ridges in the greenhouse by line traces and sprays pesticides based on the results of image recognition and measurement of the distance to crops by ultrasonic sensors. Using n CCD camera for line tracking was adopted as the driving method. The width of the robot was kept within 50 cm, so it was possible to significantly reduce costs and maintain the yield of crops without having to rebuild the fields. In addition, identifying the crops to apply pesticides by image recognition and accurately applying pesticides only to the crops, the usage of pesticides was reduced by about 42%. This has the advantage of reducing the cost of pesticides and reducing the impact of pesticides on crops. As a future improvement of the robot, we will try to reduce the cost by replacing myRIO used in the microcomputer with an inexpensive microcomputer such as Arduino. Robots have already been put in Practical use for cucumbers, white radishes, and peanuts, tomatoes, etc., but we will continue to put them into practical use for other types.
Keywords:- Pesticide spraying robot, greenhouse, image analysis, autonomous robot
-
INTRODUCTION
To prevent farmers from heatstroke and poisoning while spraying pesticides in the greenhouse, using a robot to automate the process of pesticide spraying is being strongly demanded. According to research conducted by the Ministry of Agriculture, Forestry and Fisheries (MAFF), there was one fatal accident reported in 2015 while spraying pesticides [1]. In Japan, about 10 to 20 people suffering from heatstroke and poisoning accidents while spraying pesticides every year [2]. Although masks or protective clothing are worn when spraying pesticides, the lack of ventilation of air inside the green-house may cause them to inhale the pesticide even with the presence of a gas mask, which may lead to poisoning. There is a risk of getting heatstroke while spraying pesticides manually under high humidity weather, especially during summer [3,4]. Furthermore, the number of pests will be increased in high temperature which led to increasing the number of pesticides spraying. There are several examples of pesticide spraying robots are being used [5-9]. For example, a robot that follows a track and sprays pesticides at a predetermined point. However, they require a high investment amount for track installation due to the elevation difference of the land between ridges [10].
In this study, we will introduce a robot that does not require a track and automatically drives and sprays pesticides to prevent health damage to farmers while spraying pesticides manually in the greenhouse. To deal with the decrease in farmers and the aging problem, unmanned and automatized method. should be used. In addition, if there is no crop, it will pass through without spraying pesticides to reduce the operation time and to spray pesticides efficiently [11].
-
DEVELOPMENT OF PESTICIDE SPRAYING ROBOT
-
Functions of pesticide spraying robot:
Usually, ridges dimensions are about length 40m and width 1m and the spaces between ridges are 0.7m or less. While moving in the spaces between ridges, the robot sprays the ridges on both sides at the same time to spray pesticide efficiently. To move accurately between the ridges, the lines for tracing are being installed [12-14]. A CCD camera is connected to myRIO and line tracing is performed using LabVIEW [15]. To spray only nearby crops, we have created a program that sprays pesticides only when it recognizes an object within a specified distance with a distance sensor and analyzes the images from a CCD camera to judge whether the object is a crop or not. To reduce the operation time required by spraying pesticides, our program will perform the following actions… When an object is recognized within a specified distance, it will move at approximately 15m/min which is the walking speed of a man. Otherwise, it will move at 54m/min.
A plastic tire with a diameter of 140 mm and a width of 50 mm is being used for moving on ridges. To move on mud, rod-like rubber with a diameter of 4 mm is installed to the tire at an interval of 23 mm. Up to now, pesticide spraying robots usually supply pesticides from tanks using hoses. However, it is difficult to supply pesticides with a hose inside the greenhouse, so we used two market goods atomizers which are installed with pesticide tanks (maximum volume up to 7 liters) for spraying. By installing two relays to control the motor of each atomizer and sending a command to control each pesticide spray to each relay, the pesticides are sprayed independently on the ridges on both sides of the robot [16].
-
Robot dimensions and system configuration diagram:
The width of the robot is designed to be less than 450 mm due to the gap between the ridges of the greenhouse in Japan which is very narrow. Fig. I show the developed pesticide spraying robot, and Fig. 2 shows the configuration diagram of
the spraying nozzle and the drive unit such as the CCD camera.
Fig.1 Overall view of pesticide spraying robot
Fig.2 System configuration diagram of myRIO
Movable spray nozzles are attached to the left and right sides of the robot so that pesticides can be sprayed independently on the ridges on both sides. Since the spray area suitable height the pesticide should be sprayed narrowed down and needed to spray at pinpoint, only one spray port is being used on each side. The angle of the spray nozzle will be adjusted by using a DC motor, to match the depends on the growing of the crop.
Fig.3 shows the dimensions of the robot. The size of the robot was set to be 793mm in length; 430mm in width; 997mm in height to travel in a wide ridge. The robot has distance sensors and CCD cameras installed in the above order in the direction of motion and can recognize the above crops. Moreover, intending to improve waterproofing, a cover has attached to the robot body, the drive unit, and the motor.
A. Pesticide spraying and robot movement program design:
To run the robot smoothly in the greenhouse, we connected a CCD camera (HD-WEBCAMC270n) to myRIO and used LabVIEW to create a line trace program [17]. Images were continuously acquired from a CCD camera using Vision Acquisition2, binarized with Vision Assistant, and image analysis was performed using straight edges. The drive amount of the DC motor is controlled by the value of the straight edge inclination. A straight-line edge changes from a negative value to a positive value depending on the angle of
the line inclination. Therefore by subdividing the value of the straight-line edge, a straight line or a curved line will be possible to perform.
(a): Overhead view of the robot
(b): Front view of the robot
(c): Side view of the robot
Fig.3 Appearance of pesticide spraying robot
Fig4 Image analysis program for pesticide application
Fig.4 shows an image analysis program for pesticide application. In the case of the crops within 60 cm to the spray nozzle which is installed with a distance sensor, the signal of True will be sent to the next case structure. Otherwise, the next case structure will receive a signal of false (Fig.4 ). When the received command signal is True, the CCD camera acquires the image in real-time, then outputs the image on the front panel named Image. Next, the color of the specific crop in the acquired image is analyzed by the HSV method. The crops of the image are binarized to white and the other crops to black [17,18]. The result will be output Image2. Last, to recognize crops hidden in the shadow, the image out turned to Image2 is being smoothed and output to Image3 (Fig. 4). When the crop color in Image3 is within the specific analyzed range, the value of First Edges becomes larger than 0 and the relay turns on, otherwise, it turns off (Fig. 4 ). Image analysis will not be performed when the result of distance measurement returns a False signal (Fig. 4). As a result, the amount of pesticide sprayed can be reduced by robot only sprays when crops nearby. To reduce the operation time required for pesticides we made spraying, a program that added image analyzing technique to the robot movement program. If the distance sensor detects an object within 60 cm, it will travel at a walking speed of 15 m/min, and if not, it will travel at 54 m/min. If there is no crop, it will pass through it; if there is a crop, the pesticide spraying time will be shortened by spraying the pesticide while moving at a walking speed.
Fig.5 Pesticide application demonstration experiment in the campus field
-
-
TEST RESULTS
-
Line tracing by using image analysis program:
To confirm whether the robot moves in the actual field, accurately recognizes the crops and sprays the pesticide normally or not. The demonstration experiments were conducted in a peanut field located at Teikyo University Utsunomiya Campus. Fig. 5 shows the robot spraying pesticides in the test field where we performed the test. By binarizing the line, the directions in which the robot movements are determined based on the straight-line edge value changed by the inclination of the line [17,18]. If the value is negative, turn right; if the value is greater than 20, turn left; if the value is 0 to 19, straight. We tried PID control to control the drive amount of the motor, but sometimes
could not be bent on the floor surface in the room. The value of the straight-line edge is subdivided into one straight line pattern and three patterns that bend to the left and right. A total of seven patterns can be used corresponding to the curved line. As a result of executing the line tracing program, it was possible to trace the line even with a black curve which is gradually changing the angle. By dividing the pattern, it becomes easier to control the power of the motor. The tests were conducted on uneven terrain and the robot worked fine and was able to run across the ridge.
-
Testing the pesticide spraying robot in field:
Results of executing the crop recognition program shown in Fig. 6. The image of the crops (Fig.6 (a)) captured by the camera was binarized by green, (Fig.6 (b)) and smoothed by LPF (Fig. 6(c)). The frame indicated by the red rectangle shows the area where the vertically moving nozzle sprays
pesticides. When the robot recognizes that there is a green crop in the frame indicated by the red rectangle, it will spray the pesticide. The operation of the relay was confirmed by turning on the virtual LED, and it was confirmed that the robot could also spray pesticides outdoors.
We attempted a robot usability test on white radish, cucumber and decreased the usage of pesticides. Some pesticide spraying robots do not control the movement of nozzles, but compared to these conventional types, the robots in this study perform image analysis while operating the nozzles, so the amount of pesticide used can be reduced! Not only on soybeans, but we also tried to spray pesticides on white radish, cucumber, and zucchini as shown in Fig.7. As an example, when a pesticide application test was conducted on white radish and edamame, the pesticide could be automatically reduced by about 40% as shown in Fig. 8.
(a): Overhead view of the robot (b): Overhead view of the robot (c): Overhead view of the robot Fig.6 On-campus crop recognition tests
(a): White radish (b): Cucumber
Fig.7 Attempt to spray pesticides on white radish, cucumber and zucchini
Fig.8 Pesticides reduction rate decreased during test on white radish
-
-
DISCUSSION
Many attempts have been made to develop pesticide spraying robots around the World to prevent pesticide poisoning [19-22]. The feature of the autonomous type used by the robot in this study is that the operator is prevented from heatstroke due to inhalation of pesticides and high temperature and humidity when comparing to the operation type. Furthermore, unmanned work can reduce w the workloads of farmers, which is a great advantage for countries with a decreasing birthrate and population aging. In some cases, the movement system uses rails to move the robot within the Greenhouse [23]. This method does not require the robot to judge the traveling route and can perform accurate and stable traveling, but it requires a large amount of cost to install rails and rebuilding the greenhouse [24]. In this research, the robot movement system is using line tracing. It is because if the line between the ridges can be recognized by the image analysis by the CCD camera, only the line needs to be drawn. In addition, the cost can be drastically reduced. Since we have succeeded in keeping the width of the robot within 50 cm, it can be introduced immediately without renovating the conventional fields in the Greenhouse. Furthermore, the ridge area in the Greenhouse is not been reduced a lot which will be led to great merit that the crop yield can be maintained. The disadvantage of the line trace method used in this study is that it must run on uneven terrain. It is necessary to improve running stability, for example, the robot sways to the left and right caused by the slip of running tires.
The robot developed in this study is equipped with a CCD camera and is also characterized in that it can identify crops which pesticides are applied by image recognition by accurately spraying only the crops [25], we have succeeded in reducing the number of pesticides by about 42% comparing to the past (Fig.8) [26]. This has the advantage of not only reducing the cost of pesticides but also reducing the impact of pesticides on crops.
As a future robot improvement, we will try to reduce the cost by replacing myRIO used in the microcomputer with an inexpensive microcomputer such as Arduino. The robot of this research has already been put into practical uses for crops such as cucumbers, white radish, and peanuts, tomatoes, etc., and will be put into practical uses for other kinds of crops (Fig.7) [26].
-
CONCLUSIONS
We have developed a pesticide spraying robot to prevent health hazards to the workers such as pesticide poisoning and heatstroke, which derived from pesticide spraying in Greenhouse, and concluded the following statements. is
-
The developed pesticide spraying robot is automatized and made to prevent health damage to the farmers. In addition, the farmers' shortage due to aging can be compensated and the decrease of farmers can be reduced. A CCD camera for line tracing is adopted as the driving method. The width of the robot was kept within 50 cm, hence there is no need to reconstruct the field, and it is possible to significantly reduce costs and maintain the yield of crops.
-
We used an image recognition technology to identify the crops, robot sprays pesticides to the target crops only which
can reduce the usage of pesticides by 42%. The technique stated above can reduce the cost of pesticides and reduce the impact of pesticides on the crops.
-
As a future improvement of the robot, we will repace the myRIO used for the microcomputer with an inexpensive microcomputer such as Arduino to reduce the cost. Robots had been put to practical use for cucumbers, white radishes, peanuts, and tomatoes, etc. We will also promote practical use for other types of crops.
-
Robot had been put to practical use for cucumbers, white radishes, peanuts and tomatoes etc. We will also promote practical use for other types of crops.
REFERENCES
-
Ministry of Agriculture, Forestry and Fisheries, Trends of Farmers and New Farmers,
https://www.maff.g .jp/j/wpaper/w_maff/p8_h/trend/1/t1_2_1_02.ht l, 1/31/2021. (in Japanese)
-
Ministry of Agriculture, Forestry and Fisheries, accidents and damages caused by the use of pesticides, http://www.maff.go.jp/j/nouyaku/n_topics/p0higai_zyokyo.html, 1/31/2021. (in Japanese)
-
Yuji Saito, Osamu Kashimura, Tsuneyuki Noda, Masao Sakurai, Thermoregulatory responses of agricultural workers at house cultivation work under heat environmental conditions in summer, Jpn.
J. Biometeor., 53 (2), pp.95-103, 2016. (in Japanese)
-
Yuji Saito, Osamu Kashimura, Tsuneyuki Noda, Masao Sakurai, Actual conditions of heat disorders and hydration status in agriculture personnel working in a greenhouse, Jpn. J. Biometeor., 54, (1), pp.13- 22, 2017. (in Japanese)
-
Yoshinori Adachi, Hajime Aoyama, Kazuyoshi Ishikawa, Saori Ishimura, Yuichi Satsumi, AsamiTakahashi and Kazutaka Yokota, deveropment of Agricultural Chemicals Injection Robot (2ndReport), The Robotis Society of japan, 29, (7), pp.584-591, 2011. (in Japanese)
-
Takahiro Kitajima, Akinobu Kuwahara, Development of autonomous mobile pesticide spraying robot, Technical Report, Graduate School of Socio Techno Science Research Center, 17, pp.20-21, 2016. (in Japanese)
-
Kyo KOBAYASHI, Current Status and Approach for Improvement of Farm Work Safety and Comfort Farming, The Japan Society of Mechanical Engineers, 113, (1100), pp.523-526, 2010. (in Japanese)
-
Kaoru KUMAGAI, IT Agrotechnology Utilized Geospatial Information, The Japan Society of Mechanical Engineers, 113, (1100), pp.531-533, 2010. (in Japanese)
-
Michio KISE, Agricultural Automation and Robotics at the U,S, and European Companies Auto- guidance vehicle products and examples of agricultural robotics researches at the companies , The Japan Society of Mechanical Engineers, 113, (1100), pp.534-538, 2010. (in Japanese)
-
Yuichi Hasuda, Toshihiko Tokoi, Hiroki Inamura, Development of a pesticide spraying robot that runs autonomously in a house, The 3rd Robot Technology Education Symposium, pp.46-47, 2018. (in Japanese)
-
Yuichi Hasuda, Hiroki Inamura, Development of pesticide spraying robot, The Japan Society of Technology Education 31st Kanto Branch Conference (Ibaraki), pp.45-46, 2019. (in Japanese)
-
Yasuhiro ohyama, Hiroshi Hashimoto, Robot Sensing-Sensor and Image/Signal Processing-(Introductory series of illustrated robot technology), Ohmsha, Ltd, pp.84-87, 2007. (in Japanese)
-
Makoto Mizukawa, Tie Kasuga, Yoshinobu Andou, Introduction to line trace robotRoboBooks, Ohmsha, Ltd, pp.2-3, pp.12-14, 2003. (in Japanese)
-
Nobuto Matsuhira, Junji Oaki, Easy-to-understand robot system introduction-from mechanism to control, Ohmsha, Ltd, pp.73-75, 1999. (in Japanese)
-
Gaku Hashimoto, Shigehiro Yamamoto, Akira Urashima, Introduction to LabVIEW image measurement, Kodansya, Ltd, pp.39-48, 2011. (in Japanese)
-
Yuki Okamoto, Easy relay and sequencer, Ohmsha, Ltd, pp.18-22, 2003.
-
Afrel, LabVIEW-based myRIO x TETRIX Ver.2, Afrel, pp.45-48, 2018. (in Japanese)
-
Ron Berenstein, Ohad Ben Shahar, Amir Shapiro, Yael Edan, Grape clusters and foliage detection algorithms for autonomous selective vineyard sprayer, Intel Serv Robotics, 3, pp.233243, 2010.
-
Peng Jian-sheng, An Intelligent Robot System for Spraying Pesticides, The Open Electrical & Electronic Engineering Journal, 8, pp.435-444, 2014.
-
Philip J. Sammons, Tomonari Furukawa and Andrew Bulgin, Autonomous Pesticide Spraying Robot for use in a Greenhouse, Australian Conference on Robotics and Automation, Sydney Australian 2008.
-
Parmar Milan, Dafada Jigna, Chauhan Kamlesh, Mehul Bataviya, Kapil Raviya and Makawana Dhaval, Automatic Pesticide Spraying Robot: Design, Development and Febrication based on farming, International Journal of Trend in Research and Development, 5, (2), pp. 635-637, 2018.
-
Dhiraj N. Kumbhare, Vishal Singh, Prashik Waghmare, Altaf Ansari, Vikas Tiwari, Prof. R.D. Gorle, Fabrication of Automatic Pesticides Spraying Machine, International Research Journal of Engineering and Technology, 3, (4), pp.912-916, 2016.
-
Naoki Nakao, Hiroshi Suzuki, Takahiro Kitajima, Akinobu Kuwahara and Takashi Yasuno, Path Planning and Travelling Control for Pesticide-Spraying Robot in Greenhouse, Journal of Signal Proccecing 21, (4), pp.175-178, 2017.9
-
Mitul Raval , Aniket Dhandhukia and Supath Mohile, Development and Automation of Robot with Spraying Mechanism for Agricultural Applications, International Journal for Research in Emerging Science and Technology, 2, (8), pp.60-66, 2015.
-
Pvr Chaitanya, Dileep Kotte, A. Srinath, K. B. Kalyan, Development of Smart Pesticide Spraying Robot, International Journal of Recent Technology and Engineering, 8, (5), 2020.
-
Yuichi Hasuda, Toshihiko Tokoi, Cihiro Tayama, Hiroki Arai, Development of a pesticide spraying robot to prevent health damage in the house, The Japan Society of Technology Education The 30th Kanto Branch Conference (Utsunomiya), pp.33-34, 2018. (in Japanese)