
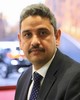
- Open Access
- Authors : Manojdeep Singh Jasrotia
- Paper ID : IJERTV14IS010125
- Volume & Issue : Volume 14, Issue 1 (January 2025)
- Published (First Online): 07-02-2025
- ISSN (Online) : 2278-0181
- Publisher Name : IJERT
- License:
This work is licensed under a Creative Commons Attribution 4.0 International License
Digital SMED: Revolutionizing Setup Time Optimization using Industry 4.0
Manojdeep Singh Jasrotia
Caresoft Global Technologies Inc.
Vice President -Engineering
AbstractThe white paper comprehensively explores the concept of Digital Single-Minute Exchange of Die (SMED) and its pivotal role in reducing setup times within manufacturing processes. It delves into the evolving landscape of Industry 4.0, highlighting the imperative of digital transformation in optimizing setup times to meet the demands of modern manufacturing. Central to this discussion is the case study of a machining cell dedicated to turning centers specifically utilized in producing transmission shafts. This case study is a focal point for illustrating the practical application of Digital SMED principles and techniques within a real-world manufacturing environment. By examining the setup optimization process within this machining cell, the paper showcases the integration of digital tools and technologies, including IoT devices, AI algorithms, and data analytics, to streamline changeover processes and enhance operational efficiency. The case study highlights the successful implementation of Digital SMED, emphasizing the measurable improvements in setup times, productivity, and overall equipment effectiveness (OEE). Through this detailed analysis, the white paper aims to provide valuable insights and best practices for manufacturers seeking to leverage Digital SMED in their operations. It underscores the transformative potential of digital technologies in revolutionizing setup time optimization and driving continuous improvement in the manufacturing sector.
KeywordsIndustry 4.0, digital transformation, manufacturing efficiency, setup time optimization, machining cell, turning centers, transmission shafts, IoT, AI, data analytics, real-time monitoring, predictive maintenance, digital work instructions, change management, case study, OEE, continuous improvement, digital tools, smart manufacturing.
- INTRODUCTIONIn the dynamic landscape of modern manufacturing, the ability to swiftly change production setups is paramount to maintaining competitiveness and meeting customer demands. Single-Minute Exchange of Die (SMED) has long been a cornerstone methodology for reducing setup times. However, in the era of Industry 4.0, the convergence of digital technologies is revolutionizing how SMED is implemented and executed. This white paper explores the concept of Digital SMED and its transformative impact on setup time optimization in manufacturing, specifically focusing on a case study involving a machining cell for turning centers used to produce transmission shafts. Through the lens of this case study, we delve into integrating digital tools and techniques, such as IoT, AI, and data analytics, to enhance setup processes and drive operational efficiency. By showcasing the practical application of Digital SMED principles, this paper aims to provide manufacturers with actionable insights and best practices for leveraging digital technologies to streamline setup times, improve productivity, and achieve operational excellence in the Industry 4.0 era.
- METHODOLOGYSetup Time Measurement: Initial setup times for the machining cell were measured using a stopwatch, capturing the time taken from the previous setup’s last good part to the new setup’s first good part.
SMED Analysis: A detailed SMED analysis was conducted following the initial setup time measurement to identify and categorize setup activities into internal and external setup elements.
Internal Setup Time: These are activities, such as tool changes and adjustments, that can only be performed when the equipment is stopped.
External Setup Time: These activities can be performed while the equipment is running, such as preparing tools and materials.
Setup Time Reduction Targets: Based on the SMED analysis, setup time reduction targets were established, focusing on converting internal setup activities to external activities and optimizing tool change and adjustment procedures.
Digital SMED Tools Implementation: Digital tools such as IoT sensors and data analytics were implemented to monitor and analyze setup processes in real-time. These tools provided insights into setup time variability and identified opportunities for further optimization.
Calculation of Setup Time Reduction: The setup time reduction achieved through Digital SMED was calculated using the formula:
Setup Time Reduction (%)= (Initial Setup TimeFinal Setup
Time / Initial Setup Time) × 100
Initial Setup Time: Time taken for setup before Digital SMED implementation.
Final Setup Time: Time taken for setup after Digital SMED implementation.
Overall Equipment Effectiveness (OEE) Calculation: The impact of Digital SMED on OEE was calculated using the formula:
Figure 1
Availability (%): Ratio of operating time to total time, accounting for setup and downtime.
Performance (%): Ratio of actual production rate to maximum production rate under ideal conditions
Quality (%): Ratio of good parts to total parts produced. To gain a lean in-plant logistics system, a cost-improvement model is proposed that focuses on:
- COST IMPROVEMENT MODELIn the context of Industry 4.0, integrating Single-Minute Exchange of Die (SMED) principles with digital technologies offers a comprehensive cost-improvement model for manufacturing operations. This model focuses on leveraging digital tools and techniques to reduce setup times, optimize resources, and enhance overall operational efficiency, ultimately leading to cost savings and improved competitiveness.
-
- Digital Tools for Setup Time Reduction: Industry 4.0 technologies such as IoT sensors, AI algorithms, and data analytics are crucial in identifying and eliminating non-value- added activities in setup processes. By monitoring equipment performance and setup procedures in real-time, these tools enable manufacturers to optimize setup times and minimize downtime, resulting in cost savingsThe setup time reduction achieved through digital tools can be calculated using the formula:
Figure 2
- Predictive Maintenance and Equipment Efficiency: Digital SMED integrated with Industry 4.0 enables predictive equipment maintenance, ensuring that machines are in optimal condition for setup and production. This proactive approach reduces the risk of unexpected breakdowns, minimizes setup delays, and improves equipment efficiency, leading to cost reductions associated with maintenance and repair. The cost savings from predictive maintenance can be calculated by comparing the cost of proactive maintenance to the cost of reactive maintenance. The formula is:Figure 3
- Resource Optimization and Inventory Management: Digital SMED allows manufacturers to optimize resource allocation and inventory management. By streamlining setup processes and reducing changeover times, manufacturers can minimize the need for excess inventory and storage space, leading to cost savings associated with inventory holding and management.The cost savings from inventory reduction can be calculated using the formula:
Figure 4
- Enhanced Data Visibility and Decision-Making: Industry4.0 technologies provide enhanced data visibility and analytics capabilities, allowing manufacturers to make informed decisions regarding setup optimization and resourc allocation. By analyzing setup data and performance metrics, manufacturers can identify trends, inefficiencies, and improvement opportunities, leading to cost-effective decision- making. The impact of data visibility on decision-making can be measured by the reduction in set-up times and the improvement in equipment efficiency. These metrics can be quantified using the formulas mentioned earlier.
- Overall Equipment Effectiveness (OEE) Improvement: Integrating SMED with Industry 4.0 can significantly improve OEE by reducing setup times, minimizing downtime, and increasing equipment efficiency. Improved OEE translates to higher productivity, lower production costs, and increased profitability. As quantified earlier, the impact of continuous improvement and flexibility can be measured by the reduction in setup times and the increase in operational efficiency.
- Continuous Improvement and Flexibility: Digital SMED integrated with Industry 4.0 enables manufacturers to adopt a culture of continuous improvement and flexibility. Manufacturers can adapt to changing market demands and optimize costs by continually analyzing setup processes and implementing improvements. As quantified earlier, the impact of continuous improvement and flexibility can be measured by the reduction in set-up times and the increase in operational efficiency.
- Digital Tools for Setup Time Reduction: Industry 4.0 technologies such as IoT sensors, AI algorithms, and data analytics are crucial in identifying and eliminating non-value- added activities in setup processes. By monitoring equipment performance and setup procedures in real-time, these tools enable manufacturers to optimize setup times and minimize downtime, resulting in cost savingsThe setup time reduction achieved through digital tools can be calculated using the formula:
-
- APPROACHFigure 5
Step 1: Assessment and Planning
Before implementing Digital SMED with Industry 4.0, it’s crucial to understand the current setup processes, their inefficiencies, and the potential for improvement. This step provides insights into the specific areas that need to be addressed, setting the foundation for a successful implementation.
Manufacturers can uncover hidden inefficiencies in their setup processes through a detailed assessment, such as redundant tasks, long changeover times, and lack of standardized procedures. This insight is essential for developing a targeted plan to optimize setup times using digital technologies.
Figure 6
-
-
- Define Objectives: Clearly define the objectives of implementing Digital SMED, such as reducing setup times by a certain percentage, improving equipment efficiency, or increasing production flexibility.
- Analyze Current Setup Processes: Conduct a thorough analysis of the current setup processes, including time and motion studies, to identify bottlenecks and areas for improvement.
- Identify Digital SMED Opportunities: Identify opportunities to leverage digital technologies, such as IoT sensors for real-time monitoring or AI algorithms for predictive maintenance, to optimize setup processes.
- Develop Implementation Roadmap: Develop a detailed roadmap for implementing Digital SMED, outlining the steps, timeline, and resources required for each implementation phase.
- Define Key Performance Indicators (KPIs): Define KPIs to measure the success of the implementation, such as setup time reduction, equipment downtime, and overall equipment effectiveness (OEE).
-
The approach to assessment and planning should be systematic and collaborative, involving input from key stakeholders, including production managers, engineers, and operators. It should also consider the specific needs and challenges of the manufacturing facility, ensuring that the implementation is tailored to the organization’s unique requirements.
This step’s deliverables include a comprehensive assessment report detailing the current state of setup processes, a detailed implementation plan outlining the steps and timeline for implementing Digital SMED, and a set of defined KPIs to measure the implementation’s success.
The outcome of this step is a clear understanding of the current setup processes, identified opportunities for improvement, and a detailed roadmap for implementing Digital SMED with Industry 4.0. This sets the stage for a successful implementation that can significantly improve setup times, equipment efficiency, and overall operational performance.
Step 2: Digital Tool Selection
Figure 7
The right digital tools and technologies are crucial for successfully implementing Digital SMED with Industry 4.0. These tools should align with the specific needs and goals of the setup time optimization process, leveraging the capabilities of Industry 4.0 technologies to drive efficiency and effectiveness.
Choosing the appropriate digital tools requires a deep understanding of the setup processes and the potential benefits and limitations of each technology. The right tools can streamline setup processes, improve equipment efficiency, and enable real-time monitoring and analysis, leading to significant cost savings and operational improvements.
-
-
- Define Technology Requirements: Based on the assessment conducted in Step 1, define the specific technology requirements for optimizing setup processes, considering factors such as data collection needs, analytics capabilities, and integration with existing systems.
- Research and Evaluation: Conduct thorough research on available digital tools and technologies that align with the defined requirements. Evaluate each tool based on its functionality, scalability, cost-effectiveness, and compatibility with existing systems.
- Pilot Testing: Select a few promising digital tools and technologies for pilot testing in a controlled environment. Evaluate their performance in improving setup times, reducing downtime, and enhancing equipment efficiency.
- Stakeholder Input: Gather input from key stakeholders, including production managers, engineers, and operators, to ensure the selected tools meet their needs and expectations.
- Select Tools: Based on the research, evaluation, and pilot testing, select the digital tools and technologies that best meet the requirements for optimizing setup processes.
-
The approach to digital tool selection should be systematic and data driven. It should focus on identifying tools that can deliver tangible benefits in terms of setup time reduction,
equipment efficiency, and overall operational performance. It should also involve collaboration with key stakeholders to ensure buy-in and support for the selected tools.
The deliverables of this step include a list of selected digital tools and technologies, along with a rationale for their selection based on the defined requirements and evaluation criteria. Additionally, a plan for implementing the selected tools should be developed, outlining the steps, timeline, and resources required for implementation.
This step’s outcome is the selection of digital tools and technologies well-suited for optimizing setup processes in the manufacturing facility. These tools should enable real-time monitoring, data analytics, and process optimization, improving setup times, equipment efficiency, and overall operational performance.
Step 3: Integration with Smart Manufacturing Systems
Figure 8
Integrating Digital SMED with smart manufacturing systems is essential for leveraging real-time data and analytics to optimize setup processes. This step ensures seamless integration between digital tools and existing manufacturing systems to maximize efficiency and effectiveness.
Smart manufacturing systems enable manufacturers to monitor equipment performance, analyze data in real time, and make informed decisions to optimize setup processes. By integrating Digital SMED with these systems, manufacturers can achieve greater visibility and control over setup operations, improving efficiency and reducing setup times.
-
-
- Define Integration Requirements: Identify the key requirements for integrating Digital SMED with smart manufacturing systems, including data exchange protocols, compatibility with existing systems, and scalability.
- Evaluate Integration Options: Based on the defined requirements and feasibility, evaluate different integration options, such as API integration, middleware solutions, or custom development.
- Develop Integration Plan: Develop a detailed integration plan outlining the steps, timeline, and resources required to integrate Digital SMED with smart manufacturing systems. Include testing and validation processes to ensure seamless integration.
-
Implement Integration: Implement the integration plan, ensuring that all digital tools and technologies are properly integrated with smart manufacturing systems. Test the integration to verify data exchange and functionality.
Monitor and Optimize: Continuously monitor the integration to ensure that it meets the defined requirements and delivers the expected benefits. Optimize the integration as needed to improve efficiency and effectiveness.
The approach to integration should be collaborative, involving close coordination between the IT department, production managers, and engineers. It should also be iterative, with regular testing and validation to ensure that the integration meets the defined requirements and delivers the expected benefits.
The deliverables of this step include a detailed integration plan, documentation of the integration process, and a validated integration between Digital SMED and smart manufacturing systems. Additionally, any necessary training materials or resources should be developed to ensure that users can effectively utilize the integrated system. The outcome of this step is a fully integrated Digital SMED system with smart manufacturing systems, enabling manufacturers to optimize setup processes, improve equipment efficiency, and drive cost savings. This integration lays the foundation for continuous improvement and innovation in setup time optimization using Industry 4.0 technologies.
Step 4: Employee Training and Change Management Implementing Digital SMED with Industry 4.0 requires a shift in employee mindset and behavior. This step focuses on providing training and implementing change management strategies to ensure employees are equipped to effectively use digital tools and embrace new ways of working.
Figure 9
Employees play a critical role in the success of Digital SMED implementation. Providing training and support helps employees understand the new system’s benefits and how it can improve their work processes. Change management strategies help address any resistance to change and ensure a smooth transition to the new working method.
-
-
- Assess Training Needs: Conduct a training needs assessment to identify the specific skills and knowledge gaps that need to be addressed for effective implementation of Digital SMED.
- Develop Training Program: Develop a comprehensive training program that covers the use of digital tools, new processes, and procedures related to setup time optimization.
- Implement Training: Implement the training program, ensuring that all relevant employees receive training on Digital SMED and its benefits.
- Ongoing Support: Provide ongoing support and guidance to employees as they begin using Digital SMED in their daily work. Address any questions or concerns they may have and provide additional training as needed.
- Implement Change Management Strategies: Implement change management strategies to address any resistance to change and ensure employees are motivated to embrace the new way of working.
- Monitor and Evaluate: Monitor the effectiveness of the training and change management strategies and make adjustments to ensure that employees effectively use Digital SMED.
-
The approach to employee training and change management should be proactive and inclusive. It should involve employees in the process and address their concerns and feedback. It should also be ongoing, with regular communication and support provided to employees throughout the implementation process.
This step’s deliverables include a training program, training materials, and documentation of change management strategies. Additionally, any support materials or resources needed to help employees transition to the new way of working should be provided.
This step’s outcome is a workforce trained and ready to use Digital SMED with Industry 4.0 effectively. Employees are engaged and motivated to embrace the new technology, leading to improved setup processes, equipment efficiency, and overall operational performance.
Step 5: Implementation and Optimization
Figure 10
Implementing Digital SMED with Industry 4.0 requires a systematic approach to implement the new processes and technologies effectively. This step focuses on implementing the new setup processes, monitoring their performance, and optimizing them for maximum efficiency.
The implementation of Digital SMED should be approached as a continuous improvement process. By implementing the new setup processes in stages and continuously monitoringtheir performance, manufacturers can identify areas for improvement and make adjustments to optimize efficiency.
-
-
- Implement in Stages: Implement Digital SMED in stages, starting with a pilot project or a small-scale implementation. This allows for testing and validation of the new setup processes before full-scale implementation.
- Monitor Performance: Monitor the performance of the new setup processes using key performance indicators (KPIs) such as setup time, equipment efficiency, and overall equipment effectiveness (OEE).
- Identify Areas for Improvement: Identify areas where the new setup processes can be further optimized, such as reducing setup times, improving equipment efficiency, or enhancing data analytics capabilities.
- Optimize Setup Processes: Adjust the setup processes based on performance data and employee feedback. Continuously optimize the processes to improve efficiency and effectiveness.
- Document Changes: Document any changes made to the setup processes and update training materials and documentation accordingly.
-
The approach to implementation and optimization should be iterative, with regular reviews and adjustments made based on performance data and feedback. It should also be collaborative, involving key stakeholders such as production managers, engineers, and operators in decision-making.
This step’s deliverables include a fully implemented Digital SMED system, documentation of any changes made to the setup processes, and updated training materials and documentation. Additionally, any optimization strategies or best practices identified during the implementation process should be documented for future reference.
The outcome of this step is a fully optimized setup process that leverages Digital SMED and Industry 4.0 technologies to drive efficiency and effectiveness. Manufacturers can reduce setup times, improve equipment efficiency, and enhance overall operational performance, leading to cost savings and improved competitiveness.
Step 6: Performance Evaluation and Continuous Improvement After implementing Digital SMED with Industry 4.0, evaluating its performance and continuously improving the setup processes is essential. This step focuses on measuring the impact of Digital SMED on setup times, equipment efficiency, and overall operational performance, and identifying opportunities for further optimization.
Figure 11
Continuous improvement is key to maintaining and enhancing Digital SMED’s benefits. By regularly evaluating performance metrics and soliciting employee feedback, manufacturers can identify areas for improvement and implement changes to optimize setup processes further.
-
-
- Evaluate Performance Metrics: Measure key performance indicators (KPIs) such as setup times, equipment efficiency, and overall equipment effectiveness (OEE) to evaluate Digital SMED’s impact on setup processes.
- Solicit Feedback: Gather feedback from employees, including production managers, engineers, and operators, on their experiences with Digital SMED. Use this feedback to identify areas for improvement.
- Identify Improvement Opportunities: Based on the performance metrics and feedback, identify areas where the setup processes can be further optimized, such as reducing setup times, improving equipment efficiency, or enhancing data analytics capabilities.
- Implement Changes: Implement changes to the setup processes based on the identified improvement opportunities. Continuously monitor the impact of these changes on performance metrics.
- Document Best Practices: Document best practices and lessons learned from implementing Digital SMED. Share these with employees to facilitate knowledge sharing and continuous improvement.
-
The approach to performance evaluation and continuous improvement should be data-driven and collaborative. Performance metrics should be regularly reviewed, and feedback from employees should be actively sought to identify areas for improvement. Changes should be implemented iteratively, and their impact on performance metrics should be regularly monitored.
This step’s deliverables include performance evaluation reports, documentation of improvement opportunities, and implementation plans for changes to the setup processes. Additionally, best practices and lessons learned should be documented and shared with employees to facilitate continuous improvement.
The outcome of this step is a culture of continuous improvement in setup time optimization using Digital SMED and Industry 4.0 technologies. Manufacturers can identify and implement changes to further optimize setup processes, leading to sustained improvements in efficiency, effectiveness, and overall operational performance.
-
- CONNECTING PREVIOUS GENERATION MACHINE TOOLS FOR DIGITAL SMEDFigure 12
While it is easy to activate Industry 4.0 technology for new- generation machine tools, connecting older-generation machines to enable Digital SMED can indeed pose challenges, especially when direct access to the controller is difficult or not feasible. However, some several approaches and technologies can be utilized to overcome these obstacles and establish connectivity for setup time optimization:
-
- Retrofitting with Sensor Systems:Install retrofit sensor systems on critical machine components, such as tooling fixtures, actuating mechanisms, and control panels. These sensors can capture relevant data points such as position, movement, temperature, and vibration, providing insights into setup processes and equipment status. Implement wireless sensor networks or wired connections to transmit data to a centralized monitoring and control system.
- External Monitoring Devices:Deploy external monitoring devices or smart peripherals that can interface with the machine’s existing interfaces or peripherals. These devices can collect data from analog or digital outputs, switches, indicators, or control panels without requiring direct access to the machine’s internal controller. Utilize communication protocols such as Modbus, OPC-UA, or Ethernet/IP for data transmission and integration with digital SMED systems.
- Edge Computing and Data Acquisition:Employ edge computing devices or industrial IoT gateways to capture data directly from the machine’s sensors, actuators, or signal outputs. Process and aggregate, raw data locally using edge analytics capabilities to derive actionable insights and trigger setup optimization actions in real time. Utilize edge-to- cloud connectivity for seamless integration with centralized data analytics platforms and digital SMED systems.
- Manual Data Entry and Integration:Implement manual data entry or barcode scanning solutions to capture setup-related information and parameters directly from operators or setup technicians. Develop user-friendly interfaces or mobile applications to streamline data collection and entry processes, minimizing errors and delays. Integrate manual input data with digital SMED systems through APIs, middleware, or data connectors for analysis, visualization, and optimization.
- Collaborative Tools and Workflows:Foster collaboration between operators, maintenance personnel, and engineering teams to gather insights and feedback on setup procedures and challenges. Implement collaborative platforms or digital work instructions that enable real-time communication, documentation, and knowledge sharing among stakeholders. Leverage augmented reality (AR) or mixed reality (MR) technologies to overlay digital information and instructions onto physical equipment, enhancing setup efficiency and accuracy.
Figure 13
Connecting the entire factory for Digital SMED involves establishing a comprehensive network infrastructure that facilitates seamless communication, data exchange, and integration across various machines, systems, and processes. Here’s how it can be achieved:
- Industrial Networking:Deploy industrial-grade networking equipment such as switches, routers, and access points optimized for harsh manufacturing environments. Utilize wired Ethernet connections for high-speed and reliable communication between critical production equipment, control systems, and data servers. Implement wireless technologies such as Wi-Fi, Bluetooth, or Zigbee for flexible connectivity in areas where wired connections are impractical or cost-prohibitive.
- Ethernet/IP and Fieldbus Protocols:Standardize communication protocols such as Ethernet/IP, Profibus, Modbus, or DeviceNet to enable interoperability and compatibility between diverse manufacturing equipment and control systems. Implement industrial gateways or protocol converters to bridge communication between legacy machines with proprietary protocols and modern Ethernet-based networks.
- Industrial IoT (IIoT) Platforms:Deploy Industrial IoT platforms or edge computing devices to collect, aggregate, and analyze data from sensors, actuators, and control systems distributed throughout the factory. Utilize edge analytics capabilities to process data locally and derive actionable insights for real-time decision-making and optimization. Establish secure connectivity between IIoT devices, cloud-based analytics platforms, and enterprise IT systems for centralized data storage, analysis, and visualization.
- Supervisory Control and Data Acquisition (SCADA) Systems:Implement SCADA systems for centralized monitoring, control, and visualization of factory-wide operations, including setup processes, equipment status, and production metrics. Integrate SCADA systems with PLCs (Programmable Logic Controllers), HMI (Human-Machine Interface) panels, and MES (Manufacturing Execution Systems) for seamless data exchange and automation.
- Cloud Connectivity and Edge-to-Cloud Integration:Establish secure connectivity between on-premises manufacturing systems and cloud-based services for data storage, analysis, and collaboration. Utilize edge-to-cloud integration capabilities to transmit real-time data from edge devices to cloud platforms for advanced analytics, machine learning, and predictive maintenance. Implement robust security measures such as encryption, authentication, and access controls to safeguard sensitive data and ensure compliance with industry regulations.
- Collaborative Tools and Digital Workflows:
Foster collaboration and information sharing among factory personnel through digital collaboration tools, communication platforms, and knowledge-sharing portals. Develop digital workflows and standard operating procedures (SOPs) that leverage interconnected systems and data sources to streamline setup processes, reduce errors, and improve productivity. Utilize augmented reality (AR) or virtual reality (VR) technologies to provide immersive training, remote assistance, and visualization of setup procedures for operators and maintenance technicians.
By implementing a robust network infrastructure, standardized communication protocols, IIoT platforms, SCADA systems, cloud connectivity, and collaborative tools, manufacturers can seamlessly connect the entire factory ecosystem and unlock the full potential of Digital SMED for setup time optimization and operational excellence.
-
- KEY PERFORMANCE INDICATORS (KPIS) FOR DIGITAL SMED WITH INDUSTRY 4.0IMPLEMENTATION
6.1 Setup Time Reduction: Measure the reduction in setup times achieved through implementing Digital SMED. This KPI reflects the efficiency of the new setup processes.
6.2. Equipment Efficiency Improvement: Measure the improvement in equipment efficiency, such as increased uptime and reduced downtime, resulting from Digital SMED implementation.
-
- Overall Equipment Effectiveness (OEE): Calculate the OEE of the manufacturing equipment before and after Digital SMED implementation to assess the overall impact on equipment performance.
- Cost Savings: Measure the cost savings achieved through reduced setup times, improved equipment efficiency, and optimized resource utilization.
- Production Flexibility: Assess the ability of the setup processes to quickly adapt to changes in production requirements, such as product changes or batch size adjustments.
- Employee Satisfaction: Gather feedback from employees on their satisfaction with the new set-up processes and their perceived impact on their work.
- Error Reduction: Measure the reduction in errors and defects in setup processes resulting from implementing Digital SMED.
- Return on Investment (ROI): Calculate the ROI of the Digital SMED implementation by comparing the implementation costs to the benefits achieved, such as cost savings and efficiency improvements.
-
- SIX-STEP SMED APPROACHFigure 14
Step 1: Problem Identification This step involves identifying the current challenges and inefficiencies in the setup process. It includes analyzing the existing setup procedures to pinpoint areas where improvements can be made to reduce setup time.
Step 2: Target & Planning. Once the problems have been identified, the next step is setting specific targets to reduce setup time. This involves creating a detailed plan that outlines the steps and resources needed to achieve these targets.
Step 3: Actual Study. In this step, a detailed study of the setup process is conducted to understand the sequence of steps, tools used, and time taken for each task. This study helps identify opportunities for improvement.
Step 4: Development of Ideas for Reducing the Setup Time. Based on the actual study, ideas, and solutions are developed to streamline the setup process and reduce setup time. This may involve standardizing procedures, reducing the number of steps, or implementing new technologies.
Step 5: Putting the Idea into Practice. Once the ideas for reducing setup time have been developed, they are implemented in a controlled environment, such as a pilot project. This allows for testing and validation of the ideas before full-scale implementation.
Step 6: Confirmation of the Result. The final step involves confirming the results of the setup time reduction efforts. This includes measuring the actual reduction in setup time achieved and evaluating the overall impact on efficiency and productivity.
By following these six steps, organizations can effectively implement SMED principles to reduce setup time, improve operational efficiency, and enhance overall productivity.
- CASE STUDY INTERNAL VS EXTERNAL TIME OF TRANSMISSION SHAFTFigure 15
From the SMED (Single-Minute Exchange of Die) perspective, the 67.5-minute setup time can be divided into internal, external, and testing time. Internal time refers to tasks that can only be done when the machine is stopped, such as adjusting settings or preparing the equipment. External time refers to tasks done while the machine runs, such as fetching tools or materials. Testing time is spent testing the setup to ensure it is functioning correctly.
The focus should be on reducing internal and external time to improve the setup time. This can be achieved through various SMED techniques:
-
- Internal Time Reduction:1)Standardize setup procedures to reduce the number of adjustments required. 2) Use quick-change tooling and fixtures to minimize the time needed for adjustments.
3)Simplify setup tasks by eliminating unnecessary steps or combining tasks where possible.
Figure 16
- External Time Reduction:1)Organize tools and materials to minimize the time needed to fetch them. 2)Implement visual management techniques to ensure tools and materials are easily accessible. 3)Use carts or other mobile storage solutions to quickly transport tools and materials to the machine.
Figure 17
- Testing Time Optimization:
- Internal Time Reduction:1)Standardize setup procedures to reduce the number of adjustments required. 2) Use quick-change tooling and fixtures to minimize the time needed for adjustments.
1)Develop standardized testing procedures to reduce the time needed for testing. 2)Implement predictive maintenance techniques to ensure equipment is in optimal condition, reducing the need for extensive testing. 3)Use automated testing tools and techniques to speed up the testing process.
By focusing on these areas for improvement, organizations can significantly reduce setup time and improve overall operational efficiency.
Figure 18
-
- RESULTS ACHIEVED
Sr. No.
Key Performance Indicators (KPIs) Base Line Status Future State 1 Shift output 28 36 Table 1
- CONCLUSIONDigital SMED: Revolutionizing Setup Time Optimization Using Industry 4.0″ highlights the significant impact of digital technologies on setup time optimization in manufacturing. Manufacturers can streamline setup processes, reduce downtime, and improve overall operational efficiency by leveraging Industry 4.0 technologies such as IoT, AI, and data analytics.
The study underscores the importance of a systematic approach to implementing Digital SMED, starting with a thorough assessment of current setup processes and culminating in continuous performance evaluation and improvement. Each step, from digital tool selection to employee training and change management, plays a critical role in the success of Digital SMED implementation.
Furthermore, the study emphasizes the need for collaboration between IT, production, and management teams to successfully integrate Digital SMED with smart manufacturing systems. This collaboration is essential for identifying and addressing challenges, optimizing setup processes, and achieving sustainable improvements in efficiency and productivity.
Overall, the study demonstrates that Digital SMED can revolutionize manufacturing setup time optimization, paving the way for greater agility, flexibility, and competitiveness in the industry 4.0 era.
- REFERENCES
- Borsato M, Filippini R, Gamberi M, Pilati F Al-Ali AR, Al-Najjar B,Industry 4.0: A Complete Overview, J Eng Appl Sci. 2017;12(15):3829-3838.
- Darrag, M., Khidir, A., & Tawfik, A. (2021),Industry 4.0 in Manufacturing Learning Factories: A Review, Procedia Manuf. 2020;48:1011-1017
- Springer, Cham. ElMaraghy, H. A. (2016),Improving Manufacturing Productivity Using Industry 4.0 Technologies: A Review, In Advances in Manufacturing Engineering and Materials (pp. 477-488).
- Kumar, S., Bhushan, B., Kumar, S., & Kumar, V. (2021), Changing manufacturing paradigms: The dawn of the fourth industrial revolution. Procedia CIRP, 54, 226-231.
- Lödding, H., Albers, A., & Esdar, T. (2015) , Past, present and future of Industry 4.0a systematic literature review and research agenda proposal, International journal of production research, 55(12), 3609-3629.
- Mourtzis, D., Doukas, M., & Bernidaki, E. (2018 ,Industry 4.0: State of the art and future trends. International Journal of Production Research, 55(12), 3609-3629.
- Sengottaiyan, Krishnamoorthy, and Manojdeep Singh Jasrotia. “SLP (Systematic Layout Planning) for Enhanced Plant Layout Efficiency.” International Journal of Science and Research (IJSR) 13, no. 6 (2024): 820-827.
- Jasrotia, Manojdeep Singh. “Unlocking Efficiency: A Comprehensive Approach to Lean In-Plant Logistics.” International Journal of Science and Research (IJSR) 13, no. 3 (2024): 1579-1587.
- Sengottaiyan, Krishnamoorthy, and Manojdeep Singh Jasrotia. “Relocation of Manufacturing Lines Structured Approach for Success.” International Journal of Science and Research (IJSR) 13, no. 6 (2024): 1176-1181.