
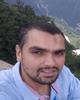
- Open Access
- Authors : Imam A. I , Fatma Abd El Gawad , G. A. El-Termezy , Soha G. Abd El Hamid, Heba, I. A. Mohamed
- Paper ID : IJERTV11IS120093
- Volume & Issue : Volume 11, Issue 12 (December 2022)
- Published (First Online): 26-12-2022
- ISSN (Online) : 2278-0181
- Publisher Name : IJERT
- License:
This work is licensed under a Creative Commons Attribution 4.0 International License
Development of A Turkish Threshing and Winnowing Machine to Suit Fenugreek Crop
Imam A. I.; Fatma Abd El Gawad, G. A. El-Termezy, Soha G. Abd El Hamid, Heba, I. A. Mohamed
Agric. Eng. Res. Inst., Agric. Res. Center, Dokki, Giza, Egypt
Abstract:- Fenugreek (Trigonella foenum graecum L.), which belongs to the botanical family of Leguminosae, is a widely used medicinal plant all over the world. Fenugreek seeds are used as a natural anti-diabetic, antioxidant, anti-cancer and antipyretic. The aim of this work is to modify the local thresher and study the feasibility of using local cereal threshing machine for threshing fenugreek crop. The modified thresher was evaluated using various operating factors, at thresher drum speeds of 520, 580, 640, and 700 rpm, moisture contents of fenugreek straw 10.16, 12.45 and 14.87 % and feeding rate of 8, 10, 12 kg /min. The evaluation included threshing productivity, total seed losses, threshing efficiency, specific energy cleaning efficiency and operational cost. The results concluded that the optimum conditions for threshing of fenugreek crop by using the modified thresher are the following: drum speed of 640 rpm, feeding rate 10 kg/min, and straw moisture content 10.16 %. The obtained results at optimum conditions were: The obtained results at optimum conditions were: threshing productivity of 0.59 Mg/h, total losses 5.67 %, and threshing efficiency of
96.89 %, cleaning efficiency 99.33 %, specific energy of 22.69 kW h/Mg and operational cost of 117.55 L.E/Mg.
Keywords: Fenugreek, Trigonella foenum-graecumL, threshing machine, threshing moisture content, threshing feed rate and threshing drum speed.
INTRODUCTION
Fenugreek (Trigonella foenum graecum L.) is one of important medicinal and aromatic plants. It is the member of Leguminosae family. It is widely cultivated in most regions of the world for its medicinal value (Petropoulos, 2002). Fenugreek has been medicinal properties such as anti-hyperthyroidism, wound healing, anti-diabetic, antioxidant, anticancer, and antipyretic, antimicrobial, anti-allergy, anti-sterility and anti-inflammatory effects (Acharya et al., 2008). Meghwal and Goswami (2012) mentioned that fenugreek contains a High fiber amount, phosphor-lipids, glycolipids, linoleic acid, oleic acid, choline, and vitamin A, C, B1, B2, niacin, nicotinic acid and several elements. It is being commercially grown in Egypt, Morocco, North Africa, Middle East, Pakistan, India, Iran, Afghanistan, Nepal, Spain, Turkey, Argentina and France (Flammang et al., 2004 ; Altuntas et al., 2005). In Egypt, according to Statistics Book (2018), 2881 tons of fenugreek produced from an area of 2910 fed.El-Hadad (2000) stated that Decreasing feed rate and increasing drum speed leads to increasing threshing efficiency. Khater (2000) indicated that the threshing efficiency and seed damage increased by decreasing moisture content. He indicated also that the moisture content percent of 14 % is the preferred; forasmuch giving the lowest seed damage, seed losses, and highest threshing efficiency. According to Simonyan and Oni (2001), the increase in extractor and threshing efficiency of locust bean with reduction in the moisture content. In addition, one of the factors that affected the threshing effectiveness was the cylinder speed.Ebaid et al. (2004) developed the chamber by removing the feeding auger from a wheat thresher. The machine evaluated using different operating conditions. The results of the study revealed that the chamber could achieve a purity efficiency of 99.30% and a total grain loss of 0.16% with drum speed of 870 rpm, feed rate of 1200 kg/h, blower air speed of 6 m/s, air speed suction of 32 m/s and tilt angle of 5°for sieves.Ajav and Adejumo (2005) mentioned that the threshing efficiency increased by increasing cylinder velocity with a given clearance level and moisture content. They added that the total losses were influenced significantly by the cylinder velocity, where the total losses were the least at the lowest cylinder velocity of 4.2 m /s and increased with increasing it. Zakaria (2006) modified the threshing drum in a local thresher machine to fit flax capsules separation. The thresher was evaluated and tested under four feed rates of 8.57, 12.86, 17.14 and
21.43 kg/min with drum speeds of 24.25, 25.81, 27.33, and 28.85 m/s. Data showed that the optimum machine threshing efficiency of 96.92 % at 28.85 m/s for drum speed, feed rate of 8.57 kg/min, 12 fingers on drum with separation time of 15 seconds. Zaki (2006) concluded that the optimum operation conditions for reducing total seed losses and seed damage with an acceptable cleaning efficiency level for black seed at using clearance between 2.5 and 3 mm, drum speed between 3.3 and 4.4 m/s, air speed from 2 m/s to consumed energy of 25.12 kW.h/ton and cost 752 L.E/ton.Afify et al. (2007) developed and tested a local flax threshing machine to thresh black seed crop with high efficiency. It concluded that the lowest value of seed losses of
1.97 % at feed rate of 600 kg/h, drum speed of 6.28 m/s and seed moisture content of 13.63 %. While, the threshing, cleaning and stripping efficiencies of 98.74, 95.88 and 99.31 % with the same previous conditions.Askari et al. (2008) during the evaluate and test of a power tiller device operated small thresher Found that total seed damage increased by decreasing crop straw moisture content and increasing drum peripheral speed.
Ismail and Elhenawey (2009) evaluated a pedal-operated sunflower thresher that was constructed and designed to determine the optimum operating conditions at three levels of the pressure surface on a friction drum of 2.0, 4.0, and 6.0 kg/cm2, and different radial curves of pressure surface of 330, 345 and 365 mm with four levels of friction drum speed of 2.2, 3.7, 4.9 and
6.9 m/s and different resting times for sunflower inside the threshing chamber of 5, 10 and 15 sec. Karthik et al. (2015)
designed and tested a multi crop thresher. The machine was evaluated for safflower at with two moisture contents of 10.89 and
12.05 %, three cylinder speeds of 840, 735 and 630 rpm, feed rates of 240 and 180 kg/h and constant concave clearance of 3.2 cm. A threshing efficiency of more than 98 % and grain output of 28.84 72.48 kg/h were obtained. The grain damage, un- threshed grain proportion, cleaning efficiencies and total grain loss varied from 0 to 0.973%, 0.62 to 1.953%, 92.79 to 99.74 % and 5.513 to 20.82 %, respectively. The threshing efficiency of the thresher was ranged from 87.21 to 89.13 per cent and increased as cylinder speed increased. The maximum threshing efficiency was at the cylinder speed of 500 rpm. This may be because of higher shearing action of the rasp bars with ear heads.
Abhishek and Stevens (2016): The evaluating of multi-crop thresher was conducted for Gram crop. The results concluded that: The optimum cylinder speed for threshing gram crop was found to be 600 rpm at feed rate 20 quintal /h. The threshing and cleaning efficiency were 98.98 percent, 97.30 %, respectively and grain loss 3.3 % and grain breakage were 1.70 % at above combination of speed and feed rate. The cost of threshing by multi crop thresher was found to be 46.14 Rs./quintal from crop
.and via compared between the threshing machine cost and traditional threshing method cost. Found that the net saving was
51.93 % for gram crop. It may be summarized that multi-crop thresher was more efficient, economical than traditional methods. Xia et al. (2018) designed and produce of a special thresher for pulses crops. Testing data showed that breaking rate and impurity content of the developed nail-tooth ype broad bean thresher machine were respectively 3.45 % and 1.09 %; it could improve the threshing process efficiency of the pulses crops significantly.
El-Morsy et al. (2019) developed and evaluated of a rubbing thresher for sunflower crop. The results showed that, the optimum conditions for threshing sunflower by the modified thresher were 10.12 m/s, 24 plates, 2.5 cm, and 11.28% w.b of drum speed, drum knife numbers, and moisture content, respectively.The objectives of this study were: (1) Modifying local thresher machine to fit threshing fenugreek crop., (2) Study some different operating factors affecting the threshing of fenugreek crop such as rotor speed, moisture content and feeding rate. And (3) Evaluate the modified thresher from the economic point of view.
MATERIALS AND METHODS
Field experiments were carried out during the growing season of 2022 at a private farm in Sharkia Governorate .This study was tested a local thresher to be suitable for threshing of fenugreek crop.
Materials:
-The utilized thresher machine: the local thresher (El-Shams) type, model tangential axial flow consists of parts as shown in fig. 1. It has gross dimensions 675 mm drum diameter, 1180 mm drum length, drum speed ranged from 450 to 850 rpm, number of spike tooth knives of 44 with 29 cm long and 0.8 cm thickness.
For modification local thresher some parts were fabricated to fit fenugreek seeds. 1- Changing the sieve under concave by another sieve of 2 mm holes diameter. 2- Replacing cleaning sieve by another with 3 mm holes diameter. This development aimed to increase the efficiency, reduce power requirements and minimizing the cost. The performance of the developed thresher will be influenced by drum speed, feeding rate and crop moisture content.
-Tractor: (Universal 650-M, Romania, Four-stroke diesel engine, 55.93 kW (75 Hp), and 1440 rpm) to operate the modified thresher by a pulley and belt.
No. | Part name | No. | Part name | No. | Part name | No. | Part name |
1 | Fan | 3 | Crop entry hole | 5 | Wheels | 7 | Sieves |
2 | Threshing drum | 4 | Cam for moving of sieve | 6 | Outlet of seeds | 8 | Outlet of hay |
Fig. 1: Schematic diagram for thresher.
-Fenugreek: local kind (Giza 2) was used in this study. The observed average mean value of fenugreek plant for length, stalk diameter, dry weight, number of pods /plant and number of seeds /pod were 597.15 mm, 3.56 mm, 12.26 g, 35 pods and 15 seeds, respectively. Fig.2 shows appearance of one of dry plant with pods and seeds. Physical and mechanical properties of seeds was measured and calculated according to Mohsinin, 1986. Fenugreek seed physical and mechanical properties are shown in table 1.
A
B
Fig.2: A. Photo for one of dry fenugreek plant with pods and B. fenugreek seeds
Table 1: Physical dimensions and mechanical properties of fenugreek seeds
Property | Mean value |
Moisture content (% w.b.) | 10.29 |
Length (mm) | 3.47 |
Width (mm) | 2.52 |
Thickness (mm) | 1.61 |
Arithmetic mean (mm) | 2.53 |
Geometric mean diameter (mm) | 2.41 |
Effective diameter (mm) | 1.69 |
Sphericity (%) | 0.70 |
Surface area(mm2) | 18.42 |
Volume(mm3) | 5.34 |
Hundred seeds mass (g) | 1.29 |
True density (kg m-3) | 1360.58 |
Bulk density (kg m-3) | 687.62 |
Porosity (%) | 49.39 |
-Stop watch: of 0.02 s. to record the threshing time.
-Tachometer: (Cole-Parmer 8204), ranged from 60 to 19999 rpm, resolution 1 rpm to calculate the rotating speed of drum.
-Electric balance: of 0.01 g as accuracy to estimate the seed losses.
-Electric oven: to estimate the moisture content. Field experiments
The machine was developed and tested at concave hole diameter of 10 mm, and tilt angle of threshing spikes of 90 0 on tangential axis for drum in threshing zone. Cleaning sieves under drum concave holes of 2 mm.
Variable parameters
- Four threshing drum speeds of 520, 580, 640 and 700 rpm or 18.37, 20.49, 22.61 and 24.73 m/s, respectively.
- Three feeding rates of 8, 10, and 10 kg/min, respectively.
- Three straw moisture content of 10.16, 12.54 and 14.87 % respectively.
Experimental measurements:
To study effect of the variable factors on threshing efficiency, the un-threshed seed losses, seed damage, power requirement and cost, the following measurements were carried.
-Threshing productivity:
Capacity is determined amount of seed crop, which threshed in time (Mg / h).
Mass of total sample before threshing Threshing productivity % = × 100 time of threshing
– Un-threshed seeds losses:
Un-threshed seeds losses were calculated as follows:
Wus
Un-threshed seeds losses % = × 100
WTs
Where: Wus is mass of un-threshed seeds, Mg and WTs is mass of total seeds, Mg
-Threshing efficiency:
Threshing efficiency and was calculated by the following formulas: Threshing efficiency % = (100 un-threshed seeds %)
-Seeds damage percentage:
The seeds damage percentage was determined as follows:
Wsd
Seeds damage % = × 100
WTs
Where: Wsd is mass of damaged seed, Mg and WTs is mass of total seed, Mg.
– Fan losses percentage:
Mass of fan seed loss
Fan losses % = × 100 Mass of total seeds
-Cleaning efficiency: Cleaning efficiency % = [ Total seed losses:
Total seed losses % = [seeds damage + Un-threshed seeds + fan losses]
- Fuel consumption:
Fuel consumption was estimated by measuring the volume-consumed fuel during threshing process.
- Required power:
The following equation was used to determine the required power (Embaby, 1985)
RP = 3.163 * fc (L/h). kW where RP is the required power, kW, fc is the fuel consumption.
- Specific energy: it can estimated by using the following formula: Required power (kW)
Specific energy = , (kW.h / ton)
Machine productivity (ton/h)
- Operational cost of threshing machine:
The hourly cost was estimated according to formula of (Awady, 1978) in the following form: C = P/h [1/a + i/2 + t + r] + (1.2 × w × f × s) + m/144
C = Hourly cost, L.E/h. | P = Price of machine, L.E. |
h = Yearly working hours, h/year. | a = Life expectancy of the machine, year. |
i = Interest rate/year. | F = Fuel price, L.E/l. |
t = Taxes, over heads ratio. | r = Repairs and maintenance ratio. |
m = Monthly average wage, L.E | 1.2 = Factor accounting for lubrications. |
W = Engine power, hp. | S = Specific fuel consumption, l/hp.h. |
144 = Reasonable estimation of monthly working hours. |
Where:
Operational cost can be determined using the following equation: Hourly cost (L.E/h)
Operational cost = , (L.E/ton)
Machine productivty (ton/h)
RESULTS AND DISCUSSION
- Effect of various operating parameters on threshing productivity:
Fig. 3 illustrates threshing productivity of fenugreek crops using different values of drum speed and feeding rate at different moisture content. The obtained results indicate that threshing productivity were increased by increasing the drum speed and feeding rate, and decreased by increasing the moisture content. Increasing the drum speed from 520 to 700 rpm, the threshing productivity increased from 0.51 to 0.64 Mg/h at feeding rate of 12 kg/min, and moisture content of 10.16 %.
The results showed that, the maximum threshing productivity value was 0.63 Mg/h, which obtained at 700 rpm of drum speed and 12 kg/min of feeding rate with 10.16 % of moisture content. Meanwhile, the minimum threshing productivity value was 0.34 Mg/h, which obtained at 520 rpm of drum speed and 8 kg/min of feeding rate with 14.87 % of moisture content.
This is due to increase the drum speed cause more cutting force and reduce threshing time, which leads to more force on threshed material.
Fig.3. Effect of drum speed, feeding rate and moisture content on threshing productivity.
2. EFFECT OF VARIOUS OPERATING PARAMETERS ON LOSSES:
There is relation between different parameter such as drum speed, feeding rate and moisture content and different losses kinds. The following data will explain this relation:
- 1.Un-threshed losses:
Data in Fig. 4 shows the effect of different factors on un-threshed losses, the un-threshed losses would be increased, if the moisture content increased and increased feeding rate but the un-threshed losses would be decreased, if the drum speed increased. By increasing the drum speed from 520 to 700 rpm, the un-threshed losses percent decreased from 3.64 to 2.90 % at feeding rate of 12 kg/min, and moisture content of 14.87 %.
The data show that, The highest value of un-threshed losses of 3.64 % was obtained at drum speed of 520 rpm, feeding rate of 12 kg/min, and moisture content of 14.87 %., respectively. Whereas the lowest value of 2.10 % was obtained at drum speed of 700 rpm, feeding rate of 8 kg/min, and moisture content of 10.16 %, respectively.
The high seed losses may be attributed to the excessive load of the threshed material on the shoe sieves. Excessive load occurred by decreasing drum speed which cause slow motion of the threshed material. Due slow motion some seeds which did not have the chance to go penetrate the threshed material layers and holes of the sieve.
Fig.4. Effect of drum speed, feeding rate and moisture content on un-threshed losses
2. 2.Seeds damage:
From the obtained data present in Fig.5, it is clear that seeds damage percentage affected on drum speed, feeding rate and moisture content. Seeds damage percentage increased by increasing drum speed and decreasing feeding rate. Meanwhile, seed damage decreased by increasing moisture content. Increasing the drum speed from 520 to 700 rpm, the seeds damage percent increased from 1.56 to 1.95 % at feeding rate of 12 kg/min, and moisture content of 14.87 %.
Fig.5. Effect of drum speed, feeding rate and moisture content on seed damage
2. 3. Fan losses:
The obtained data in Fig. 6 indicated that, a positive proportion was noticed between the fan losses and operating factors. The results show that, the fan losses increased by increasing drum speed, feeding rate and increasing moisture content. Increasing the drum speed from 520 to 700 rpm, the fan losses increased from 0.52 to 0.76 % at feeding rate of 8 kg/min, and moisture content of 10.16 %.
The data show that, The highest value of fan losses of 0.94 % was obtained at drum speed of 700 rpm, feeding rate of 12 kg/min, and moisture content of 14.87 %., respectively. Whereas the lowest value of 0.52 % was obtained at drum speed of 520 rpm, feeding rate of 8 kg/min, and moisture content of 10.16 %., respectively.
2. 4. Total seed losses:
Fig.6. Effect of drum speed, feeding rate and moisture content on fan losses
From the previous data and results obtained, the total seed losses including both un-threshed grain, seed damage and fan losses were illustrated in Fig.7.
The results showed that, the minimum total loss of 5.02 % is obtained at 700 rpm of drum speed and 8 kg/min of feeding rate with 10.16 % of moisture content. Meanwhile, the maximum total loss of 6.21 % was recorded at 580 rpm of drum speed and 12 kg/min of feeding rate with 14.87 % of moisture content.
Fig.7. Effect of drum speed, feeding rate and moisture content on total losses
- EFFECT OF VARIOUS OPERATING PARAMETERS ON THRESHING EFFICIENCY:
Figs. 8 indicate a clear increase in the values of threshing efficiency for fenugreek crop as the drum speed was increased.
Also, threshing efficiency increased by decreasing feeding rate and decreasing moisture content.
Increasing the drum speed from 520, 580, 640 to 700 rpm leads to increasing the threshing efficiency from 97.21, 97.43,
97.47 to 97.90 % at feeding rate of 8 kg/min, and moisture content of 10.16 %. The increase in the percentage of threshing efficiencies by increasing drum speed was attributed to the high stripping and impacting forces applied to the threshing materials (straw and seeds), which tend to improve the threshing operation and increase threshing efficiency.
Also, increasing the feeding rate from 8, 10 to 12 kg/min leads to decreasing the threshing efficiency from 97.90, 97.67 to 97.42 % at drum speed of 700 rpm, and moisture content of 10.16 %. Whereas, increasing the moisture content from 10.16,
12.45 to 14.87 % leads to decreasing the threshing efficiency from 97.90, 97.82 to 97.73 % at drum speed of 700 rpm, and
feeding rate of 8 kg/min. These results were attributed to the high elastic conditions with increasing moisture content, which tend to reduce the impacting force on the threshing materials.
Fig.8. Effect of drum speed, feeding rate and moisture content on threshing efficiency at LSD 0.05 = 0.0766
- EFFECT OF VARIOUS OPERATING PARAMETERS ON CLEANING EFFICIENCY:
Fig. 9 displays the relation between different operating parameters with cleaning efficiency for fenugreek seeds. Hence, it appears that the cleaning efficiency increased by decreasing feed rate, deceasing moisture content and increasing threshing drum speed. By increasing the drum speed from 520 to 700 rpm, the cleaning efficiency increased from 99.21 to 99.48 % at feeding rate of 8 kg/min, and moisture content of 10.16 %. On the other side increasing the feeding rate from 8 to 12 kg/min at drum speed of 520 rpm and moisture content of 10.16 %, the cleaning efficiency decreased from 99.21 to 99.14 %. Whereas, increasing the moisture content from 10.16 to 14.87 % leads to decreasing the cleaning efficiency from 99.21 to 99.15 % at drum speed of 520 rpm, and feeding rate of 8 kg/min.
The results showed that, the maximum cleaning efficiency of 99.48 % was recorded at 700 rpm of drum speed and 8 kg/min of feeding rate with 10.16 % of moisture content.
Fig.9. Effect of drum speed, feeding rate and moisture content on cleaning efficiency
- EFFECT OF VARIOUS OPERATING PARAMETERS ON SPECIFIC ENERGY:
Specific Energy for threshing fenugreek plants depending on some variables as drum speed, feeding rate and moisture content. Fig (10) shows the relation between drum speed, feed rate and moisture content with specific energy. Increasing feed rate from 8 to 12 kg/h at drum speed of 700 m/s and moisture content of 10.16 % the specific energy decreased from 28.31 to 21.70kW.h/ton.
On the other side increasing the drum speed from 520 to 700 kg/min at feeding rate of 12 kg/min and moisture content of
10.16 %, the specific energy decreased from 24.87 to 21.70kW.h/ton. Whereas, increasing the moisture content from 10.16 to
14.87 % leads to increasing the specific energy from 21.70 to 25.02kW.h/ton at drum speed of 700 rpm, and feeding rate of 12 kg/min. This increase was due to elastic condition of the threshing materials at high moisture content of plants, which need more force more fuel consumption and specific energy.
Fig.10. Effect of drum speed, feeding rate and moisture content on specific energy
- EFFECT OF VARIOUS OPERATING PARAMETERS ON OPERATIONAL COST:
The data presented in Table 2 cleared that the operational cost values decreased by increasing drum speed and feeding rate. That is because of increasing the threshing productivity by increasing the drum speed and increasing feeding rate. The results revealed also that, the operational cost values for fenugreek increased by increasing moisture content. This attributed to increase the threshing losses and decreasing threshing productivity.
The results show that, the lowest values of the operational cost were 145.61, 124.25 and 111.63 LE/Mg respectively, which obtained at drum speed of 700 rpm, moisture content of 10.16 %, and feeding rate of 8, 10 and 12 kg/min, respectively. In addition to, the highest values of the operational cost were 204.35, 173.10 and 152.26 LE/Mg respectively, which obtained at drum speed of 520 rpm, moisture content of 14.87 %, and feeding rate of 8, 10 and 12 kg/min, respectively.
Table 2: Effect of various operating parameters on operational cost:
Drum speed, rpm | Operational cost, L.E/Mg | ||||||||
Moisture content =10.16% | Moisture content =12.45% | Moisture content =14.87% | |||||||
Feeding rate, kg/min | Feeding rate, kg/min | Feeding rate, kg/min | |||||||
8 | 10 | 12 | 8 | 10 | 12 | 8 | 10 | 12 | |
520 | 176.91 | 154.74 | 133.67 | 190.52 | 165.75 | 141.30 | 204.35 | 173.10 | 152.26 |
580 | 172.28 | 146.82 | 129.21 | 181.33 | 152.80 | 133.78 | 197.85 | 166.10 | 148.19 |
640 | 159.42 | 142.99 | 117.55 | 175.87 | 144.60 | 123.76 | 180.30 | 154.12 | 133.37 |
700 | 145.61 | 124.25 | 111.63 | 154.74 | 131.65 | 114.62 | 166.54 | 143.17 | 124.28 |
CONCLUSION
It is concluded that the optimum conditions for threshing of fenugreek crop by using the modified thresher are the following: Drum speed of 640 rpm, Feeding rate 12 kg/min, and Straw moisture content 10.16%.
The obtained results at optimum conditions were: threshing productivity of 0.59 Mg/h, total losses 5.67 %, and threshing efficiency of 96.89 %, cleaning efficiency 99.33 %, specific energy of 22.69 kW h/Mg and operational cost of 117.55 L.E/Mg.
REFERRENCES
[1] Abhishek Pandey and R. M. Stevens (2016): Performance evaluation of high capacity multi crop thresher on gram crop. International Journal of Agricultural Engineering. Vol. (9), Issue 1, April 2016, 94-101. [2] Acharya, S., Thomas, J., Basu, S., 2008. Fenugreek, an alternative crop for semiarid regions of North America. Crop Sci. (3): 841853. [3] Afify M. K., M. M. A. El-Sharabasy and M. M. A. Ali (2007) Development of a Local Threshing Machine Suits for Threshing Black Seed (Nigella sativa). Misr J. Ag. Eng., 24(4): 699-724. [4] Ajav, E.A. and B.A. Adejumo (2005): Performance evaluation of an okra thresher. Agr. Eng. International: the CIGR Journal. Manuscript PM 04006 Vol. VII. October. [5] Altuntas, E., Ozgoz, E., Taser, O.F. (2005) Some physical properties of fenugreek (Trigonella foenum-graceum L.) seeds. Journal of food engineering. 71(2005): 37-43. [6] Askari Asli-Ardeh, E.; S. Sabori and M.R. Alizadeh (2008): Effect of peripheral speed of cylinder and crop moisture on threshing losses of various rice varieties. Iranian Journal of Agricultural and Natural Resources Sciences. 12(44): 223- 231. [7] Awady, M.N. (1978) Tractor and farm machinery. Text Book, Fac. Of Agric., Ain-shams University, 164-167. [8] Ebaid, M. T; A. A. Abd El-Rahman, G. G. Radwan and H. E. Osman (2004): Development of a thresher for wheat of beater type for maximum productivity. Misr J. Ag. Eng. , 21 (1):14 28. [9] El-Hadad, W.Z. (2000): A simplified design and performance study of threshing and winnowing machine suitable for small holdings. M. Sc. Thesis.Agric. Mech., Fac. Of Agric., Kafr El-Sheikh, Tanta Univ.
[10] El-Morsy, H. E. 1; A. S. El-Ashr and A. A. El-Kfrawy (2019) Development and performance evaluation of a rubbing Thresher for sunflower crop.J.Soil Sci. and Agric. Eng., Mansoura Univ., Vol. 10 (1): 61- 67.
[11] Embaby, A. T. (1985) “A comparison of different mechanization system for cereal crop production” M. Sc. Thesis, (Ag. Eng.,) Cairo Univ. [12] Flammang, A., Cifone, M., Erexson, G., Stankowski, L., (2004) Genotoxicity testing of a fenugreek extract. Food Chem. Toxicol, 11: 1769-1775. [13] Gomez K. A. and Gomez A. A. (1984). Statistical Procedures for Agricultural Research. John Wiley & Sons, New York, USA, 680 p. [14] Ismail Z.E. and M.N. Elhenaway (2009): Optimization of machine parameters for sunflowers thresher using friction drum. J. Agric. Sci. Mansoura Univ., 34 (10):10293-10304. [15] Karthik, S. K., Satishkumar and Basavaraj (2015) Development and performance evaluation of multi crop thresher, International Journal of Agricultural Science and Research (IJASR) Vol. 5, Issue 5, Oct 2015, 313-322. [16] Khater, A.E.A. (2000): Mechanization of sunflower threshing. M.Sc. thesis Agr. Mech. Dept. Fac. Of Agr. Mansoura Univ. pp: 86. [17] Krishnaswamy, K. (2008) Traditional Indian spices and their health significance. Asia Pacific journalof clinical nutrition, 17(S1): 265-268. [18] Meghwal, M., Goswami, T.K. (2012) A review on the functionalproperties, nutritional content, medicinal utilization and potentialapplication of fenugreek. J. Food Process Technol. 3. http://dx.doi.org/10.4172/2157-7110.1000181. [19] Mohsenin, N.N. (1986), Physical properties of plant and animal materials, Gordon and Breach Sc. Pub., New York: 25-33. [20] Petropoulos, G.A. (2002) Fenugreek- the Genus Trigonella. Taylor and Francis, London and NewYork, Pages: 200. [21] Simonyan K. J. and K. C. Oni (2001): Performance evaluation of a motorized locust bean decorticator. Journal of Agricultural Technology 9(1): 55 – 65. [22] Statistics Book (2018) Ministry of Agricultural and land reclamation, Medicinal and Aromatic Plants Research Department, Horticulture Research Institute, Agricultural Research Center. [23] Xia, X., Chen, Q., H. Xiao and G. Yang (2018) Design and trial-produce of a special nail-tooth thresher for pulses crops MATEC Web of Conferences 242, 01019, https://doi.org/10.1051/matecconf/201824201019. [24] Zakaria, M. I. (2006): Modification of the thresher drum of stationary thresher to suit separating of flax crop. Misr J. Ag. Eng., 23(2): 324-345. [25] Zaky, W. M. (2006): Engineering studies on threshing of black seed (NigellaSativa). M. Sc. Thesis. Agric. Eng. Dep., Fac. of Agric., Mansoura Univ.