
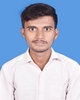
- Open Access
- [post-views]
- Authors : Gurramkonda Vsn Prasad , Tippireddy Mani Krishna
- Paper ID : IJERTV10IS030309
- Volume & Issue : Volume 10, Issue 03 (March 2021)
- Published (First Online): 06-04-2021
- ISSN (Online) : 2278-0181
- Publisher Name : IJERT
- License:
This work is licensed under a Creative Commons Attribution 4.0 International License
Digital Manufacturing of CAM profile by using Reverse Engineering Technique
Tippireddy Mani Krishna Simulation and System Design, Dept. of Mechanical Engineering
Hochschule Stralsund, Stralsund, Germany
Gurramkonda VSN Prasad
Product Design,
Dept. of Mechanical Engineering, JNTU college of Engineering, Ananthapur, Andhrapradesh, India,
Abstract In this paper the new strategy of digital manufacturing of a cam profile by integrating reverse Engineering with the 3D printer. In reverse engineering, 3D printing (Rapid Prototyping) plays a vital role in reproducing the physical component. 3D printing is a process of making three dimensional solid objects from a digital file by laying down successive layers of material until the entire object is created. In reverse engineering, the 3D modelling of the component is generated by measuring the dimensions using vision-based non-contact type sensors for regenerating the 3D virtual model of the component. After measuring the dimensions of the physical object, we can reconstruct it as a 3D model digital file using the cura software. So, by integrating both Reverse Engineering and 3D printing techniques, we can easily produce physical 3D models from digital files. By this method of manufacturing a cam profile, we can easily understand how to collect the external coordinates of the physical model (cloud data) and convert that data into the virtual 3D model of the required object for 3D printing.
Keywords Reverse Engineering, Digital Manufacturing, and 3D Printing.
automotive supplier that needs to produce spare parts, but lack the CAD data, in that case the Reverse engineering can be used to obtain the required specifications so that rare spare parts can be reproduced using 3D printing. Additionally, reverse engineering is beneficial when you need to make improvements to an existing object, but dont have its digital model. In this instance, reverse engineering allows you to scan the object and make in-process design changes, resulting in significant time savings.
-
METHODOLOGY
I. INTRODUCTION
Reverse engineering is a powerful tool for additive manufacturing, and this is combined with 3D Printing technology can greatly enhance product design as well as shorten the product development cycle. Whether you need to manufacture a legacy part that has no digital model or a spare part for replacement, reverse engineering has many benefits. The designing an object from scratch, a design engineer will produce drawings detailing how the object should be constructed. In contrast, reverse engineering involves the opposite approach of the design engineer starts from the end product, working backwards through the design process to reach the original design information. In theory, any object can be reverse engineered, whether it is a mechanical part, a consumer product or even an ancient artefact.
To begin the reverse engineering process, you will typically start by measuring the objects size and shape. This can be done manually but, particularly for industrial applications, the use of 3D scanning has increasingly become more commonplace. The data relating to the objects design specifications is then converted into a digital CAD file. At this point, the digital model can be converted to STL file for 3D printing.
There are several reasons why reverse engineering is a useful manufacturing technique. For example, are you an
Fig 1: Methodology for CAM Manufacturing in Reverse Engineering.
-
3D Scanning of CAM Profile:
3D scanners are devices used for 3-dimensional measurement and allow capturing data of the physical object quickly and precisely to create point clouds, which are then rendered into digital 3D representation. As the digital representation of an object is the backbone of 3D printing, 3D scanning offers an efficient digital solution when there is a need to reverse engineer old parts for replacement or parts without existing CAD models. Combining 3D printing and 3D scanning methods presents significant advantages to engineering applications requiring high accuracy and shorter product development times.
-
Cloud Point Deta to Mesh Mixure software
A point cloud is a set of data points in space. Point clouds are generally produced by 3D scanners, which measure many points on the external surfaces of objects around them. As the output of 3D scanning processes, point clouds are used for many purposes, including to create 3D CAD models for manufactured parts, for metrology and quality inspection, and for a multitude of visualization, animation, rendering and mass customization applications. While point clouds can be directly rendered and inspected, point clouds are often converted to polygon mesh or triangular mesh models, or CAD models through a process commonly referred to as surface reconstruction.
There are many advantages in the Mesh Mixer software for converting the point cloud data into a 3D model without caring about its 3D topology. Namely the mesh-mix functionality is very powerful, it allows to easily attach one model to another where the software takes care of all the nuances related to the mesh modification. The interface is simple, first, you choose the position where to attach the model, then you choose its orientation and finally the entire file save in the STL form.
-
Cura for slicing the virtual CAM profile
The cura slicing software is used in the majority of 3D printing processes for the conversion of a 3D object model to specific instructions for the printer. In particular, the conversion from a model in STL format to printer commands in G-code format in fused filament fabrication and other similar processes. The slicer first divides the object as a stack of flat layers, followed by describing these layers as linear movements of the 3D printer extruder, fixation laser or equivalent. All these movements, together with some specific printer commands like the ones to control the extruder temperature or bed temperature, are finally written in the G-code file, which can be transferred to the 3D printer. The cura majorly focused on the following strategies:
-
In-Fill
Solid objects need a big amount of valuable material (filament) and print time. The slicer can automatically convert solid volumes to hollow ones, saving costs and time. The hollow object can be partially filled by internal structures, as internals walls, to provide additional robustness. The amount of these structures is called infill density, being this parameter one of the adjustments to be provided to the slicer
-
Supports
Most of the 3D printing processes create the object layer by layer, down to up, with the layer under construction being deposited over the previous one. As consequence, all object parts must relay, at least in some part, over another one. In the case of an object layer that is floating (by example, the flat roof of a house or an horizontally extended arm in a figure), the slicer automatically can add supports for it. The support touch the object in a way that is easily detachable from it at the finish stage of the object production.
-
Rafts, skirts and brims
Printing of the first object layer, the one in contact with the printer bed, has some peculiarities, like problems of object adherence to the bed, rugosity, smooth deposition of the first amounts of filament. The slicer can automatically add some detachable structures to minimize these problems. Usual types of these base structures are a skirt (a single band around the base of the object without touching it), a brim (several lines offilament around the base of the object, each one a few more far from it until touch it, but not under it) and rafts (several layers of material that forms a detachable base, being the object printed over it)
Fig 2: CAM Profile in CURA Software.
-
-
3D Printing setup
The 3D printer machine must be set up properly before the build process starts. These preprocess setting would relate to the build parameters like the material constraints, power source, nozzle diameter, velocities extruder, temperature setup of build plate, etc.
-
3D Printing of CAM Profile
Building the physical component is mainly an automated process and the special supervision require to ensure no errors have taken place like running out of material, power or software glitches, etc. Once the 3D printer has completed the build, the parts must be removed.
Fig 3: 3D printed CAM profile.
-
Removal & post processing
After removed 3D printed CAM profile from the bill plate of 3D printer, may require an amount of additional cleaning up before they are ready for use. Parts may be weak at this stage or they may have supporting features that must be removed. This therefore often requires time and careful, experienced manual manipulation.
-
-
EXPERIMENTAL WORK AND DISCUSSION An attempt is made to build commercial 3D model of cam
by using Reverse Engineering & Fused Deposition Modelling. This work has proven that a 3D model can be built at much lower price than the other alternative techniques. The 3D model obtained was good and as accurate.
-
FUTURE SCOPE
Even though, the Fused deposition modelling was launched long back but still it wasnt used to its full potential. Its low
price and user-friendly feature caught our attention and lead us to build a 3D model using Fused deposition modelling. In future, in the field of automobiles Fused deposition modelling can widely use to build a commercial 3D model economically because of its cheaper price and accuracy in printing. Updating the present Fused deposition modelling machine may result the users around the world to use Fused deposition modelling in many areas like medical, rapid manufacturing and fashion etc.,
REFERENCES
-
Helen Loeb,Jinyong Kim, Kristy Arbogast, Jonny Kuo, Sjaan Koppel,
Suzanne Cross, Judith Charlton 2017 Published by Elsevier Ltd
-
Ingrid Parry, Clarissa Carbullido, Jason Kawada b, Anita Bagley, Soman Sen, David Greenhalgh, Tina Palmieri R
-
Rodrigo Ibañez, Ãlvaro Soria, Alfredo Teyseyre, Marcelo Campo
-
G. Shigley, J., & Uicker, J. (2010). Cam Design. Theory of machines and Mechanisms (4 ed.). Oxford University Press, USA. p. 200.