
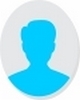
- Open Access
- Authors : Wen-Chih Yang , Kuan-Yi Lee , Jhih-Yun Tien , Lo-Tung Chen
- Paper ID : IJERTV11IS120101
- Volume & Issue : Volume 11, Issue 12 (December 2022)
- Published (First Online): 26-12-2022
- ISSN (Online) : 2278-0181
- Publisher Name : IJERT
- License:
This work is licensed under a Creative Commons Attribution 4.0 International License
Development of An Integrated Circuits for Non-Isolated DC-DC Converters
Wen-Chih Yang, Kuan-Yi Lee, Jhih-Yun Tien, Lo-Tung Chen
Department of Electrical Engineering Taipei City University of Science and Technology
Taiwan, R.O.C.
SW1
AbstractNon-isolated buck circuit, boost circuit, buck/boost circuit and Cuk circuit are important basic circuits of DC-DC converters. An integrated circuit of these four circuits has been developed and presented in this paper. The integrated circuit was developed according to the rules of thumb. It can be applied to energy storage systems, uninterruptible power
the integrated circuit can become a buck circuit, a boost circuit, a buck/boost circuit or a Cuk circuit. Moreover, an N-channel MOSFET Q1 is used as an electronic switch to change the charge and discharge state of the inductors. The control rules are described as follows.
systems and charging systems to improve the application flexibility of these systems.
KeywordsBuck circuit, boost circuit, DC-DC converter.
INTRODUCTION
Non-isolated DC-DC converters are commonly used power converters in the industry [1]. They can change the
+
Vin
–
SW2
L1
SW8
to driver
Q1 SW3
C1 L2
SW4
SW5
SW6
SW9
SW7
SW10
D1
SW13
SW12
SW11
C2
+
Vout
–
level of DC voltage according to the needs of users and provide qualified DC power to the loads [2]. Non-isolated DC-DC converters include four circuits, namely buck circuit, boost circuit, buck/boost circuit and Cuk circuit, where the buck circuit is used to reduce the level of the input voltage, the boost circuit is used to increase the level of the input voltage, the buck/boost circuit is used to reduce or increase the level of the input voltage, and the Cuk circuit is an improved circuit of the buck/boost circuit, which can also be used to reduce or increase the level of the input voltage [3,4].
Fig. 1. The topoloy of the developed integrated circuit.
-
Buck mode
The microcontroller changes the original states of realys SW1, SW2, SW3, SW7, SW8, SW9 and SW10 and keeps the original states of other realys, then the topology of the integrated circuit becomes a buck circuit, as shown in Fig. 2. The output voltage of this buck circuit is shown in formula (1).The output voltage is lower than the input voltage when the duty cycle D is less than 100%.
Non-isolated DC-DC converters are widely used in industrial products due to their simple topologies and stable performance. However, with the progress of the times, the application of energy storage systems, uninterruptible power systems, and charging systems has become more and more popular [5,6]. The topologies of conventional non-isolated DC-DC converters lacks the flexibility to change, making it
+
Vin
–
Q1 L2
to driver D1
+
C1 Vout
–
difficult to meet the needs of the industry.
For this reason, an integrated circuit of non-isolated DC-
Fig. 2. The topology of the buck circuit changed from the integrated circuit.
Fig. 3.
DC converters was developed and presented here. The integrated circuit was developed using rules of thumb. It has the function of variable topology. Users can obtain the topology of a buck, a boost, a buck/boost or a Cuk circuit through the control of switches. The integrated circuit has the flexibility of variable topology and then can meet the needs of the storage systems, uninterruptible power systems, and
Vout D Vin
Where
Vin is the input voltage; Vout is the output voltage; D is the duty cycle.
-
Boost mode
(1)
charging systems.
CIRCUIT DESIGN
The microcontroller changes the original states of realys
SW4, SW5, SW8, SW9, SW11 and SW12 and keeps the original states of other realys, then the topology of the integrated
The topology of the developed integrated circuit is shown
in Fig. 2. The topology includes the circuits of a buck converter, a boost converter, a buck/boost converter and a Cuk converter. There are thirteen switches, named SW1 to SW13, in the integrated circuit. Every relay has a normally closed contact and a normally open contact. The thirteen relays can be used to change the topology of the integrated circuit, so that
circuit becomes a boost circuit, as shown in Fig. 3. The output voltage of this boost circuit is shown in formula (2), and the output voltage is lower than the input voltage when the duty cycle D is greater than 0%.
L1 D1
+
Input voltage
+
Output voltage
Vin Q1
–
to
driver
C1 Vout
–
Voltage
sensor
The integrated circuit
Voltage
sensor
Fig. 4. The topology of the boost circuit changed from the integrated circuit.
A/D
MOSFET
Realy
A/D
1
V V
(2)
converter
driver
drivers
converter
out
1 D in
-
Buck/Boost mode
The microcontroller changes the original states of realys SW1, SW2, SW3, SW6, SW8, SW9, SW10, SW12 and SW13 and
keeps the original states of other realys, then the topology of the integrated circuit becomes a buck/boost circuit, as shown in Fig. 4. The output voltage of this buck/boost circuit is shown in formula (3). The output voltage is lower than the input voltage when the duty cycle D is less than 50%, and the output voltage is greater than the input voltage when the duty cycle D is greater than 50%.
Microcomputer
Fig. 7. The functional block diagram of the developed integrated circuit.
Fig. 7 shows the prototype of the developed integrated circuit. The microcontroller used by this research is a STM32 chip. The MOSFET Q1 is an N channel NexFET power MOSFET. The MOSFET driver is LM5106MM. The realys are G6S-2 and the relay drivers are NPN transistors S8050.
+
Vin
–
Q1 D1
to L1
driver
–
C1 Vout
+
Fig. 5. The topology of the buck/boost circuit changed from the integrated circuit.
D
V V
(3)
out
1 D in
-
Cuk mode
The microcontroller keeps the original states of all realys, then the topology of the integrated circuit is a Cuk circuit, as shown in Fig. 5. The characteristics of the Cuk circuit are the same as that of the buck/boost circuit, so its output voltage is also the formula (3). The output voltage is lower than the input voltage when the duty cycle D is less than 50%, and the output voltage is greater than the input voltage when the duty cycle D is greater than 50%.
Fig. 8. A photo of the physical circuit of the developed integrated circuit.
In order to examine the performance of the developed integrated circuit, four test cases were carried out in this research. The test conditions and test results are explained as follows.
+
Vin
–
L1
to
driver
C1 L2
Q1 D1 C2
–
Vout
+
-
Buck mode
When the microcontroller drives relays SW1, SW2, SW3, SW7, SW8, SW9 and SW10 to the normally open state and drives the relays SW4, SW5, SW6, SW11, SW12 and SW13 to the normally cloased state, the integrated circuit enters the buck mode. At this test case, the microcontroller sent a PWM signal to the MOSFET Q1. The frequency of the PWM signal
Fig. 6. The topology of the Cuk circuit changed from the integrated circuit.
PERFORMANCE TEST
Fig. 6 shows the functional block diagram of the developed integrated circuit for testing. The relay drivers are used to drive the relays SW1 to SW13. The MOSFET driver is used to drive the MOSFET Q1.
was 150kHz and the duty cycle is 37.5%. The test results of the developed integrated circuit are shown in Fig. 8. The input voltage of the developed integrated circuit was 19.2V and the output voltage was 6.44V. The output voltage was indeed less than the input voltage.The integrated circuit therefore did work in buck mode.
Fig. 9. The test results of the integrated circuit working in buck mode.
-
Boost mode
When the microcontroller drives relays SW4, SW5, SW8, SW9, SW11 and SW12 to the normally open state and drives the relays SW1, SW2, SW3, SW6, SW7, SW10 and SW13 to the normally cloased state, the integrated circuit enters the boost mode. At this test case, the microcontroller sent a PWM signal to the electronic switch Q1. The frequency of the PWM signal was 150kHz and the duty cycle is 16.9%. The test results of the developed integrated circuit are shown in Fig. 9. The input voltage of the developed integrated circuit was 5.6V and the output voltage was 16.4V. The output voltage was indeed greater than the input voltage.The integrated circuit therefore did work in boost mode.
in Fig. 11. The input voltage of the developed integrated circuit was 5.4V and the output voltage was 55.1V. The output voltage was indeed greater than the input voltage.The integrated circuit therefore did work in boost mode.
Fig. 11. The test results of the integrated circuit working in buck mode of the
buck/boost mode.
Fig. 12. The test results of the integrated circuit working in boost mode of the
buck/boost mode.
Fig. 10. The test results of the integrated circuit working in boost mode.
-
Buck/Boost mode
When the microcontroller drives relays SW1, SW2, SW3, SW6, SW8, SW9, SW10, SW12 and SW13 to the normally open state and drives the relays SW4, SW5, SW7 and SW11 to the normally cloased state, the integrated circuit enters the boost mode. This test case contains two sub-cases. In the first sub- case, the microcontroller sent a PWM signal to the electronic switch Q1. The frequency of the PWM signal was 150kHz and the duty cycle is 24.1%. The test results of the developed integrated circuit are shown in Fig. 10. The input voltage of the developed integrated circuit was 24.5V and the output voltage was 9.6V. The output voltage was indeed less than the input voltage.The integrated circuit therefore did work in buck mode. In the second sub-case, the microcontroller still sent the same PWM signal to the electronic switch Q1. The frequency of the PWM signal was 150kHz and the duty cycle is 65.3%. The test results of the developed integrated circuit are shown
-
Cuk mode
-
When the microcontroller keeps all relaysin the normally cloased state, the integrated circuit enters the Cuk mode. This test case also contains two sub-cases. In the first sub-case, the microcontroller sent a PWM signal to the electronic switch Q1. The frequency of the PWM signal was 150kHz and the duty cycle is 16.87%. The test results of the developed integrated circuit are shown in Fig. 12. The input voltage of the developed integrated circuit was 5.63V and the output voltage was 2.18V. The output voltage was indeed less than the input voltage.The integrated circuit therefore did work in buck mode. In the second sub-case, the microcontroller still sent the same PWM signal to the electronic switch Q1. The frequency of the PWM signal was 150kHz and the duty cycle is 60.68%. The test results of the developed integrated circuit are shown in Fig. 13. The input voltage of the developed integrated circuit was 5.72V and the output voltage was 16.8V. The output voltage was indeed greater than the input voltage.The integrated circuit therefore did work in boost mode.
Fig. 13. The test results of the integrated circuit working in buck mode of the
Cuk mode.
Fig. 14. The test results of the integrated circuit working in boost mode of the
Cuk mode.
CONCLUSIONS
In recent years, the use of energy storage systems, uninterruptible power systems and charging systems has become more and more common [7]. Energy storage systems, uninterruptible power systems and charging systems must use
DC-DC converters to convert voltage levels in order to provide qualified power for loads. Since there are various types of DC-DC converters, it causes a lot of inconvenience in manufacture and application [8].
This research has developed an integrated circuits of four non-isolated DC-DC converters based on the rules of thumb. The developed integrated circuit can provide the power conversion function of buck mode, boost mode, buck/boost mode or Cuk mode according to the needs of users. The developed integrated circuit has the function of variable topology. It is very convenient to use and can improve the application flexibility of the non-isolated DC-DC converters.
REFERENCES
[1] A. Rufer and P. Barrade, Non-Isolated DC-DC Converters for High Power Applications – Control of the Capacitive Voltage Divider, International Exhibition and Conference for Power Electronics, Intelligent Motion, Renewable Energy and Energy Management, pp. 1- 5, May 2014. [2] A. Alzahrani, P. Shamsi and M. Ferdowsi, A novel non-isolated high- gain dc-dc boost converter, IEEE North American Power Symposium (NAPS), pp. 1-6, September 2017. [3] R. Marius, Z. Ping, L. Dinsheng, I. Dan and P. Mircea, Multiphysics Simulation by Design for Electrical Machines, Power Electronics and Drives, Wiley-IEEE Press: Newyork, 2017, pp.253-263. [4] D. W. Hart, Power Electronics, McGraw-Hill Education: Newyork, 2010, pp.287-290. [5] M. Prudente, L. L. Pfitscher, G. Emmendoerfer, E. F. Romaneli and R. Gules, Voltage Multiplier Cells Applied to Non-Isolated DCDC Converters, IEEE Transactions on Power Electronics, vol. 23, issue. 2, pp. 871 – 887, March 2008. [6] G. J. Kish, On the Emerging Class of Non-Isolated Modular Multilevel DCDC Converters for DC and Hybrid ACDC Systems, IEEE Transactions on Smart Grid, vol. 10, issue. 2, pp. 1762 – 1771,March 2019.
[7] G. Dileep and S. N. Singhb, Selection of non-isolated DC-DC converters for solar photovoltaic system, ELSEIVER Renewable and Sustainable Energy Reviews, vol. 76, pp. 1230-1247, September 2017. [8] M. H. Taghvaee, M. A. M. Radzi, S. M. Moosavain, H. Hizam, M. H. Marhaban, A current and future study on non-isolated DCDC converters for photovoltaic applications, ELSEIVER Renewable and Sustainable Energy Reviews, vol. 17, pp. 216-227, January 2013.