
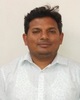
- Open Access
- Authors : Dhruv Panchal , Nidhish Patel , Jaykant Patel , Nirmal Patel, Jignesh Patel
- Paper ID : IJERTV9IS070260
- Volume & Issue : Volume 09, Issue 07 (July 2020)
- Published (First Online): 15-07-2020
- ISSN (Online) : 2278-0181
- Publisher Name : IJERT
- License:
This work is licensed under a Creative Commons Attribution 4.0 International License
Development of Mechanism for Frictional Stir Welding of Cylindrical Pipes
Prof. Jignesh Patel1, Nidhish Patel2, Dhruv Panchal3, Nirmal Patel4, Jaykant Patel5 1Professor,Department of Mechanical Engineering, Indus Institute of Technology and Engineering, Ahmedabad ,Gujarat, India
2, 3,4,5 UG Student, Department of Mechanical Engineering, Indus Institute of Technology and Engineering, Ahmedabad, Gujarat, India
Abstract – In Friction Stir Welding (FSW) process, there is a substantial amount of research done on aluminum plate but very few are found for aluminum pipe due to its tubular shape. A specially customized Orbital Clamping Unit (OCU) was used and fixed on the drilling machine in order to weld an aluminum alloy 6063 pipe butt joint at several welding parameters. This OCU will hold the work pieces together tightly, rotate them at the required constant low speed, and ensure easy removal. This paper will investigate the effect of welding parameters on the tensile strength of joint produced by the FSW process. Several good samples of pipes joint were produced using the present experiment setting.
-
INTRODUCTION
The Friction Stir Welding (FSW) is the state-of-the art joining process which was invented and later patented by The Welding Institute (TWI) in 1991. This is a solid- state joining process which uses heat from frictional work to soften and join the material together through stirring process. This welding technique provides many advantages such as it produces no fumes, no arc and requires no filler metal. Thus, this process can be regarded as an environmental-friendly process. However, the experiment setting is the most critical part in this process especially for joining aluminum alloy 6063 pipes. Good samples are needed before tensile testing. The Orbital Clamping Unit (OCU) was developed and fixed on the drilling machine. This OCU will hold the pipes together tightly, rotate them at required constant low speed, and ensure easy removal. This paper will study the effect of welding parameters on the tensile strength of the friction stir welded aluminum alloy 6063 pipe butt joint. FSW trials were carried out using a drilling machine on Al 6063 alloy. The tool rotational speeds 485, 710, 910, 1120 and 1400 rpm with a traverse speed 4 mm/min were applied. The Mechanical properties of welded joints were investigated using different mechanical tests including destructive test (tensile test and hardness). Solid-state welding is the process whereby coalescence is produced at temperatures below the melting point of the base metal without the use of any filler metal. Examples of solid-state welding processes include friction welding, Friction Stir Welding (FSW), ultrasonic welding, resistance welding, explosive welding and diffusion welding. There are fewer defects in solid-state welding because the metals do not reach their melting temperatures during the welding process.
However, the base metals being joined retain their original properties, and the Heat Affected Zone (HAZ) is small when compared with the fusion welding techniques. Friction Stir Welding is a variant of friction welding that produces a weld between two or more work pieces by the heating and plastic material displacement caused by a rapidly rotating tool that traverses the weld joint. This application of FSW on pipes can be used for petroleum, petrochemical, and natural gas industries which in some studies, estimated to provide 25% and 7% cost saving for offshore and onshore construction respectively.
-
WELDING FORCES
During welding, a number of forces will act on the tool:
A downwards force is necessary to maintain the position of the tool at or below the material surface. Some friction-stir welding machines operate under load control, but in many cases the vertical position of the tool is present, and so the load will vary during welding.
The traverse force acts parallel to the tool motion and is positive in the traverse direction. Since this force arises as a result of the resistance of the material to the motion of the tool, it might be expected that this force will decrease as the temperature of the material around the tool is increased.
The lateral force may act perpendicular to the tool traverse direction and is defined here as positive towards the advancing side of the weld.
Torque is required to rotate the tool, the amount of which will depend on the down force and friction coefficient (sliding friction) and the flow strength of the material in the surrounding region (stiction).
In order to prevent tool fracture and to minimize excessive wear and tear on the tool and associated machinery, the welding cycle is modified so that the forces acting on the tool are as low as possible, and abrupt changes are avoided. In order to find the best combination of welding parameters, it is likely that a compromise must be reached, since the conditions that favor low forces (e.g. high heat input, low travel speeds) may be undesirable from the point of view of productivity and weld properties.
-
TOOL TILT AND PLUNGE DEPTH
Adrawingshowingtheplungedepthand tilt ofthetool. The tool is moving to the left.
Adrawingshowingtheplungedepthand tilt ofthetool. The tool is moving to the left.
The plunge depth is defined as the depth of the lowest point of the shoulder below the surface of the welded plate and has been found to be a critical parameter for ensuring weld quality. Plunging the shoulder below the plate surface increases the pressure below the tool and helps ensure adequate forging of the material at the rear of the tool. Tilting the tool by 24 degrees, such that the rear of the tool is lower than the front, has been found to assist this forging process. The plunge depth needs to be correctly set, both to ensure the necessary downward pressure is achieved and to ensure that the tool fully penetrates the weld. Given the high loads required, the welding machine may deflect and so reduce the plunge depth compared to the nominal setting, which may result in flaws in the weld. On the other hand, an excessive plunge depth may result in the pin rubbing on the backing plate surface or a significant undermatch of the weld thickness compared to the base material. Variable-load welders have been developed to automatically compensate for changes in the tool displacement, while TWI have demonstrated a roller system that maintains the tool position above the weld plate.
-
-
PRINCIPLE OF OPERATION
Two discrete metal workpieces butted together, along with the tool (with a probe)
The progress of the tool through the joint, also showing the weld zone and the region affected by the tool shoulder A rotating cylindrical tool with a profiled probe is fed into a butt joint between two clamped workpieces, until the shoulder, which has a larger diameter than the pin, touches the surface of the workpieces. The probe is slightly shorter than the weld depth required, with the tool shoulder riding atop the work surface. After a short dwell time, the tool is moved forward along the joint line at the pre-set welding speed.
Frictional heat is generated between the wear-resistant tool and the work pieces. This heat, along with that generated by the mechanical mixing process and the adiabatic heat within the material, cause the stirred materials to soften without melting. As the tool is moved forward, a special profile on the probe forces plasticized material from the leading face to the rear, where the high forces assist in a forged consolidation of the weld.
This process of the tool traversing along the weld linein a plasticized tubular shaft of metal results in severe solid- state deformation involving dynamic recrystallization of the base material.
-
WELD QUALITY
FSW produces excellent weld quality with these features:
Low distortion: In butt welding aluminum, for example, from 2.8 mm and thicker, the plate distortion in a properly built FSW machine is more or less zero. Tests on 12-m lengths have been carried out in which sideway bends smaller than 0.25 mm (0.01inch) were achieved, and no twist was seen with material thicker than 2.8 mm. In thinner materials, a slight upward bend occurred, but no twist or side bends were seen.
Low shrinkage: FSW produces the same predictable amount of shrinkage each time, normally found lower than 2 mm on 6-m-wide aluminum panel application.
No porosity: Because the base material does not melt, there is no porosity.
No lack of fusion: Because this is an extruding and forging joining method with a more accurate control of the heat, no lack of fusion is seen.
No change in material: When joining aluminum, material properties change little from the parent material as the maximum temperature during the joining process is approximately 450 degrees C, and no filler material or anything other than heat is added to the joint. Due to the resultant finer grain structure in the weld nugget, the weld sometimes is stronger than the base material. In steels, most of these same advantages apply.
-
MATERIAL
-
OBSERVATION TABLE
SR. NO
.
RPM
Shoulder Diamete r (mm)
Pin Length (mm)
Welding Speed (mm/sec
)
Ultimat e Tensile Strengt
h (MPa)
1
485
15
4.7
4
158.554
2
1400
15
4.7
4
126.466
Ultimate Tensile Strength=
FIGURE:1
Excessive weld flash on trailing edge at 485 rpm speed
FIGURE:2
Slight weld flash on trailing edge that has exhibited more good quality weld at 1400 rpm speed
-
LIMITATIONS
-
Exit hole left when tool is withdrawn.
-
Large down forces required with heavy-duty clamping necessary to hold the plates together.
-
Less flexible than manual and arc processes (difficulties with thickness variations and non- linear welds).
-
Often slower traverse rate than some fusion welding techniques, although this may be off set if fewer welding passes are required.
-
-
CONCLUSION
-
REFERENCES
-
Friction Stir Welding Tool Design and Their Effect on Welding of AA-6082 T6 Kalmeshwar Ullegaddia, Veeresh Murthy, Harsa R Nc, Manjunathad published in 2016
-
Analysis and design of friction stir welding tool byC.B.
Jagadeesha Published in 2017
-
Effect of tool pin side area ratio on temperature distribution in friction stir Welding by A.M.Sadouna, A. Wagihb, A Fathy,
A.R.S. Essac published in 2019
-
Mechanical behaviour of FSW joint welded by an oval designed Stationary shoulder tool by Sunil Sinhmara, Dheerendra Kumar Dwivedia published in September 2019
-
Studies on process parameters and tool geometry selecting aspects of friction stir welding by, R. Anand and V.G. Sridhar published in December 2019
-
FRICTION STIR WELDING OF PIPELINE STEELS By Murray Mahone, Sam Sanderson, Zhili Feng, Russell Steel, Scott Packerl and Dale Fleck published in 2013
-
Design and Experimental study of Friction stir welding of AA6061-T6 Alloy for Optimization of welding parameters by using Lathe Machine by Piyush Patel, Sachin Patel, Hiren Shah Volume: 04 Issue: 3| March-2017
-
Experimental Investigations of Friction Stir Welding (FSW) on Al6061 a Case Study by Dr. Sanjeev Reddy K Hudgikar, Dr. Chandrakant Y. Seemikeri, Prof. Prasad S. Kamble. Volume: 04 Issue: 08 | Aug-2017
-
Estimation of material properties using hysteresis loop analysis in Friction stir welded steel plate by Avinash Ravi Raja, Meghanshu Vashista, Mohd Zaheer Khan Yusuf zai published on 13 September 2019
-
Studies on the effect of welding parameters for friction stir welded AA 6082
-
Reinforced with Aluminium Oxide Khalique Ejaz Ahmed, B.M. Nagesh, B.S. Raju, D.N. Drakshayani published on15 October 2019
-
FRICTION STIR WELDING STUDY ON ALUMINUM PIPE BY A M Khourshid and I Sabry Vol.2, No.3, July 2013
-
Friction stir welding of small-dimension Al 3003 and pure Cu
pipes Binxi Chena, Ke Chena, Wei Haoa, Zhiyuan Lianga, Junshan Yaoc, Lanting Zhanga, Aidang Shana published on 7April 2015
-
[13] FRICTION STIR WELDING IN CIRCULAR PIPES by Kishore Prasaath, Manikandan, Shanmuga Praveen,
Ponmurugan. Volume:05 Issue:03|Mar- 2018
-
Identifying the optimal FSW process parameters for maximizing the Tensile strength of friction stir welded AISI 316L butt joints by S. Shashi Kumar, N. Murugan, K.K. Ramachandran published on 18 January 2019
-
Effect of tool tilt angle on strength and micro structural characteristics of Friction stir welded lap joints of AA 2014 – T6 aluminium alloy by C. RAJENDRAN, K. SRINIVASAN, V. BALASUBRAMANIAN, H. BALAJI P. SELVARAJ published on 15 July 2019
-
Using coupled Eulerian La Grangian formulation for accurate modelling of the friction stir welding process by KunLia, Firas Jarrara, Jamal Sheikh- Ahmada, Fahrettin Ozturkb. Published on September 2017
-
Numerical and experimental study on friction stir welding of aluminium Alloy pipe by Md Perwej Iqbala, Rahul Jainb, Surjya
K. Pala published on 10 June 2019