
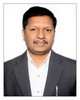
- Open Access
- Authors : S. Arjuna Rao, Rakesh K.G, Girija.G., Himangshu Roy, Sumbul Munshi
- Paper ID : IJERTV14IS030098
- Volume & Issue : Volume 14, Issue 03 (March 2025)
- Published (First Online): 02-04-2025
- ISSN (Online) : 2278-0181
- Publisher Name : IJERT
- License:
This work is licensed under a Creative Commons Attribution 4.0 International License
Effect and Influence of Temporary Test Conductors on LT Panel Temperature-Rise Test
Published by : http://www.ijert.org
International Journal of Engineering Research & Technology (IJERT)
ISSN: 2278-0181
Vol. 14 Issue 03, March-2025
[S. Arjuna Rao, Rakesh K.G, Girija.G., Himangshu Roy, Sumbul Munshi]Abstract: In electrical distribution network, the switchgear is viewed as the beating heart. Due to the switchgear’s continuous operation and continual power flow, thermal effects are a crucial consideration while conducting a type test. Both mechanical stress and temperature will rise with an increase in current input. Hence, Thermal analysis on switchgears is therefore essential. A critical step in ensuring that a low voltage assembly is built for usage within its intended operating capacity, as specified in the IEC 61439 standard, is the verification of temperature rise on the assembly. The test sample will be tested for temperature-rise until it reaches the steady temperature condition, in accordance with the rated current declared by the manufacturer. When the temperature measured at various points, does not exceed the set level stipulated in the test requirements it is said to have been successfully comply with the requirements of the standard. This paper presents an experimental analysis of the Temperature rise test on low voltage switch board panel. The obtained experimental results have been compared for different test configurations conducted by changing Temporary test conductors.
Keywords: Temperature- rise, Test conductors, Current density
temperature rise tests and others. While doing the Temperature rise test as per IEC standard, we have to place the temperature sensor probes in several locations where temperature may vary and rise gradually after balancing the load.Current is applied until conditions stabilize, usually around eight hours, and in the final hours, temperatures are monitored, normally with thermocouples. The IEC standard recommends to mount the thermocouple at the various locations of LV assembly as shown in figure 1. Critical areas for temperature measurement are covers, operating handles, busbars and joints, insulators, cable terminals, device and/or internal air temperatures. It is well known that the critical point in temperature rise LV switchgear tests are the connections of the busbar to the circuit breakers usually a bolted silvered connection [1].
- INTRODUCTION
The Temperature rise test determines the system’s maximum working temperature at which it operates effectively. According to Ohms law, the voltage across a circuit (V) divided by the resistance within the circuit (R) equals the current (I) across the circuit. The current will drop as the resistance rises for a constant voltage since current is inversely proportional to Resistance. The increased mobility of a conductor’s molecules and free electrons brought on by heating is one of the factors contributing to higher electrical resistance. This is because their random clashes with the electrons that make up the current tend to obstruct their onward motion. The free electrons do indeed move quicker when the conductor is heated, but they do so randomly. As a result of the higher frequency of random collisions, the net electron current will be reduced.
- EFFECT OF TEMPERATURE ON TEST SAMPLE
What is written in IEC standards will influence what will happen in the electric products market all over the World. IEC 61439-1 has brought the intelligent concept of design rules [1]. It is a great advance. Could be much better if it was clear that the design rules concept is applicable not only to the short circuit aspect but also to
Figure.1 Locations of Thermocouples in Assembly.
Additionally, if the overheating is not detected, it may progress to thermal runaway and result in an internal arc or short circuit within the assembly. In order to confirm that temperature increase limitations are acceptable for various assembly components, including bus bar, connections, and functional units, testing as per IEC 61439 was conducted [1]. The rated current must be carried by each circuit individually and collectively without creating too many hot spots. But such testing must also take into account actual circumstances. The ambient temperature in the room is assumed to be 35 °C. The risk of failure would increase because a typical temperature rise inside a cabinet could cause several of the components to reach their stipulated environmental limitations. When installing the same device with other devices in an enclosure, we should manage the nominal current defined and validated on a
device alone in the free air to a rated current. To ensure performance over the course of the assembly, the rated current must be modified due to the rise in internal air ambient [2]. The electrical safety of a switchboard is ensured by taking this into consideration during temperature rise test, helping to prevent negative consequences from overheated equipment like overheat & impaired connections and compromise of Insulation performance.
- Recommendations of IEC 61439
In order to conduct the tests at the rated current, bus bars must be placed in the assembly enclosure with all typical covers and barriers in place. Functional units must be installed in the enclosure such that they are accessible when needed. Once more, all external covers and interior dividers must be in place. Additionally, each unit should receive its rated current plus the diversity factor, as before. This acknowledges that not all functioning units will be operating at their maximum rated load simultaneously. As a result, the energy lost as heat won’t just equal the maximum of each component added together. Instead, it will be marginally less, with the diversity aspect dictating this. The testing of bus bars and functional units is mandated by IEC 61439 Clause 10.10. The worst-case scenarios are used in these evaluations. The maximum temperature is 105oC for externally insulated conductors, 140oC for copper bus bars, and 125oC for individual components. Because insulation’s performance deteriorates with temperature more than bare metal’s does, the last limit is lower. The minimum temperature for an insulated bus bar support would be 140oC. Such a derating process ensures that the assembly’s individual components won’t deteriorate or fail. Additionally, it ensures that the entire assembly will operate securely and dependably for the duration of its useful life. Finally, it frees up designers of electrical panels to focus on other areas of the project without having to worry about service continuity and safety failures. Therefore, the highest temperature rises for 35°C ambient temperature is:
- 105oK for copper busbars and joints
- 90oK for incorporated components
- 70oK for terminals, external insulated conductors
- Copper versus Aluminum Bus bars
There are Only two substances can be used as electrical conductors. These are copper and aluminum. Both materials offer benefits and drawbacks, despite their significant differences as indicted in Table 1. It is inevitable that those who utilize copper will draw comparisons between it and aluminum [3]. That’s why comparisons are given where appropriate. The
International Annealed Copper Standard (IACS) conductivity of pure aluminum is around 65%.
Vol. 14 Issue 03, Marc-2025
Table.1 Properties of Copper and Aluminum
Electrical Properties Aluminum Copper Specific Resistance, cm Volume Conductivity mm2 Conductivity % IACS Co-efficient of expansion mm/m/ºC
3.133 31.9
57
2.3 x 10-5
1.7241 58
100
1.73 10-5
- Oxidation
This chemical process causes the base metal to lose electrons while increasing its oxygen concentration. Copper oxide is created when copper is left exposed. When oxygen-containing atmospheres are present, the constant oxidation of metal-metal contacts can quickly raise the contact resistance to a high value after it has been relatively low for a while. Copper oxides separate, grow, and flake off of the base metal. In comparison to aluminum oxides, copper oxides are softer and more readily broken apart by an applied contact force. They are semiconducting as well, and copper contacts that had a high resistance at first due to improper surface preparation might gradually lose resistance over time as a result of the semiconducting layer spreading over a wide region. Surface tarnishing of copper is typically observed in Sulphur-bearing atmospheres due to sulphide production from atmospheric hydrogen sulphide. Humidity has a significant impact on the growth of tarnished film; it can either increase or decrease it depending on the prevailing sulphide content. Aluminum is converted to alumina. The mechanism of degradation in this situation is typically seen as less likely due to the self- limited nature of oxide growth, which reaches a limiting thickness of approximately 10nm (nanometers) in a very short time. The diameter of the contact points, which is typically thought to be considerably more than 10 nm for rough surfaces, is far less than this [3]. With a high resistivity, aluminum oxide is brittle, hard, and persistent. Additionally, because it is transparent, a low contact resistance cannot be reached without proper surface preparation, even with an aluminum conductor’s shiny and clean look [4]. Where the oxide film is broken, current flow is limited in electrical connections with one or both aluminum contact components.
- Special Considerations about Test Conductors Painting is occasionally recommended because black matte surfaces radiate heat better than bright shining surfaces. The emissivity of the surface determines the efficacy of radiation. It is one for a perfect radiator (matt black), and zero for a perfect reflector. Practically speaking, the emissivity of shiny bright copper is about 0.3, dull copper is about 0.7, and discolored copper, like a bus bar after a few weeks of use, can reach 0.9. Radiation only loses about 10 to20% of heat, so the difference between a matte black surface and dull copper is approximately 3 to 6% of the total [4]. Because the thermal insulation supplied by the paint layer must pass through 90% of the heat that escapes by convection in order to achieve this apparent gain, the temperature of the bar rises rather than falls [5].
- Oxidation
- Recommendations of IEC 61439
- TEST METHODOLOGY
In the absence of precise information regarding the external conductors and the service Conditions, the cross-section of the external test conductors should be chosen taking into account the rated current of each circuit as described in IEC standard. The length of test conductor shall be 1 m for cross sections that are up to and including 35 mm2 in size. It shall be 2 m for cross sections greater than 35 mm2.
Table.2 Test conductors for test currents of at least 400A
Range of Rated Current-A Cross Section Sq.mm Type 0<A8 1 PVC Insulated Copper Cables 8<A12 1.5 12<A20 2.5 20<A25 4 25<A32 6 32<A50 10 50<A65 16 65<A85 25 85<A115 35 115<A150 50 150<A175 70 175<A225 95 225<A250 120 250<A275 150 275<A350 185 350<A400 240 As listed out in table 2, for rated currents up to and including 400 A, Copper cables or insulated wires with a single core must be used as the test conductors and shall be in the open air as much as is practical. Generally, the equipment ventilation has an obvious impact on the rate of temperature rise and regular pattern of temperature distribution of switchgear. The test current in all the phases need to be passed uniformly [5]. The different input currents lead to unbalance currents in phases and will impact on the temperature rise. As per IEC 61439-1: 2020 the temporary test conductor as indicted in the figure 2 needs to be used during Temperature tests at both incoming side as well as outgoing side forming the star point with external shorting links. The details about the test conductors for different values of test currents are listed out in the IEC standard in four different categories with ranges as given as follows.
- Test conductors for test (rated) currents up to and including 400A
- Test conductors for test (rated) current more than 400A but less than 1600A
- Test conductors for test (rated) current more than 1600A but less than 7000A
- Test conductors for test (rated) currents more than 7000A
Vol. 14 Issue 03, March-2025
The cost of copper bus bars will be always much higher than the PVC cables. As per IEC 61439, if bare copper bus bars are not available, the temporary bus bars can be of PVC insulated copper cables up to the test current of 1600A. But, the size of the bare copper bus bars that need to be used for the test currents up to and including 7000A is listed out in the standard the same has be indicated in graph 1. It is general practice in testing laboratories to use temporary test conductors made up of bare copper. Beyond the rating 7000A, for any panel the original manufacturer needs to specify the type, size & number of runs that need to be used during the TR test and the same will be reported in the test reports. But, nowhere mentioned about size, type and number of runs of Aluminum conductors that can be used for temporary test conductors. It is point of ambiguity whether aluminum conductors or bus bars can be used for test not.
Figure.2 Configurations of Temporary test conductors
Graph.1 Temporary Test conductors for test currents above 400 and up to including 7000A
- EXPERIMENTAL ANALYSIS
In order to analyze and investigate the effect of temporary test conductors selection on temperature rise test, an LT non-extendable panel has been chosen for the experimentation. The sample consists of only main bus bars with aluminum material. Four Number of joints are considered for the study with inside panel. The details of bus bars and distance between joints, clearance values are listed out eparately. The entire bus bars assembly was enclosed in a metal enclosure made up of CRCA sheet of thickness 2.5mm. In order to make effective analysis, the position of the Bus bars Joint 1 (JB1) & Bus bar Joint 4 (JB4) are created such way to exist nearer to the respective incoming and outgoing terminals. While performing Temperature-rise test, the internal and external ambient temperatures of the panel are measured as guided in IEC 61439, which enables to predict the steady state condition. The experiments of temperature-rise tests during this study are conducted in three major steps on an LT panel consist of only main bus bars. For the sake of study, the tests conductors selected are of various types & sizes are as listed out in the figure 3 and table 3 respectively . The tests currents considered during the temperature rise tests are 700A, 800A & 900A respectively which are chosen selectively for this study. The schematic of the panel under study with Thermocouples position and test data is given in figure 4 & table 4 respectively. For the above selected test currents the test conductors are used as per IEC 61439-1:2020.
Figure.3 Test Set up with test conductors mounted Table 3 Table.3 Details of the Test conductors
with sizes
Figure.4 Schematic of the panel under study with Thermocouples position
Figure.4 The description of the panel under study with schematic and test data.
Table 4. Obtained Test data for various test configurations
Figure 5. Temperature Rise Results with different test currents by changing the Test conductors
- Observations with Findings
Out of the test configurations that were conducted for the study towards the effect of temporary test conductors on TR test the following observations were drawn and the respective results are shown in figure.5.
- The temperature rises values obtained are more in case of the tests that were conducted with test current of 900A irrespective of the type of test conductors used. Higher the value of test current higher will be rise.
- The values of temperature rise are relatively higher in case of tests that were conducted by using PVC insulated Cu cables for the respective test currents of 700A, 800A & 900A.
- When compared the temperature rise values between bare Cu and Al test conductors, the rise obtained in case of Al test conductor is higher. Of course, the current density of test conductors plays a vital role in judging the temperature rise results. For the copper bus bars the current density is about 1.5 to 1.7 whereas for Al busbars is about 0.8 to 1.0. The size of Al test conductors used are chosen approximately based on the value of test current during this analysis.
- In order to achieve the optimum values of temperature rise, it is always recommended to use bare Cu busbars as temporary test conductor based on the test current. Irrespective of test current value, Al busbars are preferable to use as test conductors in case of the non- availability of Cu conductors but with bit sacrifice of temperature rise results.
- As on when declared by the customer/manufacturer PVC insulated Cu cables can be used as test conductors up to the test current of 1600A. The test results will be comparatively higher than former option with Cu or Al as test conductors.
- The Temperature rise test results obtained are relatively higher when the test is performed without the use of Test conductors itself. The recommendation to use the PVC is insulated cable is very minimal as the due the issues with reference to surface contact area and also number of runs need to be connected in parallel.
- Cu test conductor with matt black finish may provide better results of temperature rise test, when compared with that of bare Cu test conductors.
- Observations with Findings
- CONCLUSIONS
The experimental investigations discloses that the significance and usage of temporary test conductors during Temperature rise tests on switchgear assembly. From the case study under analysis out of the nine number of tests conducted for temperature-rise, we can reveal that, the rise in temperature on middle phase terminals and joints is always high about 10% compared with the extreme phases of the assemblies. The temperature rises values obtained at terminals and joints with the PVC insulated copper cable are about 10 to 15% higher compared with bare copper conductors. Similarly,
irrespective of value of test current, the temperature rises values obtained at terminals and joints with the bare aluminum conductors are about 5 to 10% more compared with bare Copper conductors. Taking the benefits in count as per the IEC 61439 standard, temporary test conductors made up of copper are always recommended irrespective of cost. During the type tests, the customer is also having scope to declare the type and size of test conductors to meet with the actual service conditions. It is giving the option to use the PVC Copper cable and also Aluminum busbars as an alternative option to do temperature rise tests. Whereas, for the HV switchgear assemblies customer/manufacturer is having more scope to declare about temporary test conductors that can be used as per IEC 62271 series of standards. The absolute values of temperatures as well as the rise values are increasing at both bus bar joints and terminals. When making temporary connections to the main circuit, care must be taken to ensure that the heat conducted to or conveyed from the test object is not significantly different from that of the connections meant for service.
ACKNOWLEDGEMENT
The authors are much thankful to the management of Central Power Research Institute, India for supporting this study.
REFERENCES
- IEC International Standard. Low voltage switchgear and control gear assemblies Part 1: General rules. IEC 61439-1, Edition 3.0
- C. Kilindjian, C. (1997). Thermal study of LV electric switchboards. Cahier Technique, (145).
- Thirumurugaveerakumar, S., Sakthivel, M., & Sharmila, D. V. (2016). Prediction and comparison of size of the copper and aluminum bus duct system based on ampacity and temperature variations using MATLAB. Thermal Science, pgs. 153-153.
- Hedia, H., Henrotte, F., Meys, B., Dular, P., Legros, W., & Pirotte,
P. (1999). Arrangement of phases and heating constraints in a busbar. IEEE Transactions on Magnetics, 35(3), 1274-1277.
- Thierry, J. P., & Killindjian, C. (1996). Electrodynamic forces on busbars in LV systems. Cahier Technique Merlin Gerin, 162, 20.
AUTHORS
S. Arjuna Rao, Obtained his M.Tech. (Power Systems) NIT Trichy, M.B.A from Bangalore University and PGD from Annamalai University. He joined CPRI in 2007 and currently holding the post of Joint Director in 100 MVA online testing Station, STDS, CPRI, Bhopal. He is FIE in Institute of Engineers and IEEE Professional Member in PES. He has more than twenty-five publications in in the area of Power systems, Distribution Transformers, CTs & Switchgears.
Rakesh. K. G, Degree in Electrical and Electronics Engineering in 2013 from BMS Collage of Engineering, Bangalore. He has 5 years of Industrial Experience before joining in CPRI in the year 2010. Currently he is holding the post of Engineering Officer in Heat Run Test Laboratory, CPRI, Bangalore.
G. Girija, M.E. from UVCE, Bangalore. Since, 1998 she is associated with CPRI and currently working as Joint Director at Short Circuit Lab, CPRI, Bangalore. She is having wide experience in of short circuit testing, Performance evaluation of Low Voltage Switchgear and control gear equipment, Distribution ransformer and Current Transformers. She is a Member of BIS committee Environmental testing procedures Sectional Committee.
Himangshu Roy, is currently holding the post of Joint Director and HOD of 100 MVA online testing Station at STDS, CPRI, Bhopal with more than 25 years of experience in short circuit testing. He obtained his M.Tech. in Electrical Engineering from IIT, Madras. His Areas of Interests are testing and analysis of & Low Voltage switchgear and control gear assemblies, Fuses & Distribution Transformers.
Sumbul Munshi, is currently holding the post of Additional Director and Unit Head at STDS, CPRI, Bhopal. She was post graduate with MBA and having more than Three decades of experience in high voltage, short circuit testing and performance evaluation of power equipment and interpretation of standards such as IS/BS EN/ IEC and ANSI. She started her career in CPRI in the year 1991 and currently serves as the Unit Head in Switchgear Testing and Development Station (STDS, Bhopal. She is also a member of the ETD-07 low voltage switchgear and controlgear Sectional committee of BIS.