
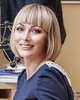
- Open Access
- [post-views]
- Authors : Svetlana Kondrashova, Egor Saprykin, Dr. Valeriy Naumyk
- Paper ID : IJERTV10IS030133
- Volume & Issue : Volume 10, Issue 03 (March 2021)
- Published (First Online): 05-05-2021
- ISSN (Online) : 2278-0181
- Publisher Name : IJERT
- License:
This work is licensed under a Creative Commons Attribution 4.0 International License
Effect of Additional Cadmium Chloride Additives To Saturating Mixture on The Formation of Diffusion Titanium Layer on Steel and Cast Iron
Svetlana Kondrashova
Director,
Berdyansk Mechanical Engineering College of National University "Zaporizhzhia Polytechnic",
Berdyansk, Ukraine
Egor Saprykin,
Deputy Director
Berdyansk Mechanical Engineering College of National University "Zaporizhzhia Polytechnic",
Berdyansk, Ukraine
Dr. Valeriy Naumyk
Vice-Rector for Research and International Activities National University "Zaporizhzhia Polytechnic", Zaporizhzhia, Ukraine
Abstract In this work, the influence of the saturating mixture composition on the processes of the surface diffusion layer formation on gray cast iron and steel is investigated.
Microstructural studies of the surface layer on gray cast iron and steel obtained using saturating mixtures of different composition were carried out.
According to the method of the experiment simplex-lattice planning, mathematical models were obtained that reflect the dependence of the diffusion layer depth, corrosion resistance, rate of oxidation on the saturating mixture composition.
Studies have shown that the optimal amount of cadmium chloride in the saturating mixture for the diffusion titanization is 610%.
Based on the obtained diagrams "property composition of the mixture" analysis, the new saturating mixture for titanization of steel and cast iron that provides effective increase of diffusion covering properties is developed
Key words: Gray cast iron, steel, diffusion saturation, titanization, cadmium chloride, microstructure, diffusion layer depth, corrosion resistance.
INTRODUCTION
One of the types of providing special properties to the surface layer of steels and alloys is the diffusion saturation with various alloying elements. The surface layer will acquire the appropriate level of properties.
Diffusion doping of the surface allows to achieve the absolute layer continuity and a high alloying elements concentration in the surface layer, which is especially important for the protection of cast products in aggressive environments [1-4]. The process of diffusion saturation does not require special equipment and can be carried out in any heating furnace with an operating temperature of 10001200
°C.
According to the literature, ammonium halides, mainly ammonium chloride, are most often used as activators in diffusion metallization [5-7].
This study is devoted to the development of methods to increase the saturating mixtures efficiency for diffusion metallization of low-carbon steel St 3 and gray cast iron in order to increase their corrosion resistance and oxidation resistance. Preliminary studies
-
of the structure and properties of diffusion layers obtained in different mixtures at saturation temperatures of 9001050ºC and holding time of 28 hours showed that the saturation temperature of 1000 ºC and holding time of 6 hours are optimal. The study of the additional additives influence on the diffusion coatings properties was performed using the methods of experiment mathematical planning.
The choice of the saturating mixture composition is a difficult task because the elements that are part of it have different intrinsic diffusion coefficients, as well as the mutual influence on the diffusion rate. There may be cases when in the presence of additional additives at a certain content of saturating elements in the working mixture, the depth of diffusion and concentration in the surface layer of one or both elements is significantly reduced compared to one-component saturation [9]. The diffusion layer properties can be significantly improved by obtaining on the complex-doped layer surface. Thus, the positive effect of Al and CdCl additives in the saturating mixture is explained by the fact that these elements form on the diffusion layer surface quite dense and strong oxide coatings, which increases corrosion resistance and the diffusion layers stability, because of the diffusion rate decrease of the coating elements into the base metal, or by creating barrier layers at the boundary of the coating the base metal [10].
Existing data [5-7, 11] suggest that titanium, as a strong carbide-forming element, combines much faster with carbon than with iron. Therefore, at the initial moment of saturation as a result of titanium diffusion with a saturating mixture, titanium carbide TiS is formed on the surface. The formation of titanium carbide is accompanied by intense diffusion of carbon to the surface, which leads to a sharp redistribution of carbon. At the same time its concentration increases in a surface zone due to association of near-surface layers, forming a decarburized layer. At the next stage, the diffusion flux of carbon to the surface decreases: first, due to the presence of a decarbonized zone under the layer; secondly, due to the decrease in the diffusion mobility of carbon in titanium carbide. Further growth of the diffusion layer is due to the diffusion of iron and titanium in the surface layer, which leads to the formation of compounds FeTi and Fe2Ti, according to the Fe-Ti diagram.
THE MAIN RESEARCH MATERIAL
Previous studies [8] have shown that ammonium chloride
is the most acceptable among the tested activators for the titanization process. It allows to obtain on low- carbon steels layers with a high content of titanium, which is consistent with the data of [6, 12], and on cast iron – titanium carbide with a narrow zone of solid solution. Obtaining a soft sublayer is a positive factor when using carbide layers that work on wear. However, the small thickness of the titanium carbide layer and the strong increase in its brittleness with increasing thickness does not allow the use of titanium surroundings with ammonium chloride for effective saturation of cast iron. In order to eliminate this disadvantage, a titanium mixture containing cadmium chloride and combining cadmium and titanium was developed. This process was carried out in mixtures of different composition. The mixtures composition, as well as the results of the layers properties study are presented in table 1.
TABLE 1. DEPENDENCE OF TECHNOLOGICAL PARAMETERS OF THE TITANIUM LAYER ON THE SATURATING MIXTURE COMPOSITION
tr>
The mixture name
Layer depth, m
Corrosion rate, g/m2h
Oxidation at 800º, g/m2h
Steel
Cast iron
Steel
Cast iron
Steel
Cast iron
1. 50%FeTi+10%CdCl2+2%NH4Cl+38%Al2O3
138,9
416,7
0,767
2,16
25,58
28,83
2. 30%FeTi+10%CdCl2+4%NH4Cl+56%Al2O3
136,1
408
0,291
1,50
36,58
35,76
3. 70%FeTi+4% CdCl2+10%NH4Cl+16%Al2O3
62
310
0,330
1,55
55,13
46,52
4. 40%FeTi+10%CdCl2+3%NH4Cl+47%Al2O3
113
372,9
0,313
1,52
43,49
42,52
5. 60%FeTi+7%CdCl2+6%NH4Cl+27%Al2O3
145,3
668,3
0,255
0,65
21,55
22,30
6. 50%FeTi+7%CdCl2+7%NH4Cl+36%Al2O3
143,3
644,8
0,288
1,04
26,58
23,33
7. 50%FeTi+8%CdCl2+53%NH4CL+36,7%Al2O3
154,3
617,2
0,347
1,13
35,29
33,87
At Figure 1 its shown the microstructures of low carbon steel and gray cast iron surface layer after saturation in the mixture 5 (which showed the best results for all parameters of the study). It was found that a white layer is formed on the steel near the surface, which together with a solid solution of
titanium in -iron contains TiC, TiFe2. The microhardness of the surface layer is 190230 MPa. Then there is a decarbonized zone, followed by the base metal. The thickness of the layer depends on the composition of the saturating mixture.
a b
Fig. 1. Microstructure of the surface layer after titanization in the mixture 5 (see Table 1), × 150: a on low carbon steel; b on gray cast iron.
At saturation of gray cast iron on a surface the titanized layer with a accurate border is formed. The results of X-ray diffraction analysis showed that the diffusion layer consists of TiFe2 and TiC compounds with a predominant amount of the
latter. The layer depth the and its structure depends on the saturating mixture composition.
The oxidation rate of the diffusion layer of different experimental variants is shown in Fig. 2.
90 3
80 3
4
Mass increase, g / m2 h
Mass increase, g / m2 h
7
7
70 4 60 2
2
7 1
6
6
50 40 6
5
1
30 5 20
10
4 8 12 16 4 8 12 16
Test time, hours
b
Fig. 2. Kinetics of the diffusion layer oxidation (1 7 mixture number): a steel; b cast iron.
The study revealed the presence of a thermal effect during titanization in saturating mixtures activated simultaneously with ammonium chloride and cadmium (see Table 1) in contrast to mixtures activated only with NH4Cl or CdCl2.
The reasons for the titanization process activation in the mixtures containing NH4Cl and CdCl2 may be:
50%FeTi+10%CdCl2 +2%NH4 Cl+38%Al2 O3
147
147
135
135
117
117
100
100
120
120
135
135
145
145
153
153
150
150
-
The interaction of cadmium chloride with hydrogen, which contributes to the appearance of additional titanium chlorides.
-
Cadmium plating of saturated materials in the process of heating to the titanization temperature.
-
Restoration of the oxide film on the surface of titanium
80
80
70%FeTi+4%CdCl2 +
+10%NH4 Cl+16%Al2 O3
157
30%FeTi+30%CdCl2 +
+4%NH4 Cl+56%Al2 O3
powder with cadmium chloride.
-
Cadmium reduction of higher titanium chlorides to lower ones, which can be further reduced to pure titanium.
-
The validity of the first three conclusions is confirmed by micro-X-ray diffraction analysis (cadmium diffusion layer after titanium is stored in the amount of up to 7%).
Mathematical processing of the research data allowed to obtain the polynomial type equations, describing the dependence of the main layer parameters on the mixture components content. Based on these equations, diagrams "property composition of the mixture" were constructed.
In Fig. 3 shows a diagram of the diffusion layer depth on the saturating mixture composition dependence for low carbon steel.
Fig. 3. Dependence of the diffusion layer depth on the saturating mixture composition (steel).
As can be seen, the maximum value is in the middle of the concentration triangle and decreases nonmonotonically to the left corner and its right side. This indicates that obtaining the optimal diffusion layer depth is affected by both the content of CdCl2 and the content of FeTi in the saturating mixture (table 1).
The change in the corrosion rate of the diffusion layer on the steel from the saturating mixture composition is presented in Fig. 4. It should be noted that the minimum value corresponds to the middle of the left side and the right corner of the concentration triangle. This suggests that the content of FeTi 60% and CdCl2 6 8% is optimal for increasing corrosion resistance.
Similar dependences are obtained at the saturation of cast iron.
In Fig. 5 presents a diagram of the dependence of the oxidation rate on the saturating mixture composition for steel.
50%FeTi+10%CdCl2 +2%NH4 Cl+35%Al2 O3
0,5
0,4
0,28
0,28
0,25
0,25
0,3
0,3
0,31
0,31
0,37
0,23
0,23
0,28
0,28
0,3
0,3
0,27
with ammonium chloride and cadmium in contrast to mixtures activated only with NH4Cl or CdCl2.
Based on the method of experiment planning, mathematical models were obtained and diagrams "property composition of the mixture" were constructed, which reflect the dependence of the diffusion layer depth, corrosion resistance, rate of oxidation on the saturating mixture composition.
Studies have shown that the optimal amount of cadmium chloride in the saturating mixture for diffusion titanization is 610%.
On the basis of the conducted experimental
70%FeTi+4%CdCl2 +
+10%NH4 Cl+16%Al2 O3
30%FeTi+30%CdCl2 +
+4%NH Cl+56%Al O
researches executed with use of mathematical planning of experiment the new saturating mixture for
Fig. 4. Dependence of the diffusion layer corrosion rate on the saturating
mixture composition (steel).
As can be seen, the minimum oxidation rate values are adjacent to the triangle left side, they rise in the direction of increasing the cadmium chloride content in the saturating mixture and decreasing of ferrotitanium (right side of the concentration triangle).
50%FeTi+10%CdCl2 +2%NH4 Cl+35%Al2 O3
42
42
40
40
36
36
33
33
34
34
30
30
26
26
27
27
37
37
35
45
45
39
39
31
titanization of steel and cast iron that provides effective increase of diffusion covering properties is developed. The developed mixture has the following composition: 60% FeTi + 7% CdCl2 + 6% NH4Cl + 27% AL2O3.
REFERENCES
-
O.E. Datsyuk, V.G. Khyzhnyak, T.V. Loskutova and others, Phase and chemical composition of diffusion titanium- aluminum chromium coatings, Journal nano- and electron. physics, 2018, 10, 3, pp. 03015-2 – 03015-4.
-
L.P. Klimenko, V.I. Andreev, L.M. Dikhta and others, Investigation of wear of cast iron surfaces of friction pairs modified with titanium sponge, Internal combustion engines, 2018, 1, pp.63-66.
-
.. Mikosyanchyk, R.G. Mnatsakanov, M.S. Khimko, Modeling of wear intensity, Problems of Friction & Wear, 2015, Vol. 1. Issue 66, pp. 140-145, Access mode: http://web.a.ebscohost.com.
-
.. Alimov, Z.A. Duryagin, Corrosion and protection of metals from corrosion, Donetsk – Lviv: Eastern Publishing House LLC, 2012, 328 p.
-
V.G. Khyzhnyak, T.V. Loskutova, O.E. Datsyuk, O.V.
70%FeTi+4%CdCl2 +
+10%NH4 Cl+16%Al2 O3
30%FeTi+10%CdCl2 +
+4%NH4 Cl+56%Al2 O3
Khyzhnyak, Multi-component diffusion coatings based on titanium, aluminum and silicon on nickel, Scientific news of NTUU "KPI": scientific and technical magazine, 2015, 1
Fig. 5. Change in the diffusion layer rate of oxidation on the saturating mixture composition (steel).
For cast iron, the properties studied above have approximately the same dependence as for steel.
Analysis of the obtaned diagrams allows us to conclude that the optimal amount of cadmium chloride in the saturating mixture for diffusion titanation is 610%. The introduction of cadmium chloride over 10% not only does not intensify the process, but also degrades the quality of the diffusion layer. Reducing the amount of cadmium chloride in the mixture below 5% weakens the effect of its action. Thus, as an optimal variant of the mixture for diffusion titanation, the following composition is proposed: 60% FeTi + 7% CdCl2 + 6% NH4Cl
+ 27% AL2O3.
CONCLUSIONES
A set of researches of the influence of the saturating mixture composition on the processes of the surface titanium diffusion layer on gray cast iron and steel formation is carried out.
It was revealed the presence of a thermal effect during titanization in saturating mixtures activated simultaneously
(99), pp. 79-84.
-
N.A. Kurilo, V.G. Khyzhnyak, V.I. Sigova, S.V. Marchenko, Physico-chemical conditions of the titanization process of nitrided alloys in chlorine medium, Visn. Sumi state university, Sir. Tech. science, 2008, 3, pp. 29-33.
standard of Ukraine. Corrosion-resistant steels. Determination of resistance to intergranular corrosion, Part 1, Austenitic and ferritic-austenitic (two-phase) steels. Corrosion test in nitric acid by weight loss test (Hugh test), Kyiv: Derzhspozhyvstandart Ukrainy, 2008, 6 p.
-
S.G. Kondrashova, E.V. Saprykin, V.V. Naumyk, Influence of saturating mixture composition on formation of structure and properties of diffusion titanium layer on gray cast iron, New materials and technologies in metallurgy and mechanical engineering, 2019, 2, pp. 24-30.
-
V. Popovych, Technology of structural materials and materials science: dictionary-reference book, Lviv: Svit, 2010, 304 p.
-
Yu.A. Karpov, A.P. Savostin, Methods of sampling and sample preparation, M.: BINOM, Laboratory of Knowledge, 2003, 143 p.
-
G.P. Fetisov, M.G. Karpman, W.M. Matyunin and others, Materials science and technology of metals, M.: Higher School, 2002, 638p.
-
V.I. Bondar Corrosion and protection of materials: textbook, manual for students of metallurgical specialties, Mariupol: PSTU, 2009, 126 p.