
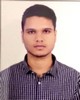
- Open Access
- Authors : Prashanth S , Adithya L R , Adithya Harithas V , Amoghavarsha K P
- Paper ID : IJERTV10IS030218
- Volume & Issue : Volume 10, Issue 03 (March 2021)
- Published (First Online): 01-04-2021
- ISSN (Online) : 2278-0181
- Publisher Name : IJERT
- License:
This work is licensed under a Creative Commons Attribution 4.0 International License
Development of an Algorithm to Obtain the Mode Shapes of a Cantilever Beam Experimentally
Adithya L R
Mechanical Engineering
The National Institute of Engineering Mysore, India
Adithya Harithas V
Mechanical Engineering
The National Institute of Engineering Mysore, India
Abstract- Free vibration takes place when a system oscillates due to initial disturbance only. The system under free vibration will vibrate at one or more of its natural frequencies and when the applied frequency matches this frequency, Resonance occurs[1]. Resonance is a phenomenon in which a vibrating system or external force drives another system to oscillate with greater amplitude. Also, by knowing the shape that the beam attains during these natural frequencies, the systems could be designed to avoid the failure of the components of the beam by resonance[5].
Each and every product is subjected to vibrations during manufacturing and transportation. So, they must be subjected to vibrational analysis to prevent the failure of those systems. In this paper, an Algorithm has been developed to find the natural frequencies and the mode shapes of a cantilever beam by experimental method making use of the Accelerometer, Data Acquisition systems and the computer software such as LABVIEW and MATLAB. The results obtained are compared with the Analytical and Numerical methods.
Keywords: Free Vibration, Natural Frequency, Resonance, LABVIEW, MATLAB.
-
INTRODUCTION
In analytical methods of vibration analysis, the data values could be directly substituted in the formulas[2] to obtain the natural frequency and the mode shapes can be plotted with the help of trigonometric equations. But these are not accurate because of the inherent assumptions made. Also, these methods do not consider other external parameters which act as extraneous variables in determination of natural frequency and mode shapes. There also arises difficulty if the component under test is of variable cross section and made up of different materials. So, in these cases it is better to adopt experimental method of vibration analysis. The conventional experimental method is of prime mover type where in the component to be tested is connected to a prime mover like motor or shaker table and the natural frequencies and mode shapes are found out. In recent times computer and smart system are used everywhere for analysis and other computational purposes. So an experimental set up and an algorithm has been
Prashanth S
Mechanical Engineering
The National Institute of Engineering Mysore, India
Amoghavarsha K P
Mechanical Engineering
The National Institute of Engineering Mysore, India
developed in this paper by using computer system and software for vibrational analysis.
A general experimental modal analysis system consists of:
-
Exciter: It is used for producing the required displacement.
-
Transducer (Accelerometer): It converts the physical movement (acceleration) into voltage.
-
Signal Conditioner (DAQ assist): The signal coming out of the transducer is not strong enough for input into analysis. So, signal conditioner is used for strengthening the signal.
-
Analyzer (LABVIEW software): The type of analyzer used is Fast Fourier Transform (FFT). This is used to convert the time domain amplitude to frequency domain. Thus, the frequencies at which the peak amplitudes are produced can be easily found.
Data obtained from the analyzer is later post- processed in MATLAB to obtain natural frequencies and mode shapes of first and second modes.
-
-
OBJECTIVE
To find out the natural frequency of a system, various theories have been proposed such as Euler-Bernoullis beam theory and Timoshenko theory. Also, various softwares such as ANSYS and Hyperworks have been developed to carry out the modal analysis. The values of natural frequencies obtained from these methods cannot be taken for practical design because theories proposed contain a lot of assumptions that are hard to realize. The numerical methods use truncated partial differential equations which results in adding lot of errors. So, finding the natural frequencies from experimental methods are very important and it is an emerging area in modal analysis.
It is important to know the mode shapes of a component especially when it is being designed to stay inside another hollow component. For example, consider a gear box. It consists of gears and shafts inside the casing. To design the casing efficiently, the designer should be aware of the different mode shapes of the components inside. So, the designer can accommodate space in the casing for the gears not just in the static conditions but also during resonance.
To carryout vibration analysis for cantilever beam using three methods: analytical, experimental and numerical methods.
To find the natural frequencies and the first two mode shapes of a cantilever beam and compare among the three methods.
Experimental method:
-
To do the experimental setup of the cantilever beam and dividing it into required number of nodes
-
Acquiring the acceleration and corresponding frequency signals by placing the accelerometer on the beam and making the beam to vibrate.
-
To analyse the frequency data using LABVIEW software and to find natural frequencies
-
To develop a code in MATLAB to plot the mode shapes at first two natural frequencies
-
-
LITERATURE REVIEW
Vibrational analysis of cantilever beam[3]: an experimental study : Mr. P. Kumar, Dr.S. Bhaduri, In this paper the natural frequencies of two different cantilever beams made of Aluminium and Iron are measured experimentally with and without the presence of end masses. The finite element analysis is done using the developed codes in MATLAB and also by ANSYS software. Experimental setup consists of FFT analyser with computer and its accessories. For further analysis of the effect of different end masses on the natural frequency of cantilever beam, free end of cantilever is loaded with different masses along with accelerometer and the result of this experiment is observed on the computer screen for the aluminium and iron beams. Then the author has concluded that numerical and experimental results are comparable.
An experimental approach to free vibration analysis of smart composite beam[4]: G A Yashavantha Kumar and K M Sathish Kumar, the numerical study of the free vibration analysis of the smart composite beam by using the ANSYS is explained in this paper. Here the author has conducted the analysis on composite beam made up of glass epoxy and PZT patches are added on the surface of the beam. Then the vibration analysis is carried out under the clamped-free condition of the beam.
From literature survey it is concluded that all the works are concentrated on finding natural frequencies only. But while designing the whole system, mode shapes of a component plays a major role. So in this work first and second mode shapes of a cantilever beam has been found out by experimental method along with the natural frequency.
-
METHODOLOGY ADOPTED
The methodology adopted for the experiment is as shown in the figure.
The experimental set up consists of aluminium 6061 cantilever beam(380mm*21mm*3mm) fixed at one end to the support. The cantilever beam is divided into 14 nodes with 2.5 cm as distance between two successive nodes.
The NI 356A15 Tri axial Accelerometer[6] is mounted on one the nodes on the beam. The accelerometer is connected to te NI 9234 DAQ module which is in turn connected to the NI 9178 DAQ chassis. The system is powered through DAQ chassis. DAQ chassis is interfaced with the computer system which is having LABVIEW software.
Acquisition of vibrational data at different nodes in the LABVIEW software
Acquisition of vibrational data at different nodes in the LABVIEW software
Acquiring Frequency domain data
Acquiring Frequency domain data
Experimental setup with cantilever beam, accelerometer and NI DAQ
Excitation of beam by releasing it from extreme end position of set amplitude
Excitation of beam by releasing it from extreme end position of set amplitude
Analysis of data in MATLAB to obtain mode shapes
Analysis of data in MATLAB to obtain mode shapes
Fig. 1. Experimental Set Up
The initial excitation is given to the beam by press- releasing it from a certain extreme position. The acceleration and time data are collected from the accelerometer. It is made sure that the extreme position of release remains the same for every position of the accelerometer on the beam. Hence, the excitation remains the same for each node. The time domain acceleration data thus collected from accelerometer is passed to the DAQ module where signal conditioning occurs. This conditioned signal is analyzed in LABVIEW software.
In the LABVIEW software the type of input is selected as acceleration. A while loop is created and inside this while loop a data assist block which represents the DAQ module is taken. Signal coming out of DAQ assist is in the form of time domain signal and has to be converted into frequency domain signal. So a spectral analysis block is placed and the input is given in the form of time domain signal. the spectral analyzer uses FFT operation and converts time domain to frequency domain signal. This frequency and acceleration data is later used for post processing in MATLAB. The frequency domain data for all 14 nodes is acquired and stored as separate files in the system.
-
POST PROCESSING MATLAB.
The frequency response curve for each node of the beam is obtained by plotting graph of frequency and acceleration data with acceleration on Y-axis and frequency on X-axis. The graphs show the frequency response curve for 13th and 14th nodes.
Fig. 2. Frequency Response curve for 14th node (Y axis: acceleration in g; X-axis: frequency in Hz)
Fig. 3. Frequency response curve for 13th node
The figures show the frequency response curves generated for the thirteenth and the fourteenth nodes. It can be observed that the values of first and the second natural frequencies for both 13th and the 14th nodes are same whereas the acceleration values reached at those natural
frequencies change. Similar graphs are obtained for all the other nodes with same natural frequency but different acceleration values at those frequencies.
The first five natural frequencies and acceleration values corresponding to those natural frequencies are extracted using the following MATLAB code.
Fig. 4. MATLAB code to get natural frequencies and acceleration
The similar code is used for all the nodes to extract frequency and acceleration values. These extracted values are clubbed together in two matrices with one matrix storing amplitudes and another storing the frequency values.
Fig. 5. Code to generate Acceleration matrix for all the nodes at first 5 Natural frequencies
In the acceleration matrix(14*5) the rows represent the acceleration values at the nodes and columns represent the natural frequencies. These values along particular column are plotted against nodal distance to obtain the mode shape at that particular frequency.
-
RESULTS
By executing the MATLAB codes as explained in the previous the following mode shapes were obtained for first
and second modes of a cantilever beam.
Fig. 6. First Mode Shape of the Cantilever Beam by Experimental Method
Fig. 7. Second mode shape of the Cantilever Beam by Experimental Method
From the figures, it can be observed that the graph is not smooth. This could be because of consideration of only 14 nodes. Since the beam is a continuous beam, the number of nodes that has to be taken to get accurate mode shape will be infinity.
Therefore, in order to obtain a smooth curve, these mode shapes were subjected to curve smoothing by polyfit using the code shown in the figure
Fig. 8. Code for Curve smoothing of the mode shapes
Here, the polyfit is a pre-defined function in MATLAB. X represents the nodal distances to be plotted along x-axis. y(:,2) represents the acceleration values of all rows (14 nodes) at second column (or) the second natural frequency. 3 in the third line represents the order of the equation to
which polyfit function is subjected to. Since the interpolation model of a cantilever beam is a third degree polynomial, mode shapes also occur as a third degree polynomial curve. So, polyfit function for 3rd degree polynomial equation is used. After the first and second mode shapes (figures) are polyfit, the following smooth curves are obtained (figures). The figures show that, the mode shapes which had many small intermediate peaks has been smoothened out.
Fig. 9. First mode shape by experimental method after curve smoothing
Fig. 10. Second mode shape by Experimental method after curve smoothing
-
CONCLUSION
The analytical and numerical analysis were also conducted and the results are compared with the experimental method.
Table Natural frequencies comparison
Mode No |
Analytical Method (Hz) |
Experimental Method (Hz) |
Numerical Method (Hz) |
1 |
16.8692 |
15 |
16.014 |
2 |
105.7253 |
110 |
104.1 |
It can be observed that the frequency obtained for modes 1 and 2 from the experimental method is in good agreement with the analytical method. The numerical method values can be validated with the experimental and analytical methods.
Fig. 11. First mode shape obtained from analytical method
Fig. 12. Second mode shape obtained from analytical method
Fig. 13. First m ode shape obtained from ANSYS
Fig. 14. Second mode shape obtained from ANSYS
Fig. 15. First mode shape obtained from experimental method
Fig. 16. Second mode shape obtained from experimental method
It can be observed that there is small variation in mode shapes when compared amongst experimental, analytical and numerical methods. This is because of the following reasons:
-
Experimental errors occur while conducting the experiment
-
The fixed condition for cantilever beam while conducting the experiment will be affected by the support, that will in turn affect the mode shapes obtained experimentally
REFERENCES
-
Mechanical Vibrations vol.II, by G.K.Grover
-
Mechanical Vibration, by V.P.Singh
-
Mr. P. Kumar, Dr.S. Bhaduri, Vibrational analysis of cantilever beam: an experimental study
-
G A Yashavantha Kumar and K M Sathish Kumar, An experimental approach to free vibration analysis of smart composite beam
-
Kotambkar, Effect of mass attachment on natural frequency of free-free beam: Analytical, numerical and experimental investigation
-
Measuring vibration with Accelerometers, an article by National Instruments.