
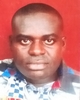
- Open Access
- Authors : Ojong Ojong Elias , Michael Oluwasegun Timothy , Ololade Moses Olatunji
- Paper ID : IJERTV10IS030202
- Volume & Issue : Volume 10, Issue 03 (March 2021)
- Published (First Online): 12-05-2021
- ISSN (Online) : 2278-0181
- Publisher Name : IJERT
- License:
This work is licensed under a Creative Commons Attribution 4.0 International License
Development of Model to Estimate the Optimal Yield of Acetaldehyde from Ethanol Oxidation
Ojong Ojong Eliasa, Michael Oluwasegun Timothyb, Ololade Moses Olatunjic,
a Department of Chemical Engineering, Faculty of Engineering & Technology, University of Calabar, P.M.B. 1115 Calabar, Cross River State, Nigeria.
b Department of Chemical Engineering, Amadu Bello University Zaria, Kaduna State,Nigeria.
c Department of Chemical/Petrochemical Engineering, Rivers State University, Port Harcourt, Nigeria.
Abstract:- Acetaldehyde is used as an intermediate in the production of acetic acid, acetic anhydride, cellulose acetate, vinyl acetate resins, acetate esters, pentaerythritol, synthetic pyridine derivatives, terephthalic acid and peracetic acid. Synthetic pyridine derivatives, peracetic acid, acetate esters and pentaerythritol account for 40% of acetaldehyde demand (Hagemeyer, 1991). The research work aimed at obtaining maximum yield of acetaldehyde through consecutive series reaction process of ethanol oxidation to reduced cost and maximizes profit under same condition of process. The conservation of material balance principle was employed on tubular (plug flow) reactor to developed the models equivalent to the rate of reaction of species balances for the series kinetics reaction. The series reaction kinetics for the oxidation of ethanol to acetaldehyde was applied to develop the plug flow reactor optimization models. Literature data was adopted to simulate the models using MATLAB program and generate results. The results indicate that the optimum yield of the intermediate acetaldehyde occurs at maximum space time value, of 0.869 hrs with the corresponding of 83%. This research
was carried out in a tubular reactor with supported catalyst containing 4.0 wt% copper and 2.0 wt% chromium respectively.
Acetaldehyde as an intermediate petrochemical feed material is used for the production of essential products in most of the petrochemical industries locally and commercially
Keywords: Optimal, yield, acetaldehyde, ethanol oxidation, model, desired product.
1.0 INTRODUCTION
The focus of an industrialist is how to achieve maximum yield of the desired product at optimum time frame. Chemical Kinetics is concerned with the velocity or time rate of reaction and the mechanisms of the reaction. The rate constant determines how quantitative the yield of the reaction is. Therefore, efforts aimed at optimizing the rate constant would enhance yield maximally. In many chemical processes of transformation of reactants into products, only the disappearance of the reactants and appearance of the final products may be observed (Puri et al., 2016). But for batch reactor occurring in steps, intermediate products may be formed which may not be detected because they are promptly used up in the subsequent step to yield the main product. The rate of reaction generally decreases with time but the coefficient of determination (rate constant) remains unchanged throughout the reaction. The rate depends on the active concentration of the reactants and is greatly influenced by temperature among other factors such as the nature and concentration of the reacting species (Higham, 2008).
Acetaldehyde is a colourless liquid or gas with a characteristic pungent odour (Budavari, 1996; Verschueren, 1996), flammable; polymerizes violently in the presence of trace amounts of metals or acids; can react violently with acid anhydrides, alcohols, ketones, phenols, ammonia, hydrocyanic acid, hydrogen sulfide, halogens, phosphorus, iso-cyanates, strong alkalis and amines. Acetaldehyde is used as an intermediate in the production of acetic acid, acetic anhydride, cellulose acetate, vinyl acetate resins, acetate esters, pentaerythritol, synthetic pyridine derivatives, terephthalic acid and peracetic acid. Synthetic pyridine derivatives, peracetic acid, acetate esters and pentaerythritol account for 40% of acetaldehyde
demand (Hagemeyer, 1991). Other uses of acetaldehyde include: in the silvering of mirrors; in leather tanning; as a denaturant for alcohol; in fuel mixtures; as a hardener for gelatin fibres; in glue and casing products; as a preservative for fish and fruit; in the paper industry; as a synthetic flavouring agent; and in the manufacture of cosmetics, aniline dyes, plastics and synthetic rubber.
Acetaldehyde is a natural product of combustion and photo-oxidation of hydrocarbons commonly found in the atmosphere. It is an important industrial chemical and may be released into the air or in wastewater during its production and use. It has been detected at low levels in drinking-water, surface water, rainwater, effluents, engine exhaust and ambient and indoor air samples. It is also photo-chemically produced in surface water. Acetaldehyde is an intermediate product in the metabolism of ethanol and sugars and therefore occurs in trace quantities in human blood. It is present in small amounts in all alcoholic beverages, such as Beer, wine and spirits and in plant juices and essential oils, roasted coffee and tobacco smoke (Jira et al., 1985; Hagemeyer, 1991)
The oxidation of ethanol to produce acetaldehyde as an intermediate product is a first order consecutive reaction in series. This process also leads to the formation of a carbon dioxide. The first order reaction is carried out in the presence of a catalyst in a threefold excess of oxygen and in dilute concentrations. The work aimed to develop the model for the optimum yield of acetaldehyde produced from ethanol oxidation which is achieved by the steps stated thus: to study the kinetics of the ethanol oxidation to acetaldehyde and hence the full process, to develop kinetic model for the ethanol oxidation to produce acetaldehyde as intermediate product, to simulate the developed models to predict the functional parameters of the process in the plug flow reactor, to predict the concentration profile of the intermediate product (desired product) of the reaction in the plug flow reactor
and to use the model to obtain the optimum conversion of the desired product. The importance of this research work is to develop a model for a tubular reactor for the oxidation of ethanol to acetyl aldehyde (desired product). The rout of conversion of ethanol is series reactants to products which gives a guarantee for actualization of optimal model development of the process.
The optimum yield was predicted and at maximum time determined too through this process of modeling the reactor process. This research work is focused on the development of a model for catalytic oxidation of ethanol to produce the desired product, called acetaldehyde which is an intermediate product. The model equation was simulated and also used to obtain optimal models for the prediction of desired yield of acetaldehyde taking place in a Plug Flow reactor. The kinetics of the process will be series reaction, Several authors have carried out work on this areas which are cited thus: The 1990 Clean Air Act Amendments presently require the addition of oxygenates to reformulated gasoline, with seasonal adjustments, on the premise that oxygen content decreases automotive emissions, particularly smog generation participants and carbon monoxide.
Ethanol is favoured to replace methyl tertiary butyl ether (MTBE), another widely used oxygenate additive that has become unpopular based upon ground water contamination and human health effects. While most ethanol is currently generated by fermentation (grain alcohol), recent developments suggest that ethanol fuel can be derived more efficiently from other biomass, thus offering potential to reduce dependenceon fossil fuel energy resources. Norton and Dryer, 1992 conducted a series of ethanol oxidation experiments in an Atmospheric Pressure Flow Reactor (APFR). In the modeling efforts of Norton and Dryer, 1992) as well as those of several other investigators the importance of including all three isomeric forms of C H O produced by H-atom
2 5
abstraction from ethanol was emphasized (Norton and Dryer, 1992). Marinov, (1999) carried out an extensive detailed kinetic modeling study of ethanol combustion at intermediate and high temperatures. His computational results indicated that ethanol oxidation exhibits strong sensitivity to branching ratio assignments of the H-atom abstraction reactions of ethanol as well as to the kinetics of its uni-molecular decomposition.
More recently, Saxena and Williams (2007) developed an ethanol mechanism by extending prior kinetic efforts on small hydrocarbon chemistry (i.e. their evolving San Diego Mechanism). Earlier works on ethanol uni-molecular decomposition is important (Marinov, 1999), for developing new comprehensive pyrolysis and oxidation model and to also develop a broader set of pyrolysis and oxidation flow reactor validation data (Marinov, 1999). Chemical kinetics relates to the studies of the rates at which chemical processes occur, the factors on which these rates depend, and the molecular acts involved in reaction mechanisms (Kayode, 2001).
-
MATERIALS AND METHODS
-
Materials
The materials used here are the thermodynamics data, literature values from plant and the conservative principle of mass and energy and finally tubular reactor. The oxidation of ethanol to form acetaldehyde is carried out on a catalyst of 4.0 %,
2.0 %, Al2O3. The reaction is carried out in a threefold excess of oxygen and in dilute concentrations. The volume change with the reaction is also neglected in this process (Fogler, 2004).
-
Methods
Oxidation of ethanol to give acetaldehyde is an essential intermediate product used for petrochemical industries for production of plastics, resins, etc. The kinetics of the reaction process is a series consecutive process shown in the reaction below equation 1.
+ 1 + 5
32 2 2 32 2 2 22 (1)
2
= 32, = 3
= 2
22
Reaction process is a series one and equation 1 can be written in a more standard way as designated by the letters A. P and C with rate constants k1 and k2 as shown in equation 2:
1
2
(2)
The rate expression for equation 2 is written mathematically for the reactant, intermediate, and the product as shown in equations 3, 4 and 5:
( ) = =
1
(3)
( ) = =
1
2
(4)
( ) = =
2
(5)
Equations 3, 4 and 5 can also be obtained also from the material balance principle on the tubular (plug flow) reactor to give:
= ( ) (6)
Where: = (, , ) /3,
= ,
.3
From equation (3), the solution kinetics (first order reaction process) is obtained from integrating it with boundary condition to give equation 6
1
1
= (7)
Substitute the expression for in Equation (7) for in Equation (4) and integrating using integrating factor of 2 gives equation 12 below
=
1
2
(8)
= (
1)
1 ,
2
(9)
= 1,1 2
(10)
+
=
1
2
1 ,
(10)
Applying the method of integration factor (I.F) to obtain the solution and multiplying through gives:
2 + 2
= 2
1
2
1 ,
(12)
2 + 2 =
(12). (13)
2
1 ,
By mathematical analysis, the Right-Hand Side of Equation (13) is of the form of product rule differentiation i.e.
() = +
(14)
(2)
( ).
= 1, 1 2
(15)
Integrate Equation (15) with respect to gives
(2) = 1, (12)
2 = 1, (12)
=
=
1,
(12)
. (12) +
2 = 1,
(12) +
(12)
(16)
To obtain the value of C, we apply the boundary conditions, at
= 0, (0) = 0, = 0
(0)() = 1,
(1)
(12)() +
=
=
1,
(12)
=
=
1,
(12)
=
=
1,
(12)
() +
+
(17)
Substitute Equation (17) into Equation (16) yields:
2 = 1, (12) + 1,
(12)
12
2 = 1, 1, (12)
12 12
2 = 1, [1 (21)]
12
(18)
Further simplification and arrangement gives,
= [1 2] (19)
1,
1,
12
Divide all through by ,
1,
1,
( ) =
= [(1) (2)] (20)
21
Equation (20) is the maximum yield of the products and was simulated and results, tables and profiles plots were generated using
simple program. Also subjected equation 20 to reactor optimality by letting that at optimum yield, = 0 to obtain
= 0 = 1, { (1) + (2)} (21)
21 1 2
Re-arranging equation 21 and taking natural log on both sides gives:
1(1) = 2(2)
[ [ln 2] = ln((1)) ln((2))
1
[]
= ln
2]
2 1
[1
ln 2] [
[= 1 =
[21]1
[21] =ln[2]
1
1
(22)
Substituting equation 22 into equation 20 to obtain optimum yield given below:
[( )]= ( )
= 1 [(1) (2)]
21
(1)
(2)
(23)
[( )]= () = 1 [
] (24)
21
Equation 24 is simplified to give equation 24 which is the optimal yield of oxidation of ethanol to acetaldehyde:
1
()
= [2]21 (25)
1
-
Input Parameters for MATLAB 2008 Simulation
Models 19, 22 and 25 are simulated with k1 and k2 values and also the initial concentration (see Table 1) using the MATLAB 2008 simulator to obtained the optimum space time and optimum yield.
-
RESULTS AND DISCUSSION
-
Results
The computer program was written using MATLAB 2008 to achieve the maximum yield of the desired product in a reasonable time frame ran and produced the following results. The results show the space time, concentration of acetaldehyde and yield of acetaldehyde respectively. Data presented in Table 1 was used as inputs for the MATLAB computer program for calculations of the concentration of acetaldehyde, yield of acetaldehyde and space time. Table 2 presents the results from MATLAB computer program for the achieved maximum yield of the desired product at a reasonable space time.
The results presented in Table 2 were plotted as concentration of acetaldehyde and yield of acetaldehyde with space time base on simulations done. The graphs plotted are discussed so as to know and predict the concentration and yield of acetaldehyde would change with respect to space time. The feed concentration was reduced to give the most important product, acetaldehyde.
It is predicted from the result obtained that the reactant concentration reduce to increase the yield of the acetaldehyde formed and compared to other works by Hagemeyer, 1991, the maximum yield of acetaldehyde was 40 % when the concentration was 40 mol/m3, this work gave maximum yield of 83.2% and occurs at 83.16 mol/m3. This can be concluded that this research work gave high yield of acetaldehyde due to optimization techniques carried out by plug flow-
Effect of Space Time on Concentration of Acetaldehyde
Figure 1 depicts the variation of concentration of acetaldehyde with space time. There is a sudden increase in concentrations from 0 molar to 85 molar at lower space time of 0 hr – 0.868 hr and then decreases in concentration from 85 molar to 40 molar when space time increases from 0.868 hr 4 hrs. However, the maximum yield occurs at space time 0.868 hr which is far better than previous work with maximum yield of 40 % at space time 2.5 hrs (Hagemeyer, 1991). Thus the models developed are reliable and gave more acetaldehydes from the oxidation of ethanol than previous methods of acetaldehyde production. The research work gives optimum space time of 0.868 hr as it was this space time that maximum yield of 83.2 % at 83.16 molar was obtained. This also means that after that space time, the plug flow may be stopped since the concentration of acetaldehyde starts decreasing after that space time. The time to achieve the desire product was normal and good enough for this production and saves cost of fabrication, running of such a plug flow reactor for design purposes.
-
Effect of on Yield on Acetaldehyde
Figure 2 demonstrates the variation of yield of acetaldehyde with space time.
There is linear increase in yield with concentration. The results indicates that higher concentration will lead to higher yield but must not necessary be maximum yield, this may depend on the maximum space time that lead to maximum yield.
-
Effect of Space Time on Concentration of Acetaldehyde
Figure 3 shows the relationship between the yield and the space time. There is a sharp increase in the yield from 0 % – 83 % at space time from 0 hr – 0.868 hr and the decrease almost linearly from 83 % – 40 % as space time increases from 0.868 hr to 4.5 hrs. This indicates that maximum space time is 0.868 hr in which gives the maximum yield of 0.832 [-] or 83.2 %. At this point, the acetaldehyde yield is highest and then gives lowest yield of 40 % at higher time of 4.5 hrs. This research work is far better and gave high yield compared to previous work carried out by Hagemeyer, 1991.
4.0 CONCLUSION
The development of optimal yield models for the oxidative catalysis of ethanol to give acetaldehyde. The kinetic model was developed which was essential in the optimization of the yield. The models developed were simulated using MATLAB and tables and profiles generated which were in agreement with the research aim and objectives. These model parameters are expressed as function of rate constants, state of the reactant, Temperature and Pressure but mostly on space time.
Notations
1 & 2 = Rate constants (1); 0 & 0 = Initial Concentrations (/3; = Yield (%); = Space Time ();
= Matrix Laboratory
REFERENCES
-
Kayode, A. C. (2001). Modeling of Chemical Kinetics and Reactor Design, Gulf: Boston Oxford Johannesburg Melbourne New Delhi Singapore, XVIII.
-
Budavari, S. (1996). The merch index, 12th Ed., Whitehouse Station, NJ, Merck & Co., p.8
-
Fogler, H. S. (2004). Elements of Chemical Reaction Engineering , 3rd Edition, Asoke K. Ghosh: New Delhi-110001, PP 296-314.
-
Hagemeyer, H. J (1991). Acetaldehyde. In: Kroschwitz, J. I & Howe-Grant, M., eds, Kirk-Othmer Encyclopedia of chemical Technology, 4th Ed., vol. 1, pp. 94 109.
-
Higham, D. J (2008). Modelling and Simulation of Chemical Reactions, Society for Industrial and Applied Mathematics (SIAM) Review, 50:347-368
-
Jira, R, Laib, R. J and Bolt, H. M (1985). Acetaldeyde. In: Gerhart, W. & Yamamoto, Y.S., eds, Ullmanns Encyclopedia of industrial Chemical, pp. 34 44.
-
Marinov, N. M. (1999). A detailed Chemical Kinetic Model for high Temperature Ethanol oxidation. International Journal of Chemical kinetics 31: 183-220
-
Saxena, P. and Williams, F. A. (2007). Numerical and Experimental studies of ethanol flames, Proceedings of the Combustion institute, 31(1):1149- 1156
-
Puri, B. R., Sharma, L. R and Pathania, M. S (2016). Principles of Physical chemistry: 47TH Edition, Vishal Publishing, Jalandhar, India, pp. 669-700.
-
Norton, T. S and Dryer, F. L. (1992). An experimental and modeling study of ethanol oxidation kinetics in an atmospheric pressure flow reactor.
International Journal of Chemical Kinetic 24: 319-344
-
Verschueren, K (1996). Handbook of Environmental Data on Organic Chemicals, 3rd Edition, New York, Van Nostrand Reinhold, pp. 101 103.
-
-
90
80
70
60
50
40
30
20
10
0
-10 0
90
80
70
60
50
40
30
20
10
0
-10 0
Concentration (mol/m^3)
Concentration (mol/m^3)
Figure captions
-1
-1
1
1
2
Space Time (Hr)
2
Space Time (Hr)
3
3
4
4
5
5
FIG 1: Graph of Concentration versus Space time
-20
0.9
0.8
0.7
0.6
Yield (%)
Yield (%)
0.5
0.4
0.3
0.2
0.1
0
-0.1
0 20 40 60 80 100
Concentration (mol/m^3)
FIG 2: Plot of Variation of Yield versus Concentration
Source: Kayode (2001)
FIG 3: Variation of Yield versus Space Time
-1
-1
0.9
0.8
0.7
0.6
0.5
0.4
0.3
0.2
0.1
0
-0.1 0
0.9
0.8
0.7
0.6
0.5
0.4
0.3
0.2
0.1
0
-0.1 0
1
1
2
Space Time (Hr)
2
Space Time (Hr)
3
3
4
4
5
5
Yield (%)
Yield (%)
Table 1:
Input Parameters for the simulations of the developed models
Parameter |
Value |
Rate Constants and |
3.446 1 and 0.215 1 |
Initial Concentration |
100 mol/m3 |
Table 2
Results of space time, yield of Acetaldehyde and concentrations of Acetaldehyde
Tau (Hr) |
C (mol/m^3) |
y (%) |
0 |
0 |
0 |
0.0014 |
0.47 |
0.005 |
0.011 |
3.84 |
0.038 |
0.23 |
52.9 |
0.53 |
0.58 |
79.6 |
0.796 |
0.72 |
82.44 |
0.824 |
0.868 |
83.16 |
0.832 |
1.08 |
82.06 |
0.821 |
1.5 |
76.76 |
0.78 |
2.04 |
68.68 |
0.687 |
2.73 |
59.4 |
0.59 |
4.5 |
40 |
0.4 |