
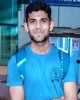
- Open Access
- Authors : Pankaj Kumar Chaudhary
- Paper ID : IJERTV10IS070254
- Volume & Issue : Volume 10, Issue 07 (July 2021)
- Published (First Online): 30-07-2021
- ISSN (Online) : 2278-0181
- Publisher Name : IJERT
- License:
This work is licensed under a Creative Commons Attribution 4.0 International License
Effect of Back Pressure on the Performance of Supersonic Intake
Pankaj Kumar Chaudhary
M. Tech (Aerospace Engineering) Indian Institute of Technology, Bombay, India
Abstract: – Air intake is a device used to diffuse the incoming mass of free stream air to the conditions which is suitable for compressor or combustion chamber and protects the aircraft engine from the foreign object damage. This project involves the computational investigation of flow field of a supersonic air intake with different back pressure and cowl deflection angles. It involves designing and analysis in CATIA and ANSYS software. The 2D geometry of intake was drafted in CATIA and it was saved in .iges format. This file is imported in ANSYS19 student version for the further process such as meshing and solution. Two dimensional steady numerical simulations has been done to capture the flow field inside the intake by using ANSYS Fluent software. Fine meshing has been done near the wall to capture the reverse flow field and boundary layer separation which is shown in the figure below. Two dimensional steady simulations are carried out on basic model for free and pressurized intake. After getting a converged solution with free flow condition, computations were further made at different back pressure. On increasing the value of back pressure ratio, the formation of normal shock is moving towards the entry of the intake geometry and the first normal shock but the weak shock is obtained when the back pressure ratio is increased three the static pressure.
Keywords- BPR, Ramp, Cowl
I-INTRODUCTION
The air intakes are mainly manufacture by the manufacturer airframe which is coordinated with the manufacturer engine. The air intake is required to capture the air which is coming from free stream and also to change directions and hence supply it to engine. It should be with less flow distortion as much as possible that is non- uniformity must be less. Intake should not result in external drag in an excessive amount to aircraft.
it is to a
it is to a
In comparison to subsonic intakes the supersonic intakes are more complicated. Often, the design of the supersonic intake involves efficiency, weight, cost and complexity. The supersonic intake consists of two segments, first one is a supersonic diffuser here flow is decelerated to subsonic from supersonic through the series of shocks. And then
followed by subsonic diffuser to decelerate the flow
lower subsonic speed from higher subsonic speeds.
The operation of the intakes varies tremendously over operating range of engine. During the take-off of the aircraft the engine requires a higher value of mass flow and is operating at a lower value of speed in order to maintain the value of thrust. To operate the intake in a supersonic flow, before it, it must have to pass through subsonic flow regimes. The process to establish the stable shock system is generally referred by Starting of an intake.
II-LITERATURE REVIEW
Talking about the supersonic intake, there is a very complex shock structures formed inside the intake geometry, so in order to improve the performance of the intake, it become necessary to investigate on it. Here are some reviews of the thesis of some researcher on the performance of the intake.
Experimental and computational investigations made by Das and Prasad to obtain details of flow field of the supersonic intake with the different cowl deflection angles & back pressure at exit. The flow field was obtained on the basic configuration designed for Mach number 2.2. The result that was obtained with the cowl deflection shows better performance in comparison to the performance achieved with the basic intake & a bleed of 2.8 %.
In [1], authors investigated the performance & unsteady behavior of a ramjet intake model. The investigation was carried out in the supersonic flow range and the experiment was conducted to understand the complex flow phenomenon of ramjet intake & the effect on performance. The ramjet was designed for a shock lip of Mach number M= 2.5. An optimum position & the width of the bleed gap avoid any reflection of cowl shock which improves the performance of intake.
In [2], authors investigated multiple shock wave turbulent boundary-layer interactions in a rectangular duct by using wall pressure measurement, surface oil flow visualization, and laser Doppler velocimetry. In this experiment two undisturbed incoming Mach numbers M=2.45 & M=1.6 were considered. At M = 2.45, the shock structure was neutrally stable pattern of oblique shocks and is followed by the repeated normal shocks with level of flow confinement having only small effect in interactions. Whereas, at M = 1.6, the pattern consisted of bifurcated normal shock followed by weaker and un bifurcated normal shocks. In contrast to the M = 2.45, the lower Mach number interaction was much steadier with the length of the interactions.
In [3], authors investigated the starting characteristics of small scale rectangular intake with a thick ingested boundary layer at a nominal Mach M = 3. The parameters that were investigated are included Reynolds number, cowl length & cowl height. In this experiment a small scale supersonic inlet has been conducted in order to better understand the major factors which are influencing. The un start & restart the characteristic of simple inlet.
In [5], authors conducted the experiment of passive boundary layer on a small supersonic side wall intake at the
Mach number of M = 1.46, to study the possibility of improving intake performance by such control. The results of experiments had shown that for a supersonic intake, passive control can reduce shock interaction losses & improves the overall pressure recovery & also controls pre entry shock position.
III-RESEARCH AND METHODOLOGY
This project involves computational work to analyse flow field inside the intake. For that geometry is taken from the reference [4] and slight modification has been done. It has been done analysis in details with the proper meshing in ANSYS software at different value of back pressure applied, which are density based rather than the pressure based. Initially we applied the zero back pressure and we observed that there are no any formations of the normal shock. As we increased the value of the back pressure greater than three then we observed the normal shocks.
as ogy
as ogy
Computational work has been carried out for current project. The 2D geometry of intake was drafted in CATIA and it was saved in .iges format. This file is imported in ANSYS19 student version for the further process such meshing and solution. The details procedure methodol
is presented in this section.
Fig.1. 2-D Intake
Two dimensional steady simulations were carried out on basic model for free and pressurised intake. After getting a converged solution with free flow condition, computations were further made at different back pressure.
Fig.2. Surface
Structured meshing has been created to ensure face to face meshing in ANSYS meshing. For this number of elements were provided at the each edge of the intake surface and also on domain surface. Fluid domain is created outside the intake from leading edge of ramp to the inclined portion of the cowl to capture the shock created due to inclination of surface. Fine meshing has been done near the wall to capture the reverse flow field and boundary layer separation which is shown in the figure below.
The entire mesh includes 31700 numbers of cells, 63940 number of faces, 32241 number of nodes and 1 partition.
Fig.3. Meshing
IV-RESULTS AND DISCUSSION
-
Density Gradient Contour at Different Back Pressure Ratio
Here, in this section the density gradient contour is showing at the different back pressure value.
-
At zero back pressure ratio
In this contour, there are two oblique shocks are formed one is at the first ramp wall and other is at the second ramp wall, and they are striking at the leading edge of the cowl inner wall. From the terminating shocks it can be observed that there are no any formations of normal shocks. And also there are no separations of the shocks throughout the geometry.
Fig.4. Density Gradient Contour at 0 BPR
the ner
the ner
-
At 3.0 back pressure ratio
Here, there are two oblique shocks are forming at both ramp wall striking at the leading edge of the cowl in
wall. The formation of normal shock has been formed as the terminal shock in the range of second diffuser section. Here the separation of the shock is taking place in the isolator section. Here the density is increasing as the area is decreased but the mass flow rate is having the higher value.
Fig.5. Density Gradient Contour at 3.0 BPR
-
At 3.5 back pressure ratio
Here, there are two oblique shocks are forming at both the ramp wall striking at the leading edge of the cowl inner wall. Here, the position of formation of terminating normal shock is moving forward towards the entry section of the intake. The separation of the shock is taking place in the isolator section. The separation area is increased here, at the isolator section.
Fig.6. Density Gradient Contour at 3.5 BPR
-
At 4.0 back pressure ratio
Here, there are two oblique shocks are forming at both the ramp wall striking at the leading edge of the cowl inner
wall. Here, the position of formation of normal shock has been formed at the leading edge of the cowl inner wall, as it is continuously moving forward towards the entry of the intake.
Fig.7 Density Gradient Contour at 4.0 BPR
-
-
Static Pressure Variation along the Ramp Wall
In the graph it has been shown that the pressure ratio is increasing at the ramp wall surface, it is decreases when the expansion fan is formed and then it is increased when reflections of shocks are achieved then further it is decreased and increased. At 3.0 back pressure value, it is observed that at the second diffuser and isolator section it is continuously increasing. At 3.5 back pressure value, it is observed that from the first diffuser section the pressure is increasing. At 4.0 back pressure ratio, it is observed that pressure ratio increased to more than 5 but then decreased to 4. In the following graphs the pressure variations along the ramp wall are shown at BPR 0, 3.0, 3.5 and 4.0 respectively.
3
2
P/P'
1
0
PRESSURE VARIATION ALONG THE RAMPWALL
3
2
P/P'
1
0
PRESSURE VARIATION ALONG THE RAMPWALL
0
0.5
X/L
1
1.5
0
0.5
X/L
1
1.5
PRESSURE VARIATION ALONG THE RAMPWALL
PRESSURE VARIATION ALONG THE RAMPWALL
Fig.8. Pressure Variation along the Ramp Wall at 0 BPR
Pressure Variation along the Ramp Wall
4
3
P/P' 2
1
0
0 0.5 X/L 1 1.5
Pressure Variation along the Ramp Wall
4
3
P/P' 2
1
0
0 0.5 X/L 1 1.5
Fig.9. Pressure Variation along the Ramp Wall 3.0 BPR
Pressure Variation along the Ramp Wall
Pressure Variation along the Ramp Wall
6
4
P/P'
2
Fig.10. Pressure Variation along the Ramp Wall 3.5 BPR
PRESSURE VARIATION ALONG THE RAMPWALL
PRESSURE VARIATION ALONG THE RAMPWALL
Pressure Variation along the Ramp Wall
Fig.12. Pressure Variation along the Ramp Wall and Cowl Inner Surface at 0 BPR
0
0 0.5
X/L
1 1.5
Fig.11. Pressure Variation along the Ramp Wall 4.0 BPR
-
Pressure Variation along the Ramp Wall and Cowl Inner Surface
From these graph shown below, the pressure variation can be observed simultaneously, by observing both the graph of pressure variation of ramp wall (reddish graph) and the cowl inner wall (blackish graph). It is also observed that both the graph are ending at the same value, and thus it can be concluded that the results are obtaining parallel in the correct form of pressure variation along the ramp wall and the cowl wall surfaces. Further at the ending of both the graph they are meeting at the same point. As the both ends are meeting at the single point then at the value of pressure ratio is same at the end point and it can be concluded that the mass flow rate is constant at the entry and exit of the geometry.
In the following graphs the pressure variations along the ramp wall and cowl inner surface are shown at BPR 0, 3.0,
3.5 and 4.0 respectively.
Fig.13. Pressure Variation along the Ramp Wall and Cowl Inner Surface at 3.0 BPR
Fig.14. Pressure Variation along the Ramp Wall and Cowl Inner Surface at 3.5 BPR
Fig.15. Pressure Variation along the Ramp Wall and Cowl Inner Surface at 4.0 BPR
V-CONCLUSION
At zero back pressure value there is no any formation of the shocks inside the intake geometry. And at this value of back pressure the maximum pressure recovery factor is obtained and also the maximum value of total pressure at exit is obtained.
On increasing the back pressure value, by three times of the static pressure, the high density gradient is obtained and the terminating normal shock is formed at this Mach number but the weak shock is obtained. And the total exit pressure is decreased here and also the pressure recovery factor also decreases. Here, the formation of terminating normal shock is moving forward to the direction of towards ramp wall. The density gradient is increasing highly and the area is decreased but the mass flow rate is constant.
On increasing the value of back pressure ratio to 3.5 the, the total exit pressure increases and also the pressure recovery factor also increases. The formation of normal shock is still moving forward and obtained in the region of second diffuser section. Here the flow separation is occurring due to the sudden change of the geometry.
And on increasing the value of back pressure ratio to 4, it can be observed that the formation of normal shock is taking place at the tip of the cowl and considered as the cowl shock. This is the stable position of the formation of the normal shock. Here, high density gradient is obtained at the cowl tip, and the area is small but mass flow rate is constant.
Here, from the above results it is observed that on increasing the value of the back pressure ratio, the formation of normal shock is moving towards the entry of the intake geometry and when the first normal shock but the weak shock is obtained when the back pressure ratio is increased three times the static pressure.
REFERENCES
-
C. Hirschen, D. Herrmann. A. Gulhan, Experimental Investigation of the performance and Unsteady Behaviour of a Supersonic Intake, Journal of Propulsion and Power, Vol. 23, No. 3, May-June 2007.
-
Bruce F. Carroll, J. C. Dutton, Characteristics of Multiple Shock Wave/Turbulent Boundary Layer Interactions in Rectangular Duct, J. Propulsion, Vol. 6, No. 2
-
D. M. Van Wie, F. T. Kwok, and R. F. Walsh, Starting Characteristics of Supersonic Inlets, Joint Propulsion Conference and exhibit, 32nd , Lake Buena Vista, FL, July 1-3, 1996.
-
S. Das, J. K. Prasad, Starting Characeristics of a Rectangular Supersonic Air-Intake with Cowl Deflection, The Aeronautical Journal, March 2010, Vol. 114, No. 1153
-
S. Rolston, S. Raghunathan, Passive Control of Pre-entry Shock in Supersonic Intakes, 31st Aerospace Science Meeting and Exibit, January 11-14, 1993/Reno, NV.
-
J. D. Anderson, Jr., Introduction to Flight, McGraw Hill, 3rd
Edition, 1989.
-
J. D. Anderson, Jr., Fundamentals of Aerodynamics, McGraw Hill, 3rd edition, 2001.
ics,
ics,
-
J. D. Mattingly, W. H. Heiser, D. T. Pratt, Aircraft Engine
Design, American Institute of Aeronautics and Astronaut Reston, Second Edition, 2002.
-
B. Roy, A. M. Pradeep, Jet Aircraft Propulsion, Department of Aerospace Engineering, IIT Bombay, Lect. 28, NPTEL Portal, MHRD India.